Are you always curious these questions about insulated metal substrate PCB:
What is insulated metal substrate? Does it the same as metal core PCB (MCPCB)?
What are the key differences between insulated metal substrate and standard PCB?
Can I use insulated metal substrate in my project? What’s its performance?
As a experienced PCB manufacturer, we can confident to say the insulated metal substrate (IMS) PCB is the same as mcpcb, there is no differences between them. But it is big differ from standard PCB. Actually, IMS PCB offer numerous benefits in high power or heat sensitive projects. In this blog we will introduce what is it, its performance and the differeces with FR4 PCB.
What is an Insulated Metal Substrate (IMS)?
An insulated metal substrate (IMS) is a type of metal core PCB designed for heat-intensive applications. Unlike traditional FR4 boards, IMS uses a metal base layerāusually aluminum or copperācovered with a thin dielectric insulation and a copper circuit layer on top.
The purpose of this design is simple: dissipate heat quickly while keeping the circuit stable. Aluminum IMS boards are most common, offering a balance of cost, strength, and thermal conductivity. Copper IMS is used where performance is critical, especially in high-current applications.
Key characteristics of IMS PCBs include:
- High thermal conductivity to transfer heat away from components.
- Strong mechanical stability compared to FR4.
- Reliable performance in harsh environments.
For industries like LED lighting, automotive electronics, and power supplies, IMS PCBs have become a preferred choice.
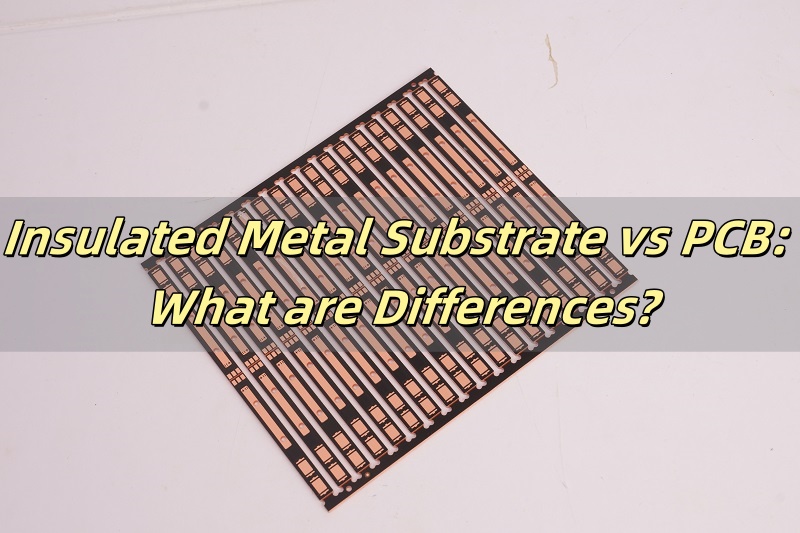
What is IMS material for PCB?
The performance and cost of an insulated metal substrate PCB depend heavily on the choice of the base material. Different metals give different levels of thermal conductivity, mechanical strength, and pricing.
1. Copper IMS PCB
Copper has the best thermal conductivity among IMS options. It spreads heat rapidly and is highly stable under load. However, copper is expensive, so it is often reserved for high-power applications such as industrial converters or advanced automotive modules.
2. Aluminum IMS PCB
Aluminum is the most common choice for IMS PCBs. It strikes a balance between cost, weight, and thermal performance. With good heat dissipation and lower price than copper, it has become the preferred material in LED lighting and consumer automotive systems.
3. Iron IMS PCB
Iron-based substrates are rarely used. While they are strong, their lower thermal performance and processing challenges make them less attractive. In most cases, aluminum and copper dominate the IMS market.
What is a Traditional PCB?
A traditional PCB typically refers to a board made with FR4 substrate. FR-4 is a code for a fire-resistant material grade. It represents a material specification where the resin material must be able to extinguish itself when exposed to a burning condition. It is not a material name but a material grade. Most consumer electronics use FR4 PCBs because they are affordable and easy to manufacture.
The construction includes:
- Fiberglass base (FR4) for insulation and strength.
- Copper foil laminated on one or both sides.
- Solder mask and silkscreen for protection and labeling.
FR4 PCBs work well in devices that do not generate extreme heat. They are versatile and suitable for phones, laptops, IoT devices, wearables, and household appliances.
