Want to master LED PCB footprint design? Explore this guide covering LED PCB footprint’s functions, polarity ID, thermal management, design steps, manufacturer selection, quality checks, and 3mm vs. 5mm differences.
Best Technology excels in delivering high quality PCB footprint RGB LED boards with unmatched speed and precision. Our ‌24 hours rapid prototyping service‌ ensures quick turnaround for design validation, supported by streamlined workflows and advanced machinery like laser direct imaging (LDI) and automated optical inspection (AOI). We specialize in ‌custom RGB LED footprints‌, optimizing pad geometries, thermal vias, and solder mask alignment to meet multi-channel color mixing and heat dissipation requirements. Rigorous adherence to ‌IPC-7351 standards‌ guarantees pad spacing accuracy and solder joint reliability. Leveraging in-house production capabilities and a vertically integrated supply chain, we minimize lead times for bulk orders without compromising quality. Our team provides ‌real-time 24 hours technical support‌ to address footprint design challenges, ensuring compatibility with automated assembly processes. Combined with competitive pricing and strict confidentiality protocols, Best Technology stands as a trusted partner for high-performance RGB LED PCB solutions. Welcome to contact us if you have any request for RGB LED PCB solutions: sales@bestpcbs.com.
What Is LED PCB Footprint?
A LED PCB footprint refers to the precise layout pattern on a printed circuit board specifically designed to accommodate light-emitting diodes (LEDs). It defines the physical and electrical interface between the LED component and the PCB, including pad dimensions, spacing, solder mask openings, and polarity markings. The footprint ensures compatibility with the LED’s package size, such as 3mm or 5mm variants, while accounting for soldering requirements, thermal dissipation paths, and mechanical stability. Proper LED PCB footprint design incorporates features like anode/cathode indicators to prevent reverse mounting, thermal relief patterns for heat management, and alignment guides for automated assembly. This layout directly impacts solder joint reliability, light output consistency, and long-term performance in applications ranging from indicator lights to high-power illumination systems.
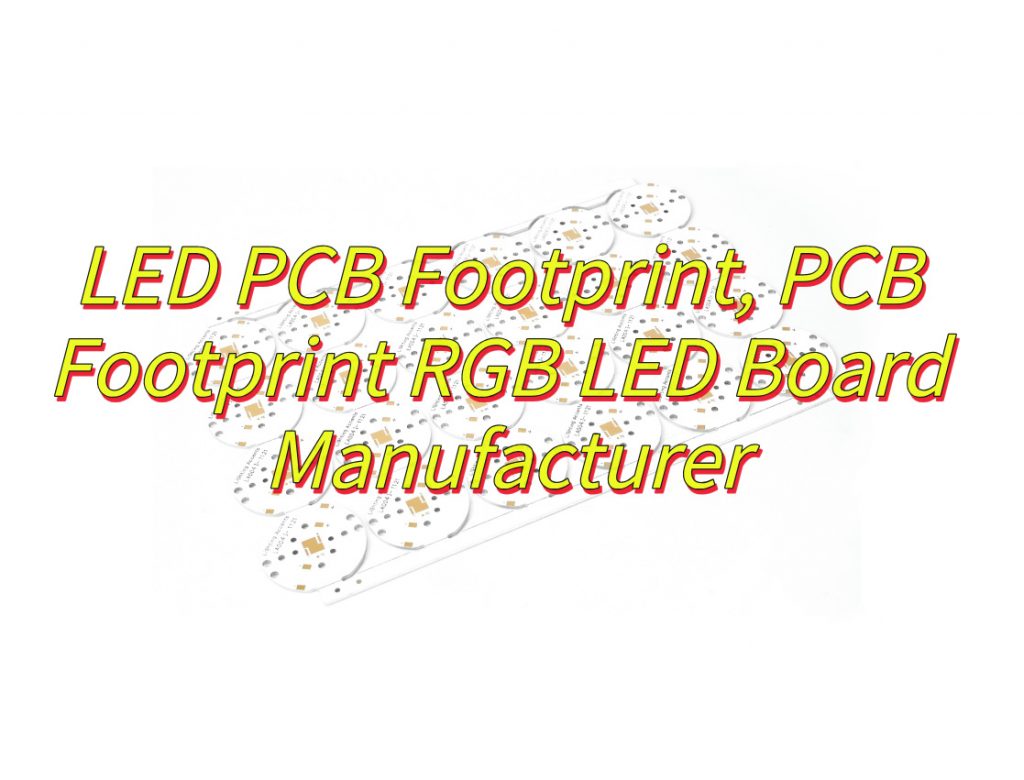
What Are Function of LED PCB Footprint?
