Robotic aluminum PCB is indispensable in the PCB robot for its high-quality heat dissipation, stable structure, high-density current load, and light weight. In this blog, we will write the critical information, including definition, features, design, price, quality factors, and where to get fast delivery and reliable service.
Do you face the following challenges in your daily project work?
- Poor Manufacturing Efficiency and Long Lead Time?
- Unstable Material Performance and Process Problem?
- Design and Manufacturing Complexity?
- Automation and Integration Problem?
Here are some good angles for Best Technology to tackle these concerns.
- Optimizing the manufacturing process and the supply chain management: Best Technology uses the automation equipment and the cutting-edge management system to improve manufacturing efficiency. For the supply chain, we have stable suppliers to ensure your material supply is on time, stable, and has no unnecessary stock costs.
- Improving the material and the process level: We choose high-quality and better-performing materials to ensure there is no problem caused by the materials during manufacturing. Besides, we employ sophisticated manufacturing processes to improve the performance and the reliability of your products.
- Strengthening the automation and the integration capability: We purchase the advanced automation equipment to improve our production efficiency, PCB quality, and the manufacturing fineness. We provide an integrated service to our customers, such as prototype, mass production, SMT, and box build.
- Strengthening the communication with the customers: We get the customers’ needs and the feedback to adjust our manufacturing plan and the product design in time, which aims to improve customer satisfaction. And we provide the technical support and the after-sales service. Some regular customers have been cooperating with us for over 10 years due to our professional commitment to their projects.
What is a Robotic Aluminum Substrate PCB?
It is valuable to note that a robotic aluminum substrate PCB is an aluminum substrate printed circuit board, designed for robot system optimization that requires high thermal conductivity, excellent mechanical strength, and stable performance under dynamic loads. Its core feature is that it achieves heat dissipation effectively and a mechanical strength balance via the aluminum core substrate layer.
- First, it has three compound structures, such as the circuit layer, insulated layer, and the aluminum core substrate layer. Moreover, it achieves the conductivity of the layers via an insulated resin filling.
- Second, it is vital to note that the robotic aluminum substrate PCB has excellent heat management capability. Compared to the FR-4 substrates, aluminum PCBs can reduce power device temperature rise by 40-60%. Besides, it has nice mechanical adaptation. Its flexibility is 8-10 times that of the ceramic substrate.
- Finally, it is worth mentioning its wide application, such as the servo drive system, joint control module, and environmental sensing unit.
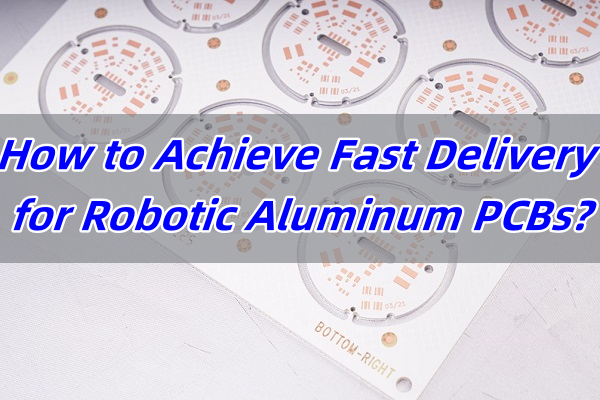
What are the Features of the Robotic Aluminum Substrate PCB?
The features of a robotic aluminum substrate PCB are tailored to meet the unique demands of robotics applications:
- High thermal conductivity ā vital for high-power components and LED modules.
- Mechanical strength ā handles vibration and shock without delamination.
- Application adaptation ā It is specifically designed to tackle the robot core components optimization of the servo drive system, joint control module, and environmental sensing unit.
- Environment Stability ā Its withstand voltage of the insulated layer is more than 3000V. Besides, it can keep dielectric stability under a humidity rate 85%.
- Customizable layer stack-up ā supports single-layer or multi-layer designs based on complexity.
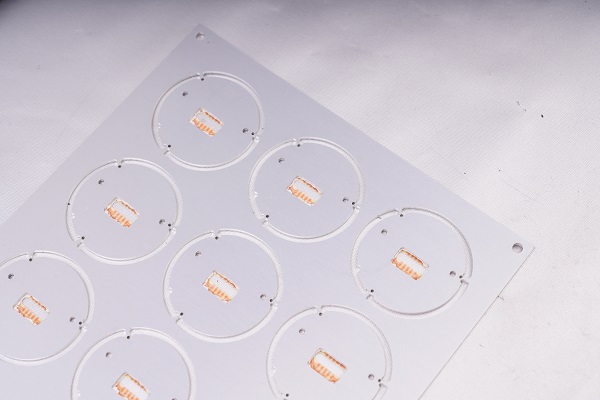
What is the Robotic Aluminum Substrate PCB Price?
The price of a robotic aluminum substrate PCB depends on several factors:
- Base material grade ā higher conductivity aluminum costs more but offers superior performance.
