How to find a MCPCB fabrication factory? This guide explains metal core PCB manufacturing, its benefits, processes, and how to select reliable suppliers.
Are you worried about these issues?
- How long can your product run stably at high temperatures?
- Do urgent orders always put you in a passive position?
- How to balance cost and price?
Best Technology Can Provide:
- Customized thermal management solution: Adopt gradient thermal conductive structure design, which can reduce the junction temperature of the device by 25℃+ and extend the service life by 3 times.
- 72-hour express delivery: reserve special production line capacity, and the expedited order can be shipped in as fast as 3 days (including quality inspection).
- Value engineering cost optimization: Through material combination innovation and process simplification, we can help customers reduce costs by 15% while ensuring IPC standards.
Feel free to contact us if you have any inquiry for MCPCB: sales@bestpcbs.com.
What Is MCPCB Fabrication?
MCPCB fabrication involves manufacturing circuit boards with a metal core (typically aluminum or copper) to enhance heat dissipation. The process includes bonding a thermally conductive dielectric layer to the metal base for electrical insulation, laminating a copper circuit layer on top, and etching circuit patterns via photolithography. Vias are drilled and plated for electrical connectivity, followed by surface finishes to protect copper and ensure solderability. Designed for high-power applications, MCPCBs efficiently manage thermal stress in devices like LEDs, automotive systems, and power electronics.

Benefits of Metal Core PCB Fabrication
- Superior Heat Dissipation – Metal cores (Al/Cu) conduct heat 8–12× faster than FR4, reducing component temperatures by up to 15°C (e.g., LEDs). Extends product lifespan and prevents thermal throttling.
- Enhanced Durability – Metal substrates resist warping and vibration, ideal for automotive/industrial use. Withstands temperatures up to 120°C continuously.
- Compact Design – Eliminates bulky heatsinks, enabling thinner devices. Supports double-sided component mounting.
- Cost Efficiency – Reduces reliance on external cooling systems. Lower maintenance costs due to higher reliability (MTBF ≥50,000h).
- Eco-Friendly – Aluminum cores are recyclable, aligning with sustainability goals.
- High-Power Performance – Handles power densities >20 W/cm² (e.g., IGBT modules) without degradation.
- EMI Shielding – Metal base acts as a natural shield, reducing electromagnetic interference.
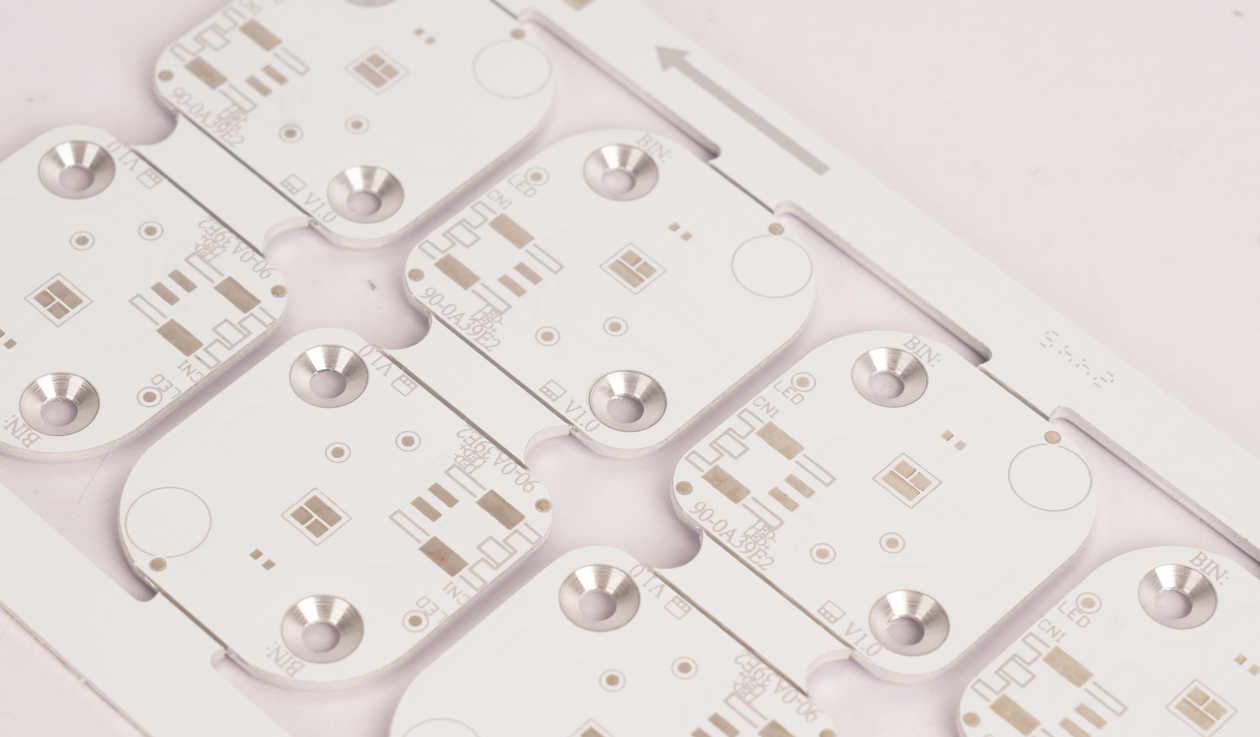
Applications of Metal Core PCB Fabrication
- High-Power LED Lighting – Directs heat from LEDs to metal core, preventing premature failure. Extends lifespan and reduces maintenance costs.
