When creating modern electronic devices, every step matters â from the first sketch to the final product. If you’re exploring the process of printed circuit boards, or PCBs, this guide is your one-stop resource. Weâll walk through PCB design, fabrication, assembly, and testing, covering what engineers and buyers need to know. Whether you’re designing your first board or sourcing from a manufacturer, getting each step right ensures performance, reliability, and cost-efficiency.
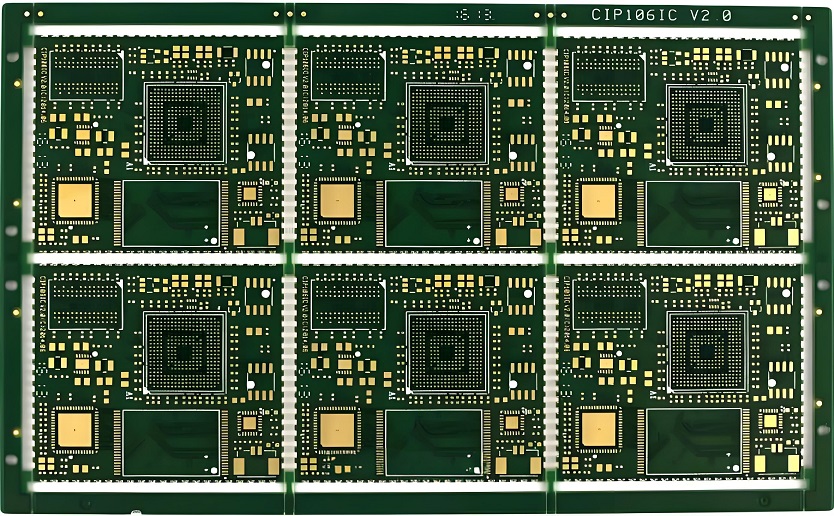
What Is a Printed Circuit Board?
A printed circuit board (PCB) is the backbone of nearly all electronic systems. Itâs a flat board that holds and connects electronic components using conductive tracks, pads, and vias etched from copper sheets laminated onto a non-conductive substrate. Common materials include FR4, ceramic, aluminum, and polyimide.
PCBs come in many forms: single-sided, double-sided, and multilayer PCB, supporting everything from simple gadgets to complex military electronics. Their role is simple yet critical: provide physical support and reliable electrical connections.
How to Design a PCB Board?
The PCB design phase sets the tone for the entire lifecycle. It begins with defining the schematic, which maps out the electronic connections between components. Once thatâs ready, designers move to layout â placing components and routing traces.
Key steps include:
- Creating schematics using software like Altium Designer, KiCAD, or Eagle.
- Assigning footprints to components for proper placement.
- Defining board dimensions, layer stack-up, and signal flow.
- Routing signals with attention to trace width, impedance, and clearance.
- Adding vias, copper pours, and power planes for optimal performance.
- Design Rule Check (DRC) to verify spacing, trace width, and other constraints.
- Generating Gerber files, which are the manufacturing blueprints.
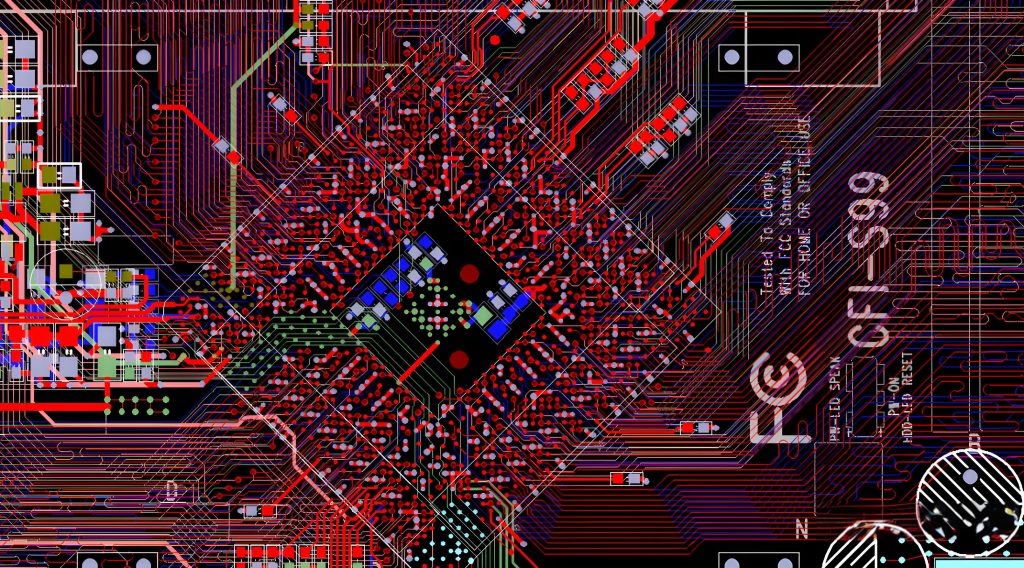
Each design must balance space, power, heat, cost, and manufacturability. One overlooked detail could delay your entire project.
