Seeking a certified LED PCB exporter? This overview examines customization processes, cost optimization, vertical farming adaptations, compliance protocols, and emerging Chinese technologies.
At Best Technology, we deliver unmatched value as your LED PCB exporter by offering rapid turnaround times, transparent pricing, and rock-solid quality—all while handling everything from niche small-batch orders to large-scale production runs. Our expertise spans a wide array of metal-core PCBs, including aluminum, copper, and advanced composite substrates, tailored for high-performance LED applications like horticultural lighting, industrial fixtures, and beyond. With agile customization capabilities, strict quality certifications, and a proven track record of on-time delivery, we ensure your projects shine brighter, faster, and within budget. Ready to experience reliability, flexibility, and precision? Reach out to Best Technology today and let’s power up your next innovation! Welcome to contact us if you have any request for LED PCB: sales@bestpcbs.com.
What Is LED PCB Exporter?
A LED PCB exporter specializes in designing, manufacturing, and distributing printed circuit boards optimized for LED applications, partnering with LED PCB factories and companies to deliver solutions for lighting systems, horticultural setups, and industrial controls. These exporters typically utilize advanced materials like aluminum substrates and integrate components such as drivers and thermal management systems to ensure reliability across diverse operating conditions. By adhering to standardized production workflows and maintaining certifications for safety and efficiency, they cater to global markets requiring precise electrical layouts and durable PCB configurations. The sector’s technical focus includes spectral tuning for agricultural lighting and compatibility with modular assembly processes.
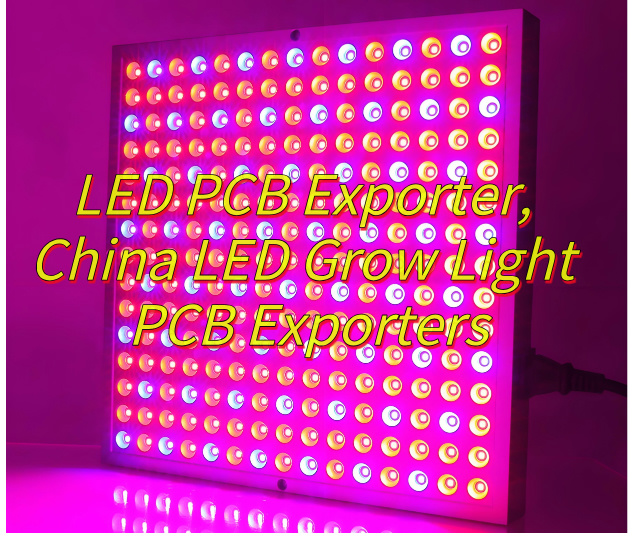
How Do Leading LED PCB Exporters Handle Customization Requests?
This is how the leading LED PCB exporter handles custom requests:
- Modular Design Platforms: Leading LED PCB exporters collaborate with LED PCB factories to create adaptable design templates, allowing clients to adjust parameters like layer stacks, impedance controls, or thermal management features without full custom tooling. This approach accelerates turnaround times by 20–30% compared to ground-up designs.
- Agile Prototyping Workflows: They partner with LED PCB companies offering quick-turn prototyping services, often delivering samples within 48 hours. Exporters use iterative testing cycles to refine designs, ensuring functionality meets specs before scaling production.
- Multi-Sourcing Strategies: Top LED PCB exporters maintain relationships with diverse substrate suppliers through LED PCB factories, providing alternatives if primary materials face shortages or price hikes. This flexibility supports niche requests like high-frequency laminates or halogen-free boards.
- Automated Design Validation: They integrate automated design rule check (DRC) tools with LED PCB companies’ CAD systems, instantly flagging issues like trace/space violations or solder mask conflicts during client uploads. This reduces approval cycles by up to 50% for complex orders.
- In-House Value-Added Services: Some LED PCB exporters operate or partner with LED PCB factories that offer post-manufacturing customization, such as conformal coating, peelable solder mask, or selective hard gold plating. This eliminates third-party coordination delays and ensures quality control.
- Lifecycle Management Support: Leading exporters collaborate with LED PCB companies to provide documentation packages (e.g., Gerber files, assembly drawings) and revision control for customized boards. This simplifies reorders and reduces errors for clients with long-term product roadmaps.
