How BMS PCB keeps your 18650 battery pack safe and efficient? This guide covers everything from wiring and design to cost-effective noise shielding and heat management for optimal BMS PCB protection.
Using 18 years of BMS PCBA technology accumulation, we will protect your battery safety!
- Poor welding? – Nitrogen reflow + 3D SPI detection to eliminate false welding
- Delivery delay? – Intelligent scheduling system guarantees 7-day delivery
- Cost out of control? – Standardized process reduces 15% assembly cost
- Poor compatibility? – Support TI/ADI/NXP and other multi-platform solution adaptation
Best Technology Provide:
- Integrated solution – From PCB design to finished product assembly, BMS protection board “plug and play” is realized
- High-precision mounting – 01005 component mounting accuracy ±25μm, ensuring the stability of the sampling circuit
- Triple test guarantee – AOI+ICT+FCT full inspection, fault interception rate increased to 99.97%
- Flexible production – Support 1-16 layer board mixed production, 24-48 hours ultra-fast prototyping.
Let every BMS PCB become the intelligent guardian of the battery system! Contact us now: sales@bestpcbs.com.
What Is BMS PCB?
A BMS PCB (Battery Management System Printed Circuit Board) serves as the central control unit for rechargeable battery packs, ensuring safe and efficient operation. It monitors vital parameters including individual cell voltages, overall current flow, and temperature distribution across connected battery cells. When detecting potentially hazardous conditions such as overcharging, excessive discharge, or abnormal heat buildup, the system automatically disconnects the battery through integrated protection circuits to prevent permanent damage.
To maintain consistent performance, most BMS PCBs incorporate cell balancing functionality, which adjusts charge distribution among cells during operation. This process helps maximize available energy storage while extending battery lifespan. Communication capabilities allow the board to relay operational data, including state-of-charge estimates and system warnings, to connected devices through standard interfaces. The implementation varies across applications, with simpler versions managing small consumer electronics and more advanced configurations supporting high-capacity systems like electric vehicles and renewable energy storage installations.
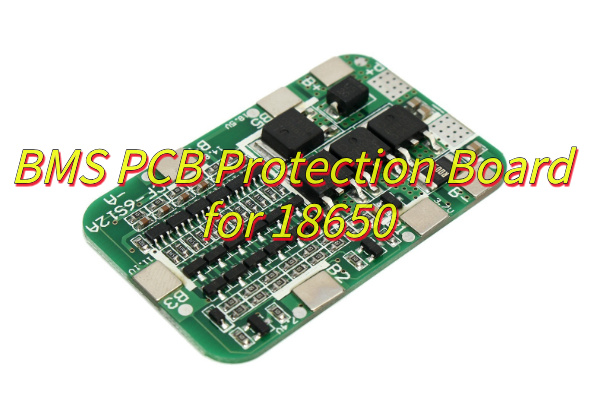
How to Wire PCB BMS?
Here’s a practical guide to wiring a BMS PCB, focusing on achieving reliability, safety, and performance:
1. Establish Accurate Cell Voltage Monitoring
- Connect each cell voltage sense wire directly to its corresponding cell terminal within the battery pack. Keep these sense wires as short and consistent in length as feasible and route them away from high-current paths to minimize noise interference and ensure precise voltage readings by the BMS PCB.
2. Implement Dedicated High-Current Paths
- Use appropriately thick traces or busbars for the main battery pack positive (P+) and negative (P-) connections entering the BMS PCB. Similarly, size the discharge (B-) and charge/discharge output (C- or P-) traces adequately to safely carry their maximum expected currents without excessive voltage drop or heating.
3. Apply Effective Grounding Strategies
- Create a solid, low-impedance reference ground plane on the BMS PCB near the current shunt resistor. Physically separate and connect sensitive analog measurement grounds (like cell sense circuits) directly to this reference point before connecting noisy digital grounds or high-current FET grounds.
4. Route Signal Traces Mindfully
- Physically separate sensitive signals like cell voltage sense lines. Shield communication lines (CAN, UART, etc.) whenever possible using twisted pairs, shielded cables, or ground planes adjacent to the traces on the BMS PCB itself.
5. Install Thermistors Securely
- Mount temperature sensors directly onto the cell surface or module terminals where thermal monitoring is required. Route their connecting wires carefully to avoid snagging or damage and connect them securely to the designated thermistor input pins on the BMS PCB.
