Looking for LED square PCB? This guide covers definitions, cost-saving strategies, manufacturer selection, and expedited services for efficient development.
Best Technology delivers LED Square PCB prototypes in 24 hours without compromising quality. Our advanced LDI (Laser Direct Imaging) systems and automated AOI (Automated Optical Inspection) ensure precision for complex layoutsâincluding multi-layer designs (up to 8L) and tight pad spacing (â€0.15mm). With pre-stocked aluminum substrates (1.6â3.0W/m·K thermal grades) and 24/7 production lines, we eliminate delays in material sourcing and fabrication. Real-time DFM feedback resolves design issues within 4 hours, while parallel thermal/vibration testing accelerates validation. Need same-day quotes or global shipping? Our expedited services include DHL/FedEx Priority with pre-cleared customs docs. Trust ISO 9001-certified processes, 98% on-time delivery rates, and dedicated engineering support for automotive, medical, or industrial LED projects. âStart your project today: sales@bestpcbs.com.
What Is A LED Square PCB?
A âLED Square PCBâ is a printed circuit board designed in a square-shaped configuration, specifically optimized to integrate and power light-emitting diodes (LEDs) efficiently. These boards feature a geometrically balanced layout that simplifies component placement, ensuring uniform thermal dissipation and electrical connectivity across the surface. The square form factor allows for modular scalability, enabling seamless alignment when multiple units are combined in arrays or grids. Constructed with materials such as aluminum substrates or FR4 laminates, LED Square PCBs prioritize heat management and mechanical stability, essential for maintaining LED performance and longevity. Traces and pads are precision-engineered to minimize impedance mismatches and voltage drops, while solder mask layers protect circuitry from environmental factors. Their standardized dimensions and symmetry make them adaptable to diverse mounting systems, balancing design simplicity with functional reliability.
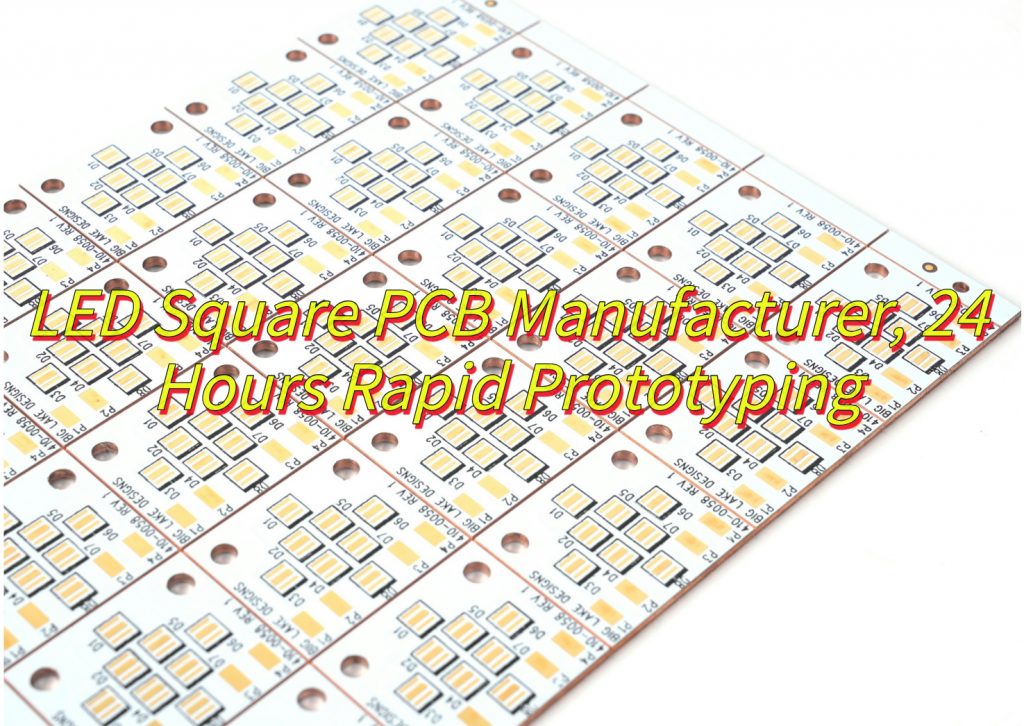
What Are Application of Square LED PCB?
