Why Choose RGBW LED PCB solutions? Explore technical specs, thermal management, cost-effective production, and manufacturer selection insights in this comprehensive guide.
Best Technology deliver fast and affordable RGBW LED PCB solutions for lighting projects without compromising quality. Our 24-hour rapid prototyping (standard designs ≤300mm) and 48-hour bulk order turnaround (up to 10,000㎡) are backed by automated SMT lines running 24/7. Competitive pricing cuts costs by 15–20% through optimized material sourcing—like FR4-Tg170 boards and direct supplier ties for copper substrates. Free DFM checks during sampling prevent layout errors, while fixed unit pricing for bulk orders (2700K–6500K color temps) ensures budget predictability. Every batch undergoes AOI/X-ray inspections, maintaining ≤0.3% defect rates. ISO 9001/UL-certified production and a dedicated engineering team (2-hour response for urgent revisions) provide reliability for smart lighting, retail displays, or architectural projects. Whether you need 500 units or 50,000, we merge speed, precision, and value to keep your timelines and margins intact. Welcome to contact us: sales@bestpcbs.com
What Is RGBW LED PCB?
A RGBW LED PCB is a printed circuit board specifically engineered to integrate red, green, blue, and white light-emitting diodes (LEDs) into a unified lighting system. Unlike standard RGB LED configurations, which rely on color mixing from red, green, and blue diodes to simulate white light, RGBW PCBs incorporate a dedicated white LED chip. This fourth channel enables precise control over both colored and pure white light outputs, eliminating the color inaccuracies and energy inefficiencies often caused by blending RGB channels. The PCB’s design incorporates advanced circuitry to manage power distribution, heat dissipation, and signal synchronization across the LEDs, ensuring consistent performance. Materials like aluminum-core substrates or high-grade FR4 are commonly used to enhance thermal conductivity and structural durability, while surface-mount technology (SMT) allows for compact, high-density LED arrangements. This technology is ideal for applications demanding accurate color reproduction, high lumen output, and energy efficiency, as the white diode directly generates neutral or warm/cool white light without relying on RGB combinations.
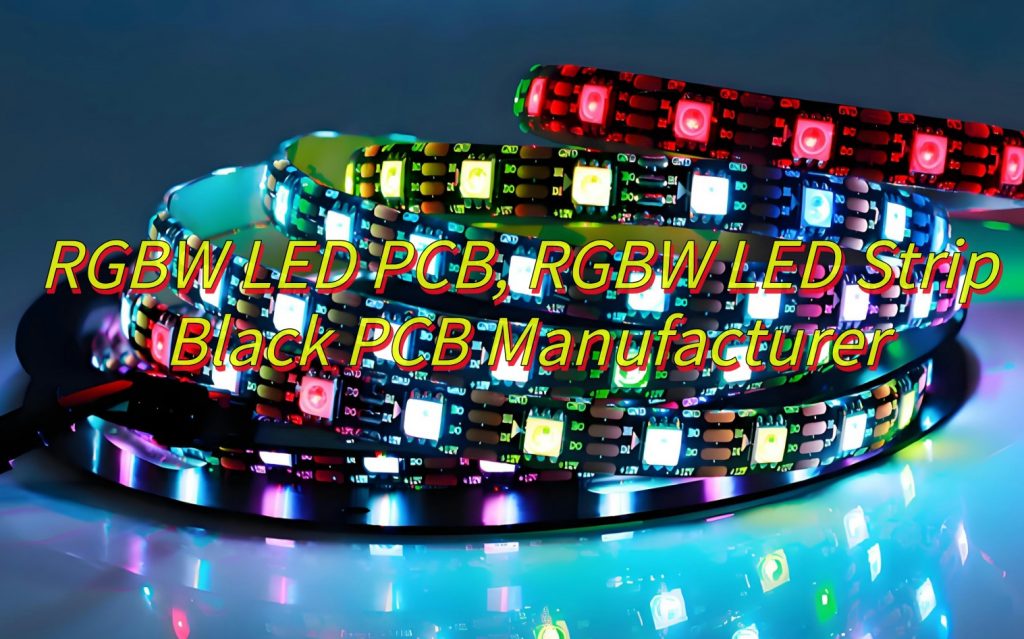
What Are Application of RGBW LED PCB?
Below are applications of RGBW LED PCB:
- Dynamic Lighting Control – RGBW LED PCB enable precise blending of colors and adjustable white light temperatures (2700K–6500K). The dedicated white diode ensures stable correlated color temperature (CCT) (±50K tolerance) without relying on RGB mixing, reducing color inaccuracies.
