Foldable PCB technology has changed how engineers design compact and flexible electronics. From smartphones that fold in half to medical devices that wrap around the body, a foldable PCB board helps make these designs possible. Unlike traditional rigid boards, these PCBs bend or twist without breaking. They save space, reduce weight, and often need fewer connectors.
In this blog, weâll explore different types of foldable PCBs, their pros and cons, where they’re used, and why certain typesâlike bendable aluminumâcost more. Weâll also share the key design tips and how to find a reliable foldable PCB manufacturer for your next project.
What is a Foldable PCB?
A foldable PCB is a printed circuit board designed to bend, flex, or fold without damaging the electrical pathways. These PCBs are made using flexible materials like polyimide or specially treated FR4. They are often thin, light, and durable, which makes them useful in tight or moving spaces.
Unlike rigid boards, foldable PCBs can take on 3D shapes. They can be used in hinges, curves, or tight enclosures where a regular FR4 PCB wonât fit. These designs cut down on cables and connectors, making the device smaller, lighter, and more reliable.
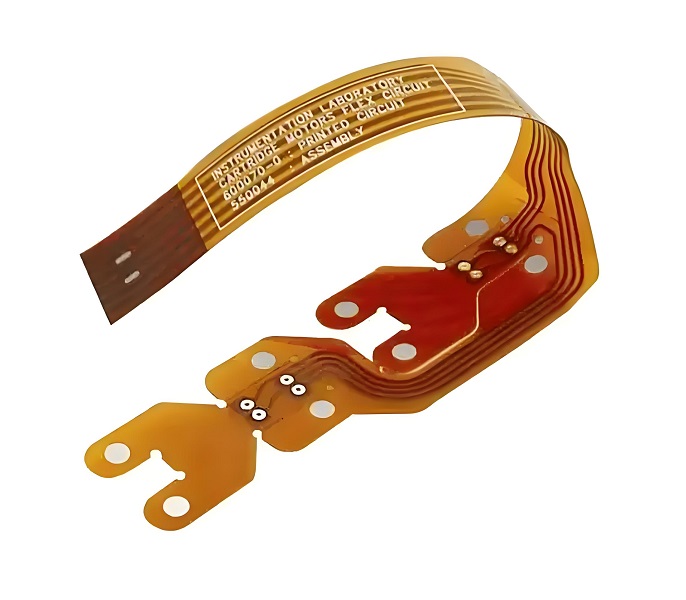
Foldable PCB Types
Foldable PCBs come in several forms. Each has its own strength and is used in different applications.
- Flexible Circuits
This is the most common flexible circuits, called FPC as well. These use a thin polyimide film instead of standard fiberglass. They can bend freely in any direction and are ideal for cameras, printers, wearables, and foldable phones. Theyâre often single-sided but can be multilayered.

- Rigid-Flex PCBs
A rigid-flex PCB combines the best of both worldsârigid sections for stable component mounting and flexible areas to allow folding. These are popular in complex devices like military gear, satellites, and high-end medical tools.
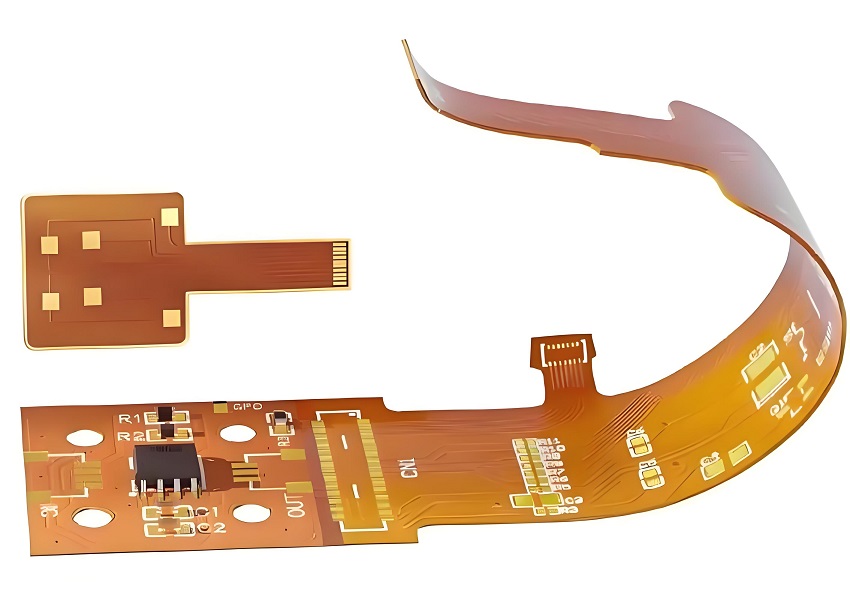
- Semi-Flexible PCBs
Semi-flexible PCB uses a flexible version of standard FR4. Itâs bendable only once or twice during installation. Itâs cheaper than flex PCBs but more limited. Youâll find these in LED modules or automotive electronics where minor bending is needed.
