What Is Sinkpad MCPCB?
SinkPAD MCPCB is a special kind of metal core printed circuit board designed for excellent heat dissipation. It’s different from regular MCPCBs because it removes one major barrier—the insulating dielectric layer under the LED.
In simple terms, it allows heat to flow directly from the LED chip to the metal base. That means less heat build-up, more efficiency, and longer lifespan for your components.
You’ll often find SinkPAD MCPCBs in high-power LED applications—like automotive lighting, industrial lamps, medical equipment, and even UV curing systems. These are places where heat control isn’t just helpful—it’s essential.
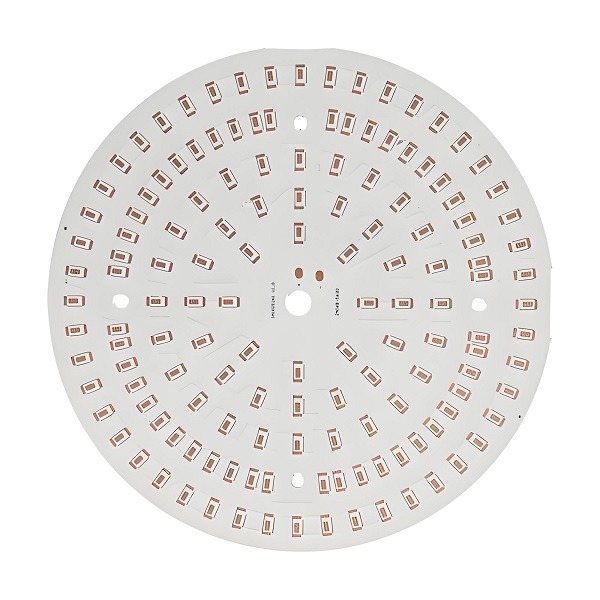
Advantages of Sinkpad MCPCB
1. Direct Heat Flow
With no dielectric between the LED and metal core, SinkPAD boards offer a direct thermal path, reducing resistance and increasing efficiency.
2. Lower Operating Temperatures
By improving heat transfer, components stay cooler. For LEDs, this means stable brightness and a longer working life.
3. Consistent Light Output
Temperature spikes can dim or discolor LEDs. SinkPAD keeps the junction temperature stable, maintaining consistent color and brightness.
4. Compact Design
Thanks to better heat handling, you can reduce or eliminate bulky heatsinks, helping make designs smaller and lighter.
5. Durability in Harsh Conditions
SinkPAD boards resist thermal cycling, shock, and vibration, making them perfect for tough environments like aerospace or outdoor lighting.
So if your design involves powerful LEDs or components that get hot fast, this type of board can be a game-changer.
Base Materials of Sinkpad MCPCB
SinkPAD boards come with different base metals. Each one has its own strengths depending on your project.
- Aluminum Core Sinkpad PCB
Aluminum is the more common choice. It’s lightweight, easy to work with, and keeps costs low. Its thermal conductivity is good—usually around 150-200 W/m·K. For applications where heat output isn’t extreme, aluminum SinkPAD PCBs are a great fit. You’ll find them in general LED lighting, backlit signs, and other consumer electronics.
They’re also a smart option if you’re trying to keep your SinkPAD MCPCB price in check. But actually, for consumer electronics, conventional metal core PCB can cover it.
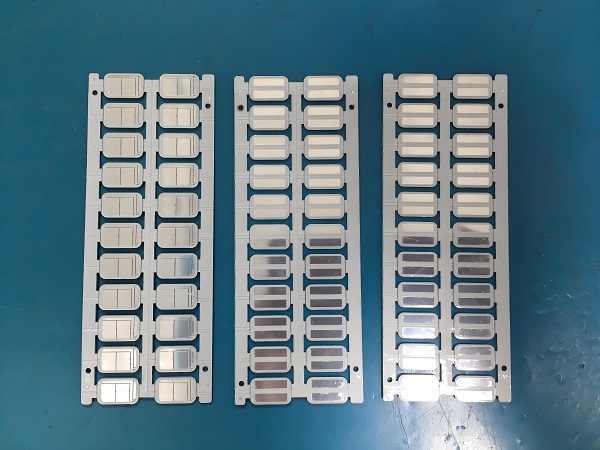
- Copper Core Sinkpad PCB
Copper is all about performance. It has much higher thermal conductivity—around 385-400 W/m·K—which means it can handle intense heat. If your LEDs are pushing a lot of power or operating in a hot environment, copper is the better option. Some industrial like UV lights, high-performance lasers, or automotive headlights that stay on for long hours.