- High-Fidelity Color Rendering – These RGBW LED PCBs achieve a Color Rendering Index (CRI) above 90, ensuring accurate representation of hues. The white channel expands the color gamut, allowing richer and more vivid visual outputs.
- Smart Device Interfaces – RGBW LED PCBs power LED rings and matrices in interactive devices (e.g., smart speakers, TVs) for visual feedback. Independent control of each diode enables customizable patterns and animations.
- Energy-Efficient Illumination – By eliminating energy waste from RGB-mixed white light, RGBW designs achieve higher luminous efficacy (up to 108 lm/W). Compact PCB designs with thermal management ensure stable performance under high loads.
- Compact and Customizable Solutions – Smaller RGBW diodes (e.g., 4040-sized chips) allow integration into tight spaces while maintaining color temperature and CRI customization. This makes them ideal for applications requiring miniaturized yet high-performance lighting.
- Precision Color Modulation – Advanced PWM algorithms and feedback loops enable granular control over brightness and color balance, supporting complex lighting scenarios.
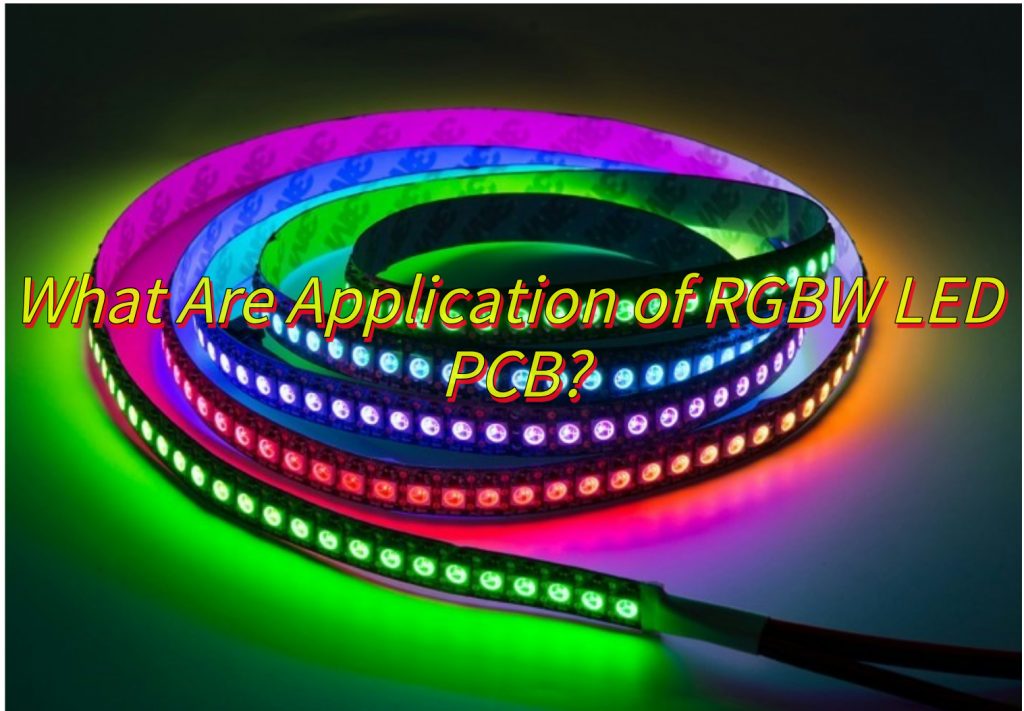
What Is the Color Temperature of RGBW LED PCB?
The color temperature of a RGBW LED PCB refers to the correlated color temperature (CCT) of the white light generated by its dedicated white diode, which typically spans 2500K (warm white) to 7000K (cool white). Unlike standard RGB LEDs that simulate white light by blending red, green, and blue wavelengths, RGBW LED PCBs use a separate white LED chip to directly produce tunable white light. This white diode can be adjusted to emit warm (2500K–3700K), neutral (3700K–4750K), or cool (4750K–7000K) tones through pulse-width modulation (PWM) algorithms that regulate current flow and balance red/blue spectral ratios. The integration of a white channel eliminates color inaccuracies from RGB-based mixing, ensuring stable CCT values with minimal deviation (±50K in high-precision designs) while maintaining CRI (Color Rendering Index) above 90 for accurate color fidelity.
