How to clean electrical copper busbar? Letâs explore cleaning methods, selection guide, specification, benefits, applications, recommend supplier for electric copper busbar.
Are you troubled with these issues?
- Delivery delays risking production halts?
- Copper purity fluctuations compromising thermal performance?
- Slow customization response losing competitive orders?
Best Technology can provide service and solution:
- 48-Hour Rapid Delivery – Strategic stockpile ensures uninterrupted supply.
- 99.99% Electrolytic Copper – Batch-specific third-party certification.
- 8-Hour Prototyping – 0.5mm precision non-standard customization supported.
Welcome to contact us if you have any request for electric copper busbar: sales@bestpcbs.com.
What Is Electrical Copper Busbar?
An electrical copper busbar is a flat or tubular conductive bar manufactured from high-purity copper (resistivity: 1.68Ă10â»âž Ω·m), designed for centralized distribution of high currents in power systems. It serves as a critical component for interconnecting equipment such as generators, transformers, and circuit breakers.
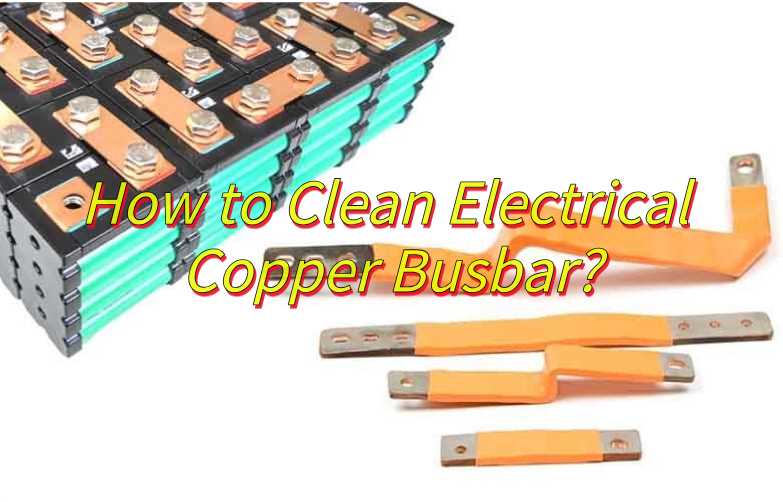
How to Clean Copper Busbar Electrical?
A Guide to Electrical Copper Busbar Cleaning:
1. Power Disconnection
- Cut off power supply and verify voltage absence using a voltage tester before operation.
- Ground the busbar to ensure safety.
2. Basic Cleaning
- Dust Removal: Use dry soft cloth or anti-static brush to clear surface dust, focusing on gaps and insulator areas.
- Stubborn Stains: Wipe with anhydrous ethanol (â„99.7% purity). Avoid chlorine-containing solvents.
- Light oil Contamination: Clean with neutral detergent and rinse with water.
- Heavy oil Contamination: Use copper wire brush (brush diameter â€0.1mm) with neutral detergent. Professional copper cleaning agents (e.g., KL-303) may be required for immersion.
3. Oxide Layer Treatment
Minor Oxidation:
- Wipe with vinegar + salt solution (3:1 ratio), then rinse with water.
- Use copper brightening agent (e.g., HQ-131S) for immersion and light brushing.
Severe Oxidation:
- Local treatment with 5%-10% oxalic acid solution (operation time <3 minutes). Rinse and apply stearic acid or organic protective film.
- Professional solutions: KL-303 copper cleaner or CJX5-4 dedicated cleaning agent.
4. Deep Maintenance
- Connection Tightening: Use torque wrench to retighten bolts (80%-120% of standard torque). Ensure smooth contact surfaces.
- Humid Environment: Dry with hot air gun (temperature â€60°C) to prevent moisture-related issues.
- Silver-Plated Contacts: Wipe unidirectionally with chamois leather. Avoid hard tools or abrasive cloths.
5. Safety Precautions
- Personal Protection: Wear insulating gloves (â„500V), goggles, and helmet. Avoid direct contact with chemicals.
- Solvent Restrictions: Prohibit hydrochloric acid or chlorine-containing agents to prevent corrosion.
- Environment Control: Humidity <60% during operation; Avoid spray cleaners near live equipment.
