Looking for high temperature PCB for your project? This article explores high-temperature PCB solutions from material selection to thermal management and cost-performance optimization for harsh environments.
18-Year High Temperature PCB Manufacturing Expert | Rapid Prototyping & Precision Assembly Your Hardware Accelerator!
PCB Manufacturing Service Offered include:
24-Hour Rapid Prototyping: Industry’s Fastest Delivery, 10% Off on Rush Orders
Aerospace Grade Quality Control: 6-Layer HDI Board ±0.05mm Accuracy, 100% AOI Full Inspection
Full-Stack Services: From Design Review to Mass Assembly, Direct Supply from ISO-Certified Factory
Order Now and Get a Free DFM Analysis Report, Making Your IoT/Industrial Control Projects One Step Ahead! Contact us now: sales@bestpcbs.com.
What Is High Temperature PCB?
High temperature PCBs or High Tg PCBs are specialized circuit boards designed to operate reliably in industrial environments with elevated temperatures. These boards utilize thermally stable materials such as polyimide-based substrates and high-temperature laminates that maintain structural integrity and electrical performance at sustained temperatures between 150°C and 250°C.
In industrial control systems, these PCBs feature enhanced copper plating for better heat dissipation and modified dielectric materials that prevent thermal degradation. The manufacturing process incorporates precise thermal management techniques to ensure consistent performance in applications like factory automation, power electronics, and process monitoring equipment.
Their ability to withstand thermal cycling and harsh operating conditions makes them indispensable for industrial applications where standard PCBs would experience premature failure due to heat-related stress or material breakdown. The design considerations include optimized trace layouts and robust interlayer connections to maintain signal integrity under continuous thermal load.
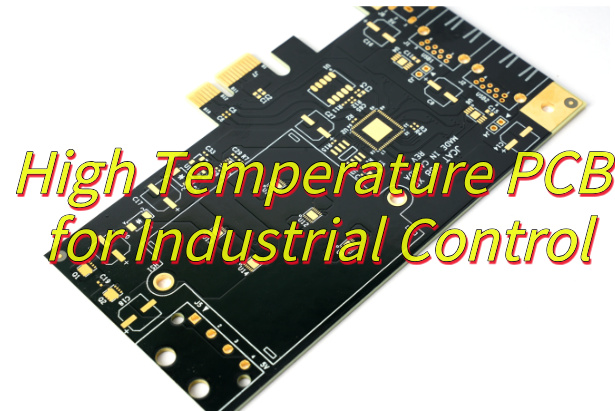
What Is Material of High Temperature PCB?
Material of high temperature PCB:
- Polyimide Resins – The most common base material for high temperature PCBs, offering continuous operation up to 260°C with excellent chemical resistance and mechanical stability.
- Ceramic-Filled PTFE Composites – Provide superior thermal conductivity while maintaining electrical insulation properties, ideal for high-frequency applications in industrial environments.
- High Tg FR-4 Variants – Fiberglass-reinforced epoxy laminates with glass transition temperatures above 170°C, suitable for cost-sensitive applications with moderate heat requirements.
- Thermally Conductive Prepregs – Specialized bonding layers that maintain adhesion at elevated temperatures while facilitating heat transfer between board layers.
- Heavy Copper Foils – Thicker copper layers (2-20 oz) that enhance current carrying capacity and improve heat dissipation across the circuit board.
- High Temperature Solder Masks – Modified coatings that withstand repeated thermal cycling without cracking or discoloration, protecting underlying circuits.
- Metal Core Substrates – Aluminum or copper bases that function as integrated heat spreaders, particularly valuable for power electronics in industrial controls.
- Ceramic Substrates – Used in extreme environments, offering unmatched thermal performance with operating temperatures exceeding 350°C.
- Specialty Thermoplastics – Materials like PEEK and PEI that combine high temperature resistance with chemical inertness for harsh industrial applications.
When to Use High Tg PCB?