Considerations During PCB Design Phase
Designers must juggle multiple variables beyond schematic accuracy. Here are essential considerations to optimize performance and reduce failure risks:
1. Component Placement: Keep analog, digital, and power circuits separate to reduce interference. Group related components logically to minimize trace lengths.
2. Signal Integrity: For high-speed designs, impedance matching, differential pair routing, and minimizing crosstalk are vital.
3. Thermal Management: Use thermal vias, copper pours, and heat sinks to handle heat dissipationâespecially in power electronics.
4. Design for Manufacturability (DFM): Ensure trace width, drill sizes, and clearances match manufacturer capabilities.
5. EMC and EMI Compliance: Ground planes, shielding, and filtering components help meet regulatory standards.
6. Mechanical Constraints: Donât overlook mounting holes, connector alignment, or enclosure fit. These small details can turn into costly errors later.
Good design minimizes rework, improves lifespan, and lowers costs across production.
Full PCB Fabrication Process â Step by Step
Once the design is complete, the PCB fabrication process turns digital files into a tangible board. Hereâs how it happens:
1. Material Selection
The manufacturer selects base materials like FR4, aluminum, or ceramic depending on thermal, mechanical, and electrical requirements.
2. Inner Layer Imaging (for Multilayer PCBs)
Each inner copper layer is patterned with the circuit using photoresist, UV exposure, and etching techniques.
3. Lamination
The etched inner layers are stacked and laminated under heat and pressure, forming a solid multilayer structure.
4. Drilling
Holes are drilled to create vias for electrical connections between layers. Laser drilling is used for microvias.
5. Plating and Copper Deposition
Holes are plated with copper using electroplating to ensure conductivity across layers.
6. Outer Layer Imaging
Outer copper layers are patterned similar to the inner layers using photoresist and etching.
7. Solder Mask Application
A solder mask is applied to insulate the board and protect traces, leaving pads and holes exposed for soldering.
8. Silkscreen Printing
Component labels, logos, and reference indicators are printed on the board.
9. Surface Finish
A surface finish like HASL, ENIG, OSP, or Immersion Silver is applied to exposed copper pads to protect them and improve solderability.
10. Electrical Testing
Flying probe or bed-of-nails tests check for open circuits and shorts.
Common PCB Assembly Issues During Manufacturing
During PCB assembly, components are mounted and soldered onto the board. This phase can be manual or automated using SMT (surface-mount technology) and THT (through-hole technology).
But several issues can disrupt this process:
1. Tombstoning: A component lifts on one side during reflow, causing connectivity failure.
2. Solder Bridges: Excess solder connects two pins unintentionally, leading to short circuits.
3. Cold Joints: Poor soldering results in weak mechanical bonds and unreliable connections.
4. Misaligned Components: Incorrect placement, often caused by poor paste application or pick-and-place calibration.
5. PCB Warping: Thin or large boards may bend during reflow, affecting soldering and mechanical integrity.
6. Component Damage: Excessive heat or mishandling can destroy delicate ICs or capacitors.
Quality control, professional assembly lines, and well-prepared Gerber + BOM files help avoid these issues.
How to Test Printed Circuit Boards?
