The typical solder temperature for PCBs is 240â to 270â for lead-free soldering, and 240âto 260â for lead-based soldering.
If you’re building or repairing a PCB, knowing the right soldering temperature is key. It keeps your components safe and ensures strong connections. The temperature you use depends on the type of solder and the method. In this blog, weâll break down everything you need to know about solder temperatures for PCBs.
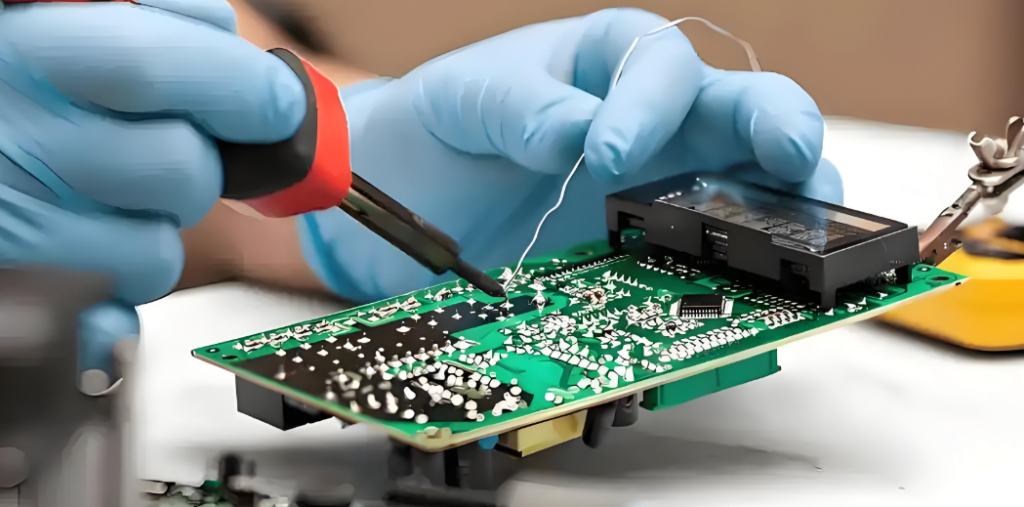
Why Solder Temperature Matters in PCB Work?
When working with printed circuit boards, one of the most critical factors for quality and reliability is soldering temperature. Whether you’re assembling prototypes, repairing a PCB, or managing high-volume production, knowing the right temperature is essential for success.
Too low, and the solder wonât melt properly. Too high, and you might damage the board or components. Accurate temperature helps create reliable joints and avoids costly rework. It also protects sensitive parts from overheating.
Solder temperature affects not only how well the joints form but also how long your product will last in real-world use. In this blog, weâll explore the ideal soldering temperatures for different solders and methodsâand how to avoid costly mistakes.
What Determines Soldering Temperature?
Soldering temperature is not a fixed value. It depends on several key factors:
- Type of solder alloy (leaded or lead-free)
- Soldering process (manual, reflow, wave)
- PCB material (standard FR-4, high-Tg, ceramic, etc.)
- Component sensitivity
- Ambient factory temperature and humidity
Each variable impacts how heat should be applied to the board. Applying the right temperature at the right time ensures the best wetting, strong mechanical bonds, and excellent electrical contact.
Solder Types and Their Melting Temperatures
- Lead-Based Solder (e.g., Sn63/Pb37)
- Melting point: 183°C
- Typical working temperature: 240°C to 260°C
- Benefits: Good wetting, lower processing temperature
- Drawbacks: Contains lead; banned in many consumer products (RoHS compliance)
Lead-based solder is often used in military, aerospace, or industrial environments where reliability outweighs regulatory restrictions. Itâs easier to work with and provides strong joints with less thermal stress on components.
- Lead-Free Solder (e.g., SAC305: Sn96.5/Ag3.0/Cu0.5)
- Melting point: ~217°C
- Typical working temperature: 245°C to 270°C
- Benefits: RoHS compliant, eco-friendly
- Drawbacks: Higher processing temperature, slightly brittle joints
Lead-free solder has become the standard in modern electronics manufacturing due to environmental regulations. However, it requires precise control of temperature and time to ensure quality results.
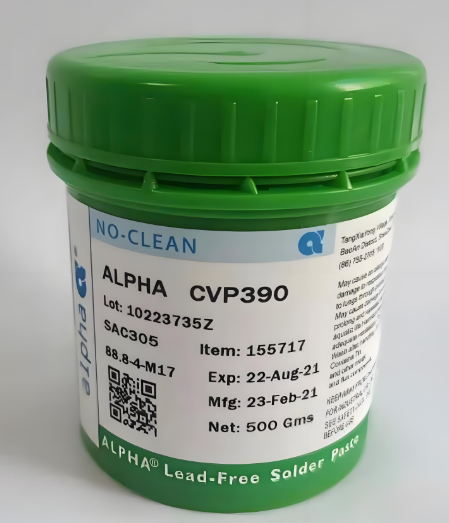
Soldering Methods and Their Temperature Profiles
Letâs explore how soldering temperatures vary across different processes used in PCB manufacturing and assembly.
