Heavy copper PCB manufacturers play a crucial role in creating circuit boards that handle high currents, distribute heat efficiently, and meet the needs of demanding industries. Whether you’re looking for extreme copper PCBs, 20oz copper PCBs, or a custom copper core PCB, understanding the factors that affect their design, quality, and assembly process will help you choose the proper manufacturer for your needs.
Heavy copper PCB (Printed Circuit Board) is a go-to solution for high-performance applications that require durability. Best Technology provides high-quality Heavy copper PCB in the PCB industry. We provide rapid prototypes within 24-48 hours. We have offered more than 1,200 customers in more than 60 countries & areas the fast turnaround heavy copper PCB service. We provide both normal delivery service and fast service, and urgent boards can be shipped out within 24 hours! Best Technology is one of the professional heavy copper PCB Manufacturers, if you need heavy copper PCB design, prototype, or assembly, pls feel free to reach out to Best Technology at sales@bestpcbs.com at any time.
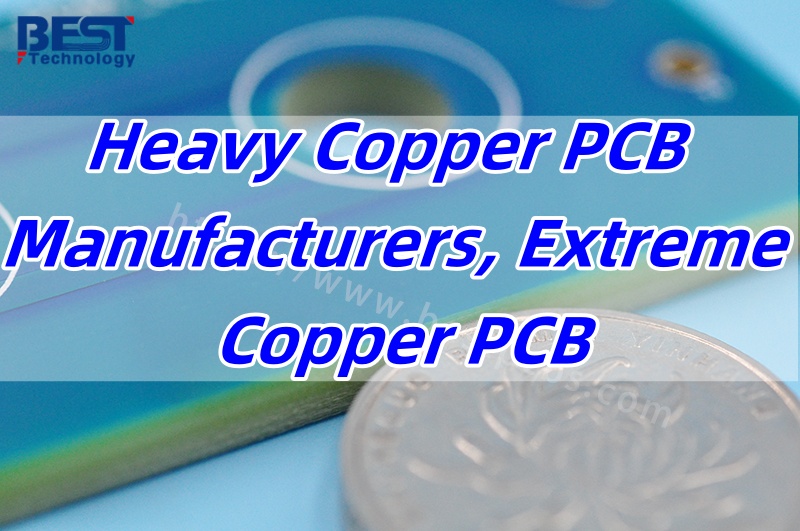
What Design Factors Do Heavy Copper PCB Manufacturers Consider for Reliability?
When designing heavy copper PCBs, manufacturers have to consider a wide range of factors to ensure the board performs reliably over time. Copper thickness, trace width, and the material’s ability to handle high current loads are just a few of the key considerations.
The first important design factor is the copper trace width. For high-current applications, manufacturers use wider copper traces to handle the increased load without overheating. This is especially important in industries like automotive, telecommunications, and power electronics, where PCB durability and performance are critical.
Another crucial aspect is layer stacking. Manufacturers use multiple layers in heavy copper PCBs to ensure that the heat generated by high currents can dissipate efficiently. This helps prevent thermal buildup, which can lead to failure or damage to the PCB. The layers are carefully arranged to maximize heat dissipation and ensure optimal performance under load.
Heat dissipation techniques are also a major design factor. A properly designed heavy copper PCB uses advanced techniques, such as copper coin technology, which places thick copper elements within the PCB to efficiently absorb and dissipate heat.
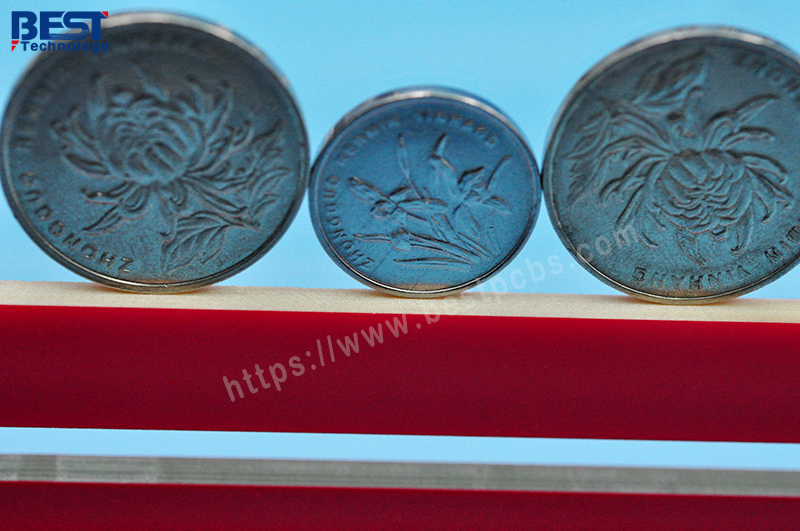
Where to Find Reliable Heavy Copper PCB Manufacturers for PCBs?