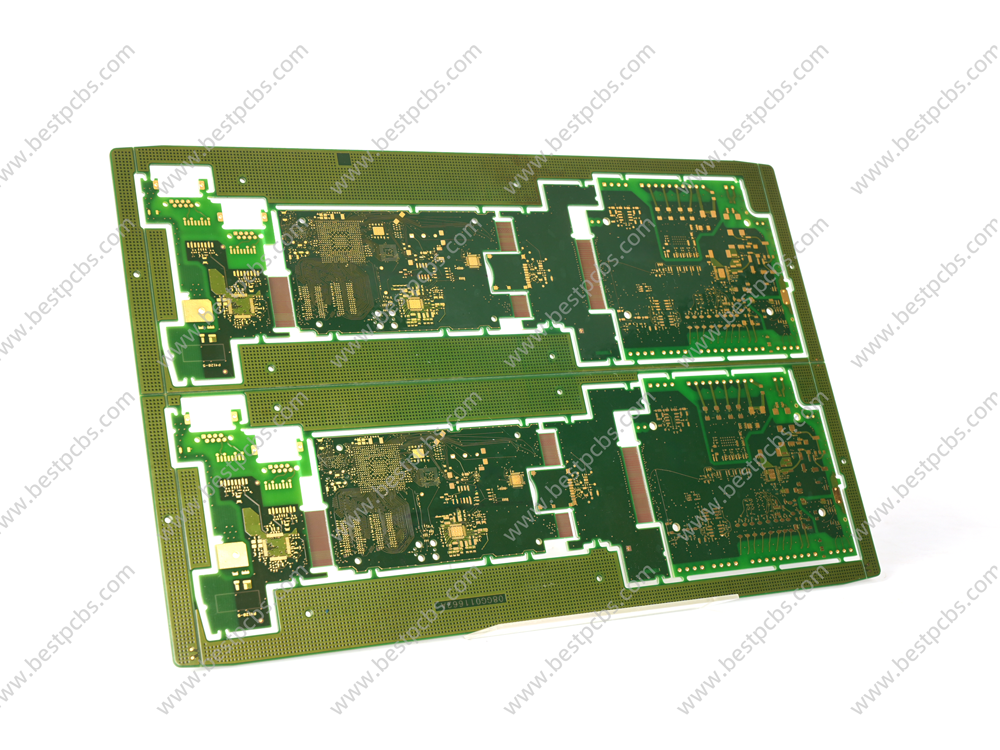
- Bendable Aluminum PCBs
Bendable aluminum boards use aluminum cores with bendable material series. They are mostly used in LED strips, vehicle lighting, or static fold setups. While they arenât as flexible as polyimide boards, they handle heat well and provide strong mechanical support.