6. Connect Balancing Components Efficiently
- Link balancing resistors or FETs directly to their respective cell sense points. Ensure the balancing current paths on the BMS PCB have adequate trace width for the balancing current level without causing localized heating. Tightly group balancing components to shorten signal paths.
7. Select and Wire Suitable Connectors
- Choose connectors rated well above the maximum operating current and voltage, with sufficient pin density and locking mechanisms. Match wire gauges to current loads. Clearly label all connector positions for unambiguous wiring to the BMS PCB.
8. Integrate Protective Elements
- Install necessary fuses or circuit breakers in series with the main pack positive (P+) input path before it reaches the BMS PCB. Ensure the fuse rating aligns with system capabilities. Connect any external contactor control coils to the designated driver outputs on the BMS PCB.
9. Verify Connections Thoroughly
- Before applying power, meticulously check all wiring against the BMS PCB schematic and layout diagram. Use a multimeter to confirm absence of short circuits, verify correct voltage polarity at each sense point, and ensure thermistor resistances read correctly at the connector.
How to Design BMS PCB Heat Dissipation Structure to Avoid MOSFET Hot Spot Failure?
Here are practical approaches to design BMS PCB heat dissipation structures that effectively prevent MOSFET hot spot failures:
- Strategic Component Placement: Position MOSFETs away from other heat-generating components and near board edges or ventilation areas. Allow sufficient spacing between devices to enable airflow and prevent thermal interference.
- Optimized Copper Pour Layout: Use thick copper layers (≥2 oz) for power traces and create large, continuous copper areas connected to MOSFET source/drain pins. Expand these pours to maximize surface area for heat dissipation.
- Thermal Via Implementation: Place dense arrays of thermal vias beneath MOSFET packages, connecting top-side heat sources to inner copper layers or bottom-side heatsinks. Follow manufacturer recommendations for via diameter and spacing.
- Effective Heatsink Integration: Design PCB mounting points for clip-on or screw-attached heatsinks. Ensure flat surface areas under MOSFETs for proper thermal interface material contact when using external cooling solutions.
- Current Distribution Balancing: Implement symmetrical layouts with identical trace lengths when using parallel MOSFETs. This prevents uneven current sharing that could cause localized overheating in individual devices.
- Thermal Relief Pad Design: Configure solder pads with appropriate thermal relief patterns – enough to allow proper soldering while maintaining efficient heat transfer to the PCB copper.
- Temperature Monitoring Integration: Embed temperature sensors near expected hot spots, positioned to detect actual MOSFET case temperatures rather than ambient board temperature for accurate thermal management.
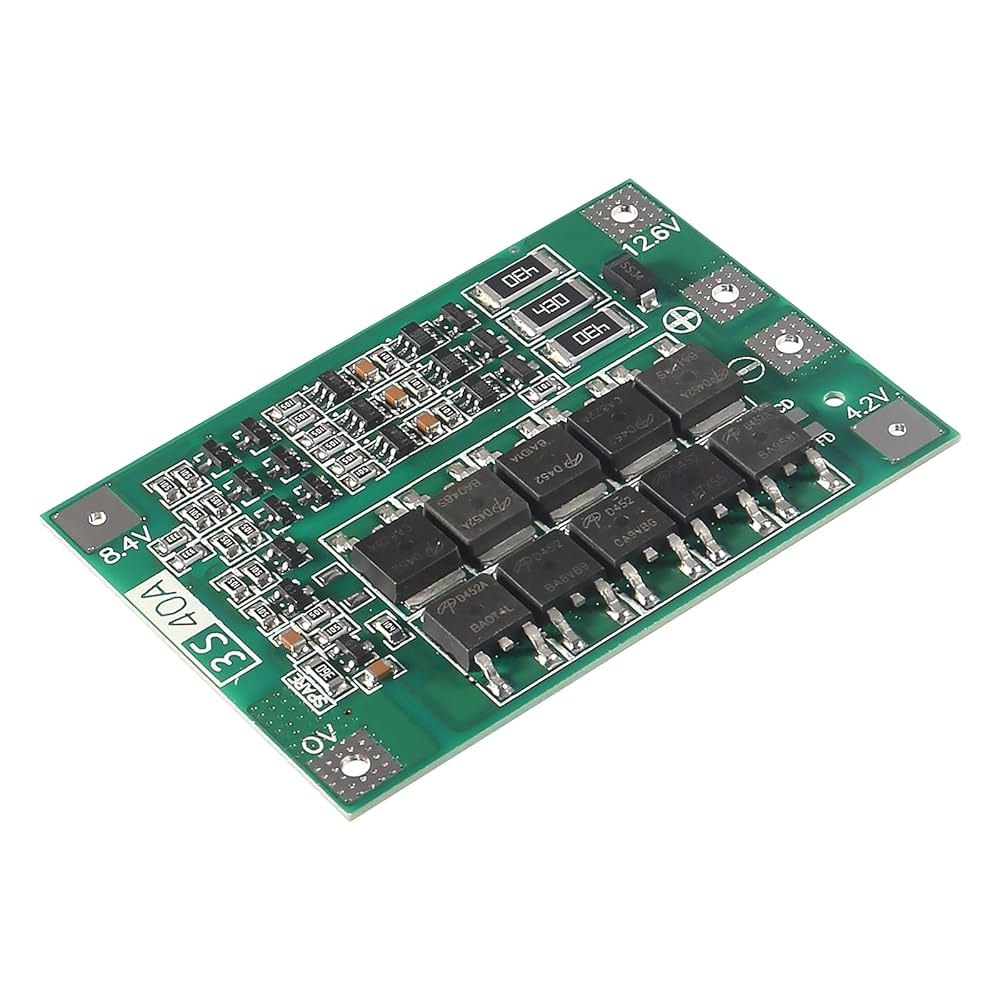
How to Shield BMS PCBs from High-Voltage Noise Without Breaking the Budget?
Cost-effective strategies to shield BMS PCBs from high-voltage noise