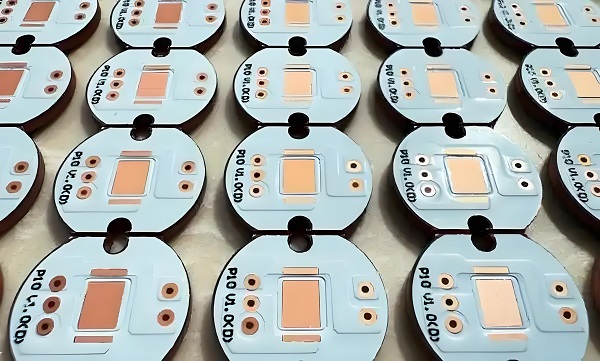
Copper boards are heavier and more expensive than aluminum ones, but they deliver top-tier thermal results.
How Does Sinkpad MCPCB Work?
In a standard MCPCB, the LED sits on a copper trace. Under that trace is a dielectric layer. Below that is the metal core, its structure just like below. Heat has to travel through all of this to get out. That creates resistance.
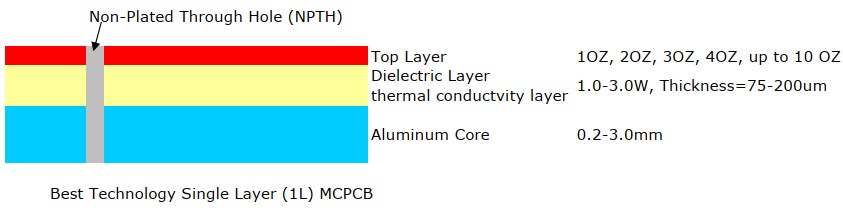
However, sinkPAD skips the dielectric layer—at least under the LED’s thermal pad. Instead, the heat flows straight from the LED’s thermal pad into a thermal cavity that connects directly to the base metal. This structure is often called a Direct Thermal Path (DTP).
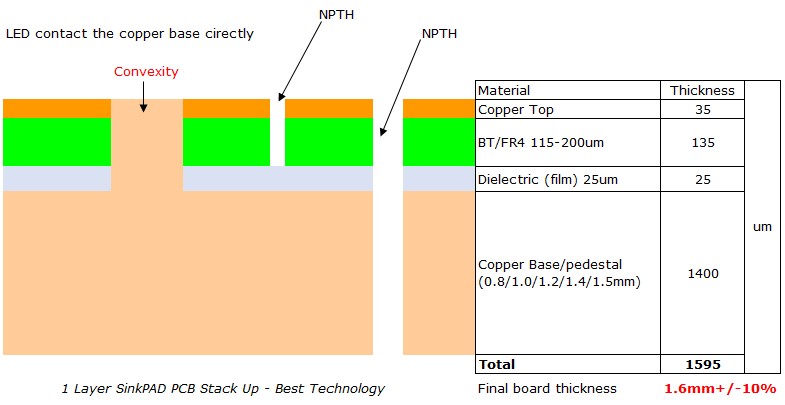
It’s like giving heat a shortcut out of the system. No extra layers. No slowdowns. Just fast, efficient cooling. This design improves overall thermal conductivity and gives you tighter control over junction temperatures.
Thermal Conductivity of Sinkpad MCPCB
Thermal conductivity is key when you’re dealing with LEDs and power electronics. The better the board can spread heat, the better your device performs.
With aluminum cores, you’ll typically see thermal conductivity in the 150–200 W/m·K range. That’s solid for most LED needs. With copper cores, you’ll reach up to 400 W/m·K, giving you elite heat handling.