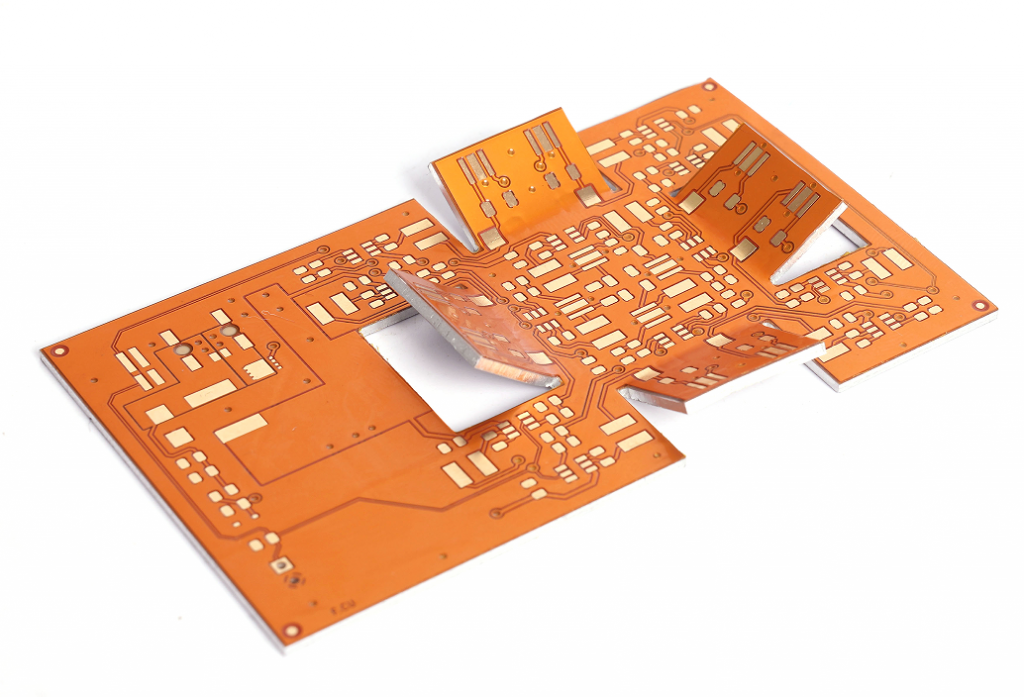
Advantages of Foldable PCBs
- Saves space: They fit in tight spots and allow for creative layouts.
- Reduces weight: Ideal for portable or wearable devices.
- Fewer connectors: Fewer mechanical connections mean fewer failure points.
- Shock resistance: Flex PCBs can absorb vibrations better than rigid ones.
- Better reliability: Strong signal paths without added cables.
Disadvantages of Foldable PCBs
- Higher cost: Especially true for rigid-flex or aluminum options.
- Complex design: Requires careful layout and material selection.
- Bending fatigue: Repeated flexing can wear out traces over time.
- Limited layer options: Fewer layers compared to rigid boards.
Foldable PCB Applications
Foldable PCB boards are now used across many industries thanks to their size and flexibility. Common applications include:
- Smartphones and tablets: Especially foldable or flip models.
- Wearable devices: Smartwatches, health bands, or fitness trackers.
- Medical devices: Flexible sensors, hearing aids, or body patches.
- LED lighting systems: Flexible LED strips, curved lighting, or signage.
- Automotive interiors: For dashboards, control panels, and ambient lighting.
- Consumer electronics: Cameras, game controllers, or fold-out gadgets.
- Aerospace and military: Lightweight systems that must handle vibration.
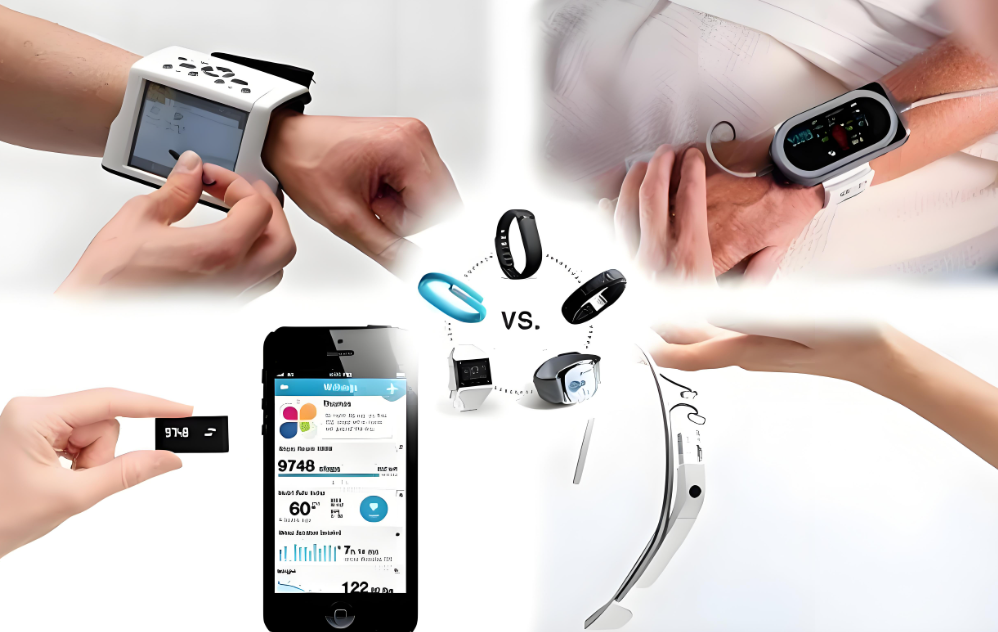
Why Bendable Aluminum PCB Costs More Than Flexible Circuits?