- Board size and thickness ā larger or thicker boards require more raw material.
- Layer count ā multi-layer designs increase manufacturing complexity.
- Surface finish type ā ENIG, HASL, and other finishes have different costs.
- Order volume ā higher quantities often lead to lower per-unit pricing.
There is no MOQ requirement in Best Technology. We produce the order quantity from robotics PCB design, prototype, mass production, and mid-volume robotics PCB assembly to high-volume robotics PCB assembly. We have the integrated production and SMT lines, which help to shorten the delivery time significantly without risking the quality.
What are the Major Considerations in Robotics PCB Design?
It is good to note that the major considerations in robotics PCB design include four aspects.
- The first factor is the signal completeness optimization. It is necessary to plan the route line to design the low impedance return current path, so as to reduce the EMI radiation. Since gaps in ground planes force return currents of microstrip lines to detour.
- The second critical factor is the mechanical reliability design. High-density via areas require via-in-pad or back-drilling processes to reduce the risk of solder joint fatigue caused by the CTE mismatch.
- The third important factor is the environmental adaptation. It is essential to take the conformal coating for the surface or making the micro-arc oxidation treatment.
- The final vital point is the manufacturability balance. The double-sided board can take the 5-layer structure: copper foil, aluminum substrate, insulation, copper foil, so as to balance the complexity and the costs.
How to Ensure the Quality During the Robot PCB Assembly?
It is required to take the following major measures to ensure the robot PCB assembly.
- First, the high-frequency signal lines require impedance-matching design, such as equal-length routing for differential pairs.
- Second, the major connection position uses the high-reliability solder material, such as SAC305 alloy.
- Third, it is vital to control the process and do the inspection. It is critical to use the AOI and X-ray to inspect the soldering quality. And it needs to control the size tolerance with 0.8mm and the assembly tolerance with 1.5mm, so as to reduce the rate of defects. And the industrial robot needs to do the tests, including vibration, temperature, and humidity cycle, etc.
- Finally, it is better to do the DFM analysis during the design phase to avoid the process conflicts.
How to Achieve Fast Delivery for Robotic Aluminum PCBs?
Metal core manufacturers maintain the consistency of fast delivery, which means a lot to the customers. And hereās how itās done:
- Material readiness ā keeping high-demand aluminum substrates in stock eliminates waiting for raw material procurement.
- Concurrent engineering ā design and manufacturing teams work together to spot issues before production starts.
- Automated processes ā using PCB assembly robots and inline inspection systems reduce human error and rework.
- Efficient logistics ā shipping partnerships that offer priority handling for international deliveries.
Best Technology insists on the policy of customer first. We know that customers winning the project and delivering the order to us for manufacturing is a trust in us. We are never stopping to improve our manufacturing process and using advanced manufacturing technology to improve the lead time. Customers avoid the common problem of weeks-long waiting times that slow down product launches.
Where to Get the Best Robotic Aluminum Substrate PCB and assembly from China?
Best Technology addresses customers’ concerns and maintains a long-term relationship by combining:
- Certifications ā ISO9001, ISO 13485 (medical), IATF 16949 (automotive), and AS9100D (aerospace).
- Full in-house process ā from aluminum PCB manufacturing to high-volume assembly. That helps to shorten the PCB manufacturing lead time.
- Professional engineering support ā DFM (Design for Manufacturability) review before production.
- Comprehensive PCB Option ā Our company started to specialize in manufacturing PCBs in 2006. We have a full product profile, such as rigid, flexible, aluminium PCB board for LED, PCB robotics, and ceramic PCB to meet different needs from customersā projects.
If you need to purchase the excellent quality robotic aluminum substrate PCB, just feel free to find Best Technology to do the full support.
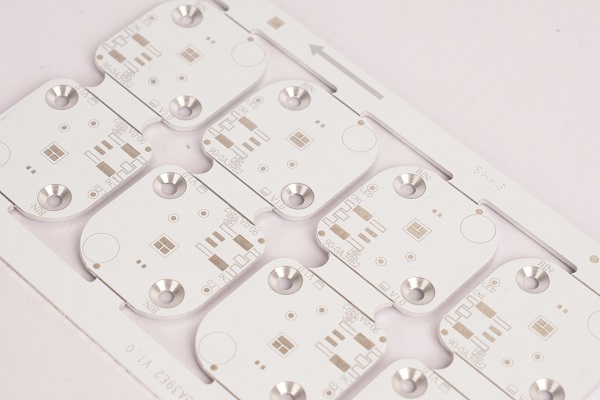
In summary, knowing what the robotic aluminum PCBs are and getting a deep understanding of the design, price, quality factor, and where to get the fast aluminium substrate PCB will help you work faster and work more effectively when you get the robotics PCB design project or mid-volume robotics PCB assembly order. Pls write an email to us at sales@bestpcbs.com to get a viable and specific solution for your PCB robotics.