Here are function of LED PCB footprint:
Mechanical Anchoring and Alignment
- The footprint defines the exact position and orientation of LEDs on the PCB, ensuring precise alignment with optical components (e.g., lenses, reflectors). For 5MM LED Strip Black PCB designs, this prevents misalignment that could cause uneven lighting or aesthetic inconsistencies.
Electrical Connection Interface
- Solder pads within the footprint establish secure electrical contacts between LED leads and PCB traces. Proper pad dimensions (e.g., 2.0mm spacing for 5mm LEDs) prevent solder bridges and ensure reliable current flow.
Thermal Dissipation Pathway
- Thermal pads or copper pours in the footprint conduct heat away from LEDs to the PCB’s ground plane. This function is critical for 5MM LED Strip Black PCB in high-power applications (e.g., automotive lighting) to prevent premature LED failure.
Polarity and Identification Markers
- Footprints include silkscreen labels or asymmetric pad shapes to indicate LED polarity, reducing assembly errors. For RGB LEDs, this ensures correct color channel alignment during soldering.
Signal Integrity Management
- Controlled impedance traces routed from the footprint minimize electromagnetic interference (EMI) and voltage drop. Essential for 5MM LED Strip Black PCB in data-driven applications (e.g., addressable LED strips).
Space Optimization for Dense Layouts
- Compact footprint designs (e.g., staggered pad arrays) allow higher LED densities on the PCB. This maximizes light output per unit area in applications like 5MM LED Strip Black PCB for architectural lighting.
Manufacturability and Assembly Efficiency
- Standardized footprints enable automated pick-and-place assembly, reducing labor costs. Features like fiducial markers in the footprint simplify machine vision alignment during production.
Compliance with Safety and Regulatory Standards
- Footprints adhere to IPC-2221 or UL standards for creepage/clearance distances, ensuring electrical safety. Critical for 5MM LED Strip Black PCB in consumer electronics or automotive certifications.
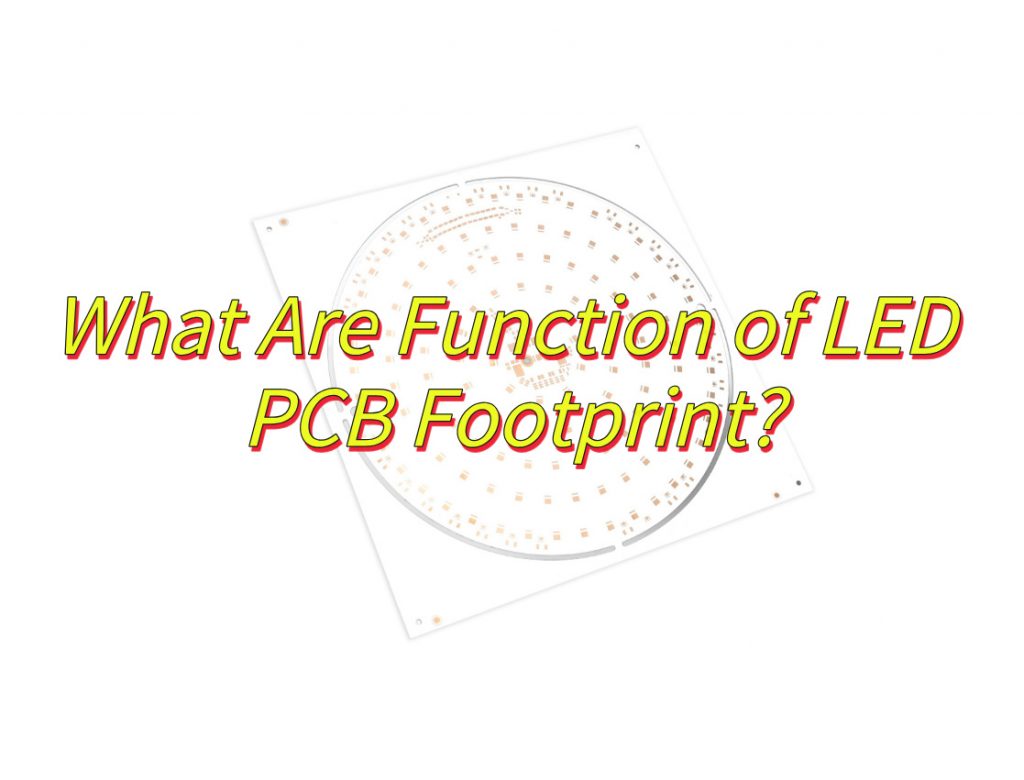
How to Identify LED PCB Footprint Symbol Polarity?