You might notice that bendable aluminum PCBs often cost more than regular flexible circuits. Hereâs why:
- Material cost: Aluminum cores and dielectric layers used in bendable boards are more expensive than polyimide film used in flex PCBs.
- Thermal performance: These boards are built for high-heat environments, so they require special treatment and thermal interface materials.
- Machining difficulty: Bending metal without damaging the circuit paths takes precision and specialized tools.
- Lower yield rate: These boards are harder to process in large volumes, especially when custom bending angles are needed.
So while bendable aluminum PCBs offer great heat management and durability, their manufacturing process drives up the cost compared to standard flexible circuits.
Design Considerations of Foldable PCB Board
When designing a foldable PCB, there are several rules to follow:
- Bend radius: Always keep the bend radius at least 6 to 10 times the board thickness to avoid cracks or delamination.
- Trace layout: Avoid sharp corners or 90-degree bends in traces, especially in flexible sections. Use curved paths for less stress.
- Stress relief: Add slots or wider copper pads in flex areas to reduce strain.
- Material selection: Choose polyimide for high flex use or semi-flex FR4 for limited bends. For heat-heavy setups, use bendable aluminum.
- Stack-up planning: Place sensitive components away from fold zones. Keep fewer layers in the flex area to maintain reliability.
- Bending direction: Plan the layout to avoid stress on solder joints or component leads when the board is bent.
Designing for foldability takes extra care, but it pays off in product performance and durability.
Where to Find a Foldable PCB Manufacturer?
If youâre building devices with foldable designs, itâs important to work with a manufacturer that understands the details. Hereâs what to look for:
- Specialized experience: Choose a factory with proven capability in flex, rigid-flex, and semi-flex designs.
- Engineering support: Youâll need layout reviews, DFM checks, and prototyping advice.
- Clean production: Flex and bendable PCBs need precise etching and lamination in controlled environments.
Best Technology is one of the leading manufacturers offering complete support for foldable PCB boards. At Best Technology, âTotal Customer Satisfactionâ is our goal, and it is the core of Best Technologyâs operation as a PCB manufacturer. Procurement, sales, engineering, manufacturing, inventory, and quality have the same common goal of ensuring directly or indirectly âTotal Customer Satisfactionâ. We provide flexible circuit production, rigid-flex builds, and even custom aluminum-based PCBs for thermal control. With our ERP traceability system and professional engineering team, we help clients go from prototype to mass production with speed and reliability.
FAQs
Q1: Can foldable PCBs be reused after bending?
Some types, like polyimide flex circuits, can bend thousands of times. Others, like semi-flex or bendable aluminum PCBs, are designed for limited bending during assembly.
Q2: Whatâs the lifespan of a flexible PCB?
With proper design, a flex circuit can last over a million bending cycles. It depends on material, bend radius, and stress exposure.
Q3: Are foldable PCBs safe for high-current applications?
Yes, with the right trace width and copper thickness. However, heat management and durability must be carefully planned.
Q4: Can I mount heavy components on the flexible part?
No. Heavy or rigid components should be placed on the rigid or reinforced sections to avoid stress damage.
Q5: How fast can I get a foldable PCB prototype?
At Best Technology, we offer fast-turn prototyping in as little as 5â7 working days, depending on design complexity.
When you’re ready to build a reliable and high-performance foldable circuit, Best Technology is here to help. Our expert team, quality certifications, and full-service support make us the go-to foldable PCB manufacturer in China.