Prioritize TVS Diodes for Transient Voltage Suppression
- Implementation: Install TVS diodes at power inputs and critical signal lines (e.g., CAN bus, sensor interfaces).
- Why: Clamps high-voltage spikes from load dumps or inductive switching, diverting excess energy to ground.
- Cost Efficiency: Low-cost unidirectional/bidirectional TVS arrays (e.g., SMAJ series) provide robust protection without complex circuitry.
Optimize PCB Layout for Noise Isolation
- Ground Plane Strategy: Use dedicated ground layers for analog/digital sections. Separate high-current paths (e.g., battery cell balancing) from low-voltage sensor traces.
- Trace Routing: Keep high-voltage traces >2mm from sensitive signals. Avoid 90-degree bends to minimize impedance discontinuities.
- Decoupling: Place 0.1µF ceramic capacitors near every IC power pin and 10µF electrolytic capacitors at PCB entry points.
Leverage Ferrite Beads for HF Attenuation
- Application: Insert ferrite beads (e.g., Murata BLM series) in series with power lines to the MCU and communication modules.
- Benefit: Dissipates high-frequency noise as heat without affecting DC power delivery.
- Budget Tip: Use multi-layer chip inductors (e.g., 1206 size) for cost-effective EMI filtering.
DIY Shielding with Copper Tape or Aluminum Enclosures
- Low-Cost Enclosure: Line BMS housing with adhesive copper foil (≤$5 for 1m²) and connect to PCB ground.
- Gap Management: Seal seams with conductive gasket tape to prevent electromagnetic leakage.
- Alternative: Repurpose aluminum tooling plates as shields, secured with nylon screws to avoid ground loops.
Software Filtering for Noisy Sensors
- Algorithm: Implement a moving average or Kalman filter in BMS firmware to smooth voltage/current readings.
- Example: Apply a 10-sample moving average to cell voltage data to reject transient spikes from motor noise.
- Zero Hardware Cost: Leverage unused MCU flash memory to store filter coefficients.
Isolation Techniques for Critical Nodes
- Optocouplers: Use low-cost optoisolators (e.g., PC817) for relay drivers or charge enable signals.
- Digital Isolators: For CAN/RS-485 interfaces, adopt cost-effective isolators like ISO7741 (under $2 in qty).
- Galvanic Separation: Prevent ground loops by isolating high-voltage sampling circuits from the main MCU.
What Is A BMS Protection PCB Board?
A BMS protection PCB board is a dedicated hardware solution designed to ensure battery pack safety by monitoring critical parameters in real time. This printed circuit board tracks cell voltages, pack current, and temperature distribution while comparing these values against predefined safety thresholds. When detecting unsafe conditions like overvoltage, undervoltage, excessive current, or high temperatures, it activates protective measures through control elements such as power MOSFETs to isolate the battery. The board also incorporates cell balancing functions, state-of-charge estimation, and communication interfaces to relay system status. Its primary purpose is to provide autonomous hardware-level protection that prevents catastrophic failures while maintaining safe battery operation.
