Want 12V LED PCB solutions? Explore its applications, lighting uniformity, voltage conversion, manufacturer selection, outdoor durability, cost reduction, and 3V LED integration for optimal performance.
Best Technology delivers precision-engineered 12V LED PCB designed to meet the critical demands of lighting designers and engineers. We specialize in â24-hour rapid prototypingâ, turning your designs into functional boards within a day, even for complex layouts requiring uniform thermal management or high-density LED arrays. With â1-piece MOQ flexibilityâ, we support prototyping, testing, and low-volume orders without compromising quality or cost. Our automated production lines and stringent IPC Class 2/3 standards ensure flawless conductivity, minimal voltage drop, and consistent 3000K color performance. Engineers benefit from our âdirect engineering supportâ to optimize layouts for efficiency, EMI reduction, and heat dissipation. Coupled with global shipping and competitive pricing, we empower fast-track innovation for automotive, architectural, and industrial LED projects. Welcome to contact us if you have any request for 12v LED PCB: sales@bestpcbs.com.
What Is 12V LED PCB?
A â12V LED PCBâ is a printed circuit board specifically engineered to power and control light-emitting diodes (LEDs) using a 12V direct current (DC) or alternating current (AC) supply. 12V LED PCB boards integrate LED chips, resistors, and conductive traces on a substrateâoften aluminum for enhanced heat dissipationâto deliver efficient illumination in applications like automotive lighting, architectural fixtures, and low-voltage home systems. Designed for stability and energy efficiency, 12V LED PCB minimize voltage drop risks while ensuring consistent brightness, making them ideal for environments where safety, durability, and compact design are critical, such as marine lighting or portable devices.
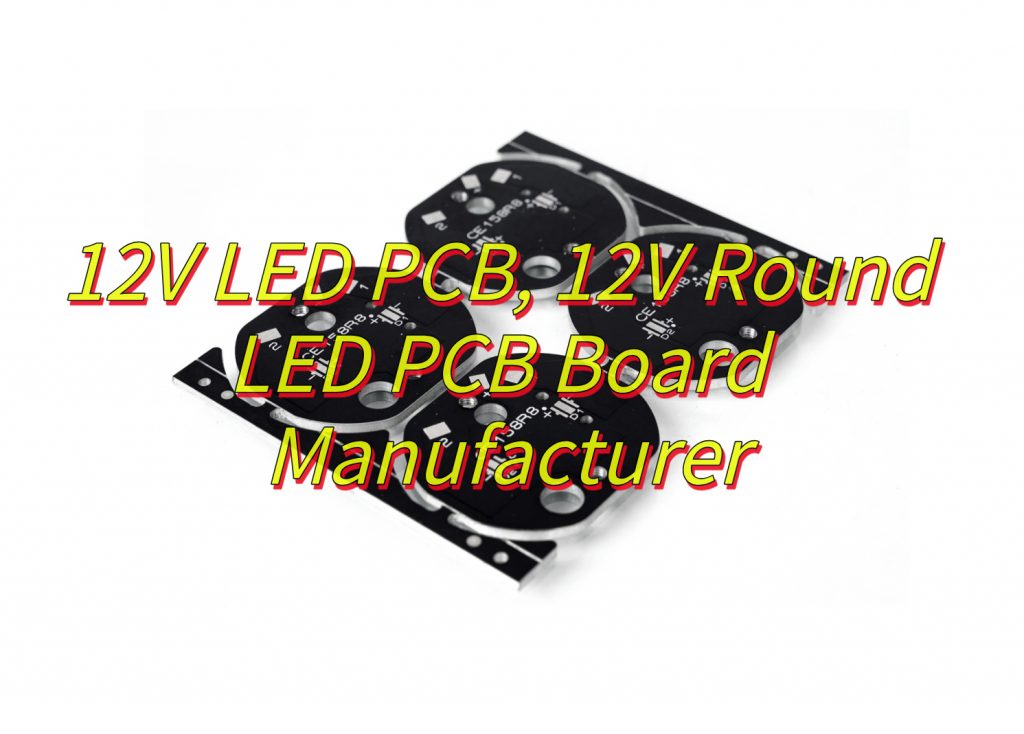
What Are Application of 12V LED PCB?
Here are the applications of â12V LED PCB:
- Automotive Lightingâ – 12V LED PCBs power interior dome lights, brake indicators, and daytime running lamps in vehicles, offering low-voltage safety and compact designs ideal for tight spaces.