- Electric Vehicle (EV) Systems – Cools battery modules, motor controllers, and charging units. Withstands vibration and thermal stress for reliable operation.
- Renewable Energy Inverters – Enhances thermal efficiency in solar/wind inverters, minimizing energy loss and boosting ROI.
- Medical Imaging & Diagnostics – Stabilizes temperature-sensitive components (e.g., lasers, sensors). Ensures precision in critical healthcare devices.
- Aerospace & Defense Electronics – Resists extreme temperatures and mechanical stress in satellite/aviation systems. Maintains performance during rapid thermal cycling.
- Industrial Motor Control – Manages heat from high-current motor drivers and inverters. Prevents thermal deformation, ensuring continuous operation.
- 5G Base Station Modules – Efficiently dissipates heat from high-frequency RF components. Maintains signal integrity and reliability in dense wireless infrastructure.
- EV Charging Infrastructure – Supports high-power DC charging by rapidly conducting heat away from power electronics. Enables faster, safer charging solutions.
MCPCB Fabrication Processes
1. Design & Engineering
- Use EDA tools to create PCB layout, adhering to IPC-2221 standards.
- Generate Gerber files and validate through Design Rule Checks (DRC).
2. Material Preparation
- Select metal substrate (aluminum/copper), insulating layer (epoxy/ceramic), and copper foil.
- Cut metal base to specified dimensions.
3. Metal Substrate Treatment
- Clean substrate to remove contaminants.
- Apply insulating layer via coating or lamination, ensuring uniformity.
4. Circuit Layer Formation
Use photolithography to pattern copper traces:
- Coat substrate with photoresist.
- Expose to UV light through circuit masks.
- Develop and etch to remove excess copper.
5. Lamination & Pressing
- Stack layers (metal base, insulating layer, copper foil) with prepreg.
- Press under high temperature/pressure to bond layers (IPC-6012 compliance).
6. Drilling & Plating
- Drill via holes for interlayer connections.
- Electroplate holes to deposit copper, ensuring conductivity (IPC-A-610).
7. Surface Finish
- Apply surface treatment (e.g., ENIG, OSP) to protect copper and enhance solderability.
8. Testing & Inspection
- Electrical test (flying probe) to verify connectivity.
- AOI for defects, thermal stress test for reliability.
9. Profiling & Cutting
- Route PCB to final shape, V-cut or bevel edges as needed.
10. Packaging & Shipping
- Final inspection, vacuum packaging to prevent oxidation.
How to Find MCPCB Fabrication Factories?
A guide about how to find MCPCB fabrication factories:
1. Search Online: Use Google/Bing with keywords: “MCPCB manufacturer China,” “metal core PCB fabrication.”
2. Browse B2B Platforms: Check Alibaba International, Made-in-China, or Global Sources. Filter by Trade Assurance, UL/IPC-6012 certifications, and MOQ.
3. Attend Global Trade Shows: Visit Productronica China, HKTDC Electronics Fair, or CES to meet suppliers and inspect samples.
4. Verify Certifications: Confirm UL, ISO 9001, and IPC-6012 compliance via official databases.
5. Request Quotes: Send detailed specs (materials, layer count, thermal requirements) and ask for free prototypes + DFM feedback.