This is how to identify LED PCB footprint symbol polarity:
Check the PCB Silkscreen Layer
- Look for polarity markers (e.g., “+” signs, cathode bars, or diode symbols) printed on the PCB surface. For 5MM LED Strip Black PCB, these marks may appear as white silkscreen on dark backgrounds.
Examine the Copper Pad Shape
- The cathode pad (negative terminal) often features a square or notched corner, while the anode pad (positive) remains circular. This distinction is critical for 3mm/5mm LEDs in dense footprints.
Review Component Datasheets
- LED manufacturers specify footprint dimensions and polarity in datasheets. Cross-reference pad spacing (e.g., 2.54mm for 5mm LEDs) with PCB layouts to confirm alignment.
Use a Multimeter in Diode Mode
- Place the multimeter probes across the LED pads (red to anode, black to cathode). A forward-biased reading confirms polarity. Repeat for all LEDs on 5MM LED Strip Black PCB to ensure consistency.
Inspect the LED Package Markings
- Physical LEDs may have polarity indicators (e.g., a flat edge on the cathode). Align these with PCB symbols during soldering to prevent reverse mounting.
Leverage Design Software Tools
- In EDA tools (e.g., KiCad, Altium), enable “show polarity” layers to visualize anode/cathode pads. For 5MM LED Strip Black PCB projects, adjust contrast settings to improve visibility.
Verify Assembly Drawings
- Consult mechanical drawings or 3D models for polarity annotations. For 5MM LED Strip Black PCB, ensure black solder mask does not obscure critical symbols.
Test with a Low-Voltage Power Supply
- Apply 2–3V to the footprint pads. A glowing LED confirms correct polarity; reverse connections may damage the LED or PCB traces.
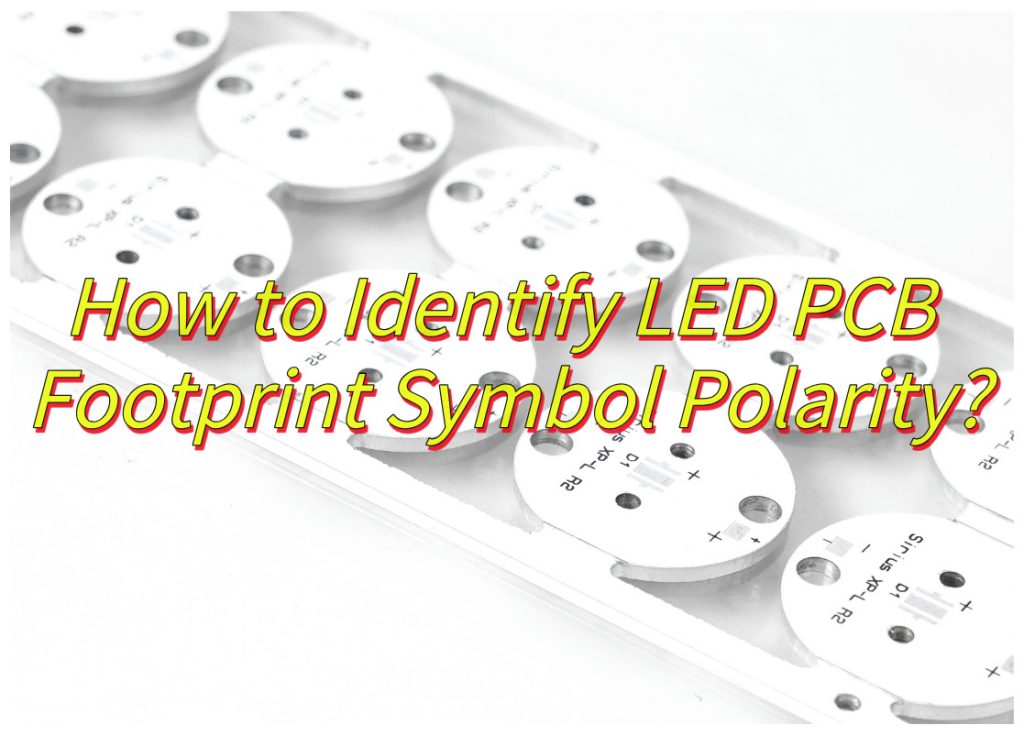
How to Optimize Thermal Management Design of LED Footprint PCB?