Applications of square LED PCB:
- Smart Home Lighting Systems – LED Square PCBs power compact, energy-efficient fixtures for recessed ceilings and wall panels, offering seamless integration and low heat emission.
- Automotive Dashboard Displays – Their rigid structure ensures precise alignment of LED indicators and touchscreens in vehicles, withstanding vibrations and temperature fluctuations.
- Wearable Tech Gadgets – Thin, lightweight LED Square PCBs enable vibrant displays in smartwatches and fitness trackers, balancing performance and battery life.
- Retail Signage & Digital Menus – High-density LED arrays on square PCBs create bright, eye-catching visuals for storefronts and quick-service restaurants, even in daylight.
- UV-C Disinfection Devices – Robust LED Square PCBs support high-power UV LEDs for germicidal equipment used in hospitals and public spaces, ensuring reliable thermal dissipation.
- Horticultural Growth Lamps – Modular LED Square PCBs customize light spectra for indoor farming, optimizing plant growth cycles while minimizing energy use.
- EV Battery Status Indicators – Compact designs fit seamlessly into electric vehicle charge ports, providing real-time feedback without compromising IP67 waterproof ratings.
- Aerospace Cabin Lighting – Flame-retardant materials and precise soldering ensure LED Square PCBs meet stringent safety standards for aircraft interior lighting systems.
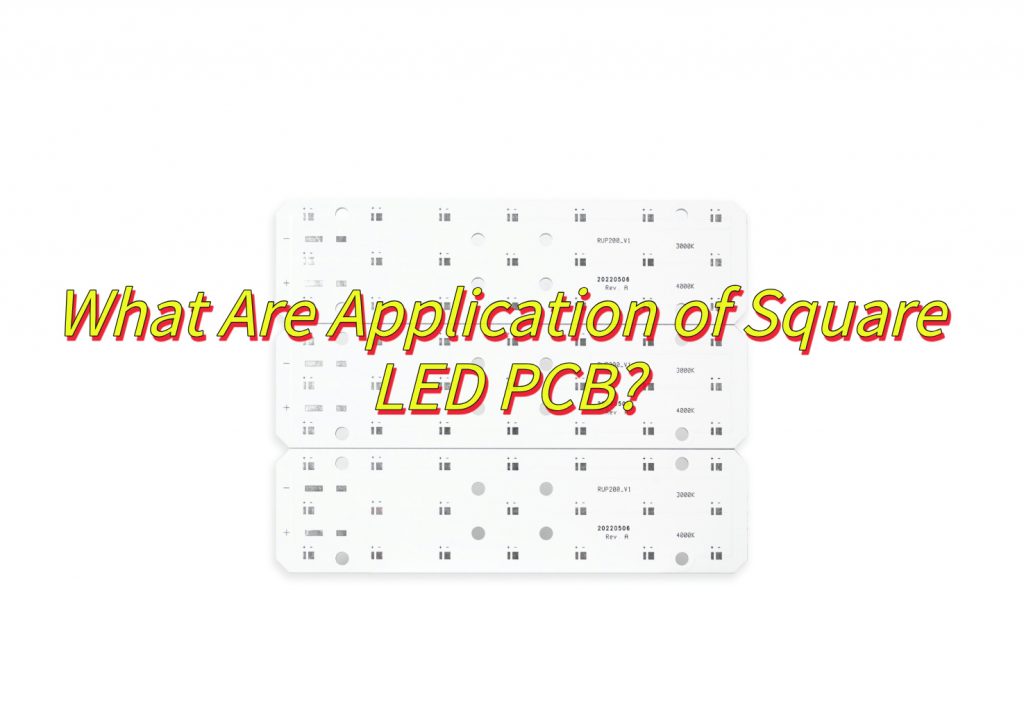
What Are Difference Between LED Square PCBs and LED Round PCBs?
