Why partner with a PCB manufacturing company for your next project? This guide reveals strategies from rapid prototyping to fast assembly, balancing cost and quality.
Best Technology stands as your trusted PCB manufacturing partner with proven capabilities to accelerate your product development. Our 24-hour rapid prototyping service maintains a 99.2% on-time delivery rate, while our optimized assembly processes reduce standard lead times by 30-50% compared to industry benchmarks. With over 8,000 successful projects completed for clients in automotive, medical, and industrial applications, we deliver consistent quality through ISO 9001-certified production facilities achieving 99.97% first-pass yield. Our engineering team (averaging 10+ years’ experience) provides complimentary DFM analysis that typically identifies and resolves 28% of potential manufacturing issues before production begins. We maintain transparent pricing with no hidden costs, offering 15-20% cost advantages through optimized material sourcing and lean manufacturing. Contact us today for a competitive quote backed by our on-time delivery guarantee and dedicated project management from prototype to volume production: sales@bestpcbs.com.
Where You Can Find A PCB Manufacturing Company?
You can find a PCB manufacturing company by following methods:
- Explore Online Industry Directories and Platforms: Begin by researching global directories and platforms dedicated to electronics manufacturing. These resources often list companies with expertise in PCB design, fabrication, and assembly, along with customer reviews and certifications. For instance, regions like Shenzhen, China, are renowned as hubs for PCB manufacturing, hosting numerous vendors with advanced capabilities. Additionally, industry reports or local environmental agency data may highlight clusters of certified and experienced firms in specific areas.
- Attend Trade Shows and Virtual Exhibitions: Participate in trade shows or virtual exhibitions focused on electronics manufacturing. These events gather suppliers showcasing their capabilities, from quick-turn prototyping technologies to high-volume production lines. For example, international exhibitions in South Korea or other technology-forward regions often feature sections dedicated to SMT/PCB manufacturing, offering opportunities to compare vendors directly.
- Leverage Professional Networks and Forums: Engage with professional communities or forums focused on hardware development or engineering. These platforms frequently host discussions, reviews, or recommendations from peers who have firsthand experience with PCB manufacturers. Networking within these groups can provide insights into vendors’ reliability, responsiveness, and technical expertise.
- Seek Out Environmental and Sustainability Certifications: Verify the company’s compliance with environmental regulations, such as RoHS or local waste management guidelines. Manufacturers committed to sustainability often use eco-friendly materials, recycle waste, and implement energy-efficient processes, which can be important for long-term ethical and operational stability.
- Research SMT PCB Manufacturing Exhibitions: Exhibitions focused on surface-mount technology (SMT) and PCB manufacturing provide a platform to discover companies specializing in advanced assembly processes. These events often include live demonstrations, technical seminars, and networking opportunities with industry experts.

What Should You Look for in a Reliable PCB Manufacturing Company?
Below are methods about how to choose a reliable PCB manufacturing company:
- Quick-Turn Prototyping Capabilities: Prioritize for manufacturers that provide rapid prototyping services. This allows you to test designs, validate functionality, and iterate quickly without significant delays, accelerating your product development cycle.
- Certifications and Quality Standards: Look for manufacturers with certifications such as ISO 9001, AS9100, or UL approval. These certifications indicate adherence to rigorous quality control processes, including automated optical inspection (AOI) and electrical testing, which minimize defects and ensure product reliability.
- Service Range and Expertise: Choose a company that offers end-to-end services, from PCB design and prototyping to assembly and volume production. Firms experienced in handling diverse projects, such as multi-layer boards, HDI (High-Density Interconnect), or rigid-flex PCBs, demonstrate adaptability to complex requirements.
- Material and Customization Options: Ensure the company can accommodate specific material needs, such as Rogers, FR-4, or high-frequency laminates, and offers finishes like ENIG or immersion silver. Flexibility in assembly processes, including SMT (Surface Mount Technology) and through-hole, ensures compatibility with your project’s technical specifications.
- Environmental and Sustainability Practices: Verify compliance with environmental regulations like RoHS and REACH. Manufacturers committed to sustainability often use lead-free soldering, recycle materials, and minimize waste, aligning with ethical and operational standards.
