How to design copper PCB plate? This guide covers substrate specs, design guidelines, thermal solution. manufacturing processes for copper PCB plate.
- Are your 5G base station power devices experiencing performance degradation due to insufficient heat dissipation?
- New energy vehicle PCBs are delaminated under high temperature conditions. How to break through the reliability bottleneck?
- In high current carrying scenarios, does the thermal expansion coefficient of traditional FR4 substrates affect device life?
Best Technology Can Provide:
- Customized copper substrates – through the combination of ā„2oz copper thickness + ceramic filling dielectric layer, the thermal conductivity is increased to 400W/mK, ensuring that the temperature rise of high-power devices is reduced by 30%.
- CTE matching technology – using copper/aluminum composite substrates, the thermal expansion coefficient is perfectly matched with semiconductor devices to avoid the risk of high-temperature delamination.
- Modular thermal management design – integrated embedded heat pipes and optimized via arrays to achieve stable operation at 15A/mm² current density.
Welcome to contact us if you have any request for copper PCB: sales@bestpcbs.com.
What Is A Copper PCB Plate?
A copper PCB plate is a printed circuit board using solid copper as its primary substrate material. This design fundamentally replaces standard insulating substrates like FR-4 with a dense copper core, serving simultaneously as the circuit’s structural foundation and primary heat dissipation medium.
The construction bonds dielectric insulation layers and conductive copper foils directly to the copper base. This integration leverages copperās inherent thermal conductivity to absorb and transfer heat from electronic components, establishing an efficient thermal pathway while maintaining electrical isolation.
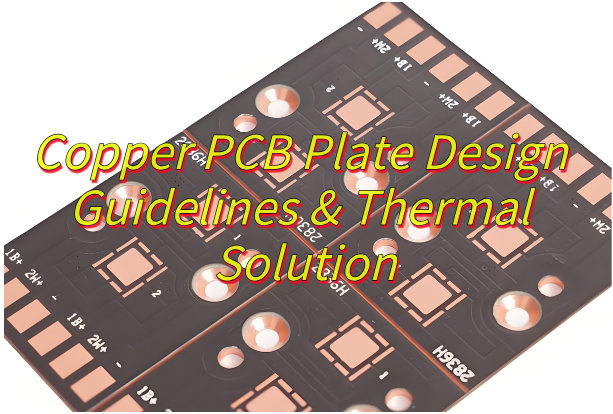
Copper Substrate PCB Specification
Parameter | Specification Range |
Copper Thickness | Standard: 1oz(35μm), 2oz(70μm)ļ½Heavy: 3oz(105μm)-10oz(350μm)ļ½Selective: 3-8oz |
Substrate Thickness | 0.2mm-3.2mm (Aluminum core typical 1.0mm/1.5mm/2.0mm) |
Thermal Conductivity | 1-8W/(mĀ·K) (Aluminum core typical 2-3W) |
Dielectric Strength | AC 1kV-4kV (2.5kV@1mm substrate spacing) |
Max Panel Size | Single/Double-side: 800Ć1200mmļ½Multilayer: 610Ć1100mm |
Copper Type | Rolled (high ductility)ļ½Electrodeposited (standard) |
Surface Finish | HASL(LF), ENIG, OSP, Immersion Ag (ENIG preferred for impedance control) |
Min Trace/Space | 1oz: 4/4milļ½3oz: 8/12mil (IPC-2152 current carrying capacity required) |
Application of Copper PCB Plate
- Automotiveā – EV battery management, motor controllers, charging systems.
- Telecomā – 5G/6G base stations, RF power amplifiers, antenna modules.
- Industrialā – Welding machines, UPS, solar inverters, robotics.
- Aerospaceā – Satellite comms, avionics, radar systems.
- Medicalā – MRI equipment, surgical lasers, X-ray generators.
- Consumerā – High-end smartphones, gaming consoles, AR/VR devices.
