Are you worried about how to choose IMS PCB material for your project? Let’s explore its definition, properties, datasheet, types, IMS PCB material selection and design guidelines through this blog.
- Wrong choice of substrate material leads to too high thermal resistance?
- Is the dielectric layer easy to delaminate during multi-layer IMS design?
- Is the dielectric loss too large under high-frequency application?
Best Technology Can Provide:
- Provide 5 standardized thermal conductivity levels (1.5~8W/mK); Free sample matching tool, generate selection report in 30 minutes.
- Patented resin system, peel strength>1.8N/mm; Support 3-layer lamination process, provide design specification manual.
- Df value as low as 0.002 (@10GHz); Equipped with HFSS simulation model library, plug-and-play.
Welcome to contact us if you have any request for IMS PCB or MCPCB: sales@bestpcbs.com.
What Is IMS Material?
IMS material, known as insulated metal substrate, consists of a metal core, typically aluminum or copper, coated with a dielectric insulation layer and a conductive copper layer for circuit traces. This structure delivers outstanding thermal management, with aluminum-based versions achieving thermal conductivity of 1-3 W/(m·K), while copper-based variants exceed 400 W/(m·K) for accelerated heat dissipation.
It serves effectively in high-power applications like LED lighting systems and automotive electronics, where efficient cooling maintains device stability and extends operational lifespan under thermal stress.
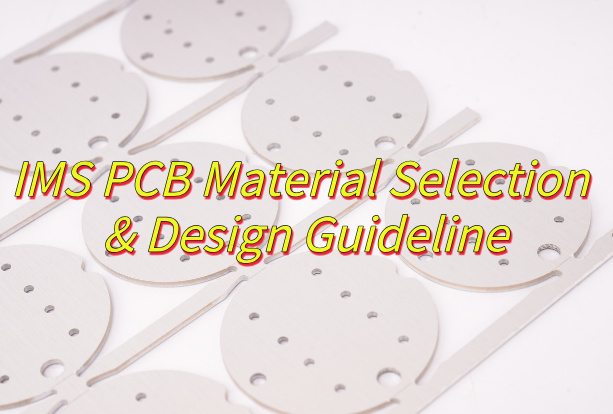
IMS PCB Material Properties
- Thermal Conductivity – Metal base (aluminum/copper) transfers heat 5-10x faster than FR4, keeping components cooler.
- Electrical Insulation– Dielectric layer provides high voltage isolation (1-10kV) while allowing heat flow.
- Mechanical Strength – Metal core resists bending/warping, ideal for heavy components or high-vibration environments.
- Thermal Expansion – Low CTE (Coefficient of Thermal Expansion) matches components, reducing solder joint stress.
- Temperature Resistance – Withstands 150-250℃ operating temperatures without degradation.
- Weight Efficiency – Aluminum bases offer lightweight heat dissipation, crucial for automotive/aerospace.
- Surface Flatness – Metal substrates ensure precise component mounting, critical for fine-pitch devices.
IMS PCB Board Material Datasheet
Property | Aluminum-Based IMS | Copper-Based IMS | Measurement Standard |
Thermal Conductivity | 1-3 W/(m·K) | >400 W/(m·K) | ASTM E1461 |
Dielectric Strength | ≥4 kV/mm | ≥4 kV/mm | IPC-TM-650 2.5.6 |
CTE (Z-axis) | 12-15 ppm/°C | 16-18 ppm/°C | IPC-TM-650 2.4.24 |
Tg (Glass Transition) | 130-150°C | 150-170°C | IPC-TM-650 2.4.25 |
Td (Decomposition) | 300-320°C | 350-380°C | IPC-TM-650 2.3.40 |
Volume Resistivity | ≥10¹² Ω·cm | ≥10¹² Ω·cm | IPC-TM-650 2.5.17 |
Flexural Strength | 100-150 MPa | 200-250 MPa | IPC-TM-650 2.4.4 |
What Are Types of IMS PCB Material?
Aluminum-Based IMS
- Thermal Conductivity: 1-2.5W/m·K.
- Application: LED lighting, consumer power supplies, and automotive controls where cost efficiency and moderate heat dissipation are prioritized.
Copper-Based IMS
- Thermal Conductivity: 3-4W/m·K.