Finding the right manufacturer is key to ensuring you get a high-quality heavy copper PCB that meets your specifications. The process of identifying reliable manufacturers often starts with online research. There are numerous online directories, trade shows, and industry events where you can find reputable heavy copper PCB manufacturers.
Customer reviews and feedback play a significant role in identifying reliable manufacturers. Look for companies that have a proven track record in producing high-quality heavy copper PCBs. Best Technology, for instance, has built a strong reputation over 18 years, delivering excellent products to industries around the world.
Industry certifications also signal reliability. Established manufacturers often have certifications such as ISO 9001, UL, and IPC, which indicate their adherence to international quality standards.
Networking is another great way to find trusted manufacturers. Industry forums, LinkedIn, and professional groups offer recommendations from other businesses that have worked with these manufacturers.
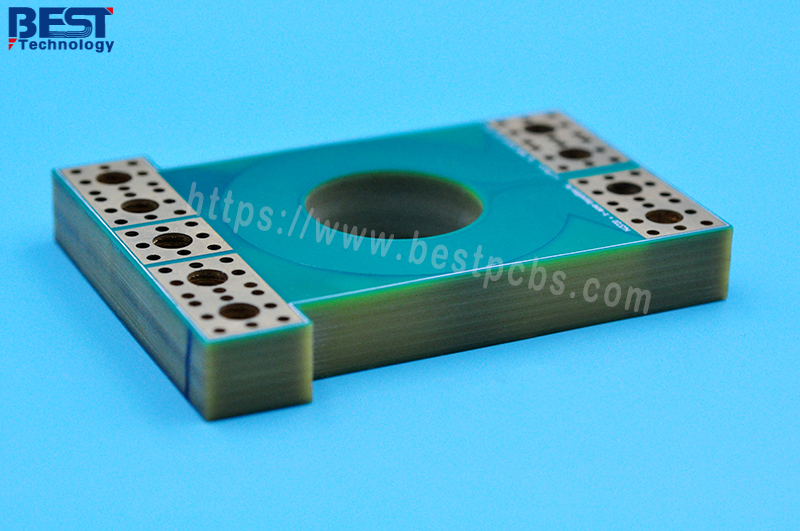
What Certifications Should Reliable Heavy Copper PCB Manufacturers Have?
Choosing a reliable heavy copper PCB manufacturer requires understanding the certifications they hold. Certifications are an assurance that the manufacturer follows quality control procedures and complies with industry standards.
The ISO 9001 certification is a widely recognized standard that shows a manufacturer’s commitment to quality management. It ensures that the manufacturer has consistent processes in place to deliver high-quality products.
The UL certification is another important factor, especially for PCBs that will be used in safety-critical applications. UL certification indicates that the manufacturer meets safety standards and that their products are safe for use in electrical applications.
Lastly, IPC certifications (such as IPC-A-600 and IPC-2221) demonstrate that the manufacturer follows best practices for PCB design, assembly, and inspection. These certifications ensure that the manufacturer produces PCBs that meet industry standards for performance and reliability.
What Is the Thickness of Copper in Best Technology?