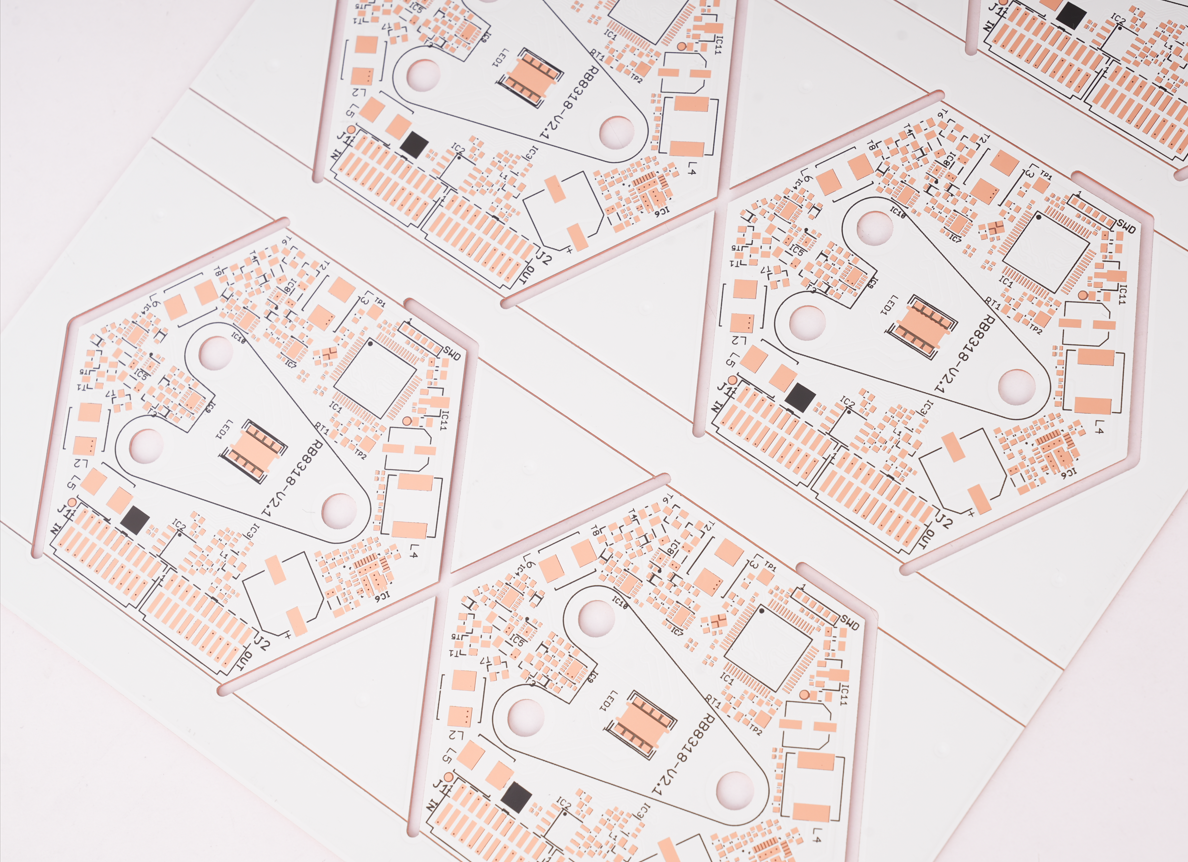
Copper PCB Plate Design Guidelines
1. Material Selection & Thickness
- Use copper foil thickness based on current requirements: 1oz (35μm) for standard applications, 2oz (70μm) or thicker for high-current designs.
- Inner layer copper thickness ā„0.5oz; outer layers add 0.5oz to base thickness.
- Ensure dielectric layer thickness ā„0.1mm to prevent voltage breakdown.
2. Layout & Layer Stackup
- Adopt symmetric design for dielectric layers, copper thickness, and trace distribution.
- Separate high-speed/low-speed, digital/analog, and power/ground planes using spatial isolation or dedicated ground lines.
- Place high-power components centrally for even heat distribution; avoid clustering.
3. Thermal Management
- Increase copper area under high-power devices to act as a heat spreader.
- Use thermal vias to connect top/bottom layers, transferring heat to a dedicated thermal pad.
- For currents >10A, opt for ā„2oz copper and widen traces to reduce resistance.
4. Signal Integrity
- Maintain 3W rule (trace spacing ā„3Ć trace width) to minimize crosstalk.
- Route high-speed signals (e.g., clock lines) away from noisy power lines.
- Ensure impedance control for differential pairs and critical nets.
5. Manufacturing Considerations
- Follow IPC-2221 for trace width/spacing and IPC-6012 for quality classes (Class 3 for aerospace/medical).
- Avoid sharp angles (>135°) to prevent EMI and manufacturing defects.
- Use solid or hatched copper pours with clearances ā„0.2mm from pads/vias.
6. Power & Ground Design
- Dedicate separate power/ground planes for analog/digital sections.
- Widen power traces and use multiple vias for low-impedance paths.
