Have you ever faced such problems when design a PCB that used in high speed application?
- Is your high-speed design bleeding signal strength?
- How to solve poor thermal management in high-frequency systems to ensure stability and reliability?
- How to effectively suppress severeEMI and meet EMC standards in high-frequency circuits?
At Best Technology, we fabricate high frequency PCB that can solve these problems. We use:
- High quality materials with low loss and better shielding performance.
- Utilize ground via array, densely arranging ground vias around radiation sources such as microstrip lines to form a “wall”.
- Design multi-layer boards and adopt dedicated ground layers through reasonable stack-up design, provide a complete reference ground plane for high-frequency signals.
High frequency PCBs are essential in applications such as automotive radar, aerospace communication, medical imaging, 5G and satellite systems. These boards must handle signals above 100 MHz and, in many cases, well into the GHz range. At such speeds, signal losses, impedance mismatches, and electromagnetic interference (EMI) can cause severe degradation. Best Technology, a leading expertise in high frequency pcb manufacturing, can help to optimize your design and manufacture such board for you!
What is a High Frequency PCB?
A high frequency PCB is a printed circuit board designed to transmit signals above 500 MHz, often extending into 10 GHz, 30 GHz, or even higher depending on the application. Some applications, like automotive radar, require PCBs that perform stably at 77 GHz or more.
These boards are not limited to one sector. They are used in:
- Wireless base stations and antennas
- Radar for defense and vehicles
- Satellite communication modules
- High-speed computing and servers
- Precision medical imaging devices
The key challenge is that as frequency rises, signals become more vulnerable to losses, reflections, and interference. A standard FR4 PCB cannot handle these issues beyond a certain point, which is why high frequency laminates and designs are essential.
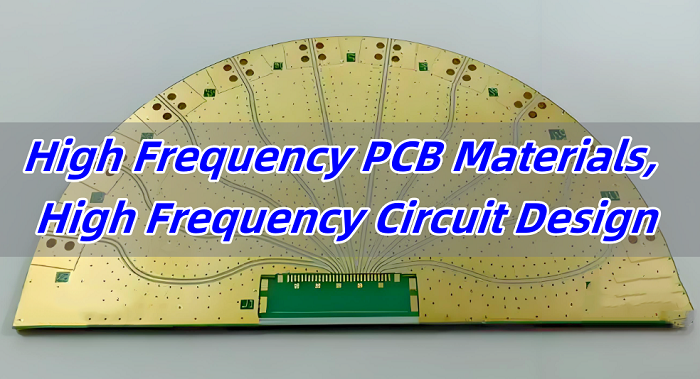
High Frequency PCB Material
The choice of material determines how well a PCB will perform in high frequency environments. Engineers usually evaluate three main parameters:
- Dielectric Constant (Dk): This defines how signals propagate through the material. A stable, low Dk improves signal speed and reduces delay.
- Dissipation Factor (Df): Also called the loss tangent, this defines how much energy is lost as heat. Lower values are better for long-distance signal transmission.
- Thermal Performance: Materials must handle fluctuating temperatures without expansion or deformation, especially in aerospace and automotive environments.
Common Materials Used in High Frequency PCB
- PTFE (Teflon-based laminates): Offers extremely low loss and stable dielectric properties. Perfect for microwave and RF circuits, though harder to process during manufacturing.
- Rogers laminates: Popular choices like RO4350B and RO3003 are widely used in communication devices due to their balance between cost and performance.
- Arlon and Taconic: Trusted for aerospace and military-grade systems.
- Ceramic-filled PTFE: Combines the benefits of PTFE with improved thermal stability, suitable for radar and satellite applications.
- FR4: Economical, but only practical for low GHz applications, as losses rise sharply at higher frequencies.
When comparing FR4 to Rogers or PTFE, the difference is like comparing regular tires to high-performance racing tires. Both work, but only one is built for extreme conditions.
What is the Best PCB Material for High Frequency?
The âbestâ material depends on the actual use case. For example:
- Up to 3 GHz: Rogers RO4350B provides stable performance at a manageable cost, widely used in RF applications.
- Microwave range (10â30 GHz): PTFE laminates such as Taconic TLY or Rogers RO3003 give superior low-loss performance.
- 5G antennas: Low Dk and Df materials like Rogers RO4835 are chosen for consistent performance in outdoor environments.