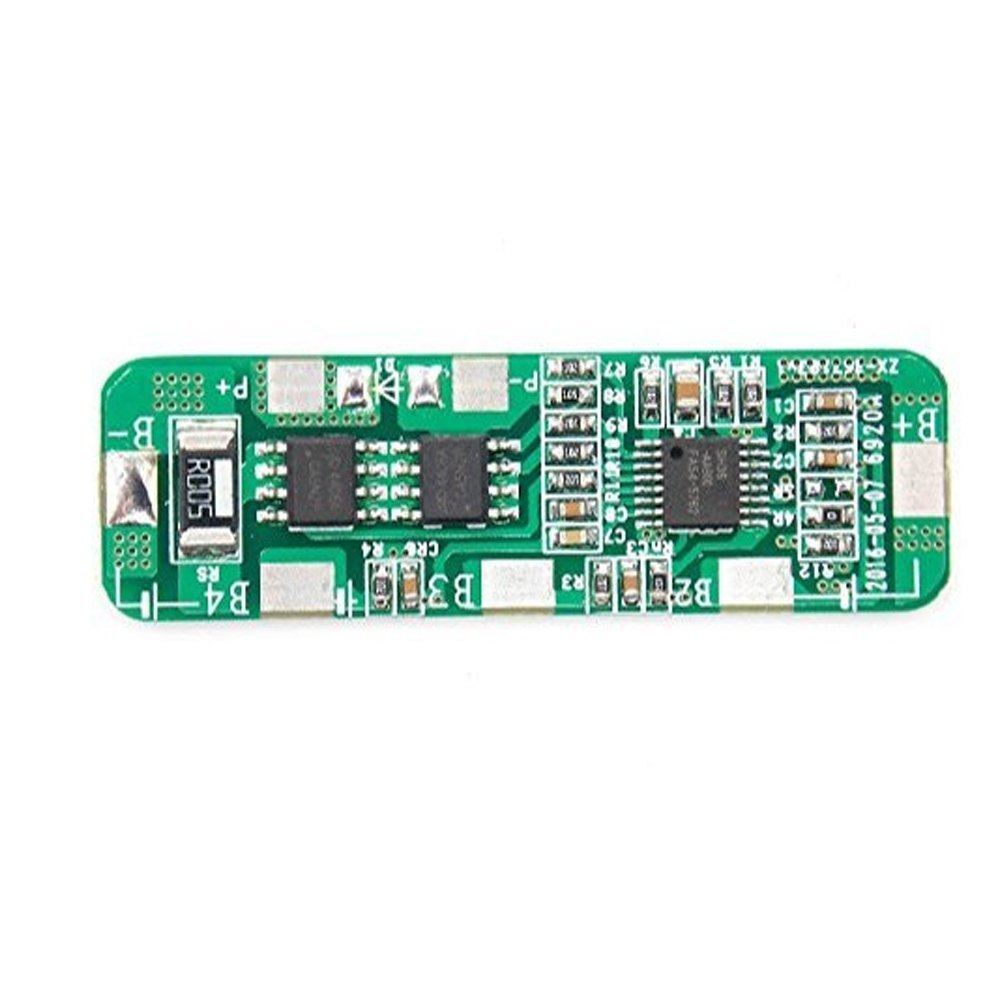
How to Use PCB BMS Protection Board for 18650s?
How to use a PCB BMS protection board for 18650 batteries:
1. Inspect the BMS and Batteries
- Confirm the BMS matches your 18650 cell count (e.g., 4S for four 3.7V cells in series).
- Check battery voltage with a multimeter to ensure no cell is below 2.5V before connecting the BMS.
2. Wire the Battery Pack
- Connect the battery pack’s negative terminal to the BMS B- port using 16–20 AWG silicon wire.
- Route each cell’s balance wire (B1+, B2+, etc.) to the corresponding BMS balance ports. Avoid crossing wires to prevent short circuits.
3. Connect Charger and Load
- Attach the charger’s negative lead to the BMS P- port and positive lead to the battery pack’s positive terminal.
- Connect the load (e.g., device, inverter) to the same P- port and pack positive, ensuring the load’s current draw does not exceed the BMS rating.
4. Secure and Ventilate the BMS
- Mount the BMS using nylon standoffs to prevent contact with metallic surfaces.