- Implement local decoupling capacitors near ICs (ā¤0.3mm from power pins).
7. Drilling & Plating Design
- For thick copper (>4oz), optimize drill parameters to mitigate copper smearing and burrs.
- Ensure hole wall plating thickness ā„25μm for Class 3 reliability.
8. Testing & Validation
- Perform thermal imaging to validate heat dissipation in high-power zones.
- Use impedance testing for high-speed signals and electrical continuity checks.
- These guidelines balance performance, manufacturability, and reliability while adhering to industry standards.
Copper PCB Plate Thermal Solution in Electric Vehicles
Five Thermal Solutions for Copper PCB Plates in Electric Vehicles
1. High-Conductivity Substrates & Thick Copper Layers
- Use metal-core PCBs (MCPCB) or ceramic substrates (AlāOā/AlN) with thermal conductivity >1.5 W/mĀ·K for power modules.
- Apply localized thick copper (ā„2oz/70μm) on high-current traces to reduce Joule heating and enhance heat spreading.
2. Dense Thermal Via Arrays Under High-Power Components
- Place thermal vias (diameter 0.3ā0.5mm, pitch 1.0mm) directly beneath IGBTs, MOSFETs, or DC-link capacitors.
- Fill vias with copper or conductive paste to eliminate air gaps and improve vertical heat transfer.
3. Zoning & Component Placement Optimization
- Centralize heat-generating devices near liquid cooling channels or heat sinks.
- Maintain ā„5mm spacing between high-voltage (>600V) and low-voltage circuits to prevent thermal crosstalk.
4. Hybrid Cooling Integration
- Combine PCB thermal vias with active cooling (e.g., microchannel liquid cooling plates) for modules exceeding 200W.
- Use phase change materials (PCMs) or graphite sheets between PCB and housing for passive thermal buffering.
5. Simulation-Driven Design & Automotive-Grade Validation
- Perform CFD thermal modeling (e.g., ANSYS Icepak) to optimize via density and material selection.
- Validate through power cycling tests (200A, 1000+ cycles) and thermal shock (-40°C to +150°C) per AEC-Q100 standards.
How Was Copper Base PCB Made?
Production Processes of Copper Base PCB:
1. Material Selectionā: Start with 99.9% pure copper plates (1-10mm thickness) and thermally conductive dielectric layers (typically aluminum nitride or ceramic-filled polymer).
2. Surface Treatmentā: Chemically clean copper surfaces to achieve <0.5μm roughness, then apply oxidation-resistant coating for better bonding.
3. Pattern Transferā: Laminate dry film photoresist onto copper, expose with UV light through designed artwork, then develop to create circuit patterns.
4. Precision Etchingā: Use ammoniacal etching solution maintained at 45±2°C to remove unwanted copper, achieving 50μm line width tolerance.
5. Dielectric Bondingā: Sandwich thermally conductive dielectric between copper layers under 180°C and 15kg/cm² pressure for 90 minutes.
6. Drilling & Platingā: Drill micro-vias with 0.1-0.3mm diameter using laser ablation, then electroless copper plate the hole walls.
7. Solder Mask Applicationā: Screen-print high-temperature resistant ink (withstand 260°C for 60s), cure with infrared for enhanced thermal cycling performance.
8. Surface Finishingā: Apply ENIG (Electroless Nickel Immersion Gold) or silver plating for optimal solderability and heat dissipation.
9. Electrical Testingā: Perform 100% continuity test with 500V DC and thermal impedance measurement using ASTM D5470 standard.
10. Final Inspectionā: Verify dimensional accuracy (±0.05mm) and thermal conductivity (300-500W/mK range) before vacuum packaging.