After assembly, PCB testing ensures the product works before final integration. There are several testing levels depending on the application and budget:
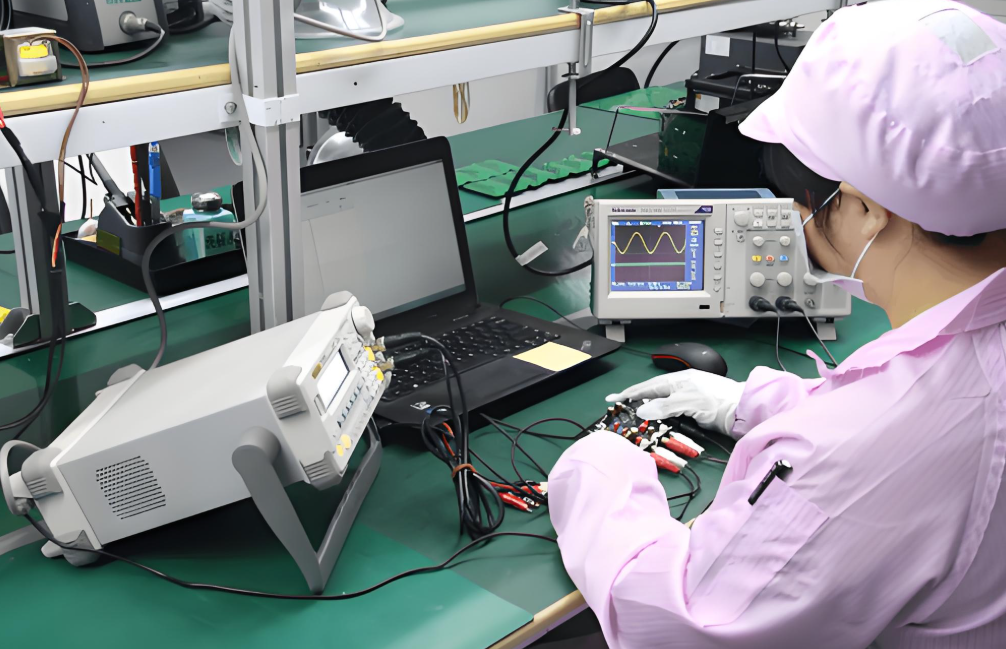
1. Visual Inspection
The simplest method. Engineers check for physical defects like solder bridges, missing components, or alignment issues.
2. Automated Optical Inspection (AOI)
AOI uses cameras to scan boards for soldering quality, polarity, and presence of components.
3. In-Circuit Testing (ICT)
Tests each component’s electrical characteristics by probing specific test points. It’s fast and accurate for large-volume production.
4. Flying Probe Testing
Uses robotic probes to test low-to-medium volume PCBs without the need for custom fixtures.
5. Functional Testing (FCT)
Verifies the complete assembled PCB in real-world operating conditions. Essential for high-reliability applications.
Testing isn’t optionalâit’s critical. Faulty boards cost time, money, and customer trust.
Why Consider Best Technologyâs Turnkey Service?
If youâre tired of juggling multiple vendors for PCB design, fabrication, assembly, and testing, Best Technology offers a full turnkey PCB service that simplifies the process.
Hereâs why clients worldwide trust us:
â Technical Support Before & After Sales
â Prototype & Small Volume Welcome
â Quick Turn-out, On-time Delivery
â High Quality, Special Request Available
â Strong R&D Team, Know How-To
â Rich Experience (>13 Years)
â Prompt Feedback (within 12H)
â One-stop Service (PCBA/Assembly)
Conclusion
Printed circuit boards are at the heart of modern electronics, and getting the design, fabrication, assembly, and testing right is non-negotiable. Each step has its roleâand skipping or rushing any part can lead to costly failures.
Whether youâre building a simple sensor or a complex industrial controller, choosing a partner like Best Technology can make the journey smoother. We understand what engineers, startups, and procurement teams need: fast delivery, quality control, and transparent communication.
FAQs
1. What software is used to design PCBs?
Tools like Altium Designer, Eagle, KiCAD, and OrCAD are commonly used for schematic and PCB layout.
2. How long does PCB fabrication take?
Standard fabrication takes 3â7 days. Express services can deliver in 24â48 hours depending on complexity.
3. What is the difference between PCB and PCBA?
PCB is the bare board. PCBA is the board after components are assembled and soldered.
4. How much does PCB assembly cost?
Costs vary based on quantity, complexity, part types, and whether parts are sourced by the manufacturer or supplied by the customer.
5. Does Best Technology support low-volume PCB manufacturing?
Yes. We support both low and high-volume production and offer prototyping services for new designs.