Looking for reliable circuit board assembly services? At Best Technology, we provide full-service PCB assembly solutions that include SMT, through-hole, mixed assembly, and turnkey capabilities. Whether you’re building prototypes or going into mass production, we support your project from start to finish with engineering guidance, quality control, and fast lead times.
What Are Circuit Board Assembly Services?
Circuit board assembly services play a crucial role in the electronics manufacturing industry. They involve the process of placing electronic components onto a blank PCB to form a functioning circuit. This process transforms a bare board into a working device. It’s used in every industry that depends on electronics — from smartphones and cars to medical devices and aerospace equipment.
There are three main methods in circuit board assembly:
- SMT (Surface Mount Technology): Components are mounted directly onto the surface of the PCB.
- THT (Through-Hole Technology): Leads are inserted into holes in the PCB and soldered underneath.
- Mixed Assembly: Combines both SMT and THT for boards that require diverse components.
Understanding these methods helps new customers communicate better with suppliers and choose the right assembly process based on the design and function of their product.
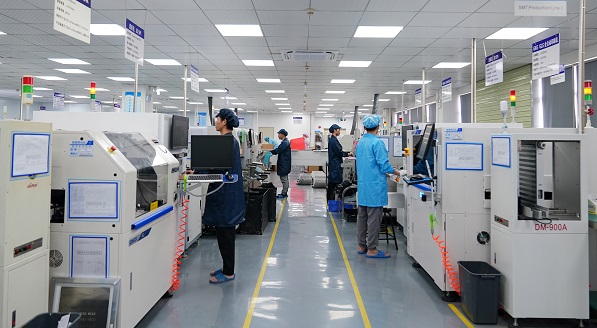
Types of Circuit Board Assembly Methods
Different circuit designs and application needs call for different assembly methods. Here’s a breakdown:
- Surface Mount Technology (SMT)
SMT is the most common technique in use today. Components are placed directly on the PCB surface, enabling smaller designs, higher component density, and faster assembly. Automated pick-and-place machines position these components with high precision. It’s suitable for compact and high-speed devices such as smartphones, tablets, and IoT products.
- Through-Hole Technology (THT)
THT involves placing components with wire leads through pre-drilled holes in the PCB. The leads are soldered on the opposite side. This method offers greater mechanical strength and is often used for components that experience physical stress or need a strong bond, like connectors or transformers. THT is common in industrial and automotive PCBs.
- Mixed Assembly
When a PCB requires both surface-mounted components and through-hole parts, a mixed assembly approach is used. It’s often found in complex designs, especially when different voltage levels or mechanical supports are needed. Mixed assembly offers more flexibility but also requires advanced equipment and careful coordination.
- Dual In-line Package (DIP) Assembly
DIP is a specific type of through-hole assembly method that uses components with two parallel rows of pins (leads). These components are inserted into matching holes on the PCB and are often hand-soldered or wave-soldered. DIP is commonly used for ICs (integrated circuits), microcontrollers, and programmable logic devices during development or low-volume production. While not as compact as SMT, DIP is easier to prototype and replace, making it useful in educational, industrial, and repair applications.
Turnkey vs. Consigned PCB Assembly: What’s the Difference?
When working with an assembly partner, it’s essential to choose the right sourcing model:
1. Turnkey Assembly
In a full-turnkey model, the assembly provider takes care of everything. This includes sourcing components, manufacturing the PCB, assembling parts, testing, and delivery. It’s a hands-off approach for the customer and is preferred by startups or teams with limited resources. It reduces management complexity and lead times.
2. Consigned Assembly
With consigned assembly, the customer provides some or all the components. This is ideal for companies that already have components in stock or require tight control over part sourcing. While it offers flexibility, it also requires more effort from the client to ensure timely material delivery.
3. Partial Turnkey
A hybrid of the two, partial turnkey services split responsibilities — the customer supplies some components, and the assembler handles the rest. This balances control and convenience.
At Best Technology, we offer both full turnkey PCB assembly service and consigned assembly. All of our components are sourced from authorized distributor or digikey, mousers, find chips and so on. We have established stable bussiness relationship with them, so that we can get the best price and shorter lead time.
