Why choose aluminum-core PCB for thermal management? This guide explores aluminum PCB materials, advantages, applications, and manufacturing solutions.
- Does your electronic product suffer from performance degradation or shortened life due to insufficient heat dissipation?
- Is it difficult to choose between the high cost of copper substrates and the heat dissipation requirements?
- Does small batch customization face the problem of long delivery time and high minimum order quantity?
Best Technology can Provide:
- We provide high thermal conductivity aluminum substrates, which improve heat dissipation efficiency by 60% to ensure stable operation of the equipment.
- Our aluminum substrate solution saves 30% of the cost compared to copper substrates, while meeting strict heat dissipation requirements.
- Support 1 piece minimum order, 72 hours fast proofing, and flexible production throughout the entire process.
Welcome to contact us if you have any request for aluminum core PCB: sales@bestpcbs.com.
What Does Aluminum-Core PCB Mean?
An aluminum-core PCB, also known as Metal Core PCB (MCPCB) or Insulated Metal Substrate PCB (IMS PCB), is a specialized circuit board that uses an aluminum base layer instead of traditional FR4 material. The aluminum core serves as both a structural support and thermal conductor, efficiently dissipating heat from components like LEDs or power electronics.
These boards typically consist of three layers: a copper circuit layer, a thermally conductive dielectric layer, and the aluminum substrate. Unlike conventional PCBs, Aluminum-Core PCBs excel in high-power applications where heat management determines performance and longevity. The IMS PCB variant emphasizes the insulated dielectric layer’s role in preventing electrical shorts while maintaining optimal thermal transfer.
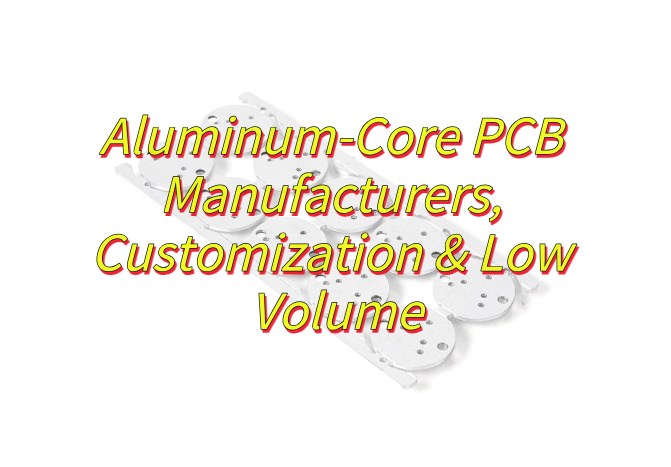
What Is Aluminum Core PCB Material?
Copper Circuit Layer
- Forms the conductive pathways for electrical signals
- Typically 1-8 oz (35-280μm) copper foil
Dielectric Layer
- Electrically insulating but thermally conductive
- Contains ceramic-filled epoxy (1-3 W/m·K thermal conductivity)
- Withstands ≥3000V electrical isolation
Aluminum Base
- 5052 or 6063 alloy (100-220 W/m·K thermal conductivity)
- 1.0-3.2mm thickness for heat spreading and mechanical support
What Are the Advantages of Aluminum-Core PCB?
- Enhanced Thermal Conductivity – Aluminum dissipates heat faster than traditional FR4 or ceramic substrates, reducing thermal stress on components and improving long-term reliability.
- Mechanical Durability – Resists bending, vibration, and physical stress, making it suitable for automotive, industrial, and high-vibration environments.
- Lightweight Construction – Offers a balance of strength and reduced weight compared to copper-core alternatives, aiding portability in consumer electronics.
- Cost Efficiency – Lower material and manufacturing costs than copper-based PCBs, ideal for cost-sensitive mass production projects.
- Dimensional Stability – Minimal expansion/contraction under temperature fluctuations ensures consistent solder joint integrity and component alignment.
- Simplified Cooling Systems – Reduces reliance on external heatsinks or fans by leveraging direct metal-to-component heat transfer.