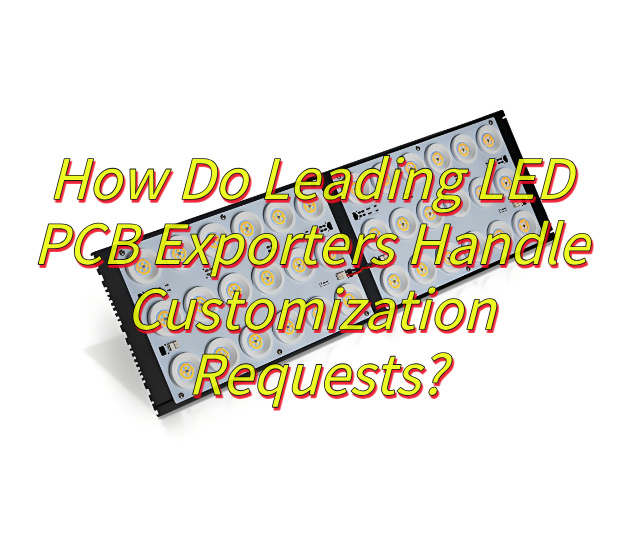
How to Avoid Hidden LED PCB Costs When Choosing LED PCB Exporter?
This is how to avoid hidden LED PCB costs when choosing LED PCB exporter:
- Request Detailed Cost Breakdowns: Require LED PCB exporters to provide itemized quotes separating material costs (e.g., substrate type, copper weight), fabrication fees (e.g., drilling, plating), and ancillary charges (e.g., tooling, testing). Compare these line items across multiple LED PCB companies to spot discrepancies, such as overpriced solder mask layers or inflated engineering fees.
- Clarify Tooling Ownership and Fees: Confirm with LED PCB factories whether tooling costs (e.g., molds, stencils) are one-time charges or recurring. Some exporters retain tooling ownership, levying fees for every reorder. Negotiate to amortize these costs over large volumes or secure free tooling for multi-year contracts.
- Validate Certification Inclusions: Ensure quotes from LED PCB companies explicitly include compliance testing (e.g., UL, RoHS, REACH) and documentation. Hidden costs may arise from last-minute charges for third-party lab reports or non-compliance fines, which can add 10–20% to total costs.
- Negotiate Flexible MOQs: Partner with LED PCB exporters offering tiered pricing for smaller batches. High minimum order quantities (MOQs) at LED PCB factories can force clients to overstock, incurring warehousing fees. Propose staggered deliveries or shared tooling to reduce upfront investments.
- Define Logistics Responsibilities: Require exporters to specify freight terms (e.g., FOB, CIF) and insurance liabilities in contracts. Hidden costs like customs duties, port storage fees, or delays from consolidated shipments can inflate costs by 15–25%. Use Incoterms 2020 to clarify obligations.
- Audit Warranty and Liability Clauses: Ensure LED PCB companies cover defects beyond standard warranties. Some exporters exclude liabilities for design-related failures or limit warranty periods. Negotiate extended liability clauses (e.g., 3 years vs. 1 year) and free failure analysis for defective boards.
- Leverage Long-Term Contracts: Secure volume discounts by signing multi-year agreements with LED PCB exporters. Factories often offer lower per-unit costs for committed forecasts, reducing risks of price hikes from material shortages (e.g., copper, laminate).
- Visit Factories Pre-Order: Conduct audits of LED PCB factories to verify capabilities (e.g., laser drilling, HDI production) and quality systems (e.g., ISO 9001, IATF 16949). Hidden costs often stem from subcontracting to non-certified shops, leading to rework or scrap.