This is how to optimize thermal management design of LED footprint PCB:
Use Thermally Conductive PCB Materials
- Select substrates with high thermal conductivity (e.g., aluminum-backed PCBs or ceramic cores) to accelerate heat dissipation from LEDs. For 5MM LED Strip Black PCB, aluminum boards reduce junction temperatures by 30–50% compared to FR-4.
Maximize Copper Pour Area
- Design footprints with generous copper pours connected to the cathode pad. A 2–3mm copper layer beneath 5mm LEDs improves heat spreading to adjacent planes.
Incorporate Thermal Vias
- Place staggered vias (0.3–0.5mm diameter) around the LED footprint to channel heat to inner layers or ground planes. For 5MM LED Strip Black PCB, use 8–12 vias per LED for optimal thermal performance.
Optimize Pad and Trace Dimensions
- Widen traces (0.5–1.0mm) near LED pads to reduce resistance and heat buildup. For 3mm LEDs, maintain a 1.5mm trace gap; for 5mm LEDs, use 2.0mm spacing to prevent thermal runaway.
Add Heat Sinks or Stiffeners
- Attach low-profile heat sinks (e.g., 5x5mm aluminum extrusions) to the PCB surface. For 5MM LED Strip Black PCB, use thermal adhesive tape to bond sinks without obstructing light emission.
Implement Airflow Channels
- Design footprints with spacing between LEDs to allow convection cooling. For dense 5MM LED Strip Black PCB layouts, include 1–2mm gaps between adjacent LEDs to prevent heat pooling.
Use Solder Mask Dams Strategically
- Limit solder mask coverage near LED pads to 0.1–0.2mm, exposing bare copper for better heat transfer. Avoid full solder mask over LED bodies in 5MM LED Strip Black PCB designs.
Validate with Thermal Simulation
- Run transient thermal analyses to predict junction temperatures under worst-case loads. For 5MM LED Strip Black PCB, simulate 85°C ambient conditions to ensure compliance with automotive standards.
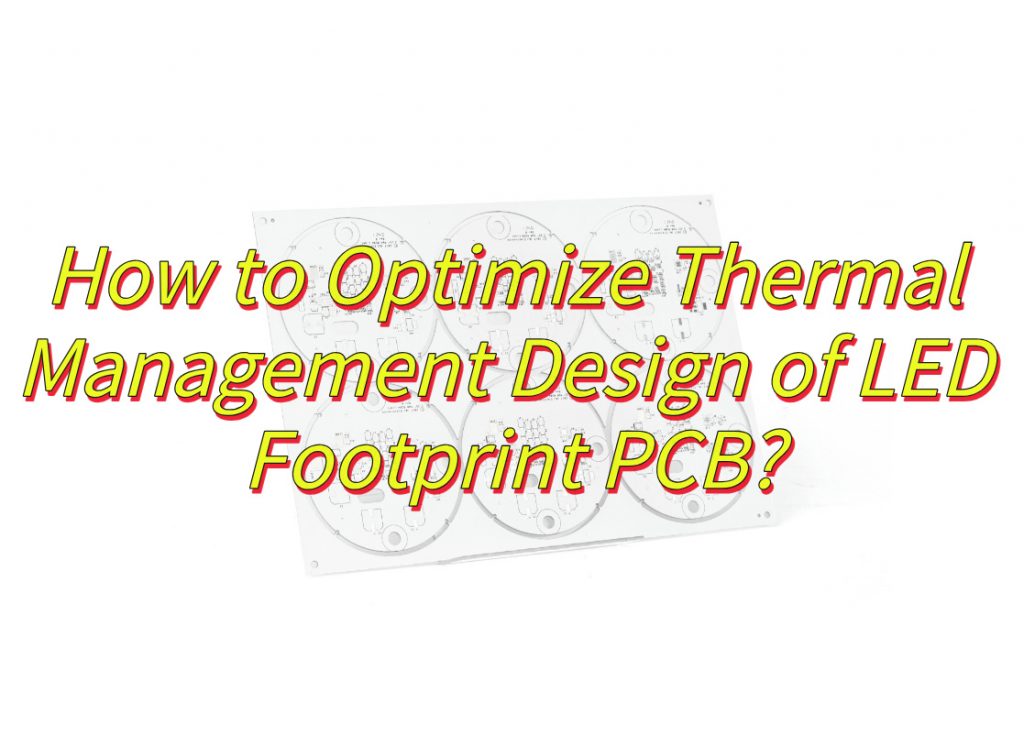
What Are the Procedures for Designing a LED PCB Footprint?