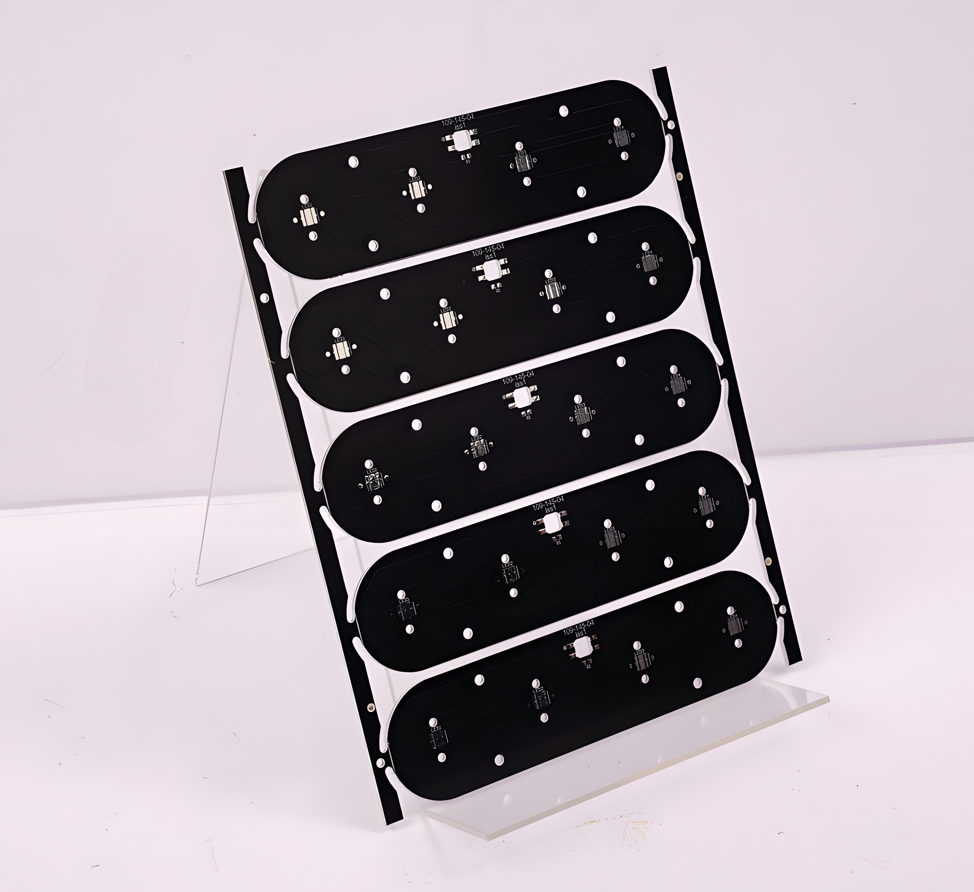
What Are Types of Aluminum-Core PCB?
Single-Layer Aluminum PCB:
- Single-sided circuit with aluminum core as the base layer, ideal for basic thermal management in LED lighting or power modules.
Double-Layer Aluminum PCB
- Dual-sided circuitry with aluminum substrate between layers, enabling compact designs for motor controls or automotive electronics.
Multi-Layer Aluminum PCB
- Stacked layers with aluminum core integrated into internal positions, balancing circuit density and thermal performance in high-power applications.
When to Use Aluminum PCB?
Application of aluminum-core PCB:
- High-Power LED Lighting – Manages heat in streetlights/headlights to prevent LED degradation.
- Automotive Power Systems – Handles vibration/heat in engine controls or battery modules.
- Compact Power Modules – Enables dense DC/DC converters without external cooling.
- Industrial Motor Controls – Stabilizes high-current transistors in factory drives.
- Outdoor Electronics – Resists moisture/UV in solar inverters or weather sensors.
- Cost-Sensitive Thermal Needs – Balances budget/performance in consumer chargers/adapters.
- Medical Instrumentation – Maintains temperature precision in diagnostic/imaging tools.