Differences between LED Square and Round PCBâ:
Shape-Driven Layout and Compatibilityâ
- LED Square PCBs feature symmetrical geometry, enabling modular alignment in grid-based lighting systems or video walls. In contrast, Round PCBs suit curved or rotational designs, such as circular fixtures or rotating displays, where angular rigidity is less critical.
Thermal Management Efficiencyâ
- The square design optimizes heat distribution through uniform copper foil patterns and aluminum substrates (â„1.5W/m·K), reducing localized hotspots. Round PCBs may face uneven thermal gradients due to radial trace layouts, requiring additional heat sinks.
Mechanical Stability and Assemblyâ
- LED Square PCBs provide enhanced structural integrity for surface-mounted components, minimizing solder joint stress during thermal expansion. Round PCBs, while compact, often require specialized mounting brackets to prevent rotational displacement in vibration-prone environments.
Manufacturing Precision and Costâ
- Square PCBs align with standardized panelization processes, reducing material waste and enabling high-volume production. Round PCBs involve more complex routing and cutting steps, increasing fabrication costs by 15-20%.
Application-Specific Light Distributionâ
- LED Square PCBs support edge-to-edge illumination uniformity in panel lights or task lighting, avoiding dark zones through centralized LED placement. Round PCBs prioritize radial light dispersion for omnidirectional fixtures but may require diffusers to mitigate annular shadows.
Material Utilizationâ
- Aluminum-based LED Square PCBs dominate industrial lighting due to their balanced thermal conductivity and cost efficiency. Round PCBs often use hybrid materials (e.g., FR4 with metal cores) to compensate for shape-related thermal limitations.
What Is LED Square PCB Rapid Prototyping Service?
LED Square PCB rapid prototyping accelerates the development of compact, thermally efficient lighting systems by enabling quick iteration of square-form circuit designs. This service focuses on transforming digital layouts into functional prototypes within 24â72 hours, emphasizing precise alignment with square geometries for applications like modular lighting grids or display panels. Engineers leverage material options such as aluminum substrates (1.5â3.0W/m·K) to validate heat dissipation and luminous uniformity, while multi-layer stacking tests ensure compatibility with mixed-signal LED driver circuits. Prototypes undergo thermal cycling and vibration simulations to replicate real-world conditions, from automotive lighting to industrial controls. By streamlining design validation and low-volume production, the service bridges concept development and scalable manufacturing for LED Square PCB-based solutions.
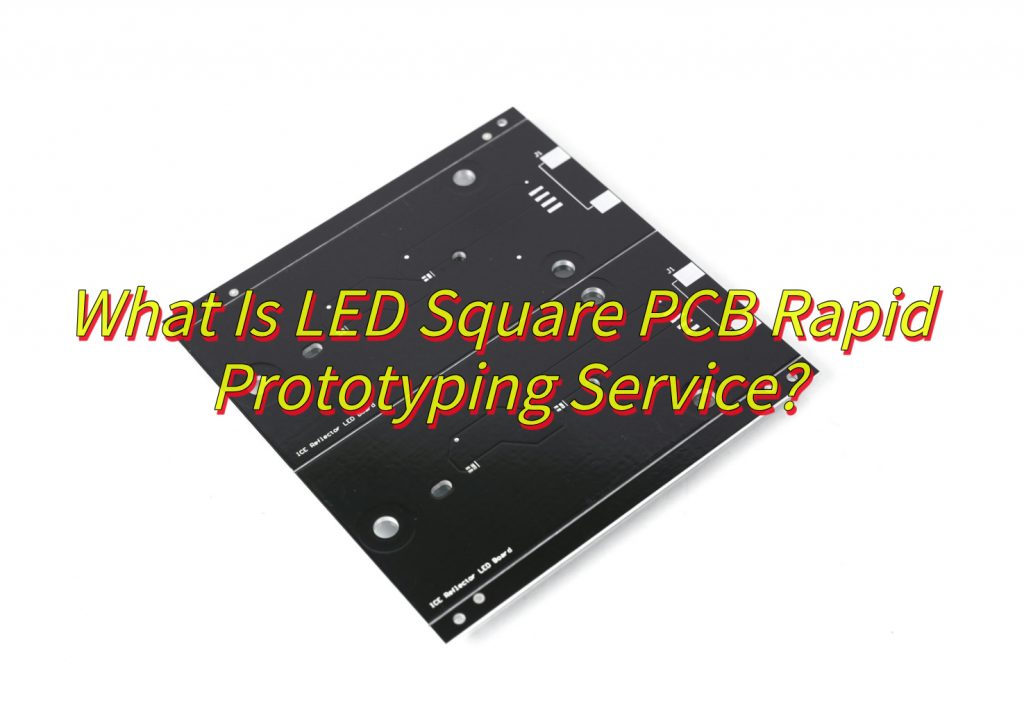
How to Streamline Square LED PCB Prototyping Processes?