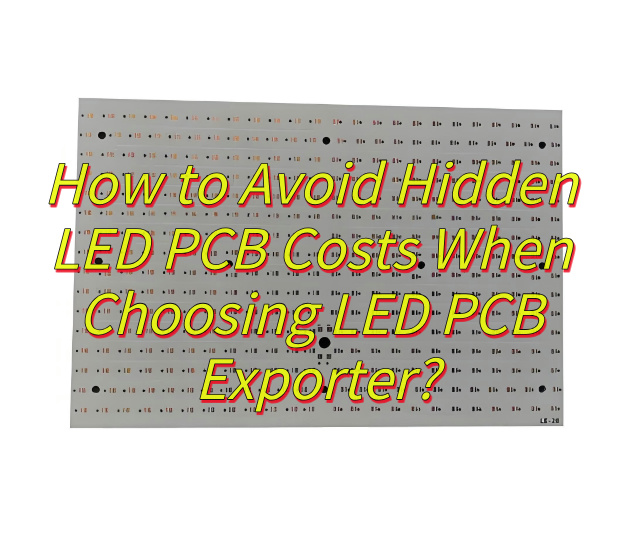
Where I Can Find A LED Grow Light PCB Exporters From China?
Here are methods about how to find a LED grow light PCB exporters from China:
Attend Industry-Specific Trade Shows
- Participate in events like the China International Horticultural Lighting Expo, which gathers manufacturers specializing in LED-related components. These platforms allow direct engagement with exporters of LED PCBs showcasing products tailored for plant growth systems, including those with high thermal conductivity or UV-resistant coatings.
Use B2B Marketplaces with Verified Suppliers
- Filter suppliers on Alibaba.com or Global Sources by selecting LED PCB exporters with certifications (e.g., ISO 9001, UL) and production capabilities for horticultural applications. Prioritize sellers offering samples or customization options, such as multi-layer boards with impedance-controlled traces for LED arrays.
Collaborate with Regional Industry Associations
- Contact China’s National Semiconductor Lighting Engineering R&D and Industry Alliance for lists of certified manufacturers. These associations often publish directories of companies specializing in LED PCBs compliant with global standards, including those supplying PCBs for smart agriculture projects.
Focus on PCB Manufacturing Hubs
- Target suppliers in regions like Guangdong Province, a global PCB production center. Local exporters of LED PCBs here typically offer competitive pricing due to mature supply chains and access to advanced materials like metal-core substrates or flexible circuits.
Evaluate Customization and Compliance
- Ensure selected LED PCB companies provide solutions like aluminum-backed boards for heat dissipation or conformal coatings for humid environments. Verify their ability to meet target-market regulations, such as FCC (U.S.) or CE (Europe), to avoid post-shipment delays.
Visit Factories for Quality Assurance
- Conduct on-site audits to assess equipment (e.g., laser drills, automated optical inspection machines) and processes. This step confirms if the exporter of LED PCBs can deliver consistent quality for high-density LED layouts used in plant lighting.
Leverage Free Trade Zones for Logistics
- Partner with suppliers of LED PCBs based in zones like Shenzhen, China. These locations offer streamlined customs procedures and bonded warehousing, reducing lead times for international orders.
Seek Recommendations from Brand-Certified Partners
- Identify LED PCB exporters that supply components to recognized lighting brands. For instance, Best Technology, a known name in precision PCBs, collaborates with manufacturers integrating advanced spectral layers for plant growth optimization.

How to Identify Reliable China LED Grow Light PCB Exporters?
Below are tips about how to identify reliable China LED grow light PCB exporters:
- Verify Industry Certifications and Standards: Prioritize China LED grow light PCB exporters holding certifications like ISO 9001 (quality management), ISO 14001 (environmental management), UL (safety), and RoHS (hazardous substances). These credentials ensure adherence to global standards for materials, production, and safety.
- Assess Production Capacity and Technology: Evaluate if the exporter of LED PCBs owns or partners with advanced facilities equipped with laser drilling machines, automated optical inspection (AOI) systems, and thermal stress testing chambers. These technologies are critical for producing high-density interconnect (HDI) boards or metal-core PCBs (MCPCBs) used in LED grow lights.
- Review Quality Control Processes: Request details on their quality assurance protocols, including incoming material inspections, in-process testing (e.g., impedance checks), and final functional tests (e.g., thermal cycling). Reliable LED PCB companies often share lot-specific traceability data.
- Check Customization Capabilities: Ensure the supplier of LED PCBs offers design flexibility, such as impedance-controlled traces, via-in-pad technology, or multi-layer boards with blind/buried vias. These features are essential for optimizing light distribution and thermal management in horticultural applications.
- Analyze Customer References and Case Studies: Request references from clients in the horticultural sector or case studies detailing projects involving LED grow light PCBs. A reputable China LED PCB exporter will provide testimonials highlighting reliability in high-humidity or high-temperature environments.