- Ensure adequate airflow around the BMS, especially if it lacks built-in heat sinks.
5. Initial Power-Up and Testing
- Charge the pack at 0.5A–1A initially to verify the BMS triggers overcharge protection at 4.25V per cell.
- Discharge the pack with a low-power load (e.g., LED light) to test over-discharge cutoff at 2.5V per cell.
6. Balance Cells Regularly
- After 3–5 cycles, use a battery analyzer to check cell voltages. Manually discharge any cell exceeding 4.2V using a resistor.
- Avoid full discharges to minimize voltage imbalance between cells.
7. Monitor Temperature and Connections
- Check for overheating near MOSFETs during high-current use. Reduce charge/discharge current if temperatures exceed 60°C.
- Tighten terminals monthly to prevent loose connections, which can cause erratic behavior.
8. Replace Aging Components
- Inspect capacitors for bulging every 12 months. Replace if signs of leakage or swelling appear.
- Upgrade to a BMS with higher current ratings if using the pack for high-drain applications (e.g., e-bikes).
How to Choose PCB BMS Protection Board for 18650?
Match Cell Count and Voltage
- Choose a BMS that supports your battery pack’s configuration (e.g., 4S for four 3.7V cells in series).
- Verify the BMS’s maximum voltage rating exceeds your pack’s fully charged voltage (e.g., 16.8V for a 4S pack).
Check Current Ratings
- Select a BMS with a continuous discharge current rating 20% higher than your application’s peak demand (e.g., 30A BMS for a 25A e-bike motor).
- Ensure the charge current rating aligns with your charger’s output (e.g., 5A BMS for a 4A charger).
Evaluate Protection Features
- Prioritize boards with overcharge, over-discharge, over-current, and short-circuit protection.
- Look for optional features like cell balancing, temperature sensors, and low-voltage recovery modes.
Inspect Physical Design
- Choose a BMS with labeled terminals and spaced-out ports to simplify wiring.
- Prioritize models with integrated NTC thermistor ports for precise temperature monitoring.
Verify Communication Protocols
- For smart packs, ensure the BMS supports your device’s protocol (e.g., I2C, SMBus) or includes Bluetooth/Wi-Fi for remote monitoring.
- Test compatibility with your charger or energy meter before finalizing.
Review User Feedback
- Check forums or reviews for reports of false triggers, uneven balancing, or premature MOSFET failures.
- Avoid boards with frequent complaints about solder joint quality or inaccurate voltage readings.
Balance Cost and Longevity
- Avoid ultra-cheap BMS units with thin traces or generic MOSFETs, as they may fail under stress.
- Invest in models with replaceable fuses or upgradeable firmware for future-proofing.
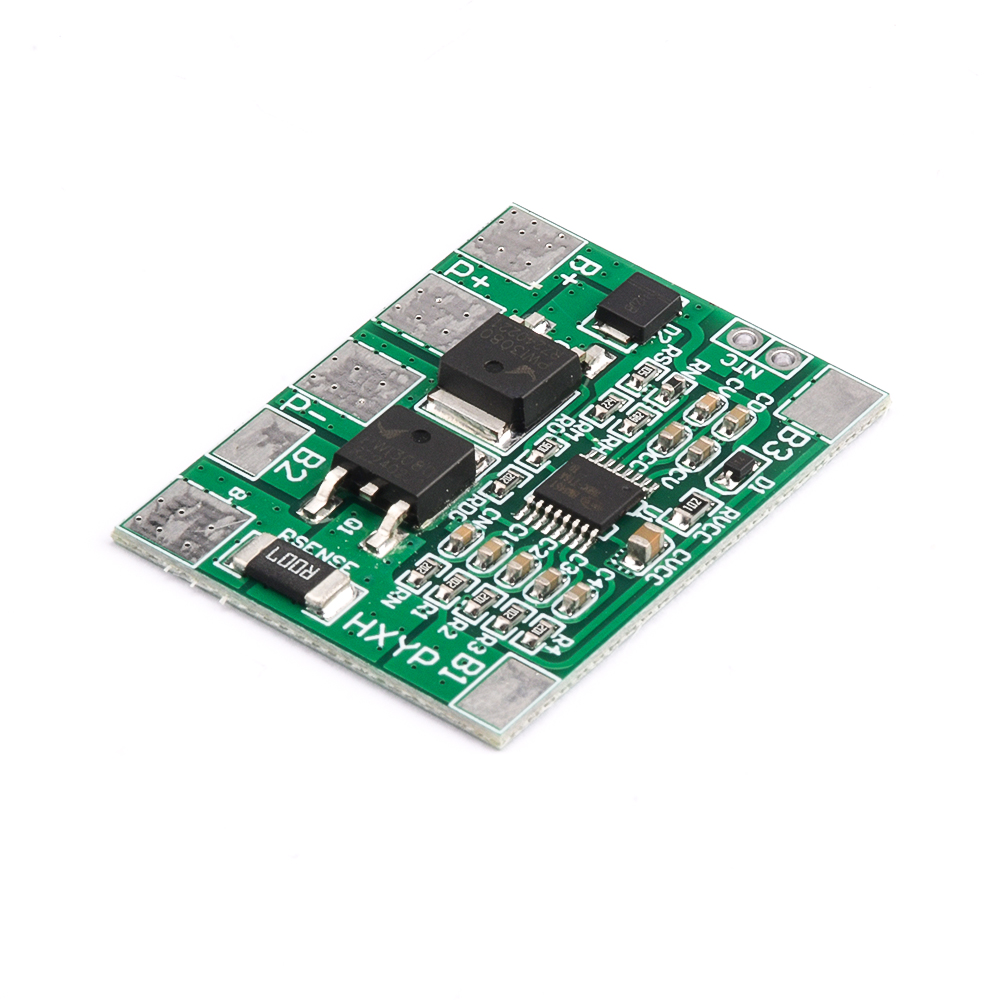
How to Balance Cost and Stability of BMS PCB Protection Board for 18650?
Here are actionable tips to balance cost and stability when selecting a PCB BMS protection board for 18650 batteries:
Prioritize Essential Protections Over Premium Add-Ons