6. Quality Inspection
- Contact Resistance Test: Post-cleaning deviation â€15% of initial value.
- Infrared Thermography: Confirm no local overheating (temperature rise â€40°C).
7. Tools and Materials Selection
Tools:
- Preferred: Dense copper wire brush (brush diameter 0.1mm), explosion-proof vacuum cleaner (â„1200W).
- Alternatives: Nylon brush + soft cloth, compressed air blow.
Cleaning Agents:
- Preferred: Professional copper oxide removal solutions (e.g., KL-303).
- Alternatives: Anhydrous ethanol (analytical grade).
Protective Gear:
- Preferred: Nitrile insulating gloves (â„500V).
- Alternatives: Latex gloves + insulating mat.
8. Special Notes
- Copper-Clad Aluminum Busbars: Avoid alkaline cleaners to prevent material corrosion.
- Pure Copper Busbars: Prohibit steel wool or hard tools to prevent surface scratching.
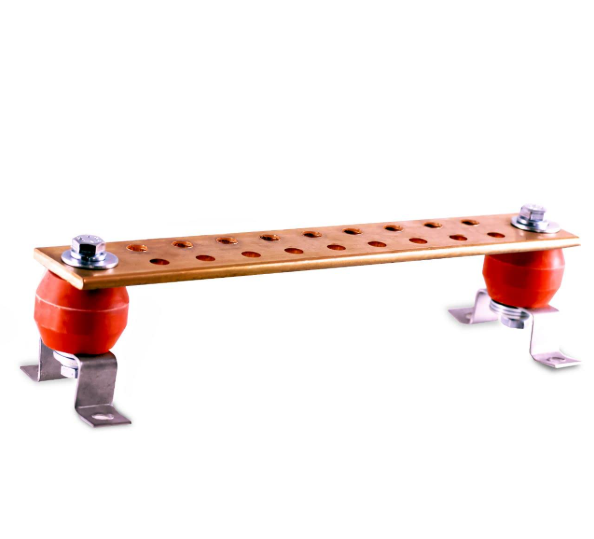
How to Choose Electrical Copper Busbar?
1. Material and Plating Selection
- Prioritize T2 or higher purity copper (conductivity â„58 MS/m); avoid copper-clad aluminum or recycled copper.
- Plating options: Silver plating (30% conductivity improvement) for high-frequency applications; tin plating for humidity/corrosion resistance.
2. Dimensions and Current-Carrying Capacity
- Cross-sectional area formula: S=I/(JĂK) (I=load current; J=2-3A/mmÂČ; K=0.8 for temperatures >40°C).
- Thickness standards: Tubular busbar wall thickness â„2mm; flat busbar thickness â„6mm (GB/T 5585.1-2005).
- Current-carrying reference: Single busbar â cross-sectional area (mmÂČ) Ă3.5 (e.g., 100mmÂČ â350A); derate for multiple bars (0.8 for 2 bars, 0.7 for 3 bars).
3. Structure and Connection Methods
- Shape selection: Flat busbar for compact panel installation; tubular busbar for long-distance transmission (40% higher bending resistance).
- Bolted Connection: Use 8.8-grade or higher bolts; torque at 80% of standard for silver-plated contacts.
- Welded Connection: TIG welding recommended for plated busbars; NDT (PT/UT) required for welds.
4. Environmental and Standard Compliance
Special environment adaptation:
- High temperature (>40°C): Use heat-resistant copper (e.g., C11000); upsize cross-section by 1-2 grades.
- High vibration: Tubular busbar + damping brackets; lock washers for bolted joints.
- High altitude (>1000m): Derate current-carrying capacity by 2% per 300m elevation.
Standards: Must comply with GB/T 5585.2-2018 or IEC 60582; certifications: 3C (China), UL (North America), CE (EU).
5. Cost and Maintenance
- Initial cost: Silver-plated busbars cost 20% more than tin-plated but reduce conductive losses by 5-8%.
- Maintenance: Inspect plating thickness every 2 years (tin â„8ÎŒm; silver â„5ÎŒm).
