If you work in Printed Circuit Board industry, you may know a normal PCB FR4-Tg is 130-140 degrees, the medium Tg is greater than 150-160 degrees, and High-TG FR4 Printed Circuit Board is greater than 170 degrees.
And what is a High-TG FR4 Printed Circuit Board? High-TG PCB is another name for a high-temperature FR4 PCB, it means the printed wiring boards designed to endure for extremely high-temperature. A Printed Circuit Board is defined as high-TG FR4 PCB if its glass transition temperature (TG) is higher than 170 degrees Celsius. High-TG FR4 will have better mechanical and chemical resistance to heat and moisture than standard FR4. The higher the TG value, the better the temperature resistance of the material, so High-TG FR4 is more and more popular particularly working in high power industry.
Best Technology can provide many different High-TG FR4 material for Rigid Circuit board, Typical High-TG FR4 PCB material including: ITEQ-IT-180A, ISOLA 370HR, ShengYi S1000-2 and etc.
From the following PCB picture, you can see the normal TG130 FR4 PCB substrate is not only softening, deformation, melting, as well as other phenomenon working under high temperatures, but also there is a sharp decline in electrical properties, which will effect on product life.
If your FR4 Printed Circuit Board or PCBA board appear to above problems, then you should consider to use a High-TG FR4 Rigid Circuit Board. it may be catching your interest willing to understand a little bit more about High-TG FR4 printed circuit boards. Because High Tg Rigid Circuit board have a better stability at high temperatures, the substrate provides better heat resistance, mechanical and chemical stability for the circuit board.
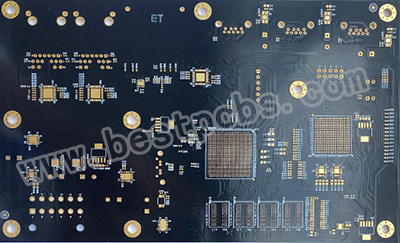
Properties/ Applications of high Tg PCB
With the rapid development of electronics industry, High-TG FR4 PCB is widely used in Uninterrupted Power Supply, precise instrument as well as industry. High-TG FR4 PCB material probably designed for the high functionality, high multi-layer development high-density circuit; higher heat resistance and high-density surface mounting technology (SMT). So, the demand on High-TG FR4 PCB material become more widely used PCB manufacturing.
What’s more, High TG material is also popular in LED lighting industry, because heat dissipation of LED is higher than normal electronic components, but same structure of FR-4 board is much cheaper than metal core PCB, such as aluminum PCB.
High-TG FR4 PCB materials have the following properties:
 Resistance to high temperatures
 Long delamination durability (aging of materials to consider for safety reasons)
 Low thermal expansion
Excellent PTH reliability
Good mechanical properties
High temperature durability
High value of thermal stress resistance
high temperature durability
long delamination durability
Low Z axis expansion (CTE)
Advantages of High-TG FR4 PCB
Higher stability:Â it will automatically improve the heat resistance, chemical resistance, moisture resistance, as well as stability of the device if increasing the TG of a printed circuit board substrate.
Bear high power density designs:Â high TG PCB will be a good solution for heat management if the device has high power density with quite high heat generation rate.
It can achieve with using a larger printed circuit board to change the design and power requirements of a device when reducing the heat generation of ordinary board, what’s more, it also can use the high TG PCB.
Ideal for multilayer & HDI PCBs:Â there will lead to high levels of heat dissipation because multilayer & HDI PCBs are more compact and have dense circuits. So high TG PCBs are often used for the multilayer & HDI PCBs so that it can make sure reliability in Printed circuit board fabrication.
If your applications are in any danger of subjecting your PCBs to extreme temperatures or the PCB is required to be RoHS Compliant, it will be in your best interest to look into high-TG FR4 PCBs.
Come to contact Best Technology Co., Limited. for High-TG PCB assistance. we can help you determine if you need high-temperature printed circuit boards and direct you to which specific boards are likely to be useful for your design and application. If you are transitioning to RoHS or just need more information about the High TG laminates, just give us a call and we’ll be happy to accommodate you. contact us online right now.