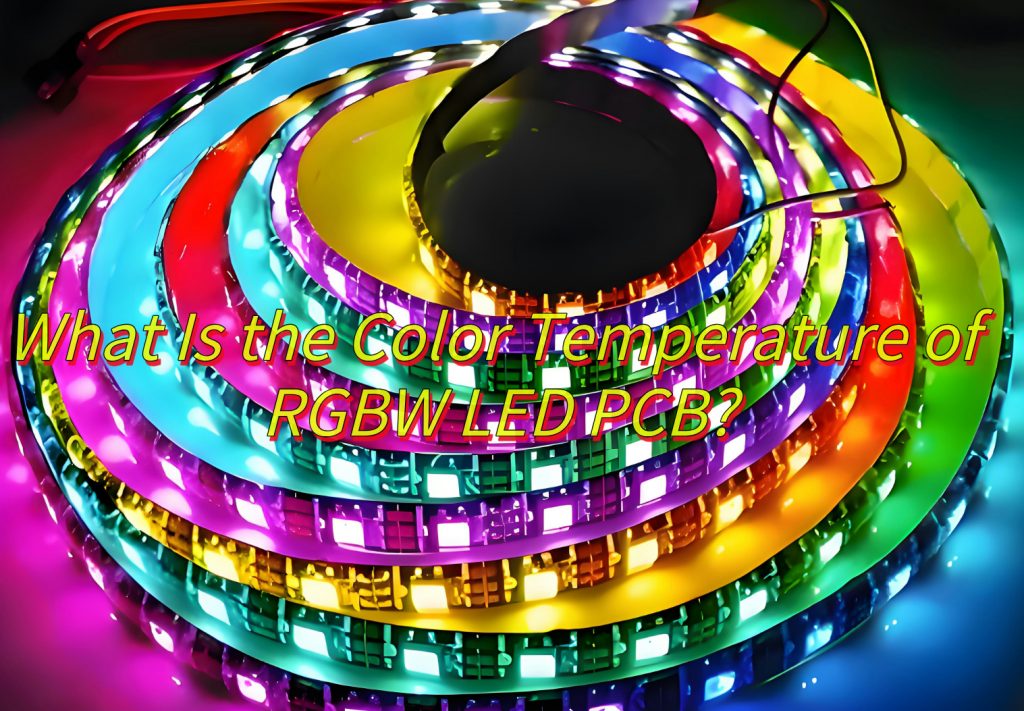
How to Design a Rigid RGBW LED PCB for Better Heat Dissipation?
Below is how to design a rigid RGBW LED PCB for better heat dissipation:
1. Material Selection
Substrate Material:
- FR-4: A cost-effective option with decent thermal stability, suitable for low-to-medium power applications.
- Metal-Core PCB (MCPCB): Aluminum or copper-core boards (e.g., IMS, Insulated Metal Substrate) offer superior heat conductivity, reducing thermal resistance by up to 80% compared to FR-4.
- Copper Thickness: Choose 2 oz. or 3 oz. copper layers to enhance current-carrying capacity and heat distribution.
2. Thermal Via Placement
- Via Arrays: Strategically place vias (plated-through holes) beneath LED pads to transfer heat from the component side to the PCB’s internal or external layers.
- Thermal Relief Pads: Use large annular rings or solid connections around LED pads to minimize thermal barriers.
3. Component Layout Optimization
- Spacing: Maintain a minimum of 2–3 mm between LEDs to prevent heat pooling and ensure airflow.
- High-Power LED Placement: Position RGBW diodes near the PCB edges or thermal vias to facilitate heat escape.
- Avoid Hotspots: Balance power-hungry components (e.g., drivers, regulators) across the board to distribute heat evenly.
4. Heat Sink Integration
- Direct Attachment: Bond the PCB to an aluminum heat sink using thermal tape or epoxy. Ensure full contact between the MCPCB’s metal core and the sink.
- Finned Designs: Use heat sinks with fins or pins to increase surface area for convection cooling.
5. Thermal Interface Materials (TIM)
- Gap Pads/Fillers: Apply silicone-based or ceramic-filled TIMs between the PCB and heat sink to eliminate air gaps and improve conductivity.
- Thermal Grease: Use low-viscosity grease for high-power applications to ensure maximum contact.
6. Convection and Airflow
- Ventilation Holes: Drill holes in non-component areas to promote air circulation (especially in enclosed fixtures).
- Forced Air Cooling: Incorporate fans or blowers for high-power RGBW strips (e.g., >10W per meter).