Strategies to Streamline square LED PCB Prototyping Processesâ:
- Adopt Modular Design Frameworks – Break complex LED Square PCB layouts into reusable modules (e.g., LED arrays, driver circuits). Standardized footprints reduce design iterations by 40% and minimize errors during prototyping.
- Use Real-Time Design Rule Checks (DRC) – Integrate automated DRC tools to flag issues like trace/space violations or solder mask errors instantly. This prevents costly reworks later and accelerates revisions by 50%.
- Leverage Rapid Prototyping Services – Partner with manufacturers offering 24â72 hour turnaround for LED Square PCB prototypes. Services like âPCB Poolâ or âInstant Quoteâ tools streamline ordering, with options to include stencils and assembly.
- Implement Parallel Testing – Test multiple LED Square PCB prototypes simultaneously using automated optical inspection (AOI) and in-circuit testing (ICT). This cuts validation time by 60% for thermal performance and light uniformity checks.
- Optimize Panelization Strategies – Arrange multiple LED Square PCB designs on a single panel using V-score or tab-routing. This maximizes yield, reduces per-unit costs, and minimizes material waste by 30%.
- Centralize Documentation– Use cloud platforms to store Gerber files, BOMs, and test reports. Version control ensures teams access the latest revisions, avoiding mismatches during assembly and reducing errors by 25%.
- Collaborate Early with Suppliers – Share LED Square PCB design files with manufacturers during the quoting phase for free DFM feedback. This identifies production bottlenecks before tooling, saving 500â2,000 per re-spin.
- Automate Post-Production Validation – Use AI-driven tools to analyze LED brightness, color consistency, and thermal performance across prototypes. This accelerates quality control by 70% compared to manual inspection.
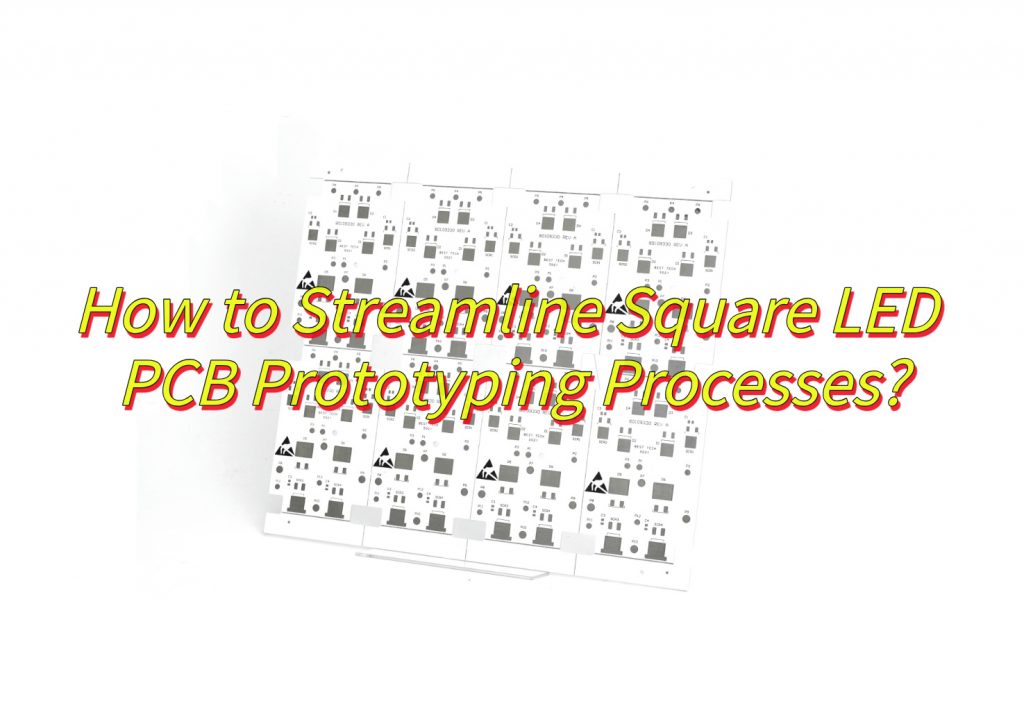
How to Choose A LED Square PCB Rapid Prototyping Manufacturer?
