In our last blog, we introduced the definition and basic of copper core PCB. But copper core PCB isn’t the only one metal core PCB, aluminum PCB provides good heat dissipation as well. So, when working with metal core boards, many engineers and buyers are unsure whether to choose an aluminum PCB or a copper core PCB. Some believe copper is always better, while others go with aluminum for lower cost. Today, we will guide you how to choose them, then let’s start it!
Material Comparison: Copper vs Aluminum Core
Both copper and aluminum are used as the core material for thermal management in PCBs, but their physical and electrical properties differ significantly:
Property | Copper | Aluminum |
Thermal Conductivity | ~380–400 W/m·K | ~200–230 W/m·K |
Electrical Conductivity | ~58 MS/m | ~35 MS/m |
Density | 8.96 g/cm³ | 2.70 g/cm³ |
Strength | Higher rigidity | More flexible |
Cost | 1.5x to 3x higher | Lower |
Copper provides superior conductivity and better rigidity but comes at a much higher cost and weight. Aluminum is lighter, easier to machine, and cost-effective for mid-range applications.
Thermal Management: Which One Handles Heat Better?
When heat dissipation is your top priority, copper clearly wins. Its high thermal conductivity allows heat to spread faster and more evenly, which is critical in high-power applications like:
- LED floodlights and stadium lighting
- Automotive headlights