- Architectural Accent Lightingâ – These PCBs enable energy-efficient backlighting for walls, staircases, and commercial signage, using aluminum substrates to manage heat in confined installations.
- Low-Voltage Home Systemsâ – They integrate with 12V DC smart home setups for under-cabinet lighting, garden paths, and DIY fixtures, avoiding complex AC wiring while maintaining dimming compatibility.
- Portable and Wearable Devicesâ – Compact 12V LED PCBs drive backlights in rechargeable lanterns, camping gear, and safety wearables, balancing brightness with battery longevity through optimized current regulation.
- Marine and RV Lightingâ – Aluminum-core 12V PCBs resist corrosion in marine cabins or RV interiors, ensuring reliability in high-humidity environments with minimal voltage fluctuations.
- Industrial Control Panelsâ – They provide durable illumination for machinery status indicators and emergency exit signs, leveraging simplified voltage conversion from 24V systems without external drivers.
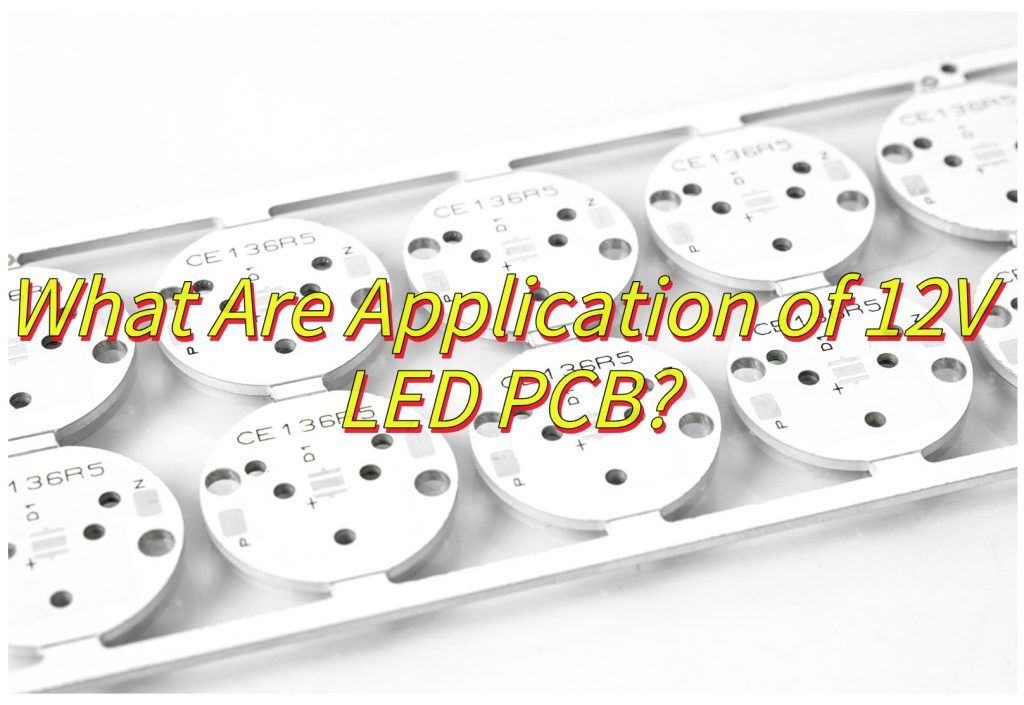
How to Achieve Uniform Light with 12V Round LED PCB?