Key Capabilities of Our Circuit Board Assembly Services
At Best Technology, we bring years of experience and investment in equipment to deliver top-quality PCB assembly services.
1. SMT Line Capability
We operate 4+ advanced SMT production lines capable of handling fine-pitch, small components (as small as 01005) both in China and Vietnam. Each line supports:
- Single- and double-sided placement
- Reflow soldering with nitrogen ovens
- Automatic solder paste printing with SPI (Solder Paste Inspection)
- High-Speed Pick and Place
- Dual online AOI
- X-ray inspect machine for fine pitch BGAs
Our pick-and-place machines operate at speeds up to 80,000 components per hour, providing high efficiency for volume production. These machines offer accurate placement and are suitable for dense and complex boards.
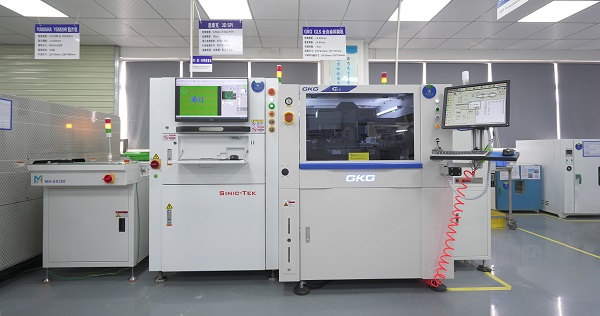
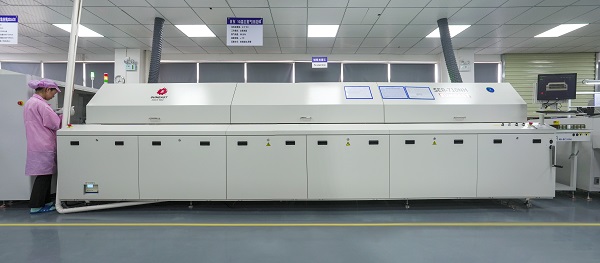
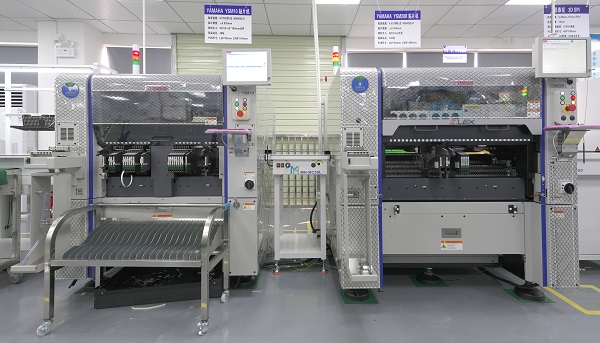

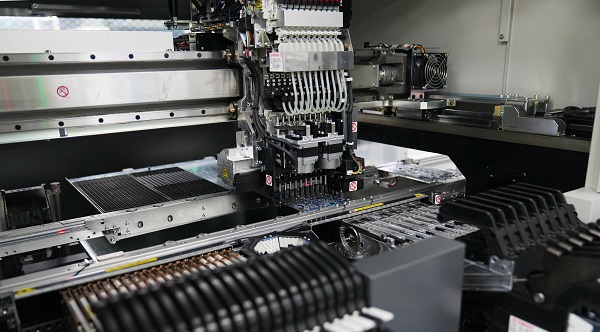

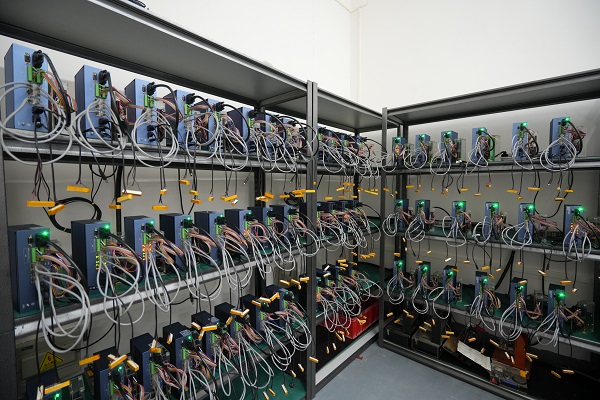
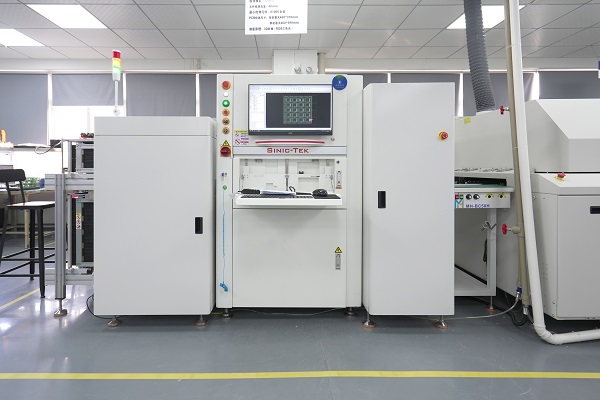
2. Fine-Pitch and BGA Soldering
We’re capable of mounting fine-pitch ICs, BGA, QFN, and other challenging components. Our BGA rework station ensures precise alignment and reliable solder joints — ideal for high-reliability sectors like aerospace and medical.