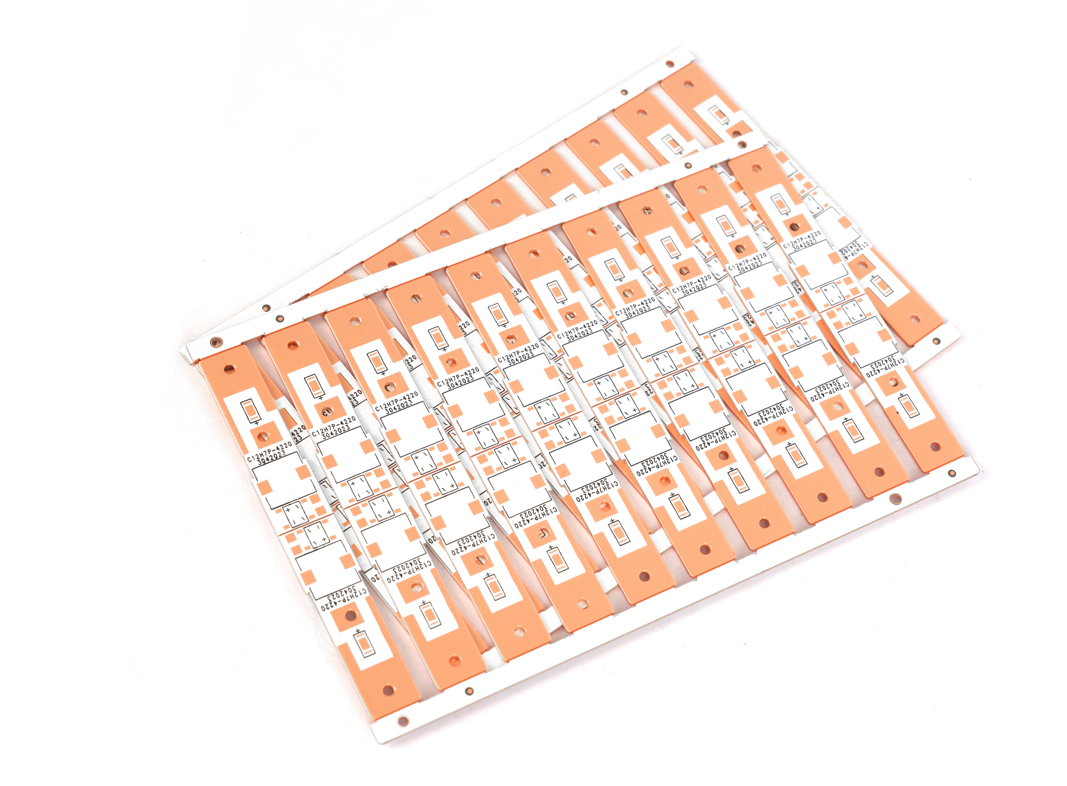
Reliability Compliance Testing for Copper Substrate PCB
1. Thermal Cycling Endurance Validationā
- Execute 1,000 rapid temperature cycles between -55°C and +150°C following IPC-9701. Confirm thermal conductivity maintains within ±5% deviation to ensure long-term stability in automotive applications.
2. Dielectric Withstand Voltage Testā
- Apply 3.5kV AC for 60 seconds between adjacent copper layers per UL 94V-0. Terminate testing if leakage current exceeds 10mA, guaranteeing insulation integrity in high-voltage designs.
3. Thermal Shock Resistance Assessmentā
- Transition boards between -65°C and +175°C chambers within 10 seconds per JEDEC JESD22-A106B. Inspect for delamination after 300 cycles using scanning acoustic microscopy.
4. Solder Reflow Compatibility Checkā
- Immerse test coupons in 288°C solder bath for 30 seconds (IPC-TM-650 2.6.8). Verify dimensional change <0.2% and solder mask adhesion strength >1.0kgf/cm² post-test.
5. Humidity Aging Evaluationā
- Condition samples at 85°C/85% RH for 168 hours (JESD22-A101). Measure insulation resistance >100MΩ after recovery to demonstrate reliability in tropical climates.
6. Mechanical Flexural Strength Testā
- Perform three-point bending at 150°C with 0.5% strain (IPC-6012). Validate zero microcracks via cross-section analysis to ensure structural robustness.
7. Interlayer Bond Strength Measurementā
- Conduct 90° peel tests before/after thermal aging (IPC-TM-650 2.4.8). Maintain >1.2kgf/cm adhesion strength for power module applications.
8. High Current Loading Verificationā
- Subject boards to 100A DC load at 110°C ambient for 24 hours (IEC 60146). Monitor thermal rise <40°C above ambient with infrared thermography.