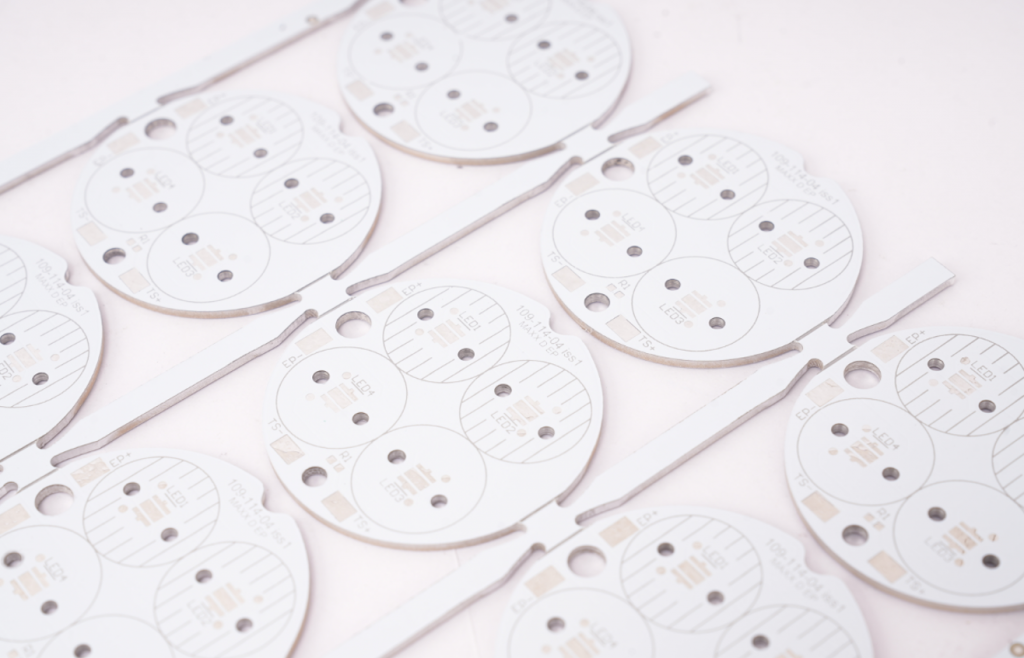
Differences Between Copper Core vs Aluminum Core PCB
Here are the 8 most important differences between Copper Core and Aluminum Core PCBs:
Thermal Conductivity
- Copper Core: ~400 W/m·K (superior heat transfer)
- Aluminum Core: 100-220 W/m·K (effective but less conductive)
Weight
- Copper Core: Heavy (~8.96 g/cm³)
- Aluminum Core: Light (~2.7 g/cm³), better for portable devices
Cost
- Copper Core: More expensive (~3-5x aluminum)
- Aluminum Core: More cost-effective
Thermal Expansion
- Copper Core: Matches well with copper traces
- Aluminum Core: Higher CTE mismatch requires careful design
Applications
- Copper Core: Extreme high-power electronics, aerospace
- Aluminum Core: LED lighting, automotive, consumer electronics
Corrosion Resistance
- Copper Core: Requires protective coatings
- Aluminum Core: Naturally forms protective oxide layer
EMI Shielding
- Copper Core: Better electromagnetic interference protection
- Aluminum Core: Adequate for most commercial uses
Manufacturing Process
- Copper Core: Requires specialized etching/plating
- Aluminum Core: Easier to machine and process
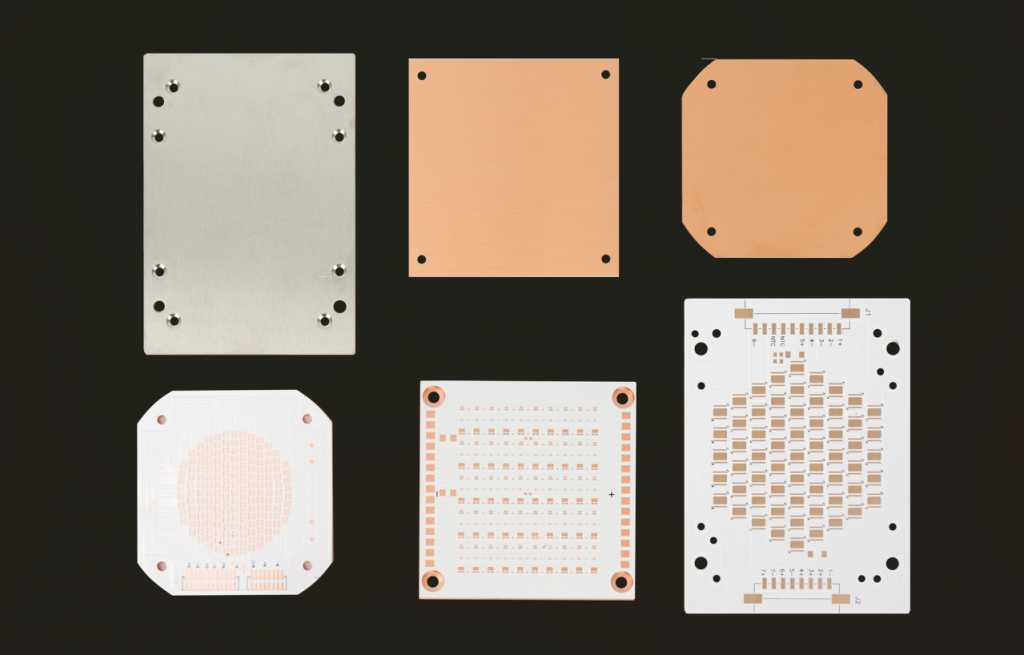
How to Optimize Your Thermal Design to Achieve Efficient Heat Dissipation?
- Select High-Thermal-Conductivity Substrates – Prioritize aluminum (200-250 W/m·K) or copper (380-400 W/m·K) cores over FR4 to directly channel heat away from components.
- Position High-Power Components Near the Metal Base – Place MOSFETs, LEDs, or power transistors in direct proximity to the substrate to minimize thermal resistance paths.
- Expand Surface Area for Radiative Cooling – Integrate fins, exposed metal pads, or extended substrate sections to enhance heat dissipation through air contact.
- Apply Thermal Interface Materials (TIMs) – Use silicone pads, greases, or phase-change films to eliminate air gaps between components and the substrate, reducing thermal resistance by 30-50%.