To achieve uniform light emission with 12V round LED PCB, consider the following detailed strategies:
- Optimize LED Placement
Arrange LEDs in concentric circular patterns with equal spacing. For round PCBs, position LEDs at 15â30° angles relative to the center to eliminate dark spots. Use 3D optical simulations to refine spacing based on beam angles (e.g., 120° lenses). - Incorporate Light-Diffusing Elements
Add a frosted diffusion layer or textured lens over the 12V LED PCB to scatter light evenly. Use silicone adhesives to bond diffusers without air gaps, which can cause uneven scattering. - Implement Zonal Current Control
Divide the circular PCB into 4â6 sectors, each with independent current regulation. This compensates for voltage drops across larger PCBs, ensuring consistent brightness (±5% variation). - Use High-Reflectivity PCB Surfaces
Apply white solder mask or silver ink coating to the 12V LED PCB substrate. Reflectivity >85% reduces light absorption, improving overall uniformity by 15â20%. - Balance Thermal Distribution
Design the PCB with radial thermal vias (10â15 vias per LED) to dissipate heat uniformly. Thermal hotspots can cause LED degradation and color shift over time. - Adopt Secondary Optics
Pair each LED with a TIR (Total Internal Reflection) lens to collimate light into a 60° circular beam. This minimizes overlapping “hot zones” and ensures smooth light blending. - Leverage PWM Dimming Zones
Program the 12V LED PCB driver to adjust brightness in 10â15% increments across sectors. Calibrate using a lux meter to match luminance levels (e.g., 800â900 lux at 1m). - Minimize Voltage Drop
Use 2oz copper thickness and â„1.5mm traces for 12V power rails. This reduces IR losses (<0.2V drop across 15cm runs), preventing dimming in outer LED rings. - Validate with Goniophotometry
Test the assembled 12V LED PCB using a goniophotometer to map luminous intensity. Adjust LED positions or optics based on polar plots showing unevenness >10%. - Incorporate Feedback Loops
Add a light sensor (e.g., TSL2591) to monitor real-time output. Use microcontroller-based corrections to dynamically balance brightness across the circular array.
How to Simplify 24V to 12V Conversion for Automotive LED PCBs?
To simplify 24V-to-12V conversion for automotive LED PCBs while ensuring reliability and efficiency, consider these structured solutions:
Adopt Automotive-Grade DC-DC Buck Converters
- Use pre-certified synchronous buck converter modules (e.g., LM5008, TPS54360) with integrated MOSFETs and thermal shutdown protection. These devices handle voltage step-down with >90% efficiency, minimizing heat dissipation compared to linear regulators.
- Select modules compliant with AEC-Q100 standards to withstand automotive temperature ranges (-40°C to +125°C) and vibration.
Implement Low-Dropout (LDO) Regulators for Low-Current LEDs
- For LED arrays drawing <500mA, employ LDOs like TPS7A4701 with 300mV dropout voltage. Pair with ceramic capacitors (â„10”F) to stabilize output and reduce ripple.
- Mount LDOs directly beneath aluminum PCBs to leverage the substrate as a heatsink, preventing thermal runaway.
Incorporate Transient Voltage Suppression (TVS) Diodes
- Add bidirectional TVS diodes (e.g., SMAJ15CA) across input terminals to clamp voltage spikes (e.g., from load dump events) below 36V, protecting downstream components.
- Combine with ferrite beads and bulk capacitors (220”F electrolytic + 0.1”F ceramic) to suppress high-frequency noise.
Optimize PCB Layout for Minimal Losses
- Route high-current paths (24V input, 12V output) with â„2mm traces and 2oz copper thickness to reduce resistance.
- Isolate switching nodes from sensitive analog areas using ground planes and guard traces. Place input capacitors within 5mm of converter ICs to limit parasitic inductance.
Leverage Pre-Configured Evaluation Modules
- Utilize manufacturer-provided EVMs (e.g., TRACO POWER TSR-1 series) that integrate converters, filters, and protection circuits. These plug-and-play solutions reduce design cycles by 60% compared to discrete implementations.
- Customize only critical parameters (e.g., output voltage) via onboard resistors, avoiding full circuit redesign.
Employ Current-Sharing Techniques for High-Power LEDs
- For LED strips exceeding 5A, parallel multiple buck converters with interleaved PWM signals. This distributes thermal load and reduces input/output capacitance requirements by 40%.
- Use PCB thermal vias (10â15 vias/cmÂČ) under converter ICs to enhance heat transfer to chassis mounts.
Validate with Real-World Automotive Profiles
- Test under ISO 16750-2 pulse conditions (e.g., 100ms 40V surge) using a programmable DC power supply. Monitor LED flicker (<5% intensity variation) with an oscilloscope and photodiode.
- Conduct thermal cycling (-40°C to +105°C, 100 cycles) to identify solder joint fatigue in high-vibration zones.