- Application: High-power industrial drives, automotive powertrains, and aerospace components requiring extreme thermal performance.
Stainless Steel-Based IMS
- Thermal Conductivity: 0.2-0.5W/m·K.
- Application: Corrosive environments (e.g., marine, chemical processing) where mechanical durability outweighs thermal needs.
Composite Metal Core IMS
- Structure: Aluminum/copper layer bonded to a thin copper circuit layer.
- Application: Compact devices like mobile chargers and RF amplifiers needing both heat spreading and fine-pitch circuitry.
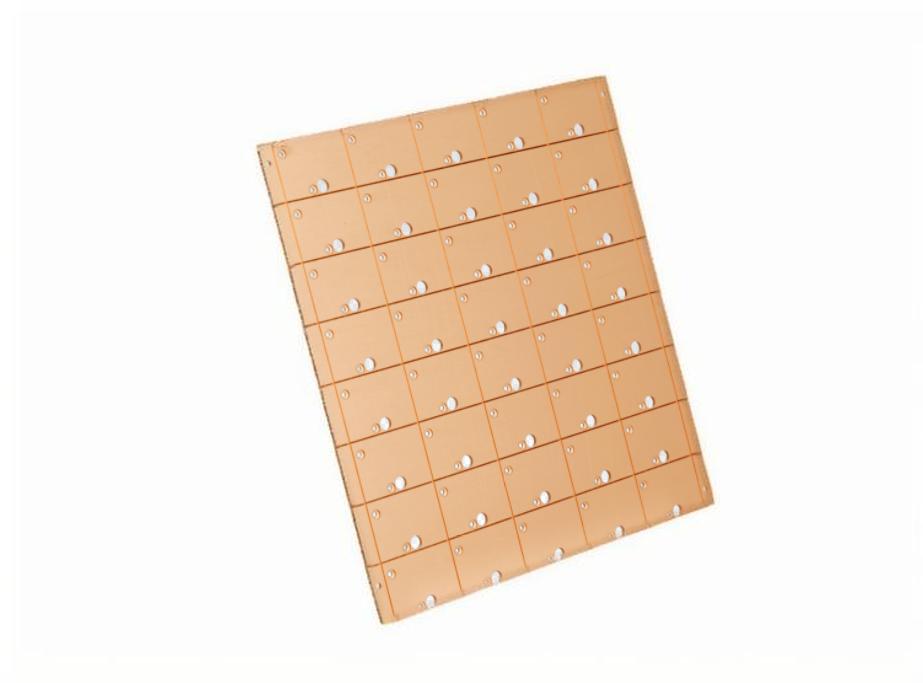
How to Choose IMS PCB Material?
IMC PCB Material Selection Guideline:
1. Assess Power Density Requirements
- High-Power Applications (e.g., industrial drives, automotive power modules):
- Choose copper-based IMS (thermal conductivity 3-4W/m·K) for power densities exceeding 5W/cm².
- Standard Applications (e.g., LED lighting, consumer electronics):
- Prioritize aluminum-based IMS (1-2.5W/m·K) for power densities below 5W/cm².
2. Align with Budget Constraints
- Aluminum-based IMS costs 20-30% less than copper, making it suitable for cost-driven projects like household appliances.
- Reserve copper-based IMS for premium sectors (aerospace, medical devices) where long-term reliability outweighs upfront costs.
3. Match Environmental Conditions
- Corrosive Environments (marine, chemical processing): Select stainless steel-based IMS for corrosion resistance, despite lower thermal efficiency.
- High-Temperature Zones (engine compartments, RF amplifiers): Use copper-based IMS with polyimide insulation (withstanding temperatures >200°C).
4. Account for Spatial Limitations
- Compact Devices (mobile chargers, wearables): Choose aluminum composite IMS (0.8mm thickness) to balance heat dissipation and space efficiency.
- Multi-Layer Designs: Prioritize copper-based IMS for structural rigidity, preventing warping in complex PCB stacks.
5. Validate Compliance with Standards
- Critical Systems (automotive ECU, aerospace): Demand IPC-6013-certified copper-based IMS with documented thermal cycling test results.
- Consumer Products (TVs, monitors): Aluminum-based IMS meets 85°C operational requirements for typical use cases.
