As we all know, it is very important to get a well-functional PCB from the PCB manufacturers. A well functional PCB means that the electricity testing has been performed well at the PCB manufacturer end. However, you may have found some PCB you purchased are with some electricity issues like short & open circuits, or some visual issues like solder pad missing., etc.
Do you know how this issue come while the PCB testing process?
According to the feedback come from the customers, here we summarized some improper ways during the PCB Electricity testing process which may lead to the PCB fail to the test.
Here are some major points for your reference:
- Incorrect direction when placing PCB board on testing worktop, the force on probes will cause indentation on boards.
- PCB manufacturers don’t regularly maintain their testing jig, causing some malfunctions on testing jig can’t be found in time. Take the counter for example, if we do not find the counter’s fixing screw loose in time, it will cause the counter to fail to read the caliper scale. Of course, it also could be the counter is dysfunctional sometimes.
- PCB manufacturers don’t regularly check/change the testing probes. Dirt on the testing probe cause testing results is inaccurate.
- PCB testing operator don’t distinguish functional board from NG board due to unclear placement area.
So, if the circuit boards testing work under above improper way, do you know what effects will be on your products?
Base on some lessons learned from our customers, you may get following influences caused by improper way of the PCB testing.
Increase your quality issues
The low testing accuracy will make the functional PCB mixing together with the defective PCB. If the PCB testing defects can’t be found in time before PCB assembly, defective products will flow into the market, which will seriously increase the quality risk hidden on the end products.
Delay your Progress
After defective PCBs are found, repairing will greatly delay the progress of the project.
Increase your overall cost
The defective PCB will cost many people and time to check and follow, this will directly to increase the overall cost of the projects.
We know deeply that poor testing will bring serious consequences for customers, so with more than 16 years experiences on Printed Circuits Board fabrication, Best Technology has rich experiences on PCB electric testing managements, and following are some of our management solutions to control our PCB testing process:
1. We execute strictly the pre-job training 3 months in advance for the testing operator, and all the testing will be operated by the professional and experienced testers.
2. Maintain or replace the test equipment every 3 months, and use a brush to clean the tester in a regular period or replace the pin cable head to make sure there is no contaminate at the test probe.
3. Add the extra tooling hole at rails for fix purpose to make sure the placement of PCB orientation is no mistake during testing process.
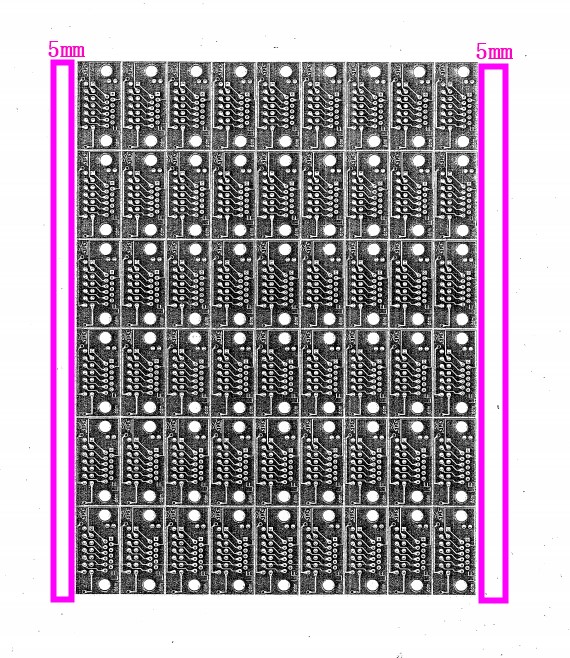
4. The testing workshop must be divided clearly for the qualified board and NG board, the location to keep NG board will be marked with red line.
5. The testing process must be strictly followed with our internal PCB testing standard operating procedure.
With the help from above management solutions for the PCB E-Testing during the PCB manufacturing process, the PCB we send to customers works very well, which also make sure their products can be assembled well and deliver well in the markets. For us, more and more kindly feedback regarding the functional feedback comes from our customers, here are some good feedback from customers for your reference.
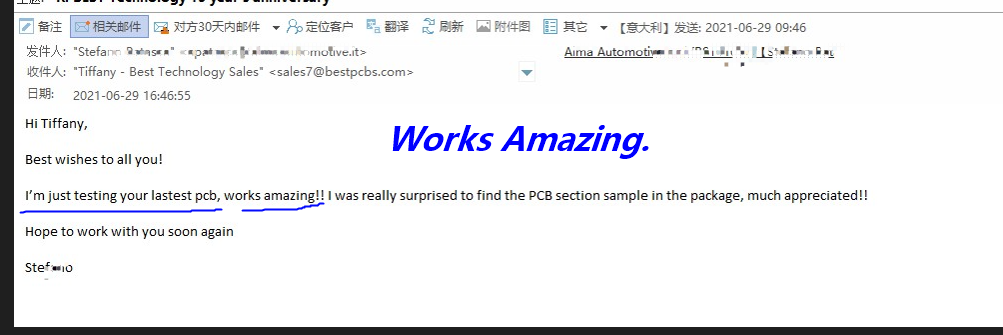
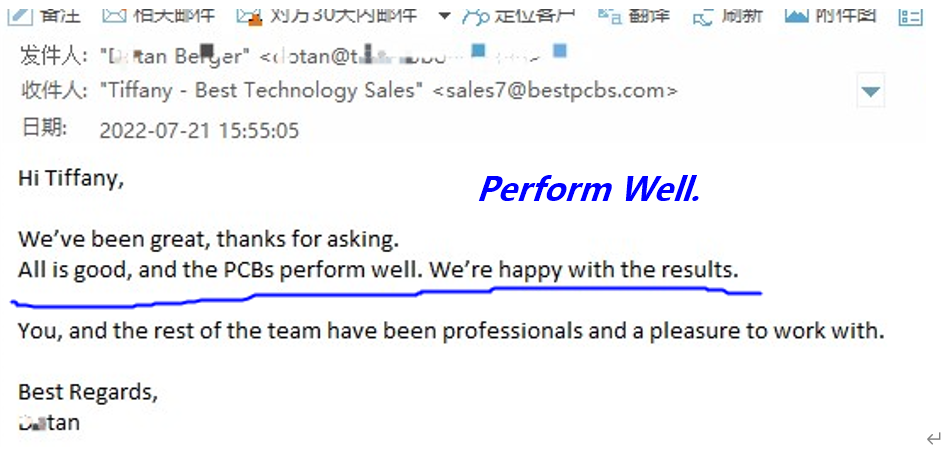
If you have any questions about PCB testing or PCB manufacturing, please feel your freely to leave your message or contact us. In our next update, we will share which test methods are used in the during the PCB Assembly.
Tags: PCB quality, PCB test