Electric Copper Busbar Specification
Parameter Categoryâ | Specification Detailsâ |
Standard Dimensions | Thickness: 2â100 mm |
Width: 10â400 mm (GB/T 5585.1-2005) | |
Surface Treatmentâ | Tin-plated / Embossed / Insulating paint (optional) |
Current Carrying Capacity(70°C ambient) | 30Ă4 mm: 365 A (vertical) |
40Ă4 mm: 480 A (vertical) | |
50Ă5 mm: 625 A (vertical) | |
Electrical Propertiesâ | Resistivity: 0.0185 Ω·mmÂČ/m (20°C) |
Conductivity: â„58 MS/m (100% IACS) | |
Mechanical Propertiesâ | Operating temperature: â€70°C (max. 75°C) |
Tensile strength: â„200 MPa (typical) | |
International Standardsâ | IEC 439 (equivalent to GB7251) |
ASTM B152/B152M (oxygen-free copper) |
Why Choose Electrical Copper Busbar?
Advantages of electrical copper busbar:
- Superior Conductivity: Pure copper conductivity â„58 MS/m (IACS standard), resistivity as low as 1.68Ă10â»âžÎ©Â·m, minimizing transmission losses.
- High Current-Carrying Capacity: Supports up to 3.5A/mmÂČ (at 25°C), 3x higher than aluminum, ideal for high-current applications.
- Mechanical Robustness: Tensile strength â„200MPa, 40% more bend-resistant than aluminum, suitable for vibration-prone environments.
- Corrosion Resistance: Tin-plated busbars withstand >500h salt spray tests; silver-plated options resist oxidation up to 200°C.
- Efficient Heat Dissipation: Thermal conductivity 401 W/(m·K), 1.8x better than aluminum, ensuring temperature rise â€40°C under load.
- Easy Installation & Maintenance: Modular design enables quick bolted/welded connections; maintenance intervals exceed 10 years with plating checks every 2 years.
- Cost-Effective Lifecycle: Higher initial cost offset by 5-8% lower energy loss; 90%+ recyclability reduces long-term expenses.
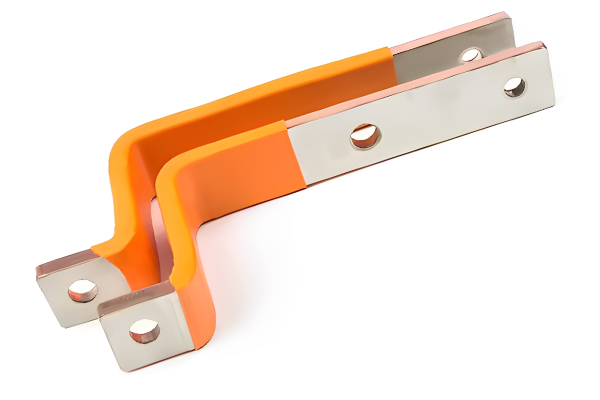
When to Use Copper Busbar Electrical?
Applications of electrical copper busbar:
Power Systems:
- 35kV/below substation main conductors.
- Solar/wind farm DC-side inverter connections.
- ±800kV UHV converter station valve hall links.
Industrial Use
- 50-150kA current carriers in metal smelters.
- EV battery module laser-welded interconnections.
- Semiconductor fab oxygen-free copper conductors.
Infrastructure
- High-rise building cable replacements (space-saving).
- Data center 12V/48V DC power distribution.
- Hospital ICU double-insulated power lines.
Special Environments
- Offshore platform corrosion-resistant busbars.
- Arctic region low-temperature conductive alloys.
- Naval vessel non-magnetic power conductors.
Copper Busbar for Automotive Electrical System Marketâ
1. Market Growth & Size
- 2025 Valuation: Global market estimated at 2.5Bâ5.5B, reflecting rapid electrification of vehicles.
- CAGR: Projected 5.4%â7.6% growth (2025â2030/2033), driven by EV adoption and technological advancements.
2. Primary Drivers
- EV/HEV Proliferation: Rising demand for high-performance electrical systems in electric vehicles.
- High-Voltage Systems: Adoption of 800V+ architectures requiring copper busbars for efficient power transmission.
- Material Superiority: Copperâs conductivity (59.6Ă10â¶ S/m) and thermal efficiency make it irreplaceable for high-current applications.
- Regulatory Push: Government incentives for EVs and emissions reduction accelerate market penetration.