- Audit Compliance with Regional Regulations: Confirm the exporter of LED PCBs understands and complies with target-market regulations, such as FCC (U.S.), CE (Europe), or Energy Star ratings. Non-compliance can lead to costly recalls or market entry barriers.
- Evaluate Pricing and Payment Terms: Compare quotes from multiple China LED PCB suppliers while considering payment terms (e.g., 30% deposit, balance against B/L). Avoid unusually low bids, as they may indicate compromised material quality or hidden fees.
- Inspect Factory and Warehouse Facilities: Conduct on-site audits to verify inventory management, equipment calibration, and worker training programs. A well-maintained facility with cleanroom standards reduces contamination risks for sensitive LED components.
- Leverage Third-Party Testing Services: Require independent lab reports (e.g., SGS) for samples to validate performance metrics like thermal conductivity, insulation resistance, and solderability before bulk orders.
- Assess Post-Sale Support: Ensure the China LED PCB exporter offers a minimum 12-month warranty, rapid RMA (Return Material Authorization) processing, and technical support for design iterations. Prompt communication during issues is critical for minimizing downtime.
How to Verify Chinese Exporters’ Compliance with International Horticultural Standards?
- Request Certification Documents: Ask China LED PCB exporters to provide copies of certifications such as UL (for safety), CE (European conformity), or FCC (for electromagnetic compatibility). These documents confirm compliance with regulations governing electrical safety and emissions in target markets.
- Audit Material Safety Data Sheets (MSDS): Obtain MSDS for substrates, solder masks, and coatings used in LED PCBs. Ensure materials meet RoHS (Restriction of Hazardous Substances) standards, particularly for lead, mercury, and cadmium, which are critical for horticultural equipment exported to Europe or North America.
- Verify Thermal Performance Testing: Request test reports for thermal conductivity, thermal cycling resistance, and operating temperature ranges. Compliance with standards like IEC 62368-1 ensures PCBs can withstand the high heat generated by LED grow lights without degradation.
- Check Humidity and Corrosion Resistance: Confirm PCBs meet IP (Ingress Protection) ratings or MIL-STD-810 standards for moisture and corrosion resistance. This is vital for LED grow lights used in humid greenhouse environments.
- Review Electrical Performance Certificates: Ensure suppliers of LED PCBs provide impedance control data, dielectric withstanding voltage test results, and insulation resistance reports. These metrics align with IPC-6012 standards for printed board quality.
- Engage Third-Party Inspectors: Hire agencies like SGS to conduct pre-shipment inspections. They verify if PCBs meet specifications for layer count, trace/space tolerances, and finish quality, reducing risks of non-compliance.
- Assess Regulatory Knowledge: Interview China LED PCB exporters on their understanding of regional horticultural standards, such as California’s Title 24 (energy efficiency) or Australia’s AS/NZS CISPR 15 (EMI limits). Providers with dedicated compliance teams are more likely to avoid violations.
- Request Sample Testing: Order prototypes for independent lab evaluation. Test for light reflectivity, thermal expansion compatibility with LED chips, and long-term reliability under UV exposure to simulate horticultural use cases.
- Review Export History: Analyze the exporter of LED PCBs’ track record in shipping to target regions. Frequent customs holds or product recalls indicate potential compliance gaps.
- Leverage Trade Agreements: Utilize China’s free trade agreements (e.g., RCEP) to streamline certification processes. Suppliers of LED PCBs familiar with mutual recognition agreements (MRAs) can expedite approvals in member countries.
What Special Features Do Chinese Grow Light PCBs Offer for Vertical Farms?
- High-Thermal-Conductivity Substrates: Chinese-made LED grow light PCBs often use aluminum or copper-core substrates to enhance heat dissipation. This prevents overheating in dense vertical farm setups, where multiple LED arrays operate continuously.
- Multi-Layer Circuit Designs: Advanced PCBs feature 4–8 layers to accommodate complex wiring for RGBW LED chips and smart sensors. This enables precise spectral control and real-time adjustments to light intensity, critical for optimizing plant growth stages.