- Power converters and inverters
- Laser driver modules
Case example: A customer replaced an aluminum PCB with a copper base for a 100W LED driver. The operating temperature dropped by 15°C, drastically improving product lifespan.
However, in low-to-mid power systems—like ceiling lights, LED bulbs, or camera light rings—aluminum is typically sufficient. Using copper in these cases is often unnecessary and drives up costs without clear benefits.
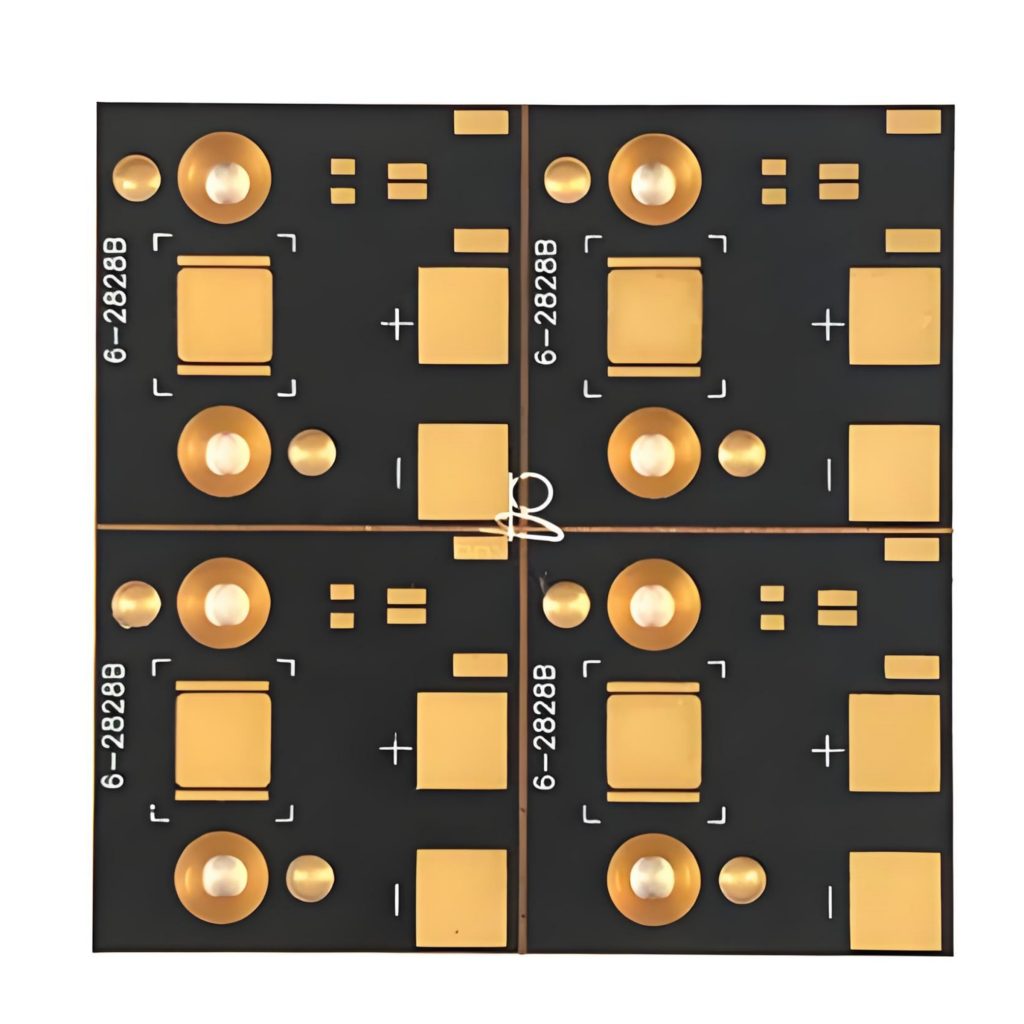
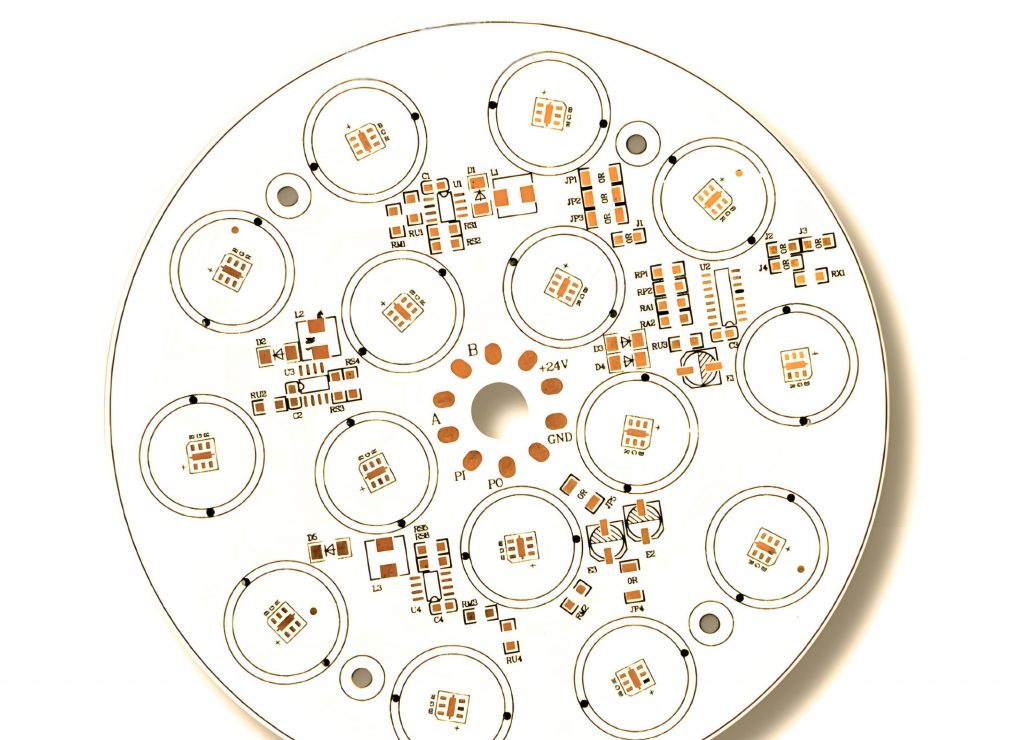
Mechanical Strength and Weight: What Does Your Design Need?
Copper core PCBs are heavier and more rigid, which makes them better for industrial applications exposed to vibration or extreme temperature cycles.
But in products where weight matters—like drones or wearable devices—aluminum PCBs are the smarter option. They are easier to machine, route, and assemble. They also cost less in terms of tooling and manufacturing time.
Choose copper core PCBs if you need:
- High mechanical stability
- Vibration resistance
- Long-term thermal durability
Choose aluminum PCBs if your product needs:
- Lightweight design
- Cost control
- Simpler routing and drilling
Cost Consideration: Is Copper Always Worth It?
Let’s be honest: copper core PCBs can cost up to 3x more than aluminum PCBs. So you should ask yourself—is the higher thermal performance really necessary for your design?