- Ensure the PCB BMS protection board includes core features: overcharge, over-discharge, over-current, and short-circuit protection. These are non-negotiable for safety.
- Avoid paying extra for advanced functions like Bluetooth monitoring or active cell balancing unless your application requires them.
Evaluate Component Quality Carefully
- Check for MOSFETs with mid-range current ratings (e.g., 40V/60A vs. 80A+). They offer sufficient durability for most 18650 packs without inflating costs.
- Look for ceramic capacitors instead of electrolytic ones for better temperature stability and longer lifespan.
Balance Current Ratings with Real-World Needs
- Choose a PCB BMS protection board with a continuous discharge rating 10–20% above your system’s maximum draw (e.g., 25A BMS for a 20A tool). This avoids over-engineering costs.
- Avoid boards rated far beyond your requirements, as higher current tolerance often increases price disproportionately.
Leverage Passive Cell Balancing
- Opt for PCB BMS protection boards with passive balancing (resistor-based) instead of active balancing (inductor-based). Passive designs are cheaper and sufficient for most 18650 applications.
- Ensure the balancing current is ≥50mA to maintain cell health over hundreds of cycles.
Inspect Trace Width and PCB Thickness
- Choose a board with 2oz copper traces and a minimum thickness of 1.6mm. These specs reduce resistance and heat buildup without adding significant cost.
- Avoid ultra-thin PCBs (e.g., 0.8mm), as they may warp or delaminate under stress.
Check for Replaceable Fuses or Resettable PTCs
- Some PCB BMS protection boards include user-replaceable fuses or polymer PTCs (resettable breakers). These features extend the board’s lifespan by allowing recovery from overcurrent events.
- Compare costs: A board with a $0.50 PTC may outlast three cheaper boards without this feature.
Review Open-Source Firmware Options
- Select a PCB BMS protection board with publicly available firmware (e.g., via GitHub). This lets you customize protections or fix bugs without relying on the manufacturer.
- Community-supported boards often have lower long-term maintenance costs due to shared troubleshooting resources.
Conclusion
In conclusion, this guide has comprehensively covered the essential aspects of BMS PCB protection boards for 18650 battery systems, from fundamental concepts to practical wiring techniques, thermal management solutions, and cost-effective noise shielding approaches. We’ve explored proper usage methods, selection criteria, and the critical balance between performance and affordability. For reliable battery management systems that prioritize both safety and efficiency, these components prove indispensable. Should you require high-quality BMS PCB solutions tailored to your specific 18650 applications, we recommend contacting Best Technology for professional consultation and competitive pricing. Their expertise ensures optimal battery protection while meeting your technical and budgetary requirements. Welcome to contact us: sales@bestpcbs.com.