1. Reflow Soldering
Reflow soldering is the most common method for assembling surface-mount components. A solder paste (a mix of powdered solder and flux) is applied to the PCB, and components are placed on top. Then, the board goes through a reflow oven with controlled temperature zones.
Reflow Temperature Profile (Lead-Free):
- Preheat: 150°Câ180°C for 60â120 seconds
- Soak: 180°Câ200°C for 60â90 seconds
- Reflow Peak: 240°Câ250°C for 30â60 seconds
- Cool-down: Controlled descent to room temperature
Reflow Temperature Profile (Lead-Based):
- Preheat: 120°Câ150°C
- Soak: 150°Câ180°C
- Reflow Peak: 210°Câ230°C
- Cool-down: Gradual cooling to avoid thermal shock
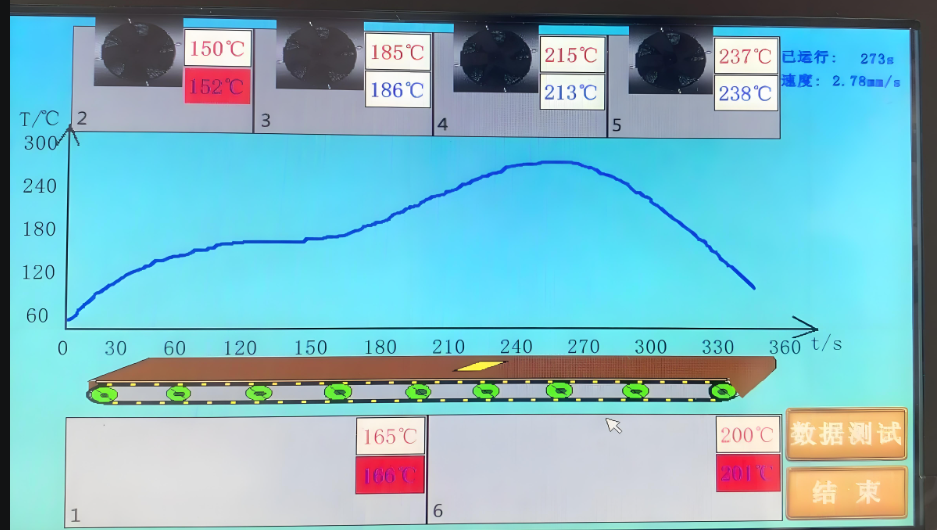
The peak temperature should not exceed the maximum rating of components, and the time above liquidus (TAL) must be kept short to avoid damaging the board.
2. Wave Soldering
Wave soldering is widely used for through-hole assemblies and some mixed-technology PCBs. The board passes over a wave of molten solder.
- Lead-Based Solder: 245°Câ255°C
- Lead-Free Solder: 260°Câ270°C
Before reaching the solder wave, the PCB is preheated to about 100°Câ150°C to prevent thermal shock and improve solder wetting. Flux is applied before the preheat stage to clean and prepare pads.
3. Hand Soldering
Hand soldering is still widely used in prototyping, repair work, or in low-volume custom assemblies. It uses a soldering iron with a temperature-controlled tip. Recommended tip temperatures:
- Lead-Based Solder: 330°C to 370°C
- Lead-Free Solder: 350°C to 400°C
While this may seem high, actual contact time is very short (1â3 seconds). A good soldering station will allow precise control and thermal recovery. Operators must avoid overheating pads or components.
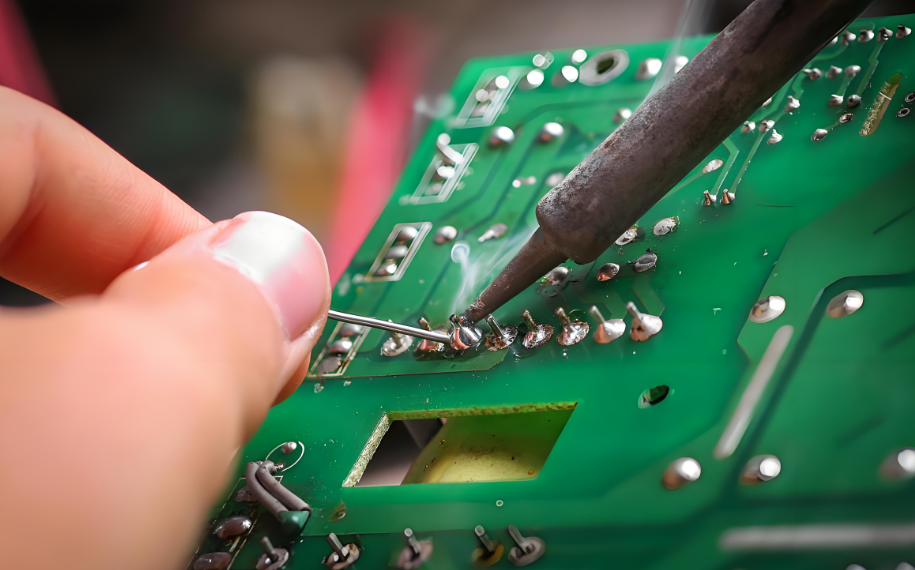
Does the PCB Material Affect Soldering Temperature?