Aluminum PCBs are the better choice when:
- Your application doesn’t exceed 80W–100W
- Weight and cost are design priorities
- You’re in mass production and need price stability
Copper core PCBs are justified when:
- Your system needs to handle heavy heat loads
- High current density is involved
- Long-term reliability matters more than price
Many of our customers reduce total project cost by switching to aluminum PCBs without sacrificing performance—once we review their thermal simulation data.
Where to Use Each PCB Type?
Here’s a quick-reference table to match your application with the recommended base material:
Application | Recommended Base | Reason |
High-power LED floodlights | Copper | Heat and current requirements are high |
Automotive lighting systems | Copper or thick aluminum | Performance and safety critical |
Indoor LED lighting | Aluminum | Lower heat, cost-sensitive |
Power modules & inverters | Copper | High voltage and thermal stress |
Camera flash or ring light | Aluminum | Lightweight and cost-friendly |
Medical power supply | Copper | Stability and safety required |
LED floodlights (150W+) | Copper Core PCB | Handles heat better |
LED bulbs & home lighting | Aluminum PCB | Affordable and thermally sufficient |
EV chargers & power modules | Copper Core PCB | High reliability under load |
Camera flashes & portable lights | Aluminum PCB | Lightweight and budget-friendly |
Medical devices (power control) | Copper Core PCB | Precise, stable performance |
Consumer electronics | Aluminum PCB | Cost-efficient for large volumes |
Use this guide to avoid over-engineering or under-specifying your metal core PCB.
5 Key Points Before You Choose
Still not sure which base material fits your needs? Walk through this five-step checklist:
1. Power Level: How much current and heat does your circuit handle?
2. Installation Environment: Is weight a constraint? Will it face vibration?
3. Target Cost: Are you selling a premium or mass-market product?
4. Design Complexity: Do you need tight tolerances or complex routing?
5. Volume & Lead Time: Can your supplier meet deadlines for the material?
If you answered “high” for performance on most points, copper is likely the way to go. If not, aluminum is your best cost-performance choice. By the way, if you’re unsure after answering these, consult with your PCB manufacturer. At Best Technology, we provide application-based advice to help you choose between aluminum PCBs and copper core PCBs—without overspending.
Why Choose Best Technology for Your Metal Core PCB?
Whether you need aluminum base PCBs for standard lighting or copper base PCBs for high-power industrial applications, Best Technology has you covered:
- Mature production lines for both copper and aluminum base PCBs
- One-on-one design support, thermal simulation, and DFM reviews
- Full in-house capabilities: thick copper etching, CNC routing, V-cutting
- Fast sample turnaround and stable mass production support
- Strict quality control and traceability through MES system
- Expert engineering team for application-specific advice
Reach out to Best Technology—we’ll help you analyze your application, recommend the ideal PCB solution, and even support custom development if needed.
FAQs
Q1: Can I use aluminum base PCBs for high-power applications?
Only for moderate heat loads. For >100W power systems, copper is strongly recommended.
Q2: What is the thinnest aluminum or copper base you can provide?
We can produce down to 0.8mm base thickness for both, depending on the structure.
Q3: Do you offer hybrid metal core PCBs?
Yes, we can integrate aluminum and FR4 or support copper-ceramic hybrid designs.
Q4: How long is the lead time for copper vs aluminum base?
Aluminum PCBs: 5–7 working days; Copper PCBs: 7–12 days depending on complexity.
Q5: Can I get thermal simulation before placing an order?
Absolutely! We offer pre-production thermal analysis and structural design assistance.
Q6: Are copper core PCBs compatible with standard SMT processes?
Yes, they are. We offer full SMT assembly services for both aluminum and copper base boards.
Q7: How do I know which type is best for my application?
Send us your design or specs, and we’ll recommend the most cost-effective and reliable option.
Conclusion
Choosing between a copper core PCB and an aluminum PCB isn’t about choosing the better material. It’s about selecting what’s right for your application. Copper is powerful but expensive; aluminum is flexible and affordable.
When designed and selected correctly, aluminum PCBs can outperform expectations, and copper core PCBs can save your system from thermal failure. Match the material to your environment, budget, and performance goals—and you’ll never go wrong. In our next blog, we will share how to select the thickness of copper. If you are interested in it, collect us and keep reading.
Tags: copper base pcb, copper core pcb