- Transparent Communication and Support: Partner with companies that provide dedicated project managers and clear documentation, such as detailed quotes, production timelines, and inspection reports. Responsive communication helps resolve issues promptly and ensures smooth collaboration.
- Cost-Efficiency and Scalability: Evaluate pricing models that balance cost with quality, including tiered options for urgent orders. Ensure the manufacturer can scale production from prototypes to large batches without compromising deadlines or budgets.
- Industry Experience and Client Feedback: Research the company’s track record in serving industries like aerospace, medical devices, or consumer electronics. Client testimonials and case studies offer insights into their problem-solving abilities and reliability under tight deadlines.
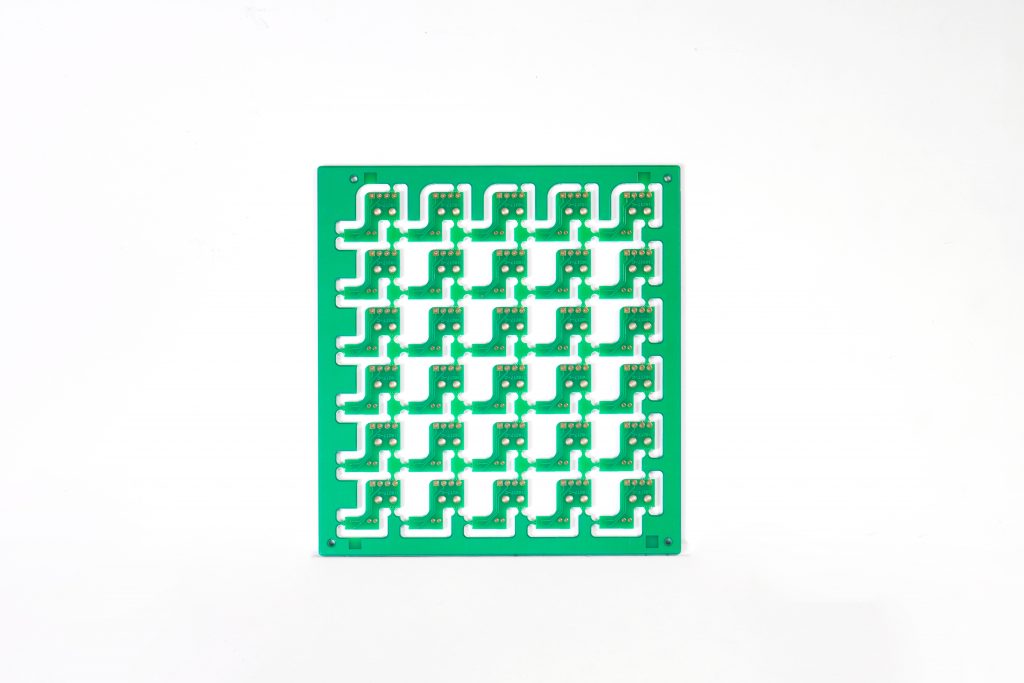
How to Reduce PCB Manufacturing Costs Without Comprising Quality?
Here are how to reduce PCB manufacturing costs without comprising quality:
- Optimize PCB Design Complexity: Simplify designs by minimizing unnecessary layers, via counts, and intricate features. For example, reducing a 6-layer board to 4 layers can lower material and fabrication costs while maintaining functionality if the design permits. Standardize hole sizes and trace widths to streamline production and reduce errors.
- Leverage Cost-Effective Materials: Select materials that balance performance and budget. FR-4, a widely used substrate, often provides a cost-efficient alternative to high-frequency laminates unless specific electrical properties are required. Collaborate with your manufacturer to identify affordable yet reliable substitutes for specialized materials.
- Consolidate Orders for Bulk Production: Combine multiple projects or versions into a single larger order to negotiate volume discounts. Manufacturers frequently offer tiered pricing, reducing per-unit costs as quantities increase. If immediate bulk production isn’t feasible, phase orders strategically to align with production schedules.
- Adopt Automated Manufacturing Processes: Partner with factories using advanced equipment like SMT (Surface Mount Technology) lines and AOI (Automated Optical Inspection). Automation reduces labor costs, minimizes human error, and accelerates production, ultimately lowering your expenses while maintaining precision.