Here are the procedures for designing a LED PCB footprint:
1. Define Application Requirements
- Determine LED type (e.g., 3mm/5mm, SMD, high-power), operating voltage, and thermal constraints. For 5MM LED Strip Black PCB, specify strip length, LED density, and environmental conditions (e.g., indoor/outdoor).
2. Consult LED Datasheets
- Extract critical dimensions: body size, lead spacing, and recommended pad layout. For 5mm LEDs, pads typically measure 1.5–2.0mm diameter with 2.54mm pitch.
3. Create a Schematic Symbol
- Design an electrical symbol in EDA software (e.g., KiCad, Eagle) with correct pin assignments (anode/cathode). Include polarity markers to avoid assembly errors.
4. Design the PCB Footprint
- Draw solder pads matching LED lead dimensions. Use rectangular pads for through-hole LEDs or oval pads for SMD variants. For 5MM LED Strip Black PCB, ensure 0.1–0.2mm solder mask clearance around pads.
5. Add Thermal Management Features
- Incorporate thermal relief pads (e.g., spokes connecting to copper pours) for high-power LEDs. For 5MM LED Strip Black PCB, place vias near pads to dissipate heat to inner layers.
6. Include Assembly Aids
- Add silkscreen labels (e.g., “+”, diode symbol) and fiducial markers for pick-and-place machines. For dense 5MM LED Strip Black PCB layouts, use contrasting silkscreen colors for visibility.
7. Run Design Rule Checks (DRC)
- Verify pad-to-pad spacing (≥0.2mm for 5mm LEDs), trace widths, and hole sizes comply with PCB manufacturer capabilities.
8. Generate Gerber Files
- Export layers (copper, solder mask, silkscreen) in industry-standard formats. For 5MM LED Strip Black PCB, confirm black solder mask aligns with pad openings.
9. Prototype and Test
- Fabricate a PCB sample and solder LEDs manually. Use a thermal camera to check for hotspots and adjust copper pours if needed.
10. Document and Standardize
- Save the footprint in a component library for reuse. For 5MM LED Strip Black PCB projects, note material stack-ups and thermal via patterns for future designs.
How to Choose a PCB Footprint RGB LED Board Manufacturer?
Here are methods about how to choose a PCB footprint RGB LED board manufacturer:
Evaluate Technical Expertise
- Prioritize manufacturers with proven experience in RGB LED PCB design, including footprint optimization for 3mm/5mm LEDs. Request case studies or samples showcasing thermal via placement and copper pour strategies.
Verify Material Quality
- Confirm the use of high-Tg laminates (e.g., FR-4 TG 170) and immersion gold finishes for reliable solder joints. For 5MM LED Strip Black PCB, ensure the solder mask adheres to dark substrates without obscuring polarity markers.
Check Design for Manufacturing (DFM) Capabilities
- Select manufacturers offering free DFM checks to identify issues like pad-to-pad spacing violations (minimum 0.2mm for 5mm LEDs) or insufficient annular rings.
Assess Thermal Management Solutions
- Inquire about metal-core PCB (MCPCB) options or aluminum substrate integration for high-power RGB LEDs. Request thermal simulation data to validate junction temperature predictions.
Review Assembly Processes
- Ensure the manufacturer supports automated optical inspection (AOI) to detect polarity reversals or missing components. For 5MM LED Strip Black PCB, confirm compatibility with reflow ovens for lead-free soldering.
Compare Pricing and Lead Times
- Obtain quotes for prototype (5–10 boards) and production runs (100+ boards). Balance cost with value-added services like stencil provision or electrical testing.
Request Certifications and Compliance
- Verify ISO 9001:2015 certification and adherence to IPC-A-600 standards. For automotive or medical RGB LED projects, confirm UL or RoHS compliance.
Leverage Customer References
- Contact previous clients to assess reliability, communication, and problem-resolution efficiency. For 5MM LED Strip Black PCB projects, inquire about long-term color consistency and lumen maintenance.
What Quality Checks Ensure Reliable PCB Footprint RGB LEDs?
Visual Inspection of Footprint Alignment
- Verify LED pads align with silkscreen polarity markers and component outlines. For 5MM LED Strip Black PCB, use a microscope to check for solder mask intrusion on pad edges.
Electrical Continuity Testing
- Perform flying probe or bed-of-nails tests to confirm anode/cathode pads are isolated (≥10^6 ohms insulation resistance). For RGB LEDs, validate all three color channels (R, G, B) are electrically distinct.