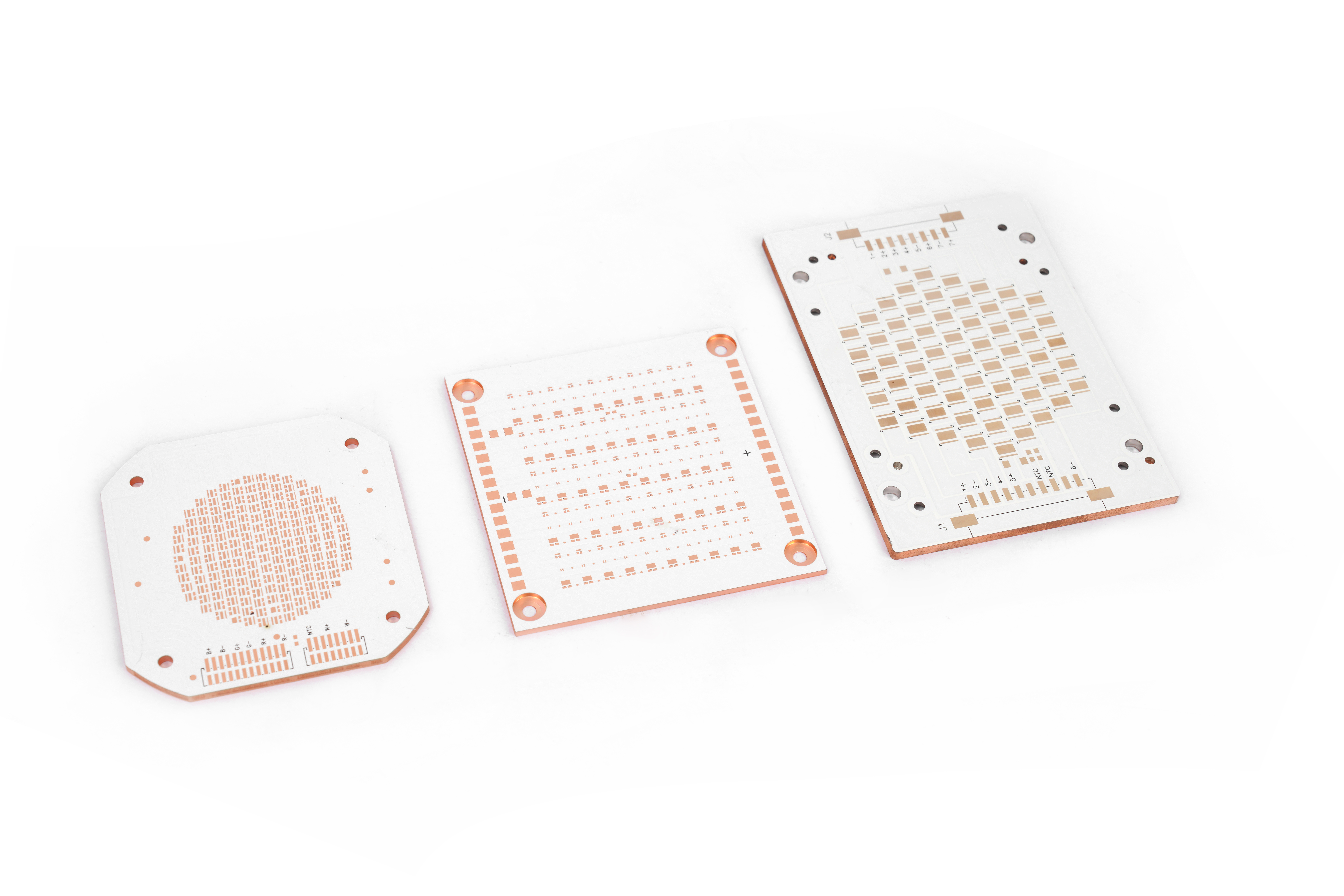
Why Choose Best Technology as Copper PCB Plate Manufacturer?
- Free DFM (Design for Manufacturability) Analysis: Optimizes PCB layouts to reduce material waste, lower production costs, and avoid late-stage design revisions.
- Thermal Simulation & Optimization: Custom heat dissipation solutions proven to reduce hotspot temperatures by 25-40°C
- 24-Hour Rapid Prototyping Delivery: Accelerates product development cycles, enabling faster time-to-market and competitive edge in high-demand industries.
- Stringent Quality Control with 100% Inspection: Eliminates hidden defects, reduces rework costs, and ensures reliability in high-current/thermal applications.
- Transparent Pricing with No Hidden Fees: Predictable budgeting and cost savings through upfront pricing models tailored to thick copper PCB specifications.
- Certified Compliance (ISO 9001, UL, RoHS): Mitigates regulatory risks and ensures products meet global standards for safety and environmental compliance.
- One-Stop Solution from Design to Delivery: Streamlines project management by consolidating prototyping, fabrication, and assembly together.
Welcome to contact us if you have any inquiry for copper PCB board: sales@bestpcbs.com. Looking hearing from you soon!