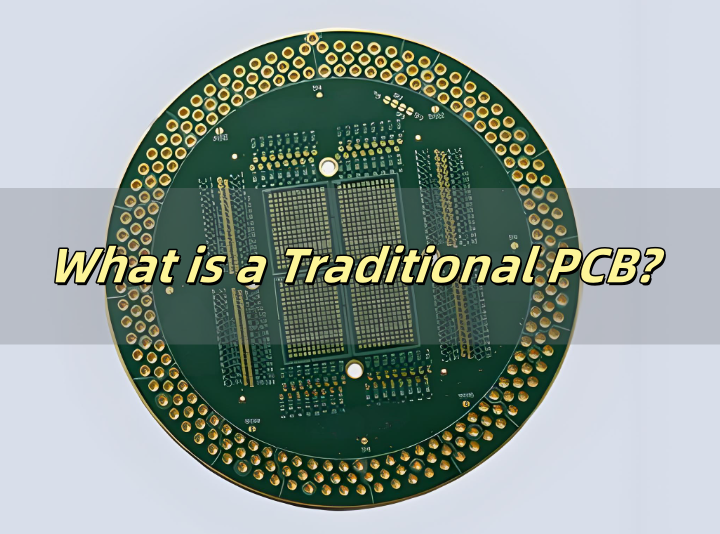
What is the Difference Between Insulated Metal Substrate and PCB?
The key differences between ims pcb and traditional PCB is the base material, IMS pcb uses metal core as the base substrate while traditional PCB uses fiberglass epoxy. Due to the differences base materials used, their performance, price and applications are different accordingly. Here we listing a detailed table for your reference:
Feature | Traditional PCB (FR4) | Insulated Metal Substrate (IMS) |
Base Material | Fiberglass epoxy (FR4) | Metal base (aluminum or copper) |
Thermal Conductivity | Low (~0.3 W/mK) | High (2ā10 W/mK dielectric + metal base can reach up to 400 W/mk) |
Heat Management | Needs extra cooling (heat sinks, fans) | Built-in heat spreading through metal layer |
Mechanical Strength | Rigid but less durable under vibration | Strong, resists shock and vibration |
Flexibility | Can be rigid, flex, or rigid-flex | Mostly rigid only |
Applications | Consumer electronics, IoT, computers | LED lighting, automotive, power modules |
Cost | Low, highly economical for mass production | Higher, due to materials and processing |
Why is IMS Better for Heat Dissipation Compared to PCB?
As we all know, heat is the biggest enemy of electronic components. If heat builds up, components degrade, solder joints crack, and lifespan shortens. Standard FR4 struggles to move heat away, leading to performance issues in high-power systems.
An IMS PCB solves this by using a metal base that acts like a built-in heat sink. The dielectric layer transfers heat from components directly to the metal, which spreads it out quickly. This keeps the board and devices cooler and improves the overall reliability.
This is why IMS PCBs are widely used in LED lighting, where heat directly impacts brightness and lifespan. Similarly, automotive systems like motor controllers and power converters use IMS to handle constant high currents.
Which Applications Do We Use IMS vs Standard PCB?
Each type of board has its own application areas.
IMS PCB applications
- LED lighting systems
- Automotive electronics (engine control units, sensors, chargers)
- Power modules and converters
- Industrial motor drives
- Telecom base stations
FR4 PCB applications
- Consumer electronics (phones, tablets, laptops)
- IoT devices and smart wearables
- Household appliances
- Audio and multimedia systems
- Office electronics
The decision depends on the heat level, power density, and cost balance.
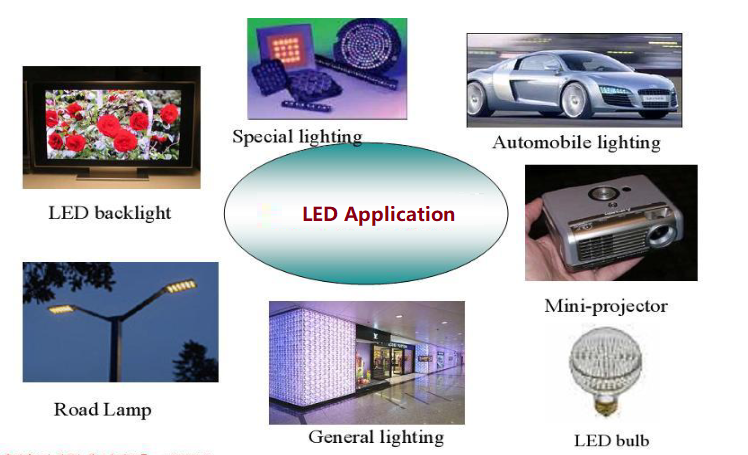
Cost Differences Between IMS and PCB
IMS PCBs are more expensive than standard FR-4 boards due to their raw materials and processing steps. Aluminum-based IMS typically costs $0.12ā$0.25 per cm², while FR-4 falls around $0.05ā$0.10 per cm². Extra copper thickness, dielectric layers, and specialized drilling add further expense.