7. Trace Width and Current Handling
- Wider Traces: Increase copper trace widths (e.g., 20–30 mil) for power lines to reduce resistive heating.
- Thermal Relief in Traces: Avoid sharp bends in high-current paths to prevent localized heating.
8. Simulation and Testing
- Thermal Imaging: Use IR cameras to identify hotspots during prototyping.
- Software Tools: Leverage PCB design software (e.g., Altium, Eagle) with thermal simulation features to predict heat flow.
9. Environmental Considerations
- Ambient Temperature: Design for worst-case scenarios (e.g., 40°C+ environments) by derating LED current.
- Conformal Coating: Apply heat-resistant coatings (e.g., silicone) to protect against moisture without trapping heat.
How to Maintain Color Consistency in RGBW LED PCB Mass Production?
Achieving consistent color performance across RGBW LED PCBs during mass production requires rigorous control over components, processes, and quality assurance. Below is a structured approach to ensure uniformity in color output:
1. LED Binning and Supplier Collaboration
- Strict Binning: Work with LED manufacturers to source diodes from the same color bin (e.g., matching wavelength, luminous flux, and voltage).
- Tolerance Specifications: Define tight tolerances (e.g., ±100K for color temperature, ±5% for brightness) in supplier contracts.
- Batch Testing: Randomly sample LEDs from each production lot to verify compliance with binning criteria.
2. PCB Design for Uniformity
- Symmetrical Layout: Arrange RGBW diodes equidistant from heat sources (e.g., drivers, regulators) to minimize thermal drift.
- Thermal Vias: Place vias beneath LED pads to equalize heat dissipation across the board.
- Trace Width Consistency: Use identical trace widths for all LED power lines to avoid current imbalances.
3. Automated Soldering and Assembly
- SMT Precision: Deploy surface-mount technology (SMT) machines with laser alignment to ensure consistent LED placement (±0.05mm tolerance).
- Reflow Oven Profiling: Optimize temperature profiles to prevent overheating, which can alter LED wavelength or brightness.
4. Color Calibration at Production Line
- Inline Spectrometers: Integrate automated spectrometers to measure RGBW output in real time.
- Dynamic Adjustment: Use microcontrollers to tweak current levels for each channel, compensating for minor variations.
- Calibration Records: Store correction data (e.g., PWM offsets) in onboard EEPROM for post-production reference.
5. Aging and Burn-In Testing
- Pre-Aging: Operate PCBs at 80% rated power for 48–72 hours to stabilize LED performance.
- Post-Aging Calibration: Re-measure color parameters after aging to identify and correct long-term drift.
6. Environmental Controls
- Temperature-Controlled Rooms: Maintain production areas at 25°C ±2°C to eliminate ambient temperature effects.
- Humidity Management: Keep relative humidity below 60% to prevent solder joint degradation.
7. Quality Control (QC) Protocols
- 100% Inspection: Use machine vision systems to check LED placement, solder joints, and color uniformity.
- Statistical Process Control (SPC): Track color metrics across batches to detect trends.
- Failure Analysis: Root-cause analyze out-of-spec PCBs to refine processes (e.g., adjust solder paste stencil thickness).
8. Traceability and Documentation
- Serial Numbers: Laser-etch unique IDs on each PCB to link performance data to production records.
- Bin Mapping: Document LED lot numbers and their positions on the PCB for future reference.
9. Post-Production Tuning (Optional)
- Remote Calibration: For smart RGBW systems, enable firmware updates to adjust color balance via Bluetooth/Wi-Fi.
- Field Testing: Sample finished products in real-world conditions to validate long-term consistency.