Below are when to use high Tg PCB:
- Lead-Free Soldering Processesâ: When manufacturing requires RoHS-compliant lead-free soldering (peak temperatures 250-260°C), standard FR-4 (Tg 130-140°C) risks delamination. High Tg materials (Tg â„ 170°C) maintain structural integrity during repeated thermal cycles.
- High-Power Industrial Equipmentâ: For motor drives, power converters, or servo controllers with concentrated heat generation, high Tg substrates resist warping and prevent copper trace separation caused by prolonged operation above 120°C.
- Multi-Layer Board Designsâ: Complex industrial PCBs with 8+ layers demand high Tg prepregs to withstand lamination temperatures while ensuring interlayer bonding strength, reducing via cracking risks during thermal expansion.
- Harsh Environment Operationsâ: In facilities like foundries or chemical plants where ambient temperatures exceed 100°C, high Tg materials (preferably Tg > 180°C) prevent resin softening and preserve dielectric properties.
- Extended Product Lifespan Requirementsâ: Industrial automation systems with 10+ year service expectations benefit from high Tg PCBsâ slower thermal degradation rates, minimizing insulation resistance decline over time.
- Thermal Cycling Conditionsâ: Applications experiencing frequent temperature fluctuations (e.g., outdoor control cabinets, metal processing machinery) require high Tg substrates to resist cumulative CTE mismatch damage.
- High-Density Component Mountingâ: Boards with fine-pitch BGAs or miniaturized components need high Tg materialsâ superior dimensional stability to maintain alignment during assembly and operation.
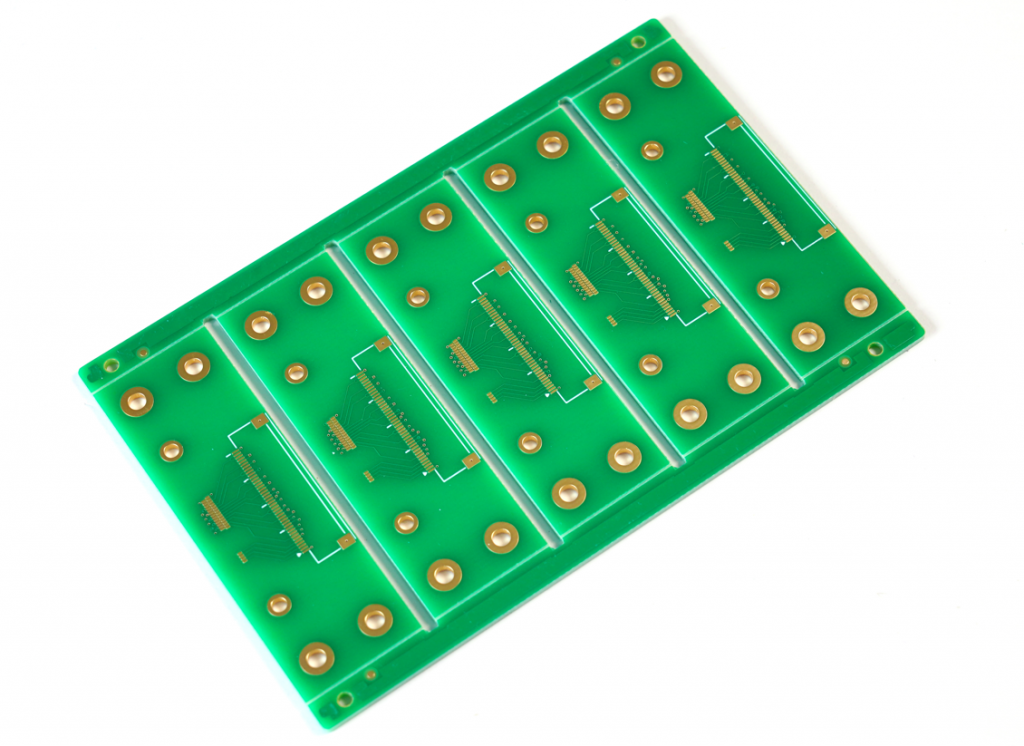
How to Optimize High Temperature PCB Design for Efficient Heat Dissipation?