- Streamline Supply Chain Collaboration: Build long-term relationships with a trusted manufacturer to secure preferential pricing and priority support. Regularly compare quotes from multiple vendors to ensure competitiveness, but prioritize reliability over marginal savings. Engage suppliers early to refine designs and avoid costly post-production revisions.
- Utilize Efficient Prototyping Methods: Prioritize for quick-turn prototyping services to validate designs before full-scale production. This reduces the risk of errors in mass batches, saving rework costs. Some manufacturers offer discounted or free prototypes for repeat clients, further cutting expenses.
- Prioritize Quality Control Over Excessive Testing: While rigorous testing is essential, avoid over-specifying inspections. Work with your manufacturer to define necessary quality thresholds, such as visual checks for basic boards versus X-ray testing for complex HDI designs. Balancing testing with budget constraints prevents unnecessary costs.
- Explore Sustainable Practices for Long-Term Savings: Choose eco-friendly materials or processes that may qualify for tax incentives or subsidies. Recycling programs for leftover materials or energy-efficient production methods can also reduce long-term operational costs.
Why Choose PCB Prototyping?
Here are reasons about why choose PCB prototyping:
- Identify and Resolve Design Flaws Early: Prototyping allows you to test your PCB design under real-world conditions before mass production. This early-stage validation helps uncover issues like signal integrity problems, thermal management gaps, or component placement errors. Addressing these flaws during prototyping prevents costly rework or product failures later.
- Reduce Long-Term Costs: While prototyping incurs upfront expenses, it saves money by avoiding large-scale production of faulty boards. For example, a minor error in a 4-layer PCB design could render an entire batch unusable, but a prototype lets you fix it at a fraction of the cost.
- Accelerate Time-to-Market: Rapid prototyping services enable quick design iterations. By refining your PCB in weeks rather than months, you can launch products faster, gaining a competitive edge in fast-paced industries like consumer electronics or IoT.
- Verify Functional Performance: Prototypes let you test electrical performance, mechanical fit, and thermal stability. For instance, you can confirm if a high-power PCB meets heat dissipation requirements or if a flexible PCB withstands bending stresses in its intended application.
- Enhance Collaboration with Manufacturers: Sharing prototypes with your manufacturing partner fosters better communication. They can provide feedback on design-for-manufacturability (DFM) issues, such as trace widths or solder mask alignment, ensuring smoother transition to mass production.
- Customize for Specific Applications: Prototyping supports experimentation with specialized features, such as HDI (High-Density Interconnect) for compact devices or rigid-flex PCBs for wearable tech. This flexibility ensures your product meets unique market demands.
- Mitigate Supply Chain Risks: By validating component selections and layouts early, you reduce the risk of part shortages or obsolescence during mass production. Prototyping also helps identify alternative suppliers if certain components become unavailable.
- Secure Funding or Investments: A functional prototype demonstrates your product’s viability to stakeholders, investors, or clients. It provides tangible proof of concept, increasing confidence in your project’s success.
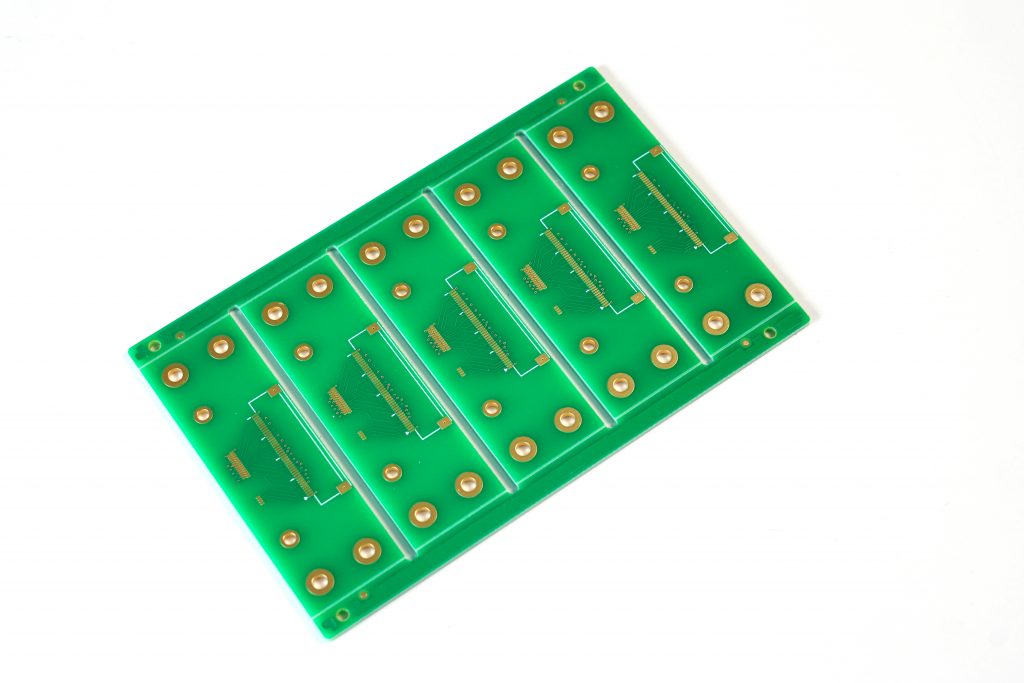
How to Choose Materials for Budget PCB Prototypes?