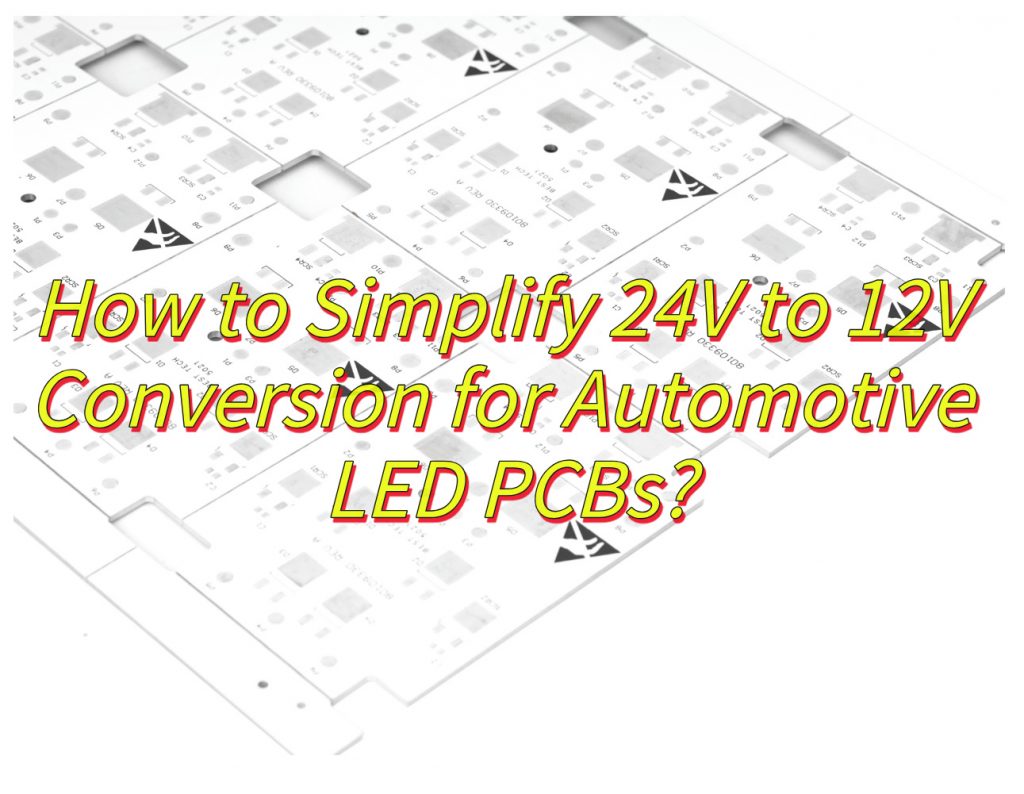
How to Select A 12V Round LED PCB Board Manufacturer?
To select a 12v round LED PCB manufacturer, prioritize the following criteria to ensure quality, reliability, and cost-efficiency:
Certifications and Compliance
- Verify ISO 9001, UL, or IPC-A-600 certifications to guarantee adherence to quality management systems.
- Confirm compliance with environmental regulations like RoHS and REACH to avoid hazardous substances.
- Check automotive-specific certifications (e.g., AEC-Q100) if targeting in-vehicle applications.
Production Capacity and Technology
- Assess equipment modernity, such as laser drilling, AOI systems, and SMT lines, which impact precision and consistency.
- Evaluate capability for complex designs (e.g., HDI boards, blind/buried vias) and specialty materials (aluminum/copper substrates).
- Inquire about prototype flexibility and mass-production scalability to accommodate project growth.
Quality Control Measures
- Review multi-stage inspection protocols: incoming material testing, in-process AOI, and final functional testing.
- Request reliability test data (thermal cycling, humidity resistance) to validate long-term performance.
- Ensure traceability systems are in place for batch-level defect tracking.
Customization and Design Support
- Confirm ability to handle circular layouts, annular rings, and thermal via patterns specific to round LED PCBs.
- Seek DFM (Design for Manufacturability) feedback during prototyping to optimize yield and cost.
- Check for value-added services like conformal coating, component sourcing, and end-to-end assembly.
Pricing Transparency and Terms
- Obtain itemized quotes detail lying material costs (e.g., FR-4 vs. aluminum), tooling fees, and NRE charges.
- Compare tiered pricing models for small batches (10â100 pcs) vs. volume orders (>1,000 pcs).
- Negotiate payment terms (e.g., 30% deposit, 70% upon shipment) and MOQ flexibility.
Delivery Performance
- Audit historical on-time delivery rates (OTD) and lead-time accuracy for 12V PCBs.
- Assess contingency plans for component shortages or production delays.