Here is a guide to selecting a LED Square PCB Rapid Prototyping Manufacturerâ:
Certified Material Compatibilityâ
- Verify manufacturers use aluminum substrates (1.5â3.0W/m·K thermal conductivity) and high-reflectivity solder masks optimized for LED Square PCB designs to prevent heat accumulation and light scattering. Confirm RoHS and ISO 9001 certifications for material traceability.
Guaranteed Rapid Turnaroundâ
- Prioritize suppliers offering 24â72-hour prototyping cycles with documented proof of on-time delivery for LED Square PCB projects involving dense arrays (e.g., â€0.2mm pad spacing). Ensure they utilize laser direct imaging (LDI) and automated optical inspection (AOI) for faster validation.
Multi-Layer Technical Expertiseâ
- Select manufacturers capable of handling 12+ layer LED Square PCBs with â€3/3mil line spacing and 0.1mm drilling accuracy, essential for high-power COB (Chip-on-Board) lighting systems. Request sample reports on impedance control and via filling quality.
Integrated Prototyping-to-Production Workflowâ
- Choose partners with panelization-optimized workflows that reduce per-unit costs by 15â20% while maintaining LED Square PCB dimensional tolerances (±0.05mm). Confirm scalability from 5â10 prototype panels to 1k+ volume batches.
Thermal Reliability Testingâ
- Demand thermal cycling reports (-40°C to +125°C) and vibration resistance data specifically for LED Square PCB prototypes, particularly for automotive or industrial applications. Validate compliance with IPC-6012 Class 3 standards during prototyping.
Component Procurement Networksâ
- Prefer suppliers with pre-vetted LED driver and COB array vendors to eliminate delays caused by third-party component shortages during prototyping.
Real-Time Design Feedback Systemsâ
- Require cloud-based collaboration platforms to resolve LED Square PCB tolerance conflicts (e.g., solder mask alignment, pad spacing) within 4â6-hour response windows.
Transparent Cost Structuresâ
- Choose manufacturers providing dynamic pricing models that account for LED Square PCB variables: layer count (4â16L), ENIG/OSP surface finishes, and custom solder mask colors.
Failure Prevention Databasesâ
- Ensure access to historical defect logs addressing LED Square PCB-specific issues like copper peel-off under thermal stress or solder joint fractures.
Concurrent Certification Supportâ
- Partner with providers offering EMI/EMC pre-testing during prototyping phases to avoid redesign costs for medical or aerospace LED applications.
How to Reduce Cost of LED Square PCBs Rapid Prototyping?
Effective strategies to reduce costs in LED Square PCB Rapid Prototypingâ:
Material Standardizationâ
- Use standardized aluminum substrates (e.g., 1.6mm thickness, 2.0W/m·K thermal conductivity) and pre-approved solder mask colors to avoid custom material premiums for LED Square PCBs. Confirm supplier inventories to eliminate rush-order fees.
Design Simplificationâ
- Optimize LED Square PCB layouts by reducing layer counts (e.g., 4-6 layers instead of 8+ where feasible) and widening trace widths (â„0.15mm) to lower fabrication complexity and defect rates.
Panelization Efficiencyâ
- Group multiple LED Square PCB prototypes onto shared production panels, cutting per-unit costs by 20â30% while maintaining ±0.1mm dimensional tolerances.