Below are how to choose materials for budget PCB prototypes:
- Start with Standard Substrates: Prioritize FR-4, the most economical and versatile substrate. It meets the needs of most general-purpose prototypes, offering a balance of durability, electrical insulation, and affordability. Unless your design requires high-frequency performance or extreme thermal stability, avoid premium laminates like Rogers or PTFE during prototyping.
- Align Copper Thickness with Requirements: Choose standard copper weights, such as 1 oz/ft² or 0.5 oz/ft², to reduce costs. Thicker copper increases material and fabrication expenses. Ensure the selected thickness matches your prototype’s current-carrying needs to avoid performance issues.
- Reduce Layer Count Strategically: Minimize expenses by using the fewest layers possible. A 2-layer board often suffices for simple circuits, while 4-layer designs handle moderate complexity. Avoid unnecessary ground or power planes unless critical for signal integrity in your prototype.
- Simplify Surface Finishes: Select HASL (Hot Air Solder Leveling) with lead-free solder for cost efficiency. While ENIG (Electroless Nickel Immersion Gold) offers superior solderability, it comes at a higher price. HASL is adequate for most prototypes unless fine-pitch components or flat surfaces are required.
- Repurpose Excess Materials: Collaborate with manufacturers to utilize leftover materials from other projects. Some factories offer discounted rates for boards fabricated using scrap or pre-cut panels, reducing waste and your expenses.
- Consolidate Orders for Volume Discounts: Combine multiple prototype projects or versions into a single larger order to negotiate lower per-unit costs. Even if delivered in phases, bulk orders often qualify for tiered pricing.
- Use Standard Drill Sizes: Avoid microvias or laser-drilled holes during prototyping. Larger, standard drill sizes (e.g., 0.3 mm–0.8 mm) are cheaper to fabricate and reduce the risk of drilling errors.
- Engage Manufacturers Early in Design: Consult your PCB partner during the design phase. They can suggest material substitutions or design adjustments that cut costs without sacrificing functionality. For example, they might recommend a thinner board thickness or an alternative laminate brand.
- Avoid Over-Engineering: Resist adding unnecessary features. Every additional specification—from impedance control to specialized coatings—adds cost. Focus on validating core functionality first, then refine details in later iterations.
- Balance Performance and Budget: Prioritize material choices based on your prototype’s intended use. If testing basic functionality, standard materials suffice. Reserve high-performance options for final production if needed.
How to Achieve 24 Hours PCB Board Prototyping for Faster Time-To-Market?
To achieve 24-hour PCB prototyping and accelerate your time-to-market, focus on streamlining processes:
Simplify PCB Design Complexity
- Reduce layer counts (e.g., use 2-layer instead of 4-layer boards) and minimize non-essential features like blind/buried vias or fine-pitch components.
- Standardize hole sizes, trace widths, and spacing to align with automated production equipment.
- Use pre-approved library components and modular design blocks to speed up layout.
Partner with Fast-Turn Manufacturers
- Select a PCB manufacturer offering 24-hour turnaround services, often available for simple designs (e.g., ≤4 layers, ≤100mm x 100mm).
- Confirm their capabilities include automated optical inspection (AOI), direct imaging, and in-house drilling to eliminate delays from third-party vendors.