3. Leaded and Lead-Free Options
We offer both leaded and lead-free soldering, depending on your application and regulatory requirements. All lead-free processes are compliant with RoHS and REACH directives.
4. Component Sourcing and BOM Management Support
Managing the bill of materials (BOM) is one of the most complex parts of circuit board assembly. We simplify this process:
- Global Sourcing Network: We work with trusted distributors like Digi-Key, Mouser, Arrow, and Avnet.
- Alternate Part Suggestion: If parts are obsolete or out of stock, our engineers will recommend alternatives based on functionality and compatibility.
- Cost Control: We offer multiple supplier options and volume purchasing strategies to help reduce costs.
- Inventory Tracking: Our MES system ensures full traceability from incoming materials to final product.
- DFM & DFA checks before assembly with free services
5. Various PCB Assembly Support
We support various PCB assembly, including:
- Rigid FR4 PCB
- Metal core PCB
- Ceramic PCB
- Rigid flex PCB
- Flex circuits
- FR4 PCB with metal dome assembly
- Box building assembly
Whether your project is a prototype or a large batch, we’ll handle procurement smoothly to keep things on schedule.
PCB Testing and Quality Inspection Services
Quality is not just a checkbox — it’s a process. Our multi-stage inspection services help identify issues early and deliver reliable products.
- AOI (Automated Optical Inspection)
AOI checks for soldering defects, missing components, and polarity errors. It’s especially useful for SMT lines and runs on every board before moving to the next step.
- X-ray Inspection
We use X-ray machines to inspect solder joints under BGAs and other invisible parts. This non-destructive method ensures hidden connections are properly made.
- ICT and Functional Testing
We support In-Circuit Testing (ICT) and Functional Testing (FCT) using customer-provided test fixtures or our internal jigs. This verifies each component’s performance and the overall function of the board.
- Visual Inspection (IPC-A-610)
Our trained QC staff visually inspects boards under IPC-A-610 standards, covering cosmetic and dimensional defects.
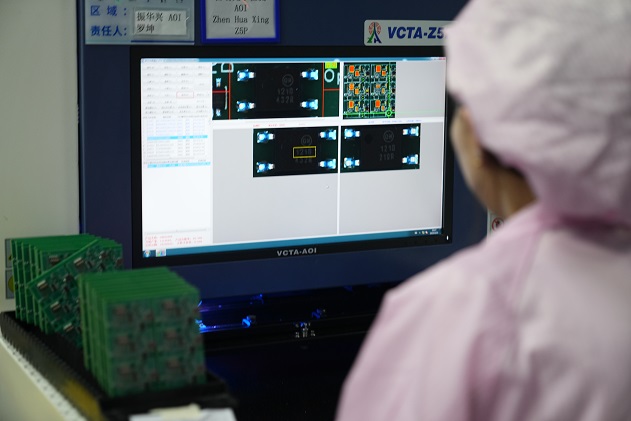
Certifications and Quality Standards We Follow
We understand the importance of compliance. That’s why Best Technology adheres to the following certifications and standards:
- ISO9001: General quality management system for manufacturing.