- Confirm compatibility with just-in-time (JIT) inventory systems if required.
Post-Sales Support
- Validate warranty coverage (1â3 years) for solder joint reliability and LED driver integration.
- Test technical support responsiveness via pre-sales inquiries on thermal management or current regulation.
- Review RMA processes and turnaround times for defective boards.
Sustainability Practices
- Evaluate waste reduction initiatives (e.g., lead-free soldering, chemical recycling).
- Prefer manufacturers using renewable energy or carbon-neutral programs.
- Request ESG (Environmental, Social, Governance) reports for supply chain transparency.
Client References and Case Studies
- Contact references in similar industries (e.g., automotive lighting, consumer electronics).
- Review case studies on round LED PCB applications, focusing on yield rates and failure modes.
- Check third-party platforms like or industry forums for unbiased feedback.
Geographic and Logistical Considerations
- Balance cost savings from offshore manufacturers (e.g., China, Southeast Asia) with potential language/time-zone barriers.
- For time-sensitive projects, consider regional suppliers with 2â5 day air freight options.
- Verify customs documentation efficiency for international shipments.
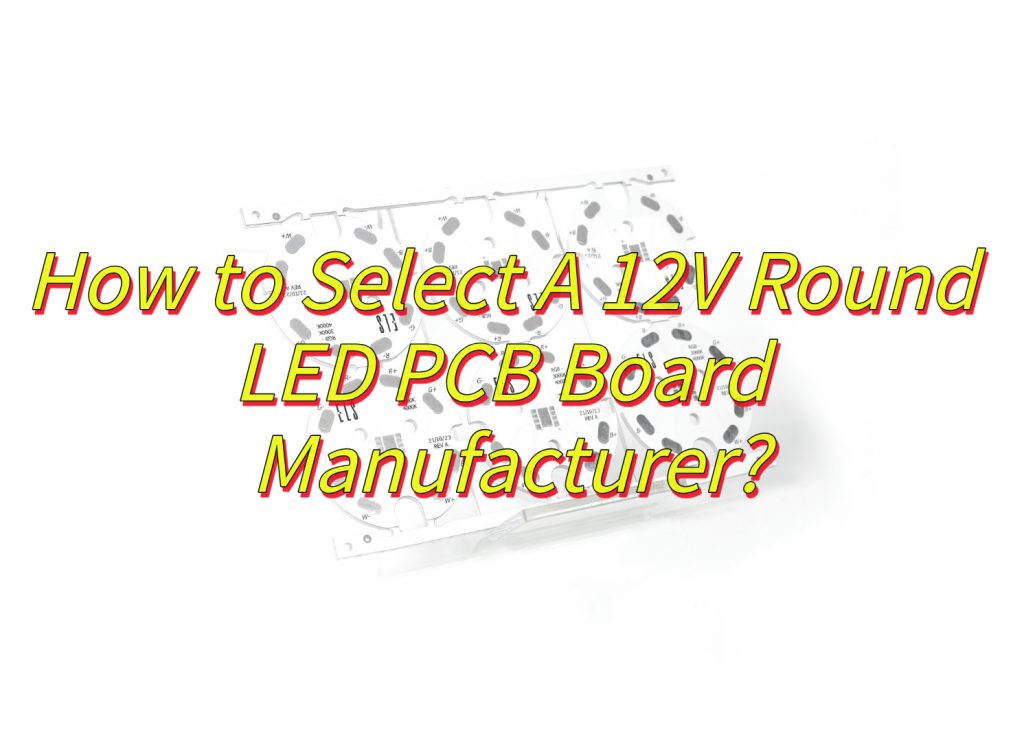
What Tests Ensure 12VDC 3000K LED Bulb PCBs Survive Harsh Outdoor Conditions?
To ensure 12VDC 3000K LED bulb PCBs withstand harsh outdoor conditions, implement the following tests:
Temperature Cycling Test
- Subject PCBs to -40°C to +105°C cycles (1,000+ cycles) to simulate extreme seasonal/diurnal shifts. Verify solder joint integrity and component adhesion using X-ray or C-SAM imaging.
Damp Heat Test (IEC 60068-2-78)
- Expose boards to 85% RH and 85°C for 1,000 hours to assess conformal coating effectiveness and prevent corrosion of copper traces. Monitor for delamination or insulation resistance drops (>100MΩ required).