Yet, the higher upfront cost can translate into system savings. In LED lighting, automotive, and power modules, IMS often reduces the need for heat sinks or cooling parts. Studies show a 15ā20% drop in overall system cost when FR-4 is replaced with IMS, thanks to better thermal control and longer product life.
Design Consideration of Insulated Metal Substrate PCB
Designing an Insulated Metal Substrate (IMS) PCB is more than just replacing FR4 with a metal base. The entire design strategy changes because thermal performance becomes the top priority. Several aspects need careful thought:
1. Dielectric Layer Thickness and Thermal Conductivity
The dielectric is the heart of an IMS PCB. Its job is to provide electrical insulation while transferring heat from the copper layer to the metal base.
- Typical FR4 dielectric has thermal conductivity of 0.3ā0.5 W/mK.
- IMS dielectrics range from 2 to 10 W/mK, depending on material choice.
- Thickness is usually 50ā150 μm. Thinner layers transfer heat better but risk breakdown if not well controlled.
For normal LED boards, a 75 μm dielectric with 1-2 W/mK conductivity is often a balance between cost and reliability.
2. Copper Thickness and Trace Design
Current capacity is vital. Wider traces reduce resistance and heat buildup.
- Standard FR4 PCBs often use 1 oz (35 μm) copper.
- IMS boards commonly use 2ā3 oz (70ā105 μm) copper to carry higher currents.
IPC-2221 guidelines suggest that a 2 oz copper trace at 10 mm width can handle around 20ā25 A continuously, which fits the demands of power devices.
3. Component Placement and Thermal Management
Hot components, such as MOSFETs, LEDs, or regulators, should be placed directly over areas where heat can spread into the metal base efficiently. Grouping high-power parts together without proper spacing often leads to localized hot spots.
Simulation tools (like ANSYS or thermal CAD software) are often used to map temperature rise. Data shows that placing components 5 mm apart can reduce local heat rise by 8ā12°C compared to tightly packed layouts.
4. Board Thickness and Mechanical Strength
IMS boards are stiffer than FR4 due to the metal layer.
- Common thickness: 0.8ā3.2 mm.
- For automotive PCBs exposed to vibration, a 1.6 mm aluminum base is typical for balancing rigidity and weight.
Designers should consider mounting holes and mechanical supports early to avoid stress cracking during assembly.
5. Surface Finishes and Soldering
Surface finishes like ENIG, ENEPIG, OSP or HASL are commonly applied. However, IMS boards undergo more thermal cycling during soldering, so ENIG is often preferred for reliability.
Factors Affect the Failure of Insulated Metal Substrate PCB
Even with proper design, IMS PCBs can fail if certain risks are not controlled. Failures usually stem from thermal, mechanical, or environmental stresses. Letās examine the main causes, with supporting data:
1. Thermal Stress and Cycling
IMS PCBs are exposed to wide temperature swings, especially in LED lighting (-40°C to +120°C) or automotive control units (-55°C to +150°C). In additional, a thinner dielectric layer (<75 μm) is more likely to fail under repeated expansion and contraction. So, using high Tg dielectrics (Tg ℠170°C) and flexible solder materials reduces the chance of cracks.
2. Dielectric Breakdown
The dielectric layer separates copper circuitry from the conductive metal base. If the insulation fails, short circuits occur.
- Standard IMS dielectric breakdown voltage: 2ā6 kV/mm.
- If the dielectric is too thin or contaminated during manufacturing, breakdown may occur earlier, especially in high-voltage power supplies.
3. Corrosion and Moisture Ingress
If the protective coating or solder mask is not properly applied, moisture, chemicals, or salts can corrode the copper traces or the aluminum base. There is no doubt that unprotected copper can corrode in under 72 hours in a salt spray environment (5% NaCl). Therefore, applying ENIG or OSP surface finishes greatly reduces corrosion risk.
4. Mechanical Stress and Vibration
IMS boards are less flexible than FR4, which means they can crack under excessive bending or vibration.
- In automotive vibration testing (10ā2,000 Hz sweep, 20 g), poor mounting caused delamination in 5ā10% of samples after 50 hours.
- Proper mechanical design (screw supports, standoffs, thicker bases) minimizes this risk.
5. Manufacturing Defects
Poor drilling, lamination errors, or uneven dielectric spreading can lead to early failures. For example:
- Misaligned lamination can create voids, which increase heat resistance and raise local temperatures by 10ā15°C.