6. Decision-Making Framework
- Start with power density thresholds to narrow material options.
- Cross-reference with budget allocation and environmental exposure.
- Finalize with space constraints and certification needs.
7. Application Examples
- Industrial Motor Control: Copper-based IMS for sustained 100A+ current handling.
- Outdoor LED Displays: Aluminum-based IMS with conformal coating for humidity resistance.
- Automotive Powertrain: Copper-based IMS + high-temperature dielectric for under-hood reliability.
8. Critical Precautions
- Request third-party thermal resistance reports to verify supplier claims.
- Avoid materials with unspecified dielectric breakdown voltage in high-voltage applications.
- Test prototypes under real-world thermal stress before mass production.
How to Design IMS PCB Board?
1. Define Design Objectives
- Clarify power density (W/cm²), operating environment (temperature/humidity), space limits, and budget. Example: Automotive ECU board needing 50A current handling in 100°C engine bay.
2. Material Selection Recap
- High-Power (>5W/cm²): Copper-based IMS (3-4W/m·K).
- Cost-Sensitive: Aluminum-based IMS (1-2.5W/m·K).
- Corrosive Environments: Stainless steel-based IMS.
3. Layer Stackup Design
- Place metal base directly below high-power components.
- Keep dielectric layer thickness ≤100µm for optimal thermal performance.
- Example: 2-layer IMS (copper base + 35µm circuit layer).
4. Thermal Management Strategies
- Thermal Vias: Use 0.5mm diameter filled vias under hot components, spaced 1mm apart.
- Reserved Cooling Zones: Allocate 30-50% of board area as unpopulated metal regions.
- Component Placement: Center power devices (MOSFETs/IGBTs) over the metal core; keep ≥2mm spacing between high-power parts.
5. Electrical Layout Optimization
- Trace Width: Use 3oz (105µm) copper for traces carrying >50A. Widen traces by 2x near heat sources.
- Avoid Sharp Bends: Maintain ≥3x trace width for bend radii to reduce resistance.
- Impedance Control: For RF/high-speed signals, keep dielectric thickness consistent (±10µm tolerance).
6. Manufacturing Compatibility
- Design Rules: Minimum trace width/spacing ≥0.2mm for aluminum IMS; ≥0.15mm for copper IMS.
- Solder Mask: Remove mask in thermal zones to maximize metal exposure.
- Panelization: Add 2mm border around boards for handling during assembly.
7. Validation & Testing
- Thermal Imaging: Test under max load to identify hotspots. Junction temp should stay ≤85°C.