3. Technological Advancements
- Copper-Aluminum Composites: Reduce costs by 30â50% while maintaining conductivity (e.g., automotive lightweighting).
- Flexible & Laminated Designs: Multi-layer busbars (3â7 layers) improve vibration resistance and space efficiency.
- High-Temperature Insulation: PET/PI films enable operation in -40°C to +125°C environments.
4. Regional Dynamics
- Asia-Pacific Dominance: China leads (45% global share) due to massive EV production and government subsidies.
- European Growth: Stricter emissions regulations drive demand for copper busbars in hybrid and electric vehicles.
- North American Market: Steady adoption linked to Tesla and legacy automakersâ EV transitions.
5. Competitive Landscape
- Top Players: Shenzhen Everwin Technology, Zhejiang RHI Electric, Schneider Electric (40% combined market share).
- Regional Suppliers: Numerous small-to-mid-sized firms cater to niche automotive segments.
- Innovation Focus: Laser-welded interconnections and modular designs enhance installation efficiency.
6. Advantages vs. Alternatives
- Efficiency: 70% shorter than cables, reducing power loss by 15â20%.
- Durability: Superior heat management and corrosion resistance extend lifespan.
- Cost Savings: Aluminum-based composites lower material costs without compromising performance.
7. Future Outlook
- Vehicle-to-Grid (V2G) Integration: Custom busbars enable bidirectional energy flow (e.g., Nissan Leaf).
- ADAS & Connectivity: Rising demand for reliable power distribution in automated driving systems.
- Sustainability: Recyclability of copper aligns with circular economy goals in automotive manufacturing.
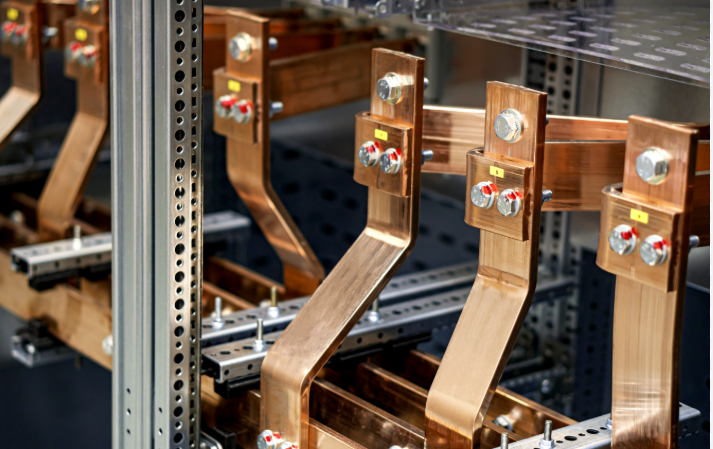
Why Choose Best Technology as Electric Copper Busbar Supplier?
Certifications & Compliance
- ISO 9001:2015, UL, and RoHS certified.
- Third-party lab reports for critical parameters (e.g., tensile strength).
Competitive Pricing Model
- Direct factory pricing reduces costs by 10-15% vs. distributors.
- Volume-based discounts (e.g., 5% off for orders >5,000 pcs) and loyalty programs.
Premium Material Selection
- Oxygen-free copper (â„99.99% purity) minimizes resistance and oxidation.
- Compliant with GB/T 5585.1-2005 and IEC 60317 standards.
Rigorous Quality Assurance
- Full-Cycle Inspection: IQC for Raw material purity tests. IPQC for Automated Optical Inspection (AOI) during production. OQC for 100% electrical performance validation.
- Advanced Testing: Salt spray resistance (48h), thermal cycling (-40°C to +125°C), and conductivity â„58.5Ă10â¶ S/m.
Fast Lead Times
- 7-10 day production for standard orders.
- 98% on-time delivery rate with emergency order support.
Integrated PCBA Services
- End-to-end solutions from busbar design to PCB assembly (PCBA).
- Supports small-batch prototyping (MOQ 100 pcs) and rapid tooling adjustments.
Technical Expertise
- In-house engineers optimize thermal management and EMI reduction.
- Customizes layouts for high-current/high-voltage systems.
Client-Centric Flexibility
- Customizes plating thickness, insulation materials, and dimensions.
- Provides free samples for testing and design validation.
Welcome to contact us if you have any request for electric copper busbar: sales@bestpcbs.com.