- ISO13485: Standard for medical device assembly.
- IATF16949: Automotive-grade quality system for reliability and traceability.
- UL Certification: For products entering North American markets.
- RoHS and REACH: Compliance with hazardous substance control.
- IPC-A-610: Acceptance standards for electronic assemblies.
These certifications reflect our commitment to consistent quality and customer satisfaction.
Fast Prototyping and Quick-Turn Assembly Options
Startups, design houses, and R&D teams often need fast iterations. We support quick-turn prototypes with lead times as fast as 24–72 hours, depending on complexity and material availability.
- No MOQ for prototypes.
- DFM (Design for Manufacturability) checks to avoid errors.
- Engineering support to adjust layout and improve yield.
For urgent projects, we offer expedited services at competitive rates. Speed doesn’t mean sacrificing quality — our rapid builds go through the same rigorous inspection process.
Industries We Serve with PCB Assembly Services
Our experience spans multiple industries, each with unique demands:
- Consumer Electronics: Wearables, smart devices, gaming consoles, and home automation.
- Automotive: In-vehicle infotainment, power control modules, and driver-assist systems.
- Medical Devices: Heart rate monitors, wearable health trackers, and diagnostic equipment.
- Industrial Automation: Sensor boards, motor controllers, and factory equipment.
- Aerospace & Military: Avionics modules, communication devices, and tactical systems.
Our engineering team understands the compliance, testing, and documentation needs of each industry, making us a trusted partner.
Why Choose Us for Your Circuit Board Assembly Needs?
At Best Technology, we’re not just a PCB manufacturer — we’re a complete solution provider.
- One-Stop Manufacturing: From PCB fabrication and component sourcing to final assembly and testing.
- Engineering Support: Our team helps you optimize your design for performance and manufacturability.
- Strict Quality Control: We apply multiple checkpoints to ensure every product meets expectations.
- Competitive Pricing: We balance cost, quality, and speed through strategic sourcing and lean manufacturing.
- Global Delivery: Our logistics team ships to over 80 countries with fast turnaround times.
Our approach combines reliability, speed, and technical depth — all under one roof.
How to Get a Quote for Circuit Board Assembly Services?
We make it easy for you to start working with us. Here’s how the quote process works:
- Upload Your Files: Submit your BOM, Gerber files, and assembly drawings via our website or email.
- Engineering Review: Our team will review the files and provide DFM feedback if needed.
- Get a Quotation: You’ll receive a detailed quote within 24–48 hours.
- Sample Production: Once approved, we make a prototype or pre-production sample for confirmation.
- Mass Production: After sample approval, full production begins with agreed lead times.
We’re happy to guide you through the process — whether you’re an experienced engineer or a first-time product developer.
FAQs About Circuit Board Assembly
1. What files do I need to provide for PCB assembly?
You should provide Gerber files, BOM (Bill of Materials), centroid file, and any special instructions or drawings.
2. What’s the minimum order quantity (MOQ)?
We have no MOQ for prototypes. For production orders, we offer flexible quantities based on your needs.
3. Can you source hard-to-find or obsolete components?
Yes. We have strong relationships with global distributors and can help identify substitutes if needed.
4. Do you offer RoHS-compliant lead-free soldering?
Absolutely. We follow RoHS, REACH, and other international standards. Just let us know your preference.
5. What’s your typical lead time for PCB assembly?
Prototypes take 2–5 working days, while volume orders may range from 7 to 15 days depending on complexity.
6. Do you offer testing services for my assembled PCBs?
Yes, we provide AOI, X-ray, ICT, and functional testing depending on your product’s requirements.
7. Can I get help if I’m unsure about my BOM or layout?
Of course. Our engineers can review your files and recommend adjustments to improve performance and reduce cost.
Whether you’re launching a new product or scaling an existing one, Best Technology is ready to support your success with professional circuit board assembly services. From prototype to production, we help simplify the process, reduce your workload, and deliver high-quality results on time.
📩 Contact us now to request a quote or speak to our engineering team.