Bus bar thick copper solution is essential for handling high currents in PCB designs. Standard copper traces often struggle with power distribution, leading to heat buildup and inefficiencies. This is where solderable PCB bus bars come inâthey offer lower resistance, better heat dissipation, and improved mechanical strength compared to standard traces. Best Technology is a trusted leader in providing advanced bus bar thick copper solutions, with over 18 years of experience in producing high-quality PCBs for diverse applications.
But what exactly is a busbar PCB? How does thickness affect performance? What materials and coatings are best? This article answers these questions and more, helping you choose the right solution for your application.
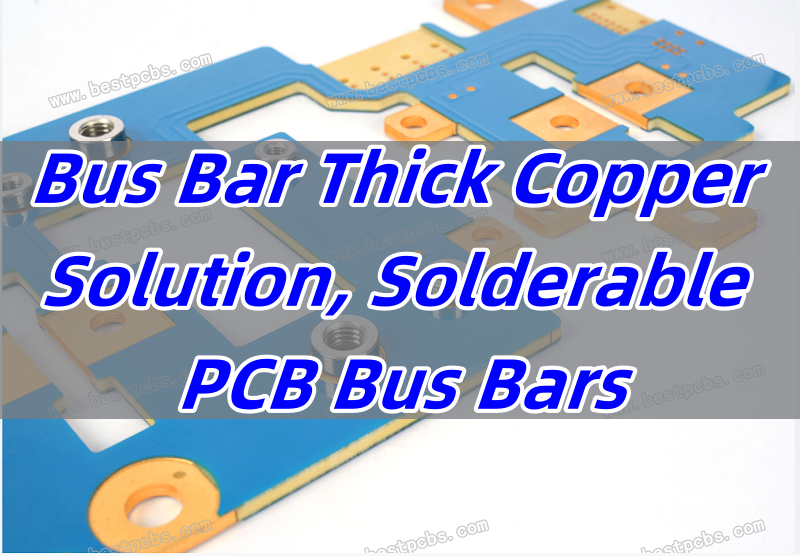
What is a Busbar PCB?
A busbar PCB is a circuit board that includes a thick copper busbar to distribute current efficiently. Unlike standard copper traces, a busbar provides a solid and stable electrical connection, making it perfect for power electronics, inverters, and high-current applications.
In traditional PCBs, thin copper layers handle electrical signals, but high-current circuits demand thicker conductors to prevent overheating. This is why pcb busbars are usedâthey significantly reduce resistance, improve power handling, and enhance overall reliability.
Additionally, different types of busbars exist based on mounting style, such as:
PCB stiffener busbars â Add structural strength to the board.
PCB mount bus bars â Designed for easy attachment to circuit boards.
SMD bus bars â Surface-mount busbars for compact electronic designs.
SMT bus bars â Ideal for automated assembly processes.
Each type offers unique benefits depending on the application.
What is the Thickness of Copper Busbars?
The thickness of a copper busbar depends on the current load and heat dissipation requirements. Common thicknesses range from:
0.5 mm to 1 mm for low-power applications.
1 mm to 3 mm for medium-current circuits.
3 mm to 5 mm or more for high-current industrial applications.
A thicker pcb busbar means lower electrical resistance and better thermal performance, ensuring that the PCB operates efficiently without overheating.
What Copper Material is Used in Bus Bars?
Copper busbars need to be highly conductive and durable. The two most commonly used copper types are:
Electrolytic Tough Pitch (ETP) Copper (C11000) â The most widely used type, with 99.9% pure copper content, offering high electrical and thermal conductivity.
Oxygen-Free High-Conductivity (OFHC) Copper (C10200) â Contains even fewer impurities, making it more resistant to oxidation and ideal for high-performance applications.
Both materials are excellent for pcb mount bus bars, but OFHC copper is preferred when superior conductivity and durability are required.
What Grade of Copper is Used in Busbars?
Copper busbars typically use C11000 or C10200 copper, both of which are high-purity grades. C11000 is more cost-effective, while C10200 offers better oxidation resistance and is used in demanding environments.
For solderable pcb bus bars, copper should have a smooth surface and be compatible with tin or silver coatings for improved solderability.
What is the Coating on Copper Bus Bars?
Copper busbars are coated to prevent oxidation and enhance conductivity. Common coatings include:
Tin â The most common coating, offering corrosion resistance and easy soldering.
Silver â Improves conductivity and is often used in high-frequency applications.
Nickel â Increases durability and is used in harsh environments.
Among these, solderable busbars often feature tin coating, which balances protection, conductivity, and ease of assembly.