- Electrical Testing: Verify current capacity and signal integrity (e.g., <5% voltage drop).
- Reliability Testing: Conduct thermal cycling (-40°C to +125°C, 100 cycles) and vibration tests (2G RMS).
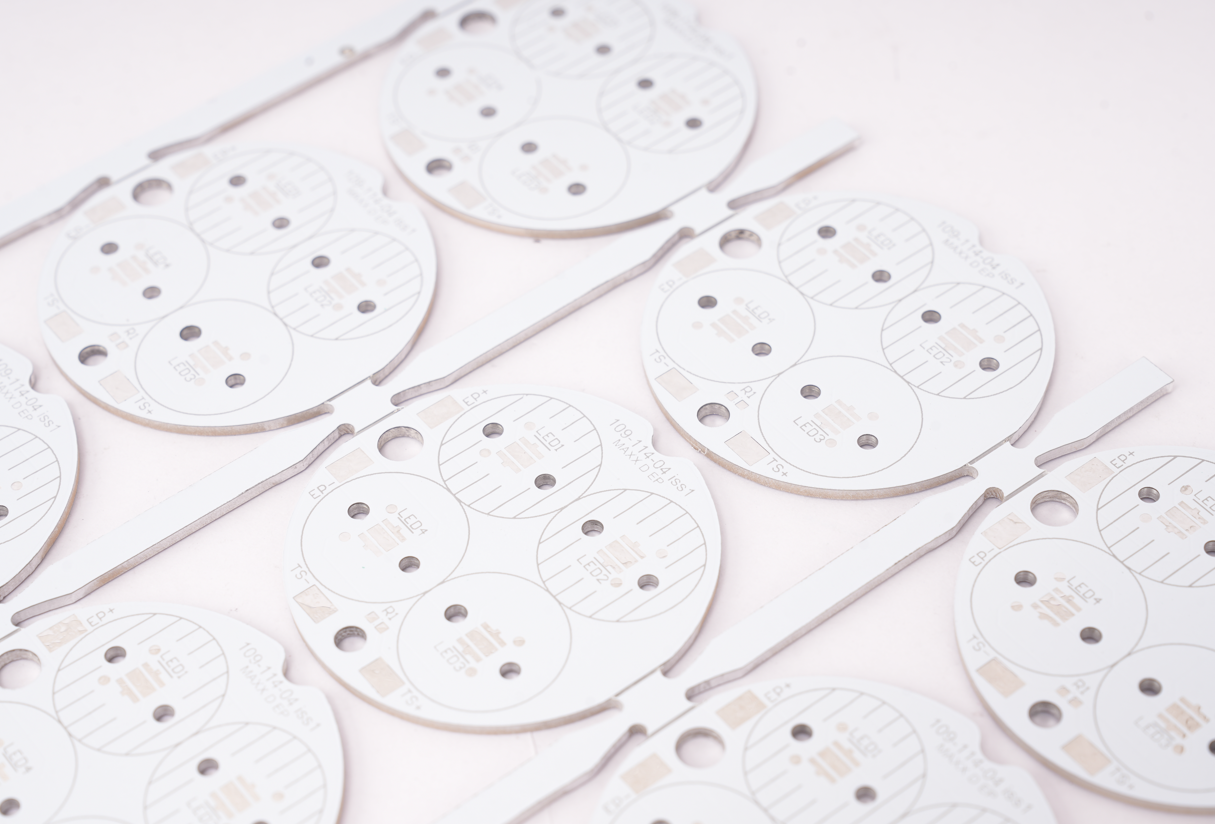
IMS PCB Board Design Considerations
Thermal Management
- Base Material Selection: Aluminum (1-3 W/mK) suits cost-sensitive, moderate-heat applications like LED lighting. Copper (>400 W/mK) is ideal for high-power modules requiring rapid heat dissipation.
- Dielectric Thickness: Thinner layers (50-100μm) improve heat transfer but reduce voltage isolation. Match thickness to operational voltage (e.g., 100μm for <1kV).
- Component Placement: Position high-heat components (e.g., power ICs, LEDs) directly over the metal core to maximize thermal path efficiency.
Electrical Performance
- Trace Width/Spacing: Wider traces reduce resistance for high-current paths. Maintain ≥0.3mm spacing for 1kV isolation in standard designs.
- Via Usage: Avoid thermal vias in the dielectric layer, they disrupt heat flow. Route signals through peripheral non-metal zones.
- High-Frequency Limits: IMS materials exhibit higher dielectric loss than FR-4. Limit use in RF circuits (>500MHz).
Mechanical Design
- Board Thickness: Standard metal cores (1.0-3.0mm) prevent flexing but increase weight. For lightweight needs, consider 1.0mm aluminum.
- Mounting Hardware: Use insulated standoffs to prevent short circuits with the metal base. Account for CTE mismatch, aluminum expands 23ppm/°C versus 17ppm/°C for copper.
- Cutouts & Edges: Smooth, rounded edges minimize stress concentrations. Internal cutouts require laser processing to avoid burrs.
Manufacturing & Cost
- Fabrication Tolerance: IMS requires specialized drilling (carbide bits) due to metal hardness. Allow ±0.1mm for hole positioning.
- Panel Utilization: Standard panel sizes (18″×24″) optimize cost. Odd shapes increase waste.
- Finish Options: HASL is cost-effective but limits thermal performance. ENIG (Ni/Au) enhances solderability for fine-pitch components.
Application-Specific Tips
- LED Arrays: Use 1.5mm aluminum cores with 80μm dielectric to balance cost and heat dissipation (ΔT<15°C at 5W/cm²).
- Automotive Inverters: Copper cores with 150μm dielectric handle 10-15A/mm² current density and 125°C ambient temperatures.
- Aerospace: Stainless steel bases provide vibration resistance but require thermal interface materials (TIMs) to offset lower conductivity.