Methods about how to optimize high temperature PCB design for efficient heat dissipation:
Select Thermally Conductive Substrates
- Use High Temperature PCB Design materials like aluminum-backed or copper-clad laminates to enhance heat transfer away from components. These substrates often feature thermal conductivity ratings exceeding 1.0 W/m·K, significantly reducing hotspot formation in power-intensive industrial controls.
Incorporate Thick Copper Traces
- Design traces with 2â3 oz/ftÂČ copper thickness to minimize electrical resistance and heat generation in high-current paths. This approach is critical for motor drives or power supplies, where thinner traces would otherwise act as focal points for thermal stress.
Strategically Place Heat-Generating Components
- Position components like MOSFETs, diodes, or inductors near thermal vias or metallic cores. Aligning these elements with PCB edges or dedicated heat sinks ensures direct heat dissipation into chassis mounts, preventing thermal runaway in enclosed industrial enclosures.
Leverage Thermal Vias and Ground Planes
- Implement staggered arrays of thermal vias (0.2â0.3 mm diameter) beneath high-power devices to spread heat across inner ground planes. This technique reduces localized temperature spikes by 15â20% in multilayer boards used for factory automation controllers.
Optimize Component Spacing and Airflow
- Maintain minimum clearances of 3â5 mm between heat-sensitive components and heat sources. Pair this with forced-air cooling channels or natural convection pathways to lower junction temperatures by 25â30% in compact industrial IoT gateways.
Use Thermal Interface Materials (TIMs)
- Apply phase-change pads or graphite sheets between PCBs and heat sinks to reduce thermal resistance. TIMs with 3â5 W/m·K conductivity improve heat transfer efficiency in power generation control modules operating at 180°C ambient temperatures.
Simulate and Validate Thermal Performance
- Conduct computational fluid dynamics (CFD) simulations early in the High Temperature PCB Design phase to identify hotspots. Iterate on copper weights, via placements, and component orientations based on simulation data to ensure compliance with industrial thermal standards.
Why Choose High Temperature PCB for Industrial Control?
Reasons why choose high temperature PCB for industrial control:
Uninterrupted Operation in Extreme Heat
- High temperature PCBs ensure industrial control systems function reliably in environments exceeding 150°C, such as near furnaces, engines, or solar inverters. By resisting thermal degradation, they minimize unexpected downtime, directly reducing production losses and maintenance costs.
Extended Service Life
- Materials like polyimide and ceramic-reinforced laminates resist cracking, delamination, and solder joint fatigue under repeated thermal cycling. This durability translates to fewer replacements and lower lifecycle costs for equipment in power plants or automated manufacturing lines.
Stable Signal Integrity
- Dielectric formulations in High temperature PCBs maintain consistent electrical properties despite prolonged heat exposure. This prevents timing errors or data corruption in precision control systems, safeguarding product quality and operational safety.
Resistance to Harsh Chemicals
- Industrial environments often involve oils, solvents, or corrosive gases. High temperature PCBs with chemically inert coatings and sealed edges resist corrosion, reducing the need for protective enclosures and frequent inspections.
Compliance with Safety Standards
- Using high temperature PCBs helps meet stringent industry certifications (e.g., UL 94V-0 for flame resistance) without additional modifications. This streamlines regulatory approvals for medical devices, aerospace components, or heavy machinery.
Cost-Effective Performance at Scale
- While high temperature PCBs may have a higher upfront cost, their ability to withstand thermal stress reduces long-term expenses related to repairs, replacements, and production delays. For high-volume industrial applications, this ROI becomes evident within 2â3 years.