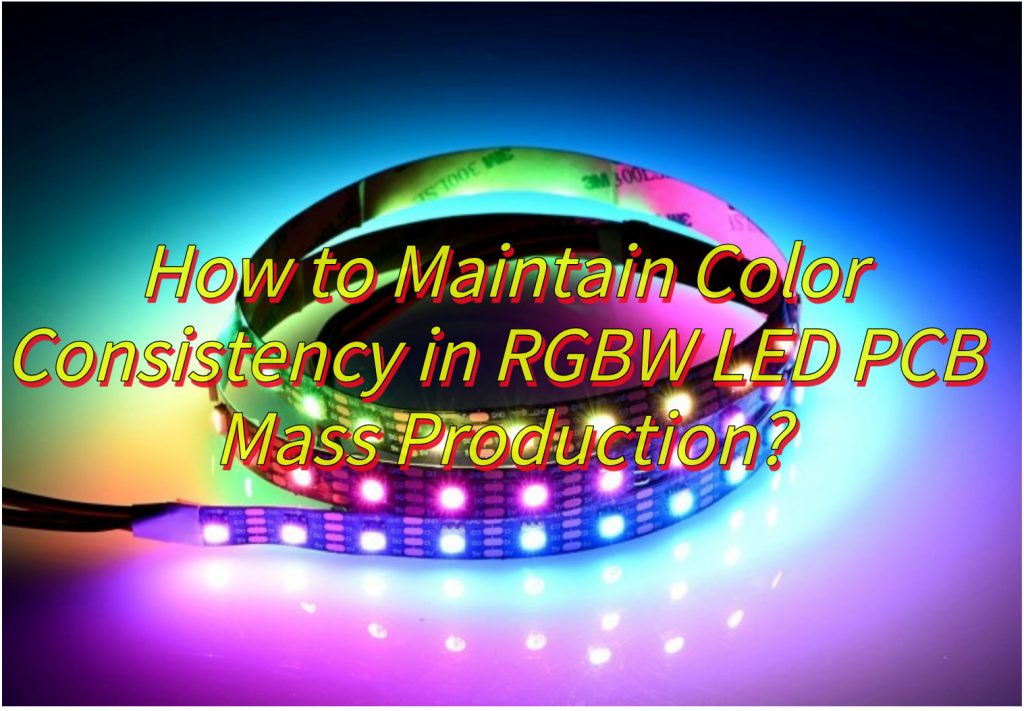
Which Manufacturing Method Lowers Costs for RGBW LED PCB? COB or SMD?
When comparing COB (Chip-on-Board) and SMD (Surface-Mounted Device) manufacturing methods for RGBW LED PCBs, cost efficiency depends on production scale, design complexity, and long-term maintenance. Below is a structured analysis of both technologies:
1. Material Costs
SMD:
- Higher Component Costs: Requires pre-packaged LEDs (with lenses, reflectors, and leads), which increase material expenses.
- PCB Complexity: Multi-layer PCBs may be needed to accommodate SMD footprints, raising board costs.
COB:
- Reduced Material Use: Eliminates LED packages by directly bonding chips to the PCB, cutting costs for plastic/ceramic housing and leads.
- Simpler PCB Design: Often uses single-layer or minimal-layer boards, lowering substrate expenses.
2. Production Efficiency
SMD:
- High Automation: Compatible with pick-and-place machines and reflow ovens, enabling fast, scalable assembly.
- Lower Labor Costs: Minimal manual intervention reduces reliance on skilled operators.
COB:
- Manual Labor Intensity: Chip bonding and wire-bonding steps often require precision handwork, increasing labor costs for small batches.
- Slower Throughput: COB’s sequential processes (e.g., die attaching, encapsulation) limit speed compared to SMD’s parallel assembly.
3. Yield Rates and Waste
SMD:
- Predictable Yields: Mature SMD processes yield fewer defects, reducing scrap rates.
- Repairability: Faulty SMD LEDs can be replaced without discarding the entire PCB.
COB:
- Higher Defect Risk: A single defective chip may render the entire PCB unusable, increasing waste.
- Irreversible Process: Errors in bonding or encapsulation often require PCB replacement, raising costs.
4. Scalability and Volume
SMD:
- Ideal for Mass Production: Automation and high yields make SMD cost-effective at scales >10,000 units/month.
COB:
- Cost-Effective for Small Runs: Avoids SMD’s upfront tooling costs (e.g., stencils, feeders) for low-volume orders.
5. Thermal and Performance Considerations
SMD:
- Heat Dissipation: LED packages include thermal pads, improving heat management but adding cost.
COB:
- Direct Thermal Path: Chips bonded directly to metal-core PCBs (MCPCBs) enable superior cooling, potentially reducing long-term failure rates (lower warranty costs).
6. Long-Term Maintenance
SMD:
- Higher Replacement Costs: Individual LED failure requires component-level repairs.
COB:
- Lower Maintenance: Fewer failure points due to fewer components, but catastrophic failure risk if a chip fails.
How to Select A Reliable RGBW LED Strip Black PCB Manufacturer?
Here’s how to select a reliable RGBW LED strip black PCB manufacturer:
1. Prioritize Certifications and Standards
Look for manufacturers with ISO 9001 (quality management), UL (safety), and RoHS (hazardous substance compliance) certifications. These guarantee adherence to global standards. For LED-specific reliability, ask about LM-80 testing (longevity) and IES files (light performance data).