6. Audit Factories: Check production equipment (automation level), AOI/X-ray inspection, and thermal testing labs via virtual/on-site visits.
7. Prioritize Technical Expertise: Choose factories with MCPCB capabilities and experience in high-power applications (LED, automotive).
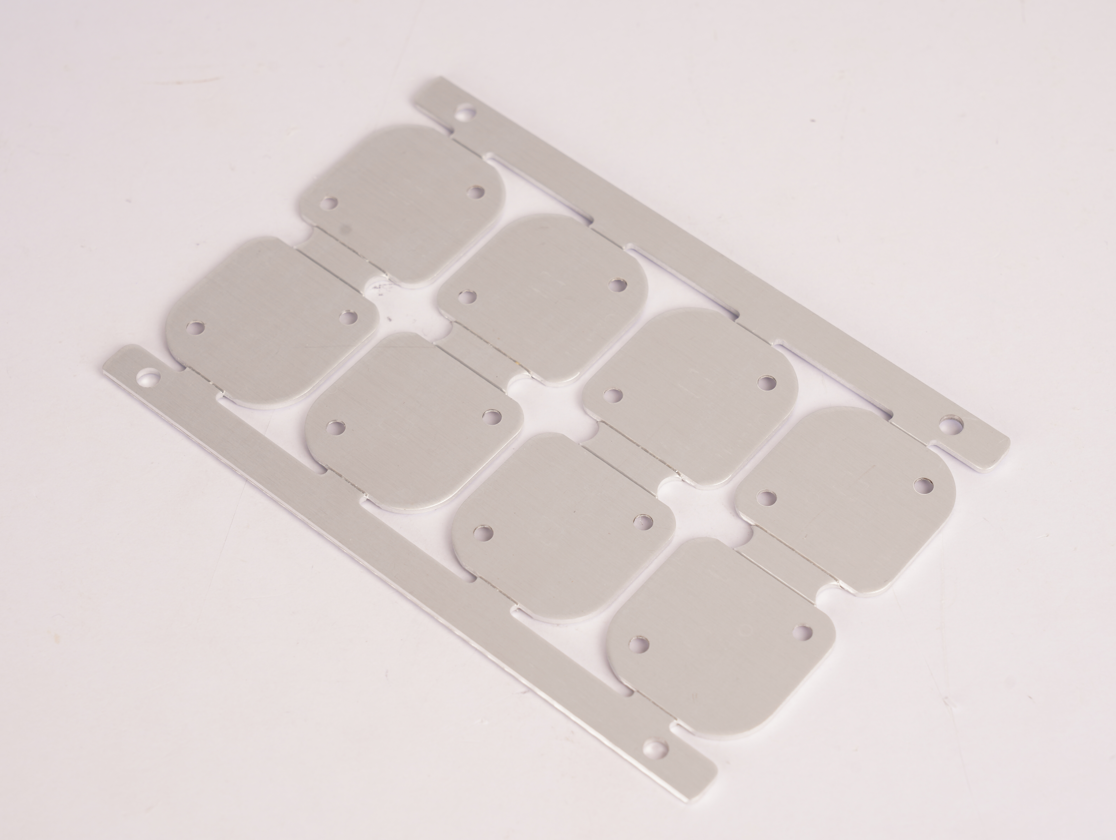
Why Choose Best Technology as MCPCB Manufacturer?
- Precision Manufacturing for High-Performance MCPCBs: Specialized in production of aluminum and copper-core PCBs with ±10μm tolerance, ensuring optimal thermal conductivity for LED, automotive, and power electronics applications.
- Custom Thermal Solutions for Your Needs: Our engineers dielectric layers and metal core designs to maximize heat dissipation, with thermal conductivity ranging from 1.0W/m·K to 4.0W/m·K for stable performance in high-power environments.
- 24-Hour Rapid Prototyping for Critical Projects: Emergency orders processed within 24 hours, reducing time-to-market by up to 70% compared to industry standards.
- Strict Quality Control for Bulk Orders: Full AOI and X-ray inspection on every bulk order, maintaining defect rates below 0.1% (industry average: 0.5%).
- Factory-Direct Pricing with No Hidden Costs: Transparent pricing saves 15-30% compared to distributors, with no additional fees for design reviews or testing.