Optimize File Preparation
- Submit production-ready Gerber files, BOMs, and centroid data with clear annotations to avoid back-and-forth revisions.
- Use design software with built-in DRC (Design Rule Check) tools to catch errors before submission.
Prioritize Rapid Communication
- Assign a dedicated contact at the manufacturer for urgent queries.
- Use real-time collaboration tools (e.g., shared cloud folders, instant messaging) to resolve issues instantly.
Leverage Local or Regional Suppliers
- Choose a manufacturer in your time zone or region to reduce shipping delays and enable same-day courier pickup for last-minute adjustments.
Pre-Negotiate Expedited Terms
- Establish a contract for priority access to 24-hour slots, even during peak seasons.
- Understand any surcharges for rush orders and factor them into your budget.
Adopt Automated Ordering Platforms
- Use online portals that allow instant quote generation, file uploads, and order tracking.
- Some platforms offer AI-driven DFM (Design for Manufacturability) checks to flag issues in seconds.
Limit Customization for Initial Prototypes
- Avoid specialized finishes (e.g., immersion gold) or materials (e.g., high-Tg laminates) unless critical for testing.
- Postpone non-functional cosmetic features (e.g., silkscreen colors, edge plating) to subsequent iterations.
Plan for Parallel Workflows
- While the PCB is in production, begin assembling components or programming firmware to save time.
- Use 3D-printed mechanical fixtures to test form factors alongside PCB validation.
Implement Post-Production Quality Checks
- Request a brief functional test (e.g., continuity check, basic power-on) before shipping.
- If issues arise, rely on the manufacturer’s quick-rework team to fix minor problems within hours.
How to Minimize PCB Assembly Defects Without Slowing Down Production?
To minimize PCB assembly defects while maintaining production speed, implement the following structured, actionable strategies:
Automate Inspection Processes
- Integrate Automated Optical Inspection (AOI) and X-ray machines to detect solder joint issues, misplaced components, or tombstoning in real time. These systems operate at high speeds without slowing down lines.
- Use In-Circuit Testing (ICT) to validate electrical performance post-assembly, catching defects like opens, shorts, or component value discrepancies before final packaging.
Optimize SMT Programming
- Streamline Surface Mount Technology (SMT) placement programs to reduce machine head movements. Shorter paths minimize vibration and component shifting during pickup-and-place cycles.
- Prioritize component grouping by size or type to limit nozzle changes and feeder adjustments, which are common time-wasters.
Implement Real-Time Data Monitoring
- Deploy IoT sensors on assembly lines to track parameters like oven temperature profiles, stencil print pressure, and conveyor speed. Alerts flag deviations instantly, preventing batch defects.
- Use AI-driven analytics to predict defects based on historical data, enabling proactive adjustments before issues arise.
Standardize Workflows and Tooling
- Adopt fiducial markers and panelization to improve alignment accuracy during reflow soldering. Consistent panel designs reduce setup times between jobs.
- Use universal stencils with interchangeable apertures for frequent board revisions, eliminating stencil changeover delays.
Train Operators on Defect Prevention
- Conduct daily 5-minute safety and quality briefings to reinforce best practices, such as proper ESD handling or solder paste stencil cleaning.
- Cross-train staff to operate multiple machines, reducing downtime during shift changes or equipment breakdowns.
Pre-Qualify Component Suppliers
- Partner with distributors offering tape-and-reel services with tight tolerance specifications to minimize feeding errors during SMT.
- Require Component Outline Drawings (CODs) and 3D STEP models from suppliers to verify part compatibility with pick-and-place machines.
Adopt Lean Inventory Practices
- Implement kanban systems for reels of common components (e.g., 0402 resistors, SOIC-8 chips) to ensure feeders are always stocked without overstocking.
- Use humidity-controlled cabinets for moisture-sensitive devices (MSLs) to prevent popcorning during reflow without slowing production for pre-baking.
Design for Assembly (DFA) Guidelines
- Enforce rules like minimum 0.2mm solder mask slivers and 0.15mm component spacing to reduce solder bridging risks.
- Avoid fine-pitch QFNs or 0201 passives in time-sensitive projects unless automated optical inspection (AOI) can validate them at full line speed.