Best Technology offers a range of copper thickness options tailored to different applications. Below is the capability of heavy copper PCB for your reference:
- Base material: FR4/Aluminum
- Copper thickness: 4 OZ~10 OZ
- Extreme Heavy Copper: 20~200 OZ
- Outline: Routing, punching, V-Cut
- Solder mask: White/Black/Blue/Green/Red Oil
- Surface finishing: Immersion Gold, HASL, OSP
- Max panel size: 580*480mm(22.8″*18.9″)
Best Technology doesn’t do “one-size-fits-all.” Our copper range fits every need. 2 oz (70 µm) is commonly used in consumer gadgets like phones, and routers. 4–10 oz heavy copper PCB is suitable for industrial applications like solar inverters. 20–200 oz extreme copper PCB is perfect for power substations and other areas that require heat dissipation and high current-carrying capacity. By customizing the copper thickness, Best Technology ensures that each PCB meets the specific needs of its customers, whether for high-frequency applications or power electronics.
How Thick Is 2 oz of Copper for PCB?
A 2 oz copper PCB typically has a thickness of around 70 microns (2.8 mils). While this is considered a mid-range thickness, it offers significant advantages over standard copper PCBs. The thicker copper enables the PCB to handle more current and provides better thermal performance, making it ideal for applications in industrial machinery, power supplies, and automotive systems.
The added copper thickness also improves the board’s resistance to thermal stress, which is particularly important in environments where heat is generated due to high power loads.
How Do Heavy Copper PCB Manufacturers Ensure Quality and Durability?
Ensuring the quality and durability of heavy copper PCBs is a multi-step process. From the initial design phase to the final assembly, manufacturers must employ strict quality control measures.
At Best Technology, advanced technologies like automated optical inspection (AOI) and X-ray inspection are used to detect potential defects early in the production process. These tools ensure that any issues are identified and corrected before they affect the final product.
Manufacturers also use high-quality materials like copper foil and ensure that the lamination process is carried out under precise conditions to avoid defects. Each PCB undergoes thorough testing to verify its electrical properties, mechanical strength, and heat dissipation capabilities.
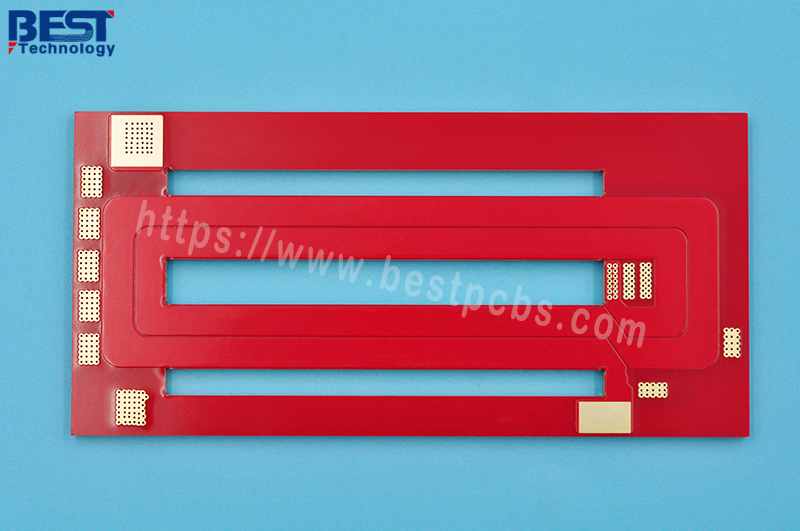
How to Choose a Heavy Copper PCB Manufacturer?
Choosing the right heavy copper PCB manufacturer requires careful consideration of several factors:
- 1. Experience: Look for manufacturers with experience in producing heavy copper PCBs, especially for the type of application you’re targeting.
- 2. Technology: Ensure the manufacturer has the latest technology for PCB design, fabrication, and testing.
- 3. Customer Service: A good manufacturer will offer support throughout the entire process, from design to assembly.
- 4. Prototyping: Request prototypes to verify the manufacturer’s capabilities before committing to large-scale production.
By evaluating these factors, you can choose a manufacturer that meets your quality standards and provides a seamless experience from start to finish.
Finally, heavy copper PCB manufacturers are essential partners for businesses in need of high-performance and durable PCBs. Best Technology stands out as a reliable provider of heavy copper PCBs, offering customized solutions and unparalleled expertise. Whether you need extreme copper PCBs or 20oz copper PCBs, choosing the proper manufacturer ensures the success and longevity of your products.
Do you need a heavy copper PCB solution? Just feel free to contact Best Technology at sales@bestpcbs.com at any time for expert guidance, exceptional quality, and fast delivery.