Early DFM Collaborationâ
- Conduct Design-for-Manufacturability (DFM) reviews with suppliers during schematic design to resolve issues like uneven copper distribution or inadequate thermal reliefs, avoiding 2â3 re-spin cycles.
Batched Prototypingâ
- Consolidate iterative LED Square PCB revisions into single batches (e.g., 5â10 design variants per order) to leverage bulk pricing on materials and machine setup fees.
Alternative Surface Finishesâ
- Substitute costlier ENIG (Electroless Nickel Immersion Gold) with HASL (Hot Air Solder Leveling) for non-critical LED Square PCB prototypes, reducing surface treatment costs by 40â50%.
Automated Testing Optimizationâ
- Replace full-board AOI (Automated Optical Inspection) with targeted testing zones for LED clusters and power traces, trimming quality control expenses by 15â25%.
Supplier Volume Agreementsâ
- Negotiate tiered pricing with manufacturers based on projected annual LED Square PCB prototyping volumes (e.g., 500+ panels/year), securing 10â15% discounts.
Reusable Fixturesâ
- Develop modular test jigs and alignment tools compatible with multiple LED Square PCB iterations, avoiding custom fixture costs for each prototype.
Simulation-Driven Iterationâ
- Leverage thermal/EMI simulation software to validate LED Square PCB designs virtually, reducing physical prototype iterations by 30â40%.
Waste Reduction Programsâ
- Partner with suppliers offering scrap buyback for unused aluminum substrates or copper clads from LED Square PCB prototyping runs, recovering 5â10% material costs.
Localized Sourcingâ
- Source LED drivers, connectors, and heat sinks from regional vendors to minimize import tariffs and logistics delays impacting prototype budgets.
Open-Tooling Partnershipsâ
- Work with manufacturers using “soft tooling” (laser drilling, LDI) for LED Square PCB prototypes instead of expensive hard tooling, eliminating $500â$1,000 mold charges.
What Are the Expedited Service Options for LED Square PCB Rapid Prototyping?
24-Hour Turnaround for LED Square PCB Prototypes
- Partner with manufacturers offering 24-hour fabrication for LED Square PCB prototypes using automated production lines. This service prioritizes your design files, bypassing standard queues to meet urgent deadlines.
Same-Day Shipping for LED Square PCB Orders
- Select suppliers with global logistics networks to ensure LED Square PCB prototypes ship within hours of completion. Expedited shipping options like DHL Express or FedEx Priority reduce delivery time by 50â70%.
Priority Design Rule Checks (DRC) for LED Square PCB
- Choose manufacturers with real-time DRC tools that flag errors like trace/space violations or solder mask misalignments in minutes. This accelerates revisions and prevents delays during LED Square PCB prototyping.
Instant Quote Systems for LED Square PCB Projects
- Use online platforms that generate pricing for LED Square PCB prototypes in seconds. Automated systems eliminate back-and-forth negotiations, allowing immediate order confirmation for time-sensitive projects.
Dedicated Account Managers for LED Square PCB Urgency
- Work with suppliers assigning a single point of contact to manage LED Square PCB orders. This reduces communication lag and ensures issues like material shortages or design queries resolve within hours.
Express Assembly for LED Square PCB Prototypes
- Choose turnkey services combining PCB fabrication, stencil cutting, and SMT assembly in one streamlined process. This cuts lead times by 30â40% compared to outsourcing stages separately.
Weekend Production for LED Square PCB Deadlines
- Select factories operating 24/7 to avoid delays from weekend shutdowns. Continuous production ensures LED Square PCB prototypes fabricate and ship even during non-business hours.
Guaranteed On-Time Delivery for LED Square PCB Orders
- Choose manufacturers offering refunds for missed deadlines. This incentive aligns priorities, ensuring your LED Square PCB prototypes arrive when needed without cost overruns.
In conclusion, that’s all about LED square PCB’s definitions, cost-saving strategies, manufacturer selection, and expedited services for efficient development. Welcome to leave a message below this blog if you have any issues about LED square PCB.