2. Inspect Their Production Power
- Automated Equipment: Factories using modern SMT machines and reflow ovens ensure precise soldering and fewer errors.
- In-House Testing: Do they own spectrometers, thermal chambers, or aging test equipment? This ensures strips meet brightness, color, and durability specs before shipping.
3. Scrutinize Material Quality
- PCB Substrates: Insist on FR-4 (standard) or MCPCB (metal-core for heat management) with ≥2 oz. copper thickness.
- LED Sources: Confirm they use tier-1 brands and follow strict binning rules (e.g., ±100K color temperature tolerance).
4. Check Customization Flexibility
Choose a manufacturer that offers:
- Custom Lengths/Widths: From compact 5mm strips to wide designs for larger fixtures.
- LED Density Options: 30–240 LEDs per meter to suit your brightness needs.
- Control Compatibility: Ensure strips work with DMX, SPI, Wi-Fi, or your preferred drivers.
5. Demand Rigorous Quality Checks
- Aging Tests: Reliable manufacturers age-test strips for 48–72 hours at 80% power to eliminate early failures.
- Color Calibration: Ask if they use spectrometers to adjust RGBW output (e.g., Δuv <0.005, CRI >90).
6. Compare Pricing (Without Surprises)
Request itemized quotes breaking down material, assembly, and testing costs. Smaller factories may accept lower MOQs (minimum order quantities) for custom designs, saving you upfront costs.
7. Confirm Timelines and Logistics
- Production Speed: Balance urgency with quality—rushed orders might skip critical tests.
- Shipping Safety: Ensure packages are insured, especially for international orders.
8. Evaluate Support and Warranty
- Tech Team: Are they responsive? Do they help troubleshoot design or application issues?
- Warranty: Look for 2–5 year warranties covering LED failure, color drift, and PCB defects.
9. Hear From Other Clients
- Case Studies: Review past projects similar to yours.
- References: Contact previous clients to ask about reliability, communication, and problem-solving speed.
10. Choose Sustainably
- Eco-Friendly Practices: Do they use lead-free solder, recyclable packaging, or energy-efficient processes?
What Is the Difference Between RGB LED and RGBW LED Strip Black PCB?
Here are main differences between RGB LED and RGBW LED strip black PCB:
1. Color Range and Accuracy
RGB LED Strips:
- Use red, green, and blue diodes to mix colors.
- Limitation: Creating pure white light requires blending all three colors, often resulting in a bluish or grayish tint.
- Best For: Decorative lighting where perfect white isn’t critical (e.g., accent lighting, parties).
RGBW LED Strips:
- Add a dedicated white diode to the RGB mix.
- Advantage: Delivers crisp, adjustable white light (warm to cool tones) without color mixing.
- Best For: Tasks needing accurate color rendering (e.g., retail displays, photography studios).
2. Energy Efficiency
RGB LED Strips:
- Consume more power when producing white light (all three diodes active).
- Impact: Higher energy costs over time.
RGBW LED Strips:
- Use the white diode alone for white light, reducing power use by up to 30%.
- Benefit: Lower electricity bills and longer lifespan for LEDs.
3. Brightness and Uniformity
RGB LED Strips:
- White light appears dimmer due to uneven color mixing.
- Risk: “Patchy” lighting in large installations.
RGBW LED Strips:
- Dedicated white diode ensures consistent brightness across the strip.
- Perfect For: Even illumination in offices, galleries, or homes.
4. Design Flexibility
RGB LED Strips:
- Limited to color-changing effects.
- Use Case: Mood lighting, events, or DIY projects.
RGBW LED Strips:
- Offer dual modes: vibrant colors for ambiance and high-quality white for functionality.
- Versatile For: Smart homes, commercial spaces, or multi-use areas.
5. Cost Comparison
RGB LED Strips:
- Lower upfront cost but higher long-term energy expenses.
RGBW LED Strips:
- Slightly pricier initially, but savings on energy and replacement costs offset the difference.
In conclusion, When deciding between RGB and RGBW LED strips, prioritize RGB if your project requires only basic color-changing effects within a tight budget and white light quality isn’t critical. However, opt for RGBW if you need precise color rendering, energy efficiency, or dependable white light—making it ideal for professional settings like retail displays, hospitality spaces, or high-end residential designs where performance and aesthetics matter most.
Tags: RGBW LED PCB, RGBW LED PCB Manufacturer, RGBW LED Strip Black PCB Manufacturer