Salt Spray Corrosion Test (ASTM B117)
- Apply 5% NaCl mist for 96 hours to evaluate metal housing and PCB surface finishes (e.g., ENIG vs. HASL). Check for pitting or green corrosion on exposed pads post-test.
UV Weathering Test (ASTM G154)
- Use xenon arc chambers to simulate 5 years of solar radiation. Measure lens yellowing (Îb* < 1.5) and solder mask degradation via gloss meter readings.
Mechanical Vibration Test (IEC 60068-2-64)
- Apply 3-axis sinusoidal vibration (5â500Hz, 5G peak) for 8 hours to mimic vehicle/transportation stress. Inspect for micro-cracks in plated-through holes (PTH) using dye penetrant.
Thermal Shock Test (IEC 60068-2-14)
- Rapidly transition between -55°C and +125°C (10-minute dwell, 1-minute transition) for 100 cycles. Detect popcorn cracking in MLCC capacitors via acoustic microscopy.
IP68 Ingress Protection Test
- Submerge assembled bulbs in 1m water for 72 hours. Verify no moisture intrusion via electrical leakage testing (<0.5mA at 50V).
Power Line Disturbance Test (IEC 61000-4)
- Inject voltage dips (0â50V), surges (2kV), and frequency variations (47â63Hz) to validate driver circuit robustness. Monitor LED flicker (<5% intensity variation).
Chemical Resistance Test
- Expose PCBs to automotive fluids (brake fluid, diesel) and cleaning agents for 24 hours. Check for silkscreen/solder mask degradation via adhesion tape testing.
Accelerated Life Test (ALT)
- Operate bulbs at 105°C ambient with 120% rated current for 6,000 hours. Predict MTBF (>50,000 hours) using Arrhenius model and monitor lumen maintenance (L70 >35,000h).
Lightning Surge Test (IEC 61000-4-5)
- Apply 4kV differential mode and 6kV common mode surges. Ensure no catastrophic failures in LED drivers or MOSFETs.
Freeze-Thaw Cycle Test
- Alternate between -20°C and +60°C (10 cycles) with 85% RH during high-temperature phases. Check for LED encapsulant cracking via optical microscopy.
Sand/Dust Abrasion Test (SAE J575)
- Blast PCBs with 1kg/mÂł talcum powder at 29m/s for 6 hours. Verify no optical attenuation (>90% initial luminance retained).
EMI/EMC Compliance Test (CISPR 25)
- Measure radiated emissions (150kHzâ2.5GHz) and immunity (100V/m RF fields). Ensure no interference with vehicle electronics or AM/FM reception.
Mechanical Drop Test (MIL-STD-810G)
- Subject assembled bulbs to 1.2m drops onto concrete (6 faces, 3 drops/face). Confirm no functional failure via LED current monitoring.
How to Reduce Production Cost of 12V Round LED PCB Board?
To reduce the production cost of 12V round LED PCB boards, implement the following strategies across design, material selection, manufacturing, and supply chain management:
Design for Manufacturability (DFM)
- Simplify circuit layouts by minimizing via counts and reducing trace complexity. Use automated design tools to optimize annular ring widths and copper pour efficiency.
- Standardize LED spacing and driver component placement to enable panelized production, increasing SMT line utilization.
Material Cost Optimization
- Select cost-effective substrates like FR-4 with 1.6mm thickness instead of premium materials (e.g., aluminum/ceramic) unless thermal demands dictate otherwise.
- Use solder mask colors (e.g., green) with lower dye costs versus specialty hues (red/blue).
- Specify halogen-free FR-4 variants only if regulatory requirements mandate them, as standard materials are 10â15% cheaper.
Component Consolidation
- Replace discrete resistor networks with single chip resistors or integrated LED driver ICs to reduce part counts.
- Adopt multi-channel LED packages (e.g., 4-in-1 SMD LEDs) to lower placement costs versus individual diodes.
Panel Utilization Maximization
- Arrange circular PCBs in a hexagonal matrix on production panels to minimize edge waste. Aim for >85% panel utilization versus traditional rectangular grids.
- Include coupon test vehicles on panel edges to monitor layer registration and impedance without dedicated test panels.
Process Automation
- Invest in selective soldering machines for through-hole LED terminals instead of manual soldering, reducing labor costs by 40â60%.