- Improper drilling of vias in IMS can leave burrs or microcracks, leading to premature electrical failure.
Best Technology has more than 19 years in IMS PCB manufacturing. It cannot be denied that we had ever faced such problems and solved them finally, then we have much experiences to solve them and mature skills to avoid such defectives.
Insulated Metal Substrates Market
The insulated metal substrates market has grown rapidly with the demand for efficient heat management in electronics. Several sectors drive this expansion:
- LED Lighting: As LEDs move into general lighting, street lamps, and automotive headlights, IMS boards remain essential for heat control.
- Electric Vehicles (EVs): Motor controllers, inverters, and battery systems require durable IMS boards to handle high currents.
- Industrial Power Systems: Power converters, motor drives, and renewable energy inverters are major adopters.
- Telecom: Base stations and 5G equipment rely on IMS to stabilize performance under heavy workloads.
Market reports suggest steady growth in IMS adoption worldwide, especially in Asia-Pacific regions like China and South Korea, where LED and EV industries are booming. Aluminum IMS PCBs dominate due to cost efficiency, but copper IMS is growing in high-performance niches.
How to Choose Between IMS PCB and FR4 PCB?
The choice between IMS PCB and FR-4 PCB depends on performance demands, cost expectations, and application environment. If your design handles high power density or generates significant heatāsuch as in LED lighting, power converters, or automotive control unitsāIMS PCB is usually the better option. Its aluminum or copper base provides strong thermal conductivity, keeping component temperatures 20ā30% lower than FR-4 under the same load.
FR-4 PCB, on the other hand, is more suitable for general-purpose electronics where heat generation is moderate. Devices like consumer gadgets, IoT sensors, and low-power communication modules often prioritize affordability and flexibility in design over extreme thermal performance. FR-4 also supports higher multilayer counts more easily than IMS, which is beneficial for complex circuits with dense routing.
So, in a word:
- Choose FR4 PCB if your device is low-power, cost-sensitive, and not heat-intensive.
- Choose IMS PCB if your design generates high heat, requires high reliability, or operates in harsh environments.
In practice, many manufacturers use both types in their product lines. Consumer electronics stay with FR4, while lighting and automotive turn to IMS.
FAQs
1. What materials are used in insulated metal substrates?
IMS PCBs usually use aluminum or copper as the base, with a dielectric insulation layer and copper foil.
2. Is IMS PCB more reliable than FR4 PCB?
Yes, especially in high-power or high-heat applications, IMS offers better thermal management and durability.
3. Can IMS replace all standard PCBs?
No, IMS is designed for specific heat-demanding uses. FR4 remains more cost-effective for everyday electronics.
4. Why are IMS PCBs used in LED lighting?
They transfer heat away quickly, improving brightness, efficiency, and lifespan of LEDs.
5. How expensive are IMS PCBs compared to normal PCBs?
IMS PCBs cost more due to metal materials and manufacturing, but they often save costs by reducing cooling needs.
About Best Technology – Your Trust Insulated Metal Substrate PCB Supplier
Best Technology is a turnkey PCB & PCBA manufacturer in China, we specialize in the design and manufacturing of high-quality PCBs, and we are confident that we can provide a tailored solution for your project. With our expertise and a broad range of materials, including SY, Rogers, Isola, KB, ceramic, metal core pcb, flex circuit and busbar copper pcb, etc, we offer flexibility and reliability for all your PCB designs.
We’ve made many PCBs for our customers, whether you need high-speed, high-frequency, or multi-layer PCBs, our experienced engineering team ensures reliable, cost-effective designs with excellent manufacturability. We’ve worked in this industry over 19 years, so we deeply know what our customers want, and make them into reality.
Our services include:
- Customized PCB design based on your schematic and specifications
- Free Design for manufacturability (DFM) to reduce production issues
- Optimization for signal integrity, thermal management, and reliability
- PCB layout and PCB design full turnkey service
Industry certifications we have:
- ISO9001 (quality management system)
- IATF16949 (for automotive device)
- ISO13485 (for medical instrument)
- AS9100D (aerospace applications)
In addition to our advanced PCB manufacturing capabilities, we also have a fully equipped SMT factory both in China & Vietnam. This facility is dedicated to providing our customers with professional PCB assembly services, including SMD soldering, component placement, and testing. This allows us to offer a complete solution, from PCB fabrication to final assembly, all under one roof. If you have PCB or IMS PCB manufacturing demands, welcome to contact us at sales@bestpcbs.com