- IP65+ Moisture Resistance: To withstand high-humidity environments in vertical farms, PCBs are coated with conformal materials or use immersion gold finishes. This protects against corrosion and electrical shorts caused by spray irrigation or condensation.
- Flexible and Rigid-Flex Options: Some PCBs combine rigid and flexible sections to fit into compact, multi-tiered vertical farm structures. This design reduces assembly complexity and allows seamless integration with movable LED fixtures.
- High-Frequency Drivers for Dimming: PCBs incorporate high-speed signal transmission layers to support PWM (Pulse Width Modulation) dimming. This enables smooth, flicker-free brightness adjustments, essential for simulating natural light cycles in indoor farms.
- Embedded Sensors and Connectivity: Modern PCBs include built-in sensors for temperature, humidity, and light spectrum monitoring. Some support IoT protocols like LoRa or Zigbee, enabling remote management and data analytics for crop optimization.
- UV-Resistant Coatings: To prevent degradation from prolonged UV exposure in LED grow lights, PCBs use specialized solder masks and laminates. This extends lifespan in vertical farms using UVA/UVB supplements for specific crops.
- Lightweight and Thin Profiles: Chinese manufacturers optimize PCB thickness (0.8mm–1.6mm) and weight to reduce load on vertical farm racks. This allows for safer stacking of multiple LED panels without compromising structural integrity.
- Customizable Spectral Layers: PCBs can be engineered with trace patterns that distribute specific wavelengths (e.g., 660nm red, 450nm blue) evenly across the board. This ensures uniform light delivery to plants in vertically stacked tiers.
- Energy-Efficient Power Modules: Integrated DC-DC converters and low-loss circuitry minimize power waste, aligning with vertical farms’ sustainability goals. Some designs achieve >90% efficiency, reducing operational costs for 24/7 lighting.
Which Technological Breakthroughs Are Redefining China’s Grow Light PCB Exports?
Here are technological breakthroughs are redefining China’s grow light PCB exports:
- High-Thermal-Conductivity Substrates: Chinese manufacturers now widely adopt aluminum-nitride (AlN) or ceramic-based PCBs to manage heat in high-power LED grow lights. These materials offer 3–5x better thermal dissipation than traditional FR-4, preventing LED degradation in 24/7 vertical farming operations.
- Advanced Manufacturing Processes: Laser direct imaging (LDI) and modified semi-additive processes (MSAP) enable finer trace/space tolerances (<50µm). This supports high-density interconnect (HDI) PCBs for compact, multi-spectrum LED arrays used in vertical farms.
- Embedded Passive Components: Innovations like embedded resistors and capacitors reduce PCB layer counts by 30%, lowering costs while improving signal integrity. This is critical for precision dimming and spectral tuning in smart LED fixtures.
- Flexible Hybrid Electronics: Rigid-flex PCBs combining polyimide flexibility with FR-4 rigidity allow 3D lighting configurations. These designs conform to tiered vertical farm structures, eliminating wires and reducing assembly time by 40%.
- AI-Driven Spectral Optimization: Machine learning algorithms integrated into PCB design tools auto-calculate copper trace patterns to distribute specific wavelengths (e.g., 660nm red, 450nm blue) uniformly. This ensures 5–10% higher crop yields in controlled environments.
- Energy-Harvesting Power Modules: PCBs now incorporate miniaturized energy-harvesting circuits that convert excess LED heat into auxiliary power for IoT sensors. This reduces energy consumption by 8–12% in smart vertical farms.
- Biodegradable Substrates: Experimental PCBs using flax fiber or mushroom mycelium substrates align with global sustainability trends. While early-stage, these materials reduce e-waste risks for disposable LED grow light modules.
- Quantum Dot Integration: Nano-coatings with quantum dots on PCB surfaces enable wavelength conversion, allowing single-color LEDs to emit full-spectrum light. This cuts component costs by 25% while maintaining crop quality.
- 5G-Enabled Real-Time Monitoring: PCBs with embedded 5G antennas and edge-computing chips enable sub-1ms latency for light adjustment commands. This supports AI-driven dynamic lighting strategies in large-scale vertical farms.
- Self-Healing Conformal Coatings: Polyurethane coatings with microcapsules containing healing agents automatically repair cracks from thermal stress. This extends PCB lifespan by 30% in high-humidity vertical farming environments.