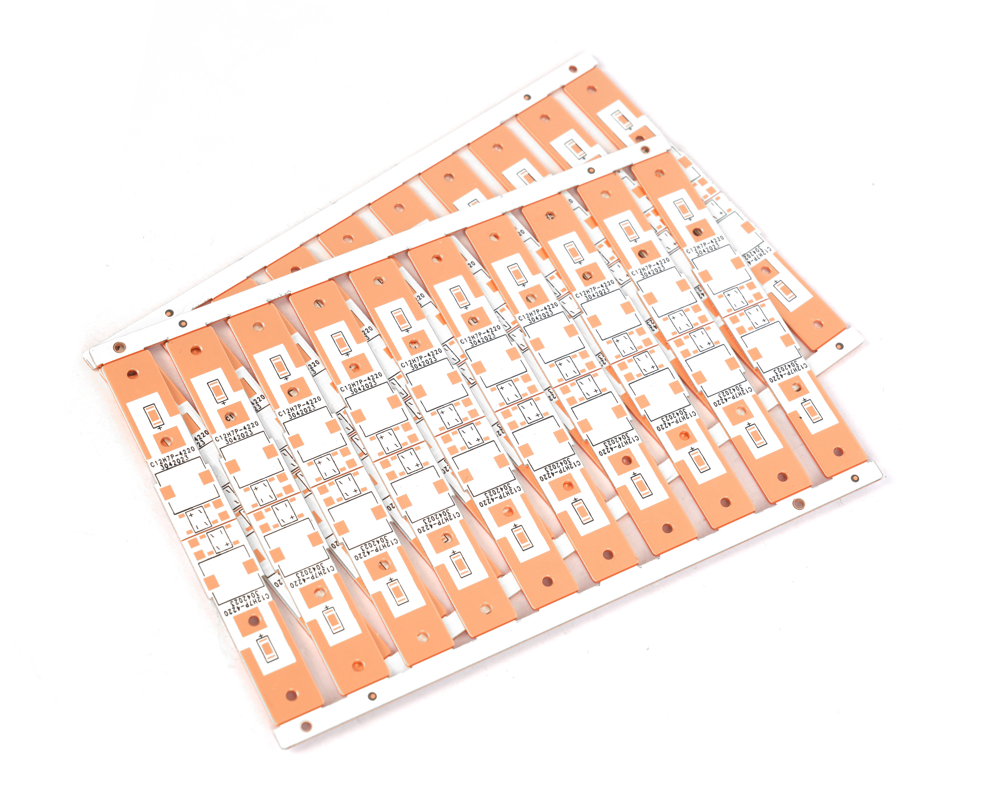
How to Select A Reliable IMS PCB Manufacturer?
Tips for selecting a reliable IMS PCB manufacturer:
- Confirm Thermal Management Expertise: Verify experience with aluminum/copper cores and UL-certified dielectric materials for effective heat dissipation in high-power applications.
- Demand Precision Manufacturing Capabilities: Ensure ≤50μm laser drilling accuracy for microvias and tight tolerances (±25μm) critical for thermal performance.
- Require Relevant Quality Certifications: Prioritize IATF 16949 (automotive) or ISO 13485 (medical) certified suppliers with documented thermal cycling tests (-40°C to +150°C).
- Evaluate True Production Speed: Compare realistic lead times. Proven manufacturers deliver prototypes in 7 days, 30% faster than industry norms without compromising quality.
- Insist on Transparent Costing: Avoid hidden fees. Competitive suppliers offer fixed pricing with 5-15% savings through efficient material utilization.
- Check Scalability from Prototype to Volume: Choose partners handling orders from 5 panels to mass production seamlessly within their facilities.
- Prioritize Technical Partnership: Select manufacturers providing free 24-hour DFM feedback and thermal simulation support to optimize your design.
- Experience the Best Technology Advantage: Get a rapid quote for your IMS PCB project today. We combine certified quality, 7-day prototype turnaround, and cost-competitive pricing—ensuring your thermal management solution excels. Request your quote now.
Ready to start your project? Contact Best Technology today for competitive pricing, guaranteed fast delivery, and certified quality. Let’s optimize your thermal management solution together: sales@bestpcbs.com.