Solder Paste Inspection (SPI)
- Check paste volume (±10% tolerance) and placement accuracy (±0.05mm) for 0402/0603-sized RGB LEDs. Poor solder deposition causes voids and thermal stress.
Automated Optical Inspection (AOI)
- Detect tombstoning, solder bridges, or missing components. For dense 5MM LED Strip Black PCB layouts, use multi-angle lighting to identify lifted pads under black solder mask.
X-Ray Inspection (AXI)
- Validate via fill quality and hidden solder joints in metal-core PCBs. Critical for RGB LEDs with thermal vias beneath pads.
Thermal Imaging
- Measure junction temperatures under maximum load (e.g., 100% duty cycle). For 5MM LED Strip Black PCB, ensure hotspots do not exceed 90°C to prevent color shift.
Cross-Section Analysis
- Micro-section PCB samples to verify copper thickness (≥1oz for high-current RGB LEDs) and via plating integrity (≥25μm).
Environmental Stress Testing
- Subject boards to 100 thermal cycles (-40°C to +125°C) and 24-hour damp heat exposure (85°C/85% RH). For 5MM LED Strip Black PCB, check for solder mask adhesion loss.
Color Consistency Verification
- Use a spectroradiometer to measure luminous flux and chromaticity coordinates. Bin LEDs within Δuv ≤0.005 for critical applications like display backlights.
Accelerated Life Testing
- Operate RGB LEDs at 120% rated current for 1,000 hours. Monitor lumen maintenance and spectral shifts (e.g., >90% lumen retention for premium products).
What Are Difference Between 3MM and 5MM LED PCB Footprint?
Here are the differences between 3mm and 5mm LED PCB footprint:
Physical Dimensions and Spacing
- 3MM LEDs have a smaller body diameter (3mm vs. 5mm), requiring tighter pad spacing (typically 2.54mm pitch). This suits compact designs like wearables or miniature indicators.
- 5MM LEDs need larger pads (e.g., 1.5–2.0mm diameter) and wider traces (≥0.5mm) to accommodate higher current loads, making them ideal for industrial lighting or dashboard backlights.
Thermal Management Requirements
- 3MM LEDs generate less heat, often needing only standard FR-4 substrates. Their footprints may omit thermal vias to save PCB real estate.
- 5MM LEDs require aluminum-backed PCBs or copper pours (≥2mm²) beneath pads to dissipate heat. Thermal vias (8–12 per LED) are critical to prevent junction temperatures from exceeding 85°C.
Optical Performance and Applications
- 3MM LEDs offer narrower viewing angles (≤60°), making them suitable for precision tasks like optical sensors or matrix displays.
- 5MM LEDs provide wider beam angles (120°+) and higher luminous flux, ideal for ambient lighting or status indicators requiring visibility from multiple angles.
Assembly and Soldering Considerations
- 3MM LEDs use smaller solder pads (0.8–1.2mm diameter), demanding precise pick-and-place accuracy (±0.05mm tolerance) to avoid tombstoning.
- 5MM LEDs require larger solder fillets for mechanical stability. Their footprints often include solder mask dams (0.1–0.2mm gaps) to prevent solder bridging.
Cost and Material Efficiency
- 3MM LEDs reduce material costs by 15–20% compared to 5MM variants due to smaller PCB areas and lower copper usage.
- 5MM LEDs justify higher costs through longer lifespans (≥50,000 hours) and better resistance to vibrations, critical for automotive or outdoor applications.
Design Flexibility for RGB Variants
- 3MM RGB LEDs use shared anode/cathode pads with 0.3mm spacing between color channels, limiting current handling (≤20mA per channel).
- 5MM RGB LEDs feature separate pads for each color (R, G, B) with 0.5mm spacing, enabling higher current drives (up to 30mA per channel) for vibrant color mixing.
Compliance with Industry Standards
- 3MM LEDs adhere to IPC-SM-782 guidelines for pad dimensions and silkscreen markings, ensuring compatibility with automated assembly lines.
- 5MM LEDs require stricter adherence to IPC-6012 Class 3 for thermal cycling resistance (-40°C to +125°C), critical for aerospace or military applications.
To sum up, for 5MM LED Strip Black PCB projects, prioritize footprints with staggered thermal vias and 0.5mm copper pours to balance thermal performance and cost. Validate designs using a 10-second solder iron test to simulate reflow oven conditions and ensure pad integrity.
Tags: LED PCB footprint, PCB Footprint RGB LED Board Manufacturer