- Automotive radar (77 GHz): Ceramic-filled PTFE materials are the only reliable solution due to their high thermal and frequency stability.
Cost also matters. PTFE offers the lowest insertion loss but requires advanced processing, increasing manufacturing cost. Rogers materials are easier to fabricate and balance cost and performance, which is why they are widely used.
High Frequency PCB Characteristics
High frequency PCBs stand out due to specific characteristics:
- Stable dielectric constant across wide frequencies
- Low signal loss
- Thermal durability
- Controlled impedance
- Dimensional stability
These boards are engineered not just to survive but to deliver reliable, repeatable performance in demanding environments.
High Frequency PCB Design Guidelines
Designing a high frequency PCB is a delicate balance of precision, material choice, and layout strategy. Even small mistakes in design can cause significant signal loss, reflection, or interference at gigahertz frequencies. Below are the key guidelines that engineers follow to ensure high performance.
1. Controlled Impedance Design
At high frequencies, the impedance of each trace must be carefully calculated and maintained. Variations in trace width, thickness, or dielectric spacing can cause reflections and signal degradation. Designers usually rely on simulation software to calculate controlled impedance for microstrip, stripline, or coplanar waveguide structures. The target impedance is often 50Ω for single-ended signals or 100Ω for differential pairs.
2. Minimize Trace Lengths
Signal paths should be as short as possible. Long traces increase insertion loss, cause delay, and may introduce unwanted reflections. In applications like RF communication or 5G antennas, even small increases in trace length can degrade signal integrity significantly.
3. Reduce the Number of Vias
Each via acts as a small inductance and capacitance, which can reflect high-frequency signals. Limiting via usage and optimizing via placement is essential. When vias are unavoidable, designers often use via stitching or back-drilling techniques to reduce parasitic effects.
4. Ground Planes and Reference Layers
A continuous, solid ground plane beneath signal traces improves return paths and minimizes electromagnetic interference (EMI). Multiple ground planes can be used in multilayer boards to enhance shielding and reduce noise coupling. Proper stacking ensures that signal layers are adjacent to reference planes, which stabilizes impedance and improves signal quality.
5. Differential Pair Routing
Differential pairs are widely used in high-speed digital and RF circuits. These pairs carry complementary signals, which improves noise immunity and reduces crosstalk. Designers maintain strict control over trace spacing, length matching, and symmetry to preserve signal integrity.
6. Stack-Up Optimization
The stack-up, or layer arrangement, determines how signal layers, power planes, and ground planes interact. Proper stack-up design can reduce cross-talk, improve thermal management, and control impedance. High frequency PCBs often use hybrid stack-ups with PTFE or ceramic layers to balance performance and manufacturability.
Every decisionâfrom material choice to trace width, via placement to ground plane configurationâdirectly impacts signal integrity. A high frequency PCB is not just about connecting components; it is about managing signals, controlling impedance, and reducing loss to ensure reliable, precise performance in the gigahertz range.
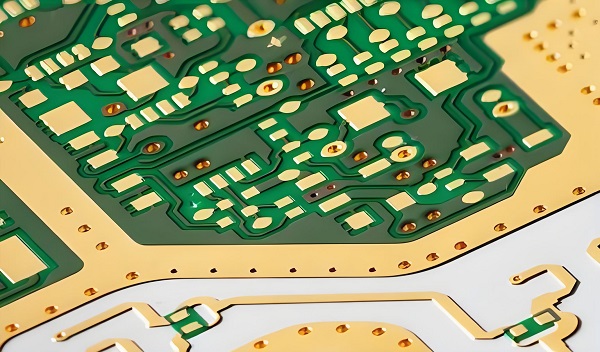
High Frequency PCB Manufacturer â Best Technology
Not all manufacturers are capable of producing high frequency PCBs. Handling PTFE and ceramic materials requires different lamination temperatures, drilling techniques, and plating processes compared with FR4.
At Best Technology, we bring specialized expertise in:
- Fabricating Rogers, Taconic, PTFE, and hybrid PCB stack-ups.
- Maintaining strict dimensional tolerances for impedance control.
- Advanced inspection to measure dielectric thickness, copper roughness, and loss factors.
- End-to-end MES traceability to ensure every board can be tracked back to its source materials and processes.
This combination of material knowledge, certified systems, and engineering support makes Best Technology a trusted partner for customers who need more than just a standard PCB.