YesâPCB material plays a major role in how much heat it can tolerate.
FR-4 (Standard)
- Can handle up to 260°C for short durations
- Common for most consumer and industrial PCBs
High-Tg FR-4
- Higher glass transition temperature (Tg ~170°C to 180°C)
- More stable under high thermal stress
- Ideal for lead-free soldering or multilayer boards
Ceramic PCBs (Alumina, Aluminum Nitride)
- Extremely high thermal stability
- Can endure 300°C+ without damage
- Requires more precise soldering to avoid cracking
Metal Core PCBs (Aluminum, Copper Core PCB)
- Withstand up to 260°C for short durations
- High thermal conductivity due to the metal core
- Used in: Power electronics, lighting, and automotive control
Aluminum boards dissipate heat quickly, which helps during soldering. However, the uneven expansion between the metal and dielectric layer requires careful control to avoid mechanical stress during reflow.
Flex Circuits (Flexible PCBs)
- Max soldering temperature: Typically <250°C
- Material: Polyimide or PET base
- Critical risk: Heat can distort, shrink, or damage traces
Flexible PCBs are more heat-sensitive than rigid boards. The polyimide or PET base can tolerate soldering but has lower thermal mass, which means it heats upâand cools downâfaster. Excessive temperature or contact time can easily cause:
- Wrinkling or warping
- Delamination of copper traces
- Tearing at bend areas
When soldering flex circuits:
- Use lower reflow peak temperatures, typically not exceeding 240°Câ245°C.
- Apply thermal barriers or stiffeners in vulnerable areas.
- Ensure the heating and cooling are gradual to prevent mechanical stress.
Flex PCBs often use selective soldering or low-temperature solders to reduce heat exposure. In some cases, hot-bar soldering or laser soldering is used for better temperature precision.
Common Soldering Issues Related to Temperature
Issue | Cause | Prevention |
Cold joints | Temp too low | Raise temperature or improve heat transfer |
Component damage | Temp too high or too long | Shorten dwell time, use proper profiling |
Solder bridges | Excess solder, poor control | Use precise stencil and paste volume |
PCB delamination | Overheating | Stay below boardâs Tg and Td |
Cracked joints | Thermal shock during cooling | Use controlled cooling stage |
Why Choose Best Technologyâs PCB Soldering Service?
At Best Technology, we ensure every PCB assembly follows strict soldering standards. Our team uses professional thermal profiling tools to fine-tune the temperature curve for each product.
We support:
- RoHS-compliant lead-free soldering
- Lead-based solder for specialized industries
- High-Tg and ceramic PCBs
- Automated reflow and wave soldering
- Manual soldering by IPC-trained operators
Suppose you have any questions about our products and service, price, MOQ, delivery, location, quality standards, certificates, engineering support and so on. We offer engineering support, thermal profiling, and high-quality PCB manufacturing for all your assembly needs. Please contact us freely any time. We aim to be the best PCB manufacturers in China to supply our customers with the best quality, price, and services. Contact us right now to discuss your next PCB project or to request a quote!
FAQs
1. What is the ideal soldering temperature for lead-free solder?
A peak reflow temperature of 245°Câ250°C is typical. Manual soldering may require a tip temp of 350°Câ370°C.
2. Can I use the same temperature for leaded and lead-free solder?
No. Lead-free solder needs a higher temperature due to its higher melting point.
3. Will high soldering temperatures damage my PCB?
If temperatures are too high or sustained too long, they can cause delamination, burnt pads, or component failure. Use proper profiling.
4. Whatâs the difference between peak temperature and tip temperature?
Peak temperature is the highest board temp during reflow. Tip temperature is the ironâs surface heat during manual soldering.
5. How can Best Technology help with soldering specifications?
We provide detailed thermal profiles, component-safe soldering, and high-reliability assembly for all PCB types.