- Fast Delivery with Consistent Lead Times: Standard lead times as short as 5 days (industry average: 10-14 days), with 98% on-time delivery rate.
- Free DFM Analysis to Optimize Your Design: Technical team reviews designs for manufacturability, reducing production errors by up to 40%.
- High-Quality Material Sourcing: Exclusively uses FR-4 and aluminum substrates from top suppliers like Rogers and Ventec for reliability.
- Scalable Production Capacity: Handles orders from 10-unit prototypes to 50K+ monthly batches without compromising quality.
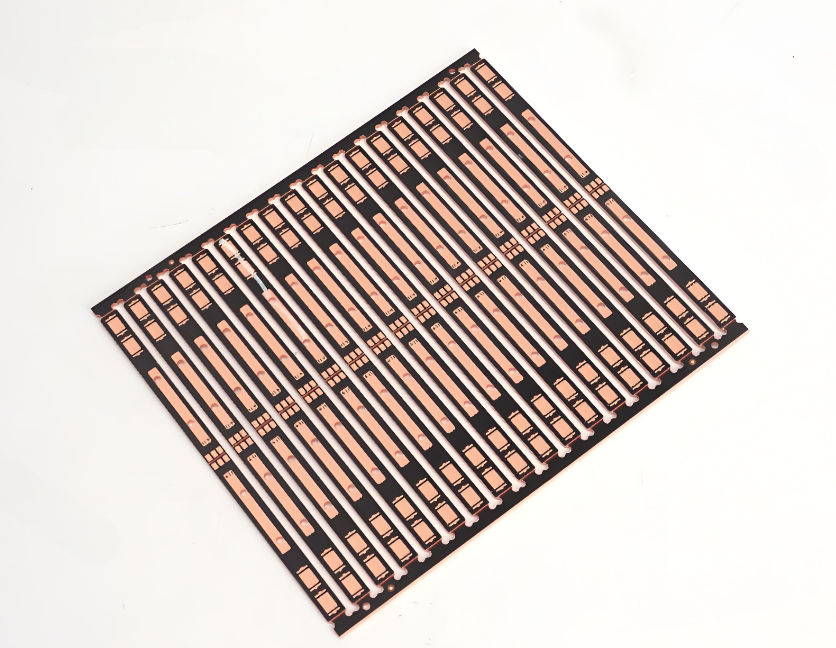
Our Certification & Quality Inspection
- Certified & Compliant Standards: ISO 9001, ISO 13485, IATF 16949 Certified, and UL, REACH, RoHS Compliant.
- AOI (Automated Optical Inspection): Detects surface defects like open/short circuits, missing components, and soldering issues.
- X-Ray Inspection (Internal Defect Screening): Checks solder joint voids, cracks, and BGA/QFN hidden defects.
- Peel Strength Test (Adhesion Assessment): Quantifies copper-clad laminate bonding force (ASTM D903).
- Aging Test (Environmental Stress Screening): Includes thermal cycling (-40℃~85℃) and humidity exposure to validate long-term reliability.
- Dimensional Verification (CMM/Profilometer): Measures thickness (±0.1mm), flatness, and hole alignment accuracy.
How to Get Quotes for MCPCB Fabrication Service?
To ensure accurate pricing and lead time, please submit the following technical specifications:
1. Gerber Files
- Layer stack-up (e.g., 1-layer Al base + 2 copper layers).
- Drill files (.txt) with hole size tolerance (±0.1mm).
2. Material Specifications
- Metal core type (e.g., 6061-T6 aluminum, 2.0W/mK thermal conductivity).
- Copper thickness (e.g., 1oz/35μm for signal layers, 2oz/70μm for power layers).
- Dielectric layer thickness (e.g., 100μm FR-4 prepreg).
3. Quantity & Lead Time
- Sample order (1-5 pcs) or bulk production (100+ pcs).
- Required delivery date (e.g., 3 days for prototypes, 15 days for bulk).
4. Special Requirements
- Thermal vias (e.g., 0.3mm diameter, 1.0mm pitch).
- Surface finish (e.g., ENIG, HASL).
- Electrical test criteria (e.g., 100% flying probe test)
Why Choose Best Technology for MCPCB?
- Factory-direct pricing with no hidden fees.
- 24-hour rapid prototyping for urgent projects.
- Thermal optimization support for high-power applications.
Welcome to contact us if you have any request for metal core PCB: sales@bestpcbs.com.