Insertion Loss Comparisons of Common High Frequency PCB Constructions
Material | Frequency (10GHz) | Insertion Loss (dB/inch) | Notes |
FR4 | ~10GHz | 0.7 â 1.0 dB | High loss, not recommended |
Rogers RO4350B | ~10GHz | 0.2 â 0.3 dB | Cost-effective, reliable |
Rogers RO3003 | ~10GHz | 0.1 â 0.15 dB | Excellent for microwave use |
PTFE Ceramic | ~10GHz | 0.05 â 0.1 dB | Premium choice for radar/5G |
This table clearly shows why FR4 is avoided for RF designs. At high GHz levels, FR4 can lose more than three times the signal strength compared with PTFE laminates.
High Speed vs High Frequency PCB â What is the Difference?
The terms âhigh speedâ and âhigh frequencyâ are often confused, but they describe different challenges:
- High Speed PCB: Concerned with digital signals, rise times, and data rates. Examples: DDR memory boards, data centers, and Ethernet.
- High Frequency PCB: Concerned with analog and RF signals in the GHz range. Examples: radar, antennas, and satellite communication.
In practice, many designs overlap. For instance, a 5G base station board must support high-speed data processing and high-frequency RF transmission simultaneously. This is why engineers often require both high-speed and high-frequency design expertise.
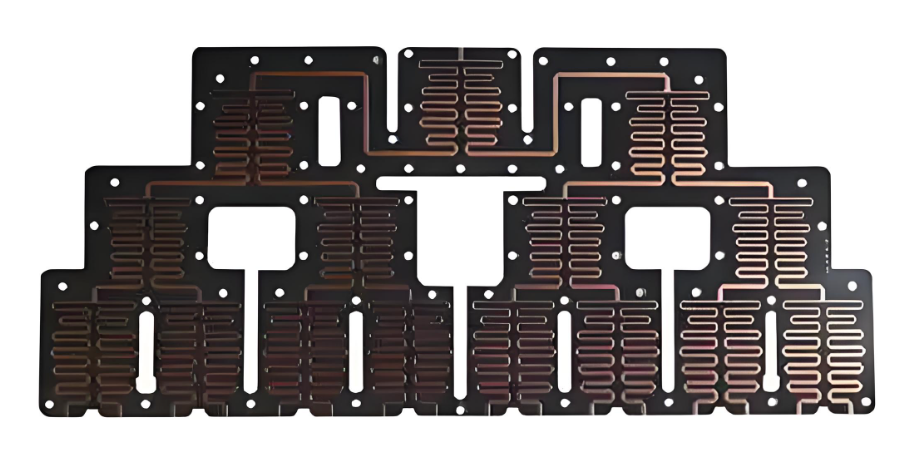
Why Do We Need High Frequency?
High frequency PCBs enable many of the technologies that define modern life:
- 5G base stations and smartphones: Delivering ultra-fast, low-latency communication.
- Automotive radar: Assisting advanced driver-assistance systems and autonomous driving.
- Satellite communication: Providing global coverage for navigation and broadcasting.
- Defense and aerospace: Supporting secure, high-performance radar and communication systems.
- Medical devices: Enabling accurate imaging through MRI, CT, and ultrasound.
Without these boards, the next generation of communication and smart systems would not be possible.
Who Should Not Get High Frequency?
Not every project needs high frequency PCBs. For example:
- A consumer product with simple sensors may not justify the extra cost.
- Low-speed devices below 500 MHz can rely on FR4.
- Cost-sensitive projects without high bandwidth needs should avoid high frequency laminates.
Choosing the right PCB type should always balance performance needs vs. budget.
FAQs
1. What frequency is considered high frequency in PCBs?
Any PCB designed to work above 500 MHz is typically considered high frequency, with advanced boards operating up to 60 GHz or more.
2. How does dielectric constant affect PCB performance?
A stable dielectric constant ensures signals propagate at predictable speeds and maintain impedance control, crucial for RF circuits.
3. Can FR4 be used for high frequency PCB?
FR4 works only up to around 1 GHz. Beyond that, losses become too high for reliable performance.
4. What are the challenges in manufacturing high frequency PCB?
Processing PTFE materials, achieving impedance accuracy, reducing insertion loss, and handling copper roughness are common challenges.
5. How to reduce signal loss in high frequency PCB design?
Use low-loss laminates, design shorter traces, avoid unnecessary vias, and apply smooth copper surfaces to reduce resistance.