- Design Airflow Channels or Active Cooling – Create ventilation paths or install low-profile fans to direct airflow over hot zones, critical for enclosed systems or high-ambient-temperature environments.
- Validate with Thermal Imaging and Simulation – Test prototypes using infrared cameras under operational loads and refine designs based on hotspot analysis.
Why Choose Best Technology As Your Aluminum-Core PCB Manufacturer?
Reasons why choose Best Technology as your aluminum-core PCB manufacturer:
- Fastest Turnaround – 24-hour rapid prototyping & 15-day bulk production to accelerate your time-to-market.
- Cost Transparency – No hidden fees; competitive pricing with direct factory savings.
- Turnkey Solution – End-to-end service (design → assembly → testing) to simplify your supply chain.
- Free DFM Analysis – Prevent costly errors early with expert design optimization.
- Certified & Compliant Standards – ISO 9001, ISO 13485, IATF 16949, AS9100D Certified, and UL, REACH, RoHS Compliant.
- Thermal Management Excellence – Our 2.0mm aluminum core reduces operating temps by 25-30°C, solving overheating in LED/high-power applications.
- Rapid Prototyping – 24-hour turnaround for double-sided MCPCB samples.
- Cost-Efficient Scaling – 15% lower batch pricing for 500+ units without sacrificing quality.
Instant Quote
Aluminum-core PCBs deliver excellent heat dissipation for LED, automotive and power electronics applications. Their aluminum base provides superior thermal performance at lower costs than copper, available in single/double/multilayer configurations. Main selection factors include thermal conductivity requirements and dielectric properties. Best Technology offers customized aluminum PCB solutions from prototypes to mass production with competitive pricing and fast delivery. Contact us for project-specific quotations: sales@bestpcbs.com.