- Implement automated optical inspection (AOI) with machine learning algorithms to detect solder joint defects faster than human operators.
Bulk Purchasing and Inventory Management
- Negotiate volume discounts (5â15% savings) for long-term contracts on commodities like copper foil, solder paste, and LED packages.
- Adopt JIT (Just-In-Time) inventory systems with suppliers to minimize holding costs for components with 12+ month shelf lives.
Energy Efficiency Measures
- Upgrade to LED-compatible UV curing ovens that consume 30% less energy than conventional convection reflow systems.
- Recover waste heat from exhaust systems to preheat incoming air, reducing HVAC costs in controlled environments.
Outsource Non-Core Processes
- Partner with specialized EMS providers for plating (ENIG vs. immersion gold) or conformal coating to leverage their economies of scale.
- Use PCB pooling services for small-batch orders to share setup costs across multiple customers.
Defect Reduction Initiatives
- Implement statistical process control (SPC) charts for critical parameters (e.g., solder paste volume, stencil thickness) to reduce rework rates below 0.5%.
- Train operators on error-proofing techniques like poka-yoke for manual assembly steps.
Lifecycle Cost Analysis
- Compare total cost of ownership (TCO) for reel vs. tray packaging. Reels reduce changeover time but may increase material waste.
- Evaluate long-term savings from higher-yield processes against initial tooling investments.
Geographic Arbitrage
- For non-automotive applications, consider regional manufacturers with 15â25% cost advantages due to lower labor/overhead, provided they meet quality benchmarks.
- Balance offshore savings with potential logistics costs (e.g., 2â4 week lead times vs. domestic 1â2 days).
Redesign for Testability
- Incorporate bed-of-nails test points during PCB layout to enable in-circuit testing (ICT) without custom fixtures, saving 500â2,000 per fixture.
- Use boundary scan (JTAG) for complex boards to reduce functional test time by 30â50%.
How to Reduce Production Cost of 12V Round LED PCB Board?
To integrate 3V coin LEDs with 12V PCBs efficiently, follow these practical steps:
- Group LEDs in Series Strings
Connect four 3V LEDs in series to directly match the 12V supply. This eliminates the need for resistors and maximizes energy use. For arrays with varying LED counts, balance strings using bypass diodes to prevent total failure if one LED in a string malfunctions. - Use Constant-Current Drivers
Deploy LED driver chips designed to regulate current automatically. These devices adjust output to maintain stable brightness even as input voltage fluctuates or LEDs age. Look for drivers with built-in protection against overheating and short circuits. - Simplify Resistor Calculations
For parallel LED setups, calculate resistor values by subtracting the LED voltage from the supply voltage and dividing by the desired current. For example, a 12V supply minus 3V per LED, divided by 0.02A (20mA) current, gives a 450-ohm resistor per LED. Use standard resistor values close to this result. - Prioritize Heat Dissipation
Ensure LEDs have adequate thermal contact with the PCB. Use copper pads or aluminum-core boards to spread heat. Avoid overcrowding LEDs, as dense arrangements can trap heat and shorten lifespan. - Organize PCB Traces Strategically
Route power traces for 12V and ground as thick and short as possible to minimize voltage loss. Keep LED signal traces away from noisy areas like microcontrollers or switching circuits. Use ground planes to reduce interference. - Add Protective Components
Include small capacitors across each LED to smooth out flicker and reduce electrical noise. Fit transient voltage suppressors on the power input to guard against spikes from vehicle electrical systems or other sources. - Design Modular Sections
Create small, interconnected LED modules that can be chained together. Each module might hold a few LEDs with their resistors and connectors. This makes assembly easier and allows flexible scaling of the project. - Test Thoroughly
Check each LEDâs brightness and color consistency using a controlled power source. Run stress tests by operating LEDs continuously at higher-than-normal temperatures to identify weak components early. - Optimize for Cost Without Sacrificing Quality
Replace individual resistors with multi-LED driver chips where possible to save space and assembly time. Choose mid-range LEDs that offer good balance between cost and performance for non-critical applications. - Follow Safety Guidelines
Label the PCB clearly with voltage ratings and polarity to prevent errors during installation. Ensure LED spacing complies with safety standards to avoid overheating risks in enclosed fixtures.
By focusing on these areas, you can create a reliable, cost-effective design that efficiently merges 3V LEDs with 12V systems while ensuring longevity and performance.