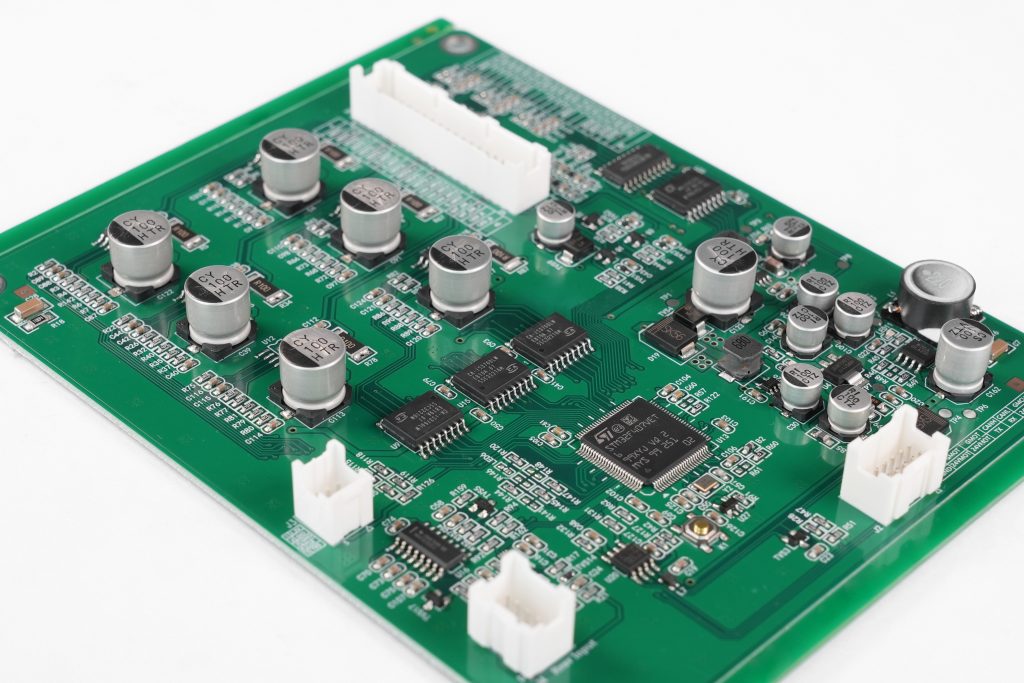
Which Automated Testing Tools Can Cut PCB Assembly Inspection Time by 50%?
Automated testing tools that can cut PCB assembly inspection time by 50% include:
Automated Optical Inspection (AOI) Systems
- Use multi-angle cameras and AI algorithms to detect solder joints, component placement, and polarity errors at speeds exceeding 10,000 components per hour.
- Reduce manual check time by 60–70% compared to visual inspections.
In-Circuit Testing (ICT) with Fixtureless Probes
- Bed-of-nails testers with spring-loaded probes validate electrical continuity, component values, and shorts in seconds per board.
- Modern systems cut test times by 40–50% via parallel testing and adaptive algorithms.
X-Ray Inspection for Complex Assemblies
- 3D computed tomography (CT) scanners identify voids, misaligned BGAs, or hidden solder joints in dense boards without disassembly.
- Faster than traditional 2D X-ray systems, reducing inspection time by 30–50% for high-mix production.
Flying Probe Testers
- Needle-less probes move dynamically to test unpopulated PCBs or low-volume runs, eliminating fixture setup delays.
- Shorten test times by 50% for prototypes or small batches compared to ICT.
Boundary-Scan (JTAG) Testers
- Programmatically verify connectivity for BGA or fine-pitch devices through chip-level self-tests, reducing physical probing needs.
- Cut test time by 70–80% for complex digital circuits.
Conclusion
This guide has explored the full spectrum of PCB manufacturing services, from rapid prototyping solutions to cost-effective assembly with automated testing tools that enhance efficiency. Whether you need aerospace-grade boards or budget-friendly prototypes, selecting the right partner is critical for quality and speed-to-market. For reliable PCB solutions that combine advanced technology with competitive pricing, contact Best Technology today. Our expertise in 24-hour prototyping, defect-minimized assembly, and material optimization ensures your project meets both deadlines and performance standards. Request a customized quote now to experience precision manufacturing tailored to your needs.