Sinkpad MCPCB vs. Conventional MCPCB
So what are the differences between sinkpad metal core PCB and traditional metal core PCB? Here we made a comparison between them:
Property | SinkPAD MCPCB | Conventional MCPCB |
Heat Transfer | Direct path (through convexity pad) | Through dielectric |
Thermal conductivity | Up to 400W/m.k | Up to 8W/m.k |
Thermal Resistance | 0.4°C/W or lower | 1.0–2.0°C/W |
Light Stability | High (because most use copper) | Medium |
LED Lifespan | Extended | Shorter under heat |
Space Needed | No | Larger cooling required |
Cost | Slightly higher | Lower upfront |
SinkPAD boards give better performance and better results—especially when heat control is non-negotiable. They cost more, but what you get in return is worth it in critical applications.
Considerations When Using Sinkpad MCPCB
SinkPAD MCPCBs aren’t plug-and-play for every project. There are a few things you’ll want to keep in mind before designing with them.
1. Know Your Heat Load
If your LEDs don’t generate much heat, you might not need SinkPAD. But if your design involves high wattage, tight spaces, or long run times—then yes, it’s worth considering.
2. Choose the Right Core
Use aluminum if your budget is tight or if weight is a concern. Go with copper when you need every ounce of thermal performance you can get.
3. Plan for Heatsinks
Even though the board transfers heat well, it still needs a place to send that heat. Match your SinkPAD PCB with a proper heatsink or thermal interface.
4. Soldering Profiles
Because these boards transfer heat so quickly, your reflow or wave soldering profile might need to be adjusted. Too much heat too fast can be a problem.
5. Work With an Experienced Supplier
Not all board suppliers are familiar with SinkPAD technology. Make sure your manufacturer knows how to handle the convexity design and machining process correctly. If you are searching for a reliable sinkpad MCPCB manufacturer, do not miss out Best Technology. We have over 18 years experiences, and we have experienced engineers and operators to give you a high quality sinkpad copper core PCB.
How Does the Cost of Sinkpad MCPCB Compare to Conventional MCPCB?
So, how does the cost of sinkpad MCPCB compare to the conventional MCPCB? Actually, the price of sinkpad PCB is higher than that of a standard MCPCB. Because the process is more complex. There’s more precision involved in removing the dielectric under the LED. And if you’re using copper, that adds more to the cost.
Here’s what influences the price:
- Core material (aluminum vs. copper)
- Board size and thickness
- Layer count
- Volume of your order
- Custom thermal pad design
But here’s the real question: does it save you money in the long run? For many, the answer is yes. Here’s why:
- You don’t need oversized heatsinks
- Your LEDs last longer
- Fewer failures mean lower service costs
- Your product performs better, with fewer returns
When you weigh the total system cost—not just the board—the extra investment often pays off.
SinkPAD MCPCBs offer a smart solution for thermal challenges in LED and power electronics. They bring something special to the table—direct heat transfer from the source to the metal base.
If your design involves strong heat loads, tight spaces, or critical reliability, this is the kind of PCB that can make a difference. In our next blog, we will share the factors affect the cost of sinkpad PCB. If you want to know more about sinkpad PCB, you are welcome to contact us at any time.
FAQs
1. What makes Sinkpad MCPCB more effective than a standard MCPCB?
It creates a direct path from the LED to the metal core, removing the thermal barrier and increasing heat flow.
2. Can I use aluminum Sinkpad MCPCB for high-power LEDs?
Yes, if thermal output is moderate. For extreme power or heat, copper may perform better.
3. Does it support double-layer designs?
Sinkpad technology is usually single-sided due to its thermal cavity, but custom options are available.
4. Is the cost justified in consumer products?
In mid- to high-end products where longevity and brightness matter, yes. It reduces long-term failures and service needs.
5. How do I choose between aluminum and copper Sinkpad cores?
Look at the application. If weight and cost are more critical, aluminum works well. For demanding environments, copper is better.
Tags: sinkpad mcpcb, sinkpad mcpcb price