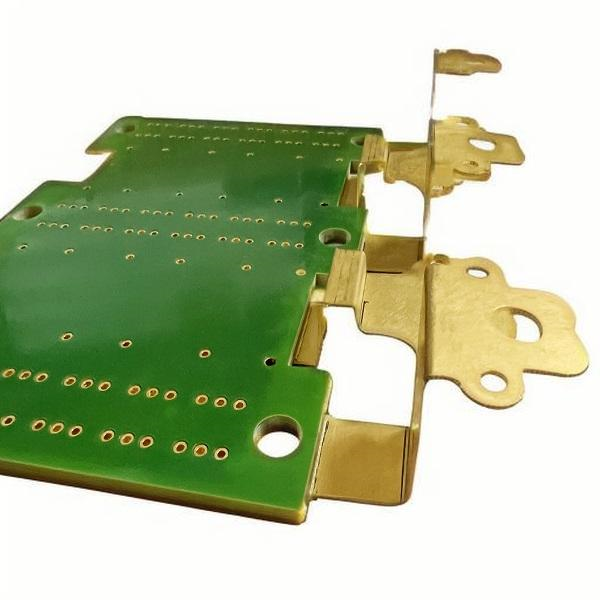
How Thick is the Tin Coating on a Busbar?
Tin coatings on busbars typically range from 1 to 10 microns.
1-3 microns â Suitable for standard applications.
5-10 microns â Used in harsh environments for added protection.
A properly coated solderable busbar prevents oxidation while maintaining good solder adhesion.
How to Join a Copper Busbar?
There are several methods to join copper busbars in PCBs:
Soldering â The most common method for solderable pcb bus bars, ensuring a strong electrical connection.
Brazing â Uses a filler metal to bond busbars at higher temperatures, creating a stronger joint.
Bolting â Allows for easy disassembly and maintenance but may increase contact resistance.
Welding â Used for permanent, high-strength connections, ideal for high-power circuits.
Choosing the right method depends on electrical, mechanical, and thermal considerations.
Why is a Busbar Not Insulated?
Many copper busbars are left uninsulated to improve heat dissipation. Since busbars handle high currents, insulation could trap heat, affecting performance.
However, some applications require insulation to prevent short circuits. In such cases, materials like PVC, epoxy, or heat-shrink tubing are applied.
Can You Bend Copper Busbars?
Yes, copper busbars can be bent to fit PCB layouts. However, bending must be done carefully to prevent:
Cracks â Too much force can damage the copper.
Stress points â Overbending weakens conductivity.
Incorrect alignment â Poor bending can affect PCB assembly.
The key is using a proper bending radius to maintain mechanical strength and conductivity.
What Are the Advantages of Using Copper Bus Bars in PCBs?
Copper busbars provide several benefits in PCBs, including:
Lower electrical resistance â Reduces energy loss.
Better heat dissipation â Keeps components cool.
Stronger mechanical structure â Increases durability.
Compact design â Simplifies PCB layout.
For high-power applications, a bus bar thick copper solution is essential for efficient and reliable performance.
How Do Solderable PCB Busbars Differ from Other Types?
Unlike press-fit or bolt-on busbars, solderable busbars are designed for direct PCB mounting. They have a tin coating for better solderability, making them ideal for surface-mount applications (SMD bus bar, SMT bus bar), compact, high-current PCB designs, and automated assembly processes. They ensure a stable electrical connection, reducing contact resistance and improving longevity.
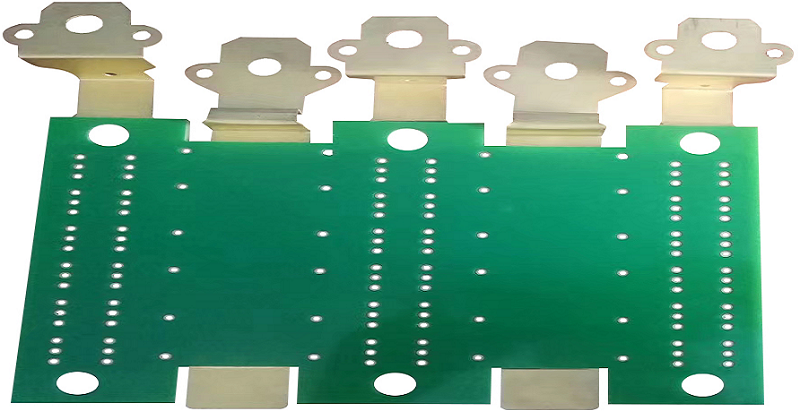
To sum up, a A bus bar thick copper solution enhances PCB reliability and efficiency. Selecting the right bus bar thick copper solution is crucial for high-power PCB designs. Whether using solderable pcb bus bars, pcb mount bus bars, or smd bus bars, choosing the right thickness, material, and coating ensures better efficiency and durability.
For businesses seeking high-performance busbars, working with an experienced manufacturer ensures the best results. With the right choice, power electronics, renewable energy systems, and industrial applications can achieve better performance, lower energy loss, and improved reliability. If youâre looking for high-quality PCB busbars, get in touch with Best Technology at sales@bestpcbs.com to explore the best bus bar thick copper solutions for your need. Our focus on innovation and customer satisfaction ensures we deliver reliable, efficient, and cost-effective copper bus bar solutions tailored to meet the unique needs of the electronics industry.