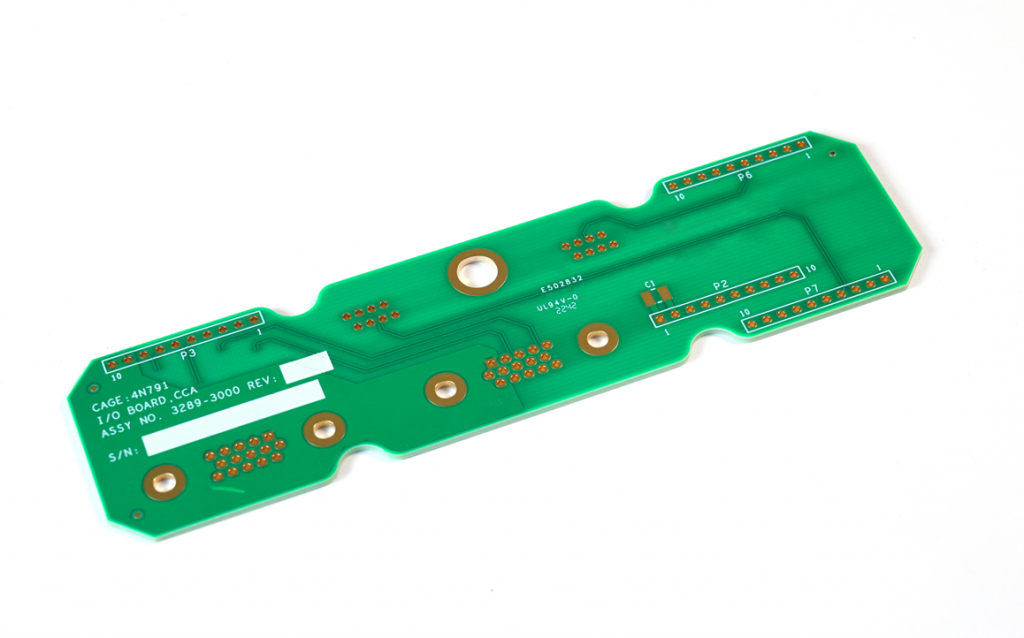
How to Maintain Signal Integrity in High Temperature PCB Board for PLC Control System?
Methods about maintaining signal integrity in high temperature PCB board for PLC control system:
- Select Low-Loss Dielectric Materialsâ: Choose substrates with stable dielectric constants (Dk) and low dissipation factors (Df) across operating temperatures to minimize signal attenuation at high frequencies.
- Control Impedance with Thermal Compensationâ: Adjust trace width and spacing based on material expansion rates at elevated temperatures to maintain consistent impedance (e.g., 50Ω/100Ω differential) throughout thermal cycles.
- Shield Sensitive Signalsâ: Route high-speed traces (e.g., clock lines, RS-485) between ground planes or use guard traces to reduce crosstalk and EMI, which worsen with temperature-induced noise.
- Minimize Via Stubsâ: Use blind/buried vias or back-drilling to eliminate stub effects that cause signal reflections, especially critical in multi-layer designs for PLCs.
- Optimize Power Delivery Networks (PDNs)â: Decouple power rails with high-temperature-rated capacitors (X7R/C0G) placed close to ICs, ensuring stable voltage despite parasitic inductance changes from heat.
- Implement Differential Signalingâ: Prefer differential pairs (e.g., CAN, Ethernet) over single-ended traces to reject common-mode noise amplified by thermal interference.
- Simulate Signal Behavior Under Heat Stressâ: Perform transient thermal analysis combined with SI tools to predict skew, jitter, and eye diagram degradation at peak temperatures.
- Validate with High-Temperature Testingâ: Characterize signal rise times, BER, and crosstalk while operating the PCB at maximum rated temperature to verify real-world performance.
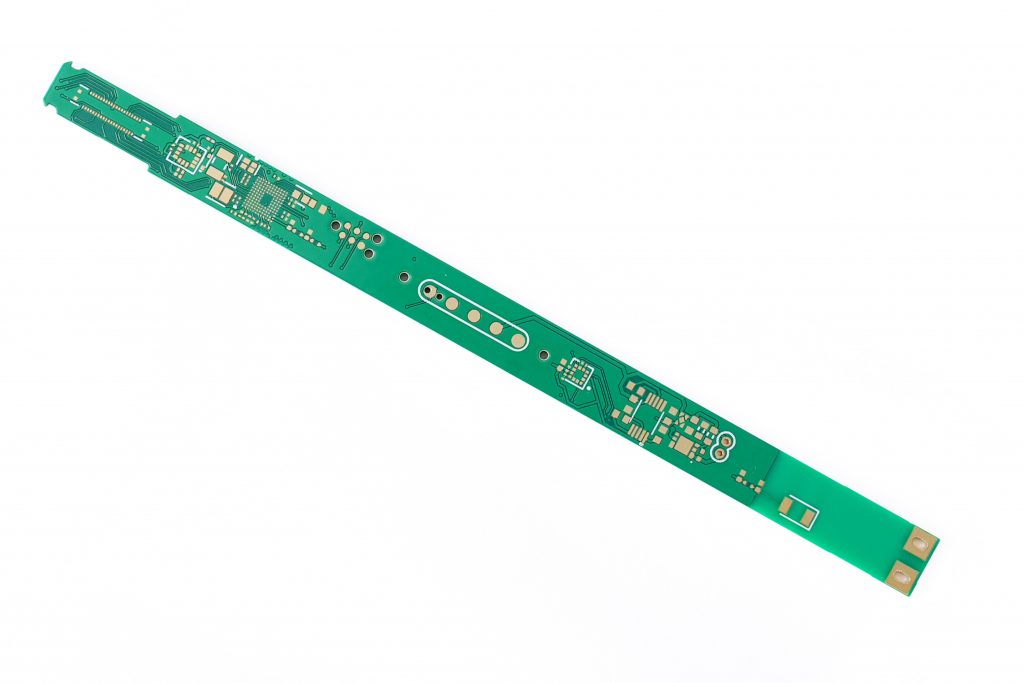
How to Ensure the Reliability of Industrial Control PCB under High Temperature Conditions?
Methods about how to ensure the reliability of industrial control PCB under high temperature conditions:
Select Thermally Stable Substrate Materials
- Choose High Temperature PCB substrates with glass transition temperatures (Tg) exceeding 170°C, such as polyimide or ceramic-filled epoxy. These materials resist softening and dimensional changes at sustained temperatures up to 200°C, ensuring mechanical stability in PLC interfaces or motor drives.
Optimize Copper Trace Geometry
- Design traces with 2â3 oz/ftÂČ copper thickness to reduce current density and minimize Joule heating. For example, a 10-mil trace carrying 3A current in a power distribution network will operate 15°C cooler than a 1-oz trace, extending solder joint lifespan in industrial actuators.
Implement Component Derating
- Select capacitors, resistors, and ICs rated for 20â30% above maximum operating temperatures. For instance, using X7R dielectric capacitors (rated for 125°C) in 150°C environments prevents capacitance drift by 10% compared to standard components, stabilizing filter circuits in sensor interfaces.
Enhance Solder Joint Robustness
- Use SnAgCu (SAC305) solder alloy with 260°C reflow tolerance and apply 5â10% larger solder paste stencils for heat-generating components. This reduces voiding by 40% in BGA packages, preventing solder joint fractures under thermal cycling in VFD controllers.
Incorporate Thermal Vias and Heat Spreaders
- Place 0.3 mm diameter thermal vias in 1.5 mm arrays beneath power MOSFETs and voltage regulators to conduct heat to inner ground planes. Pair this with 20-mil copper heat spreaders to lower junction temperatures by 25°C in compact PLC modules.
Conduct Accelerated Life Testing
- Subject prototypes to 1,000 thermal cycles (-40°C to 180°C) and 10,000 hours of continuous operation at 150°C. Identify weak points like delamination or parameter drift in analog-to-digital converters (ADCs) early, reducing field failure risks by 60%.
Apply Conformal Coatings for Environmental Protection
- Use silicone or parylene coatings with 200°C continuous service ratings to shield against moisture, dust, and chemical contaminants. For example, a 25-Όm parylene layer prevents arc-over in high-voltage relay interfaces exposed to industrial solvents.
Validate via Computational Fluid Dynamics (CFD)
- Simulate airflow patterns and temperature gradients in enclosed control cabinets to optimize PCB placement. Adjust spacing between boards and add ventilation slots to lower ambient temperatures by 10â15°C in crowded automation panels.
How to Balance Performance and Cost in High Temperature Industrial Control PCB Fabrication?
Below are ways about how to balance performance and cost in high temperature industrial control PCB fabrication:
Select Cost-Effective High-Temperature Substrates
- Use FR-4 variants with Tg â„ 170°C (e.g., ISOLA IS410) for moderate thermal demands or polyimide blends (e.g., Dupont Pyralux AP) for temperatures up to 260°C. These materials offer 25â30% lower CTE than standard FR-4, ensuring solder joint reliability at 15â20% lower cost than exotic ceramics.
Design Hybrid Layer Stackups
- Combine high-performance outer layers (e.g., Megtron 6 for signal integrity) with standard FR-4 cores for inner power planes. This reduces material costs by 15â20% while maintaining thermal stability. For example, a 4-layer board using Megtron 6 for outer layers and FR-4 for inner layers achieves 42% lower transmission loss in power distribution networks.
Optimize Trace Geometry for Current Capacity
- Use 2â3 oz/ftÂČ copper thickness for high-current paths to minimize Joule heating. For instance, a 15-mil trace carrying 5A reduces temperature rise by 18°C compared to 1-oz copper. Employ thermal simulation tools (e.g., Siemens Simcenter) to identify bottlenecks and adjust trace widths dynamically, avoiding over-engineering.
Implement Smart Component Placement
- Position heat-generating components (e.g., MOSFETs, inductors) near thermal vias or board edges to leverage natural convection. Maintain 8â10 mm spacing between hot components and temperature-sensitive ICs to prevent thermal runaway. In PLC control modules, this reduces junction temperatures by 12â15°C.
Apply Targeted Thermal Management
- Use 0.3 mm thermal vias in 1.2 mm arrays beneath power devices, lowering thermal resistance by 22%. Apply 20-mil copper heat spreaders only in critical areas (e.g., under BGA packages) rather than entire boards, cutting material costs by 30%. For example, a 50Ă50 mm copper spreader reduces hotspot temperature by 28°C in motor drive circuits.
Automate Manufacturing Processes
- Invest in dual-track reflow ovens with AI-driven temperature profiling. These systems reduce energy consumption by 45% and improve first-pass yield by 5â8% through adaptive heat control. Pair with laser direct imaging (LDI) for ±3ÎŒm linewidth accuracy, eliminating photo tooling costs and reducing setup time by 60%.
Validate via Accelerated Stress Testing
- Conduct 500-cycle thermal shock tests (-40°C to 180°C) on prototypes to identify weak points early. Replace failed components with equivalents rated for 20% higher temperatures, adding minimal cost while extending MTBF by 2â3x. For example, using X7R capacitors instead of Y5V in 150°C environments prevents 35% capacitance drift.
Conclusion
High-temperature PCBs provide thermal stability, reliability, and signal integrity. Material selection, thermal management, and cost-performance balance are main factors in design. These PCBs are used in PLC systems, automotive electronics, and heavy machinery to prevent delamination, warping, and signal loss under extreme heat.
For high-temperature PCB solutions, contact âBest Technologyâ. We offer â24/7 rapid prototypingâ, âmilitary-grade quality controlâ, and âfree DFM analysisâ to ensure robust performance. âRequest a quote todayâ to advance your industrial projects: sales@bestpcbs.com.