Looking for round LED light PCB solutions? Discover how circular PCB geometry enhances thermal management, reduces costs, manufacturers selection tips and streamlines LED integration across commercial applications.
Best Technology delivers rapid 24-hour prototype turnaround for round LED light PCB and circle LED PCB, supported by automated SMT lines that reduce bulk production lead times to â€7 days. Competitive pricing starts at $0.15/unit for 100-piece orders of aluminum base boards (1.6mm thickness, 100mm diameter), with ISO 9001, UL, and RoHS certifications ensuring IPC Class 3 soldering precision. Thermal management designs achieve <8°C/W resistance for 5050/5730 LED arrays, validated via 72-hour thermal cycling and salt-spray tests. Free DFM analysis minimizes design flaws, while 3D AOI inspection guarantees >99.8% defect-free output across 10,000+ monthly shipments. Flexible customization includes diameter adjustments (50â500mm), non-standard drill patterns, and mixed LED layouts (â€200 LEDs per board). DDP shipping and 3-year warranties against soldering/dielectric failures streamline global logistics. Welcome to contact us if you have any request for round LED light PCB: sales@bestpcbs.com.
What Is A Round LED Light PCB?
A round LED light PCB refers to a circular printed circuit board specifically engineered to support and power LED arrays in lighting applications. Its design integrates conductive pathways and components arranged in a circular layout, enabling efficient energy distribution and thermal management for LEDs positioned around its perimeter or surface. This configuration optimizes light emission uniformity while minimizing space usage, making it suitable for compact fixtures like bulb replacements, decorative lamps, automotive interior lights, and indicator panels. The PCBâs shape facilitates seamless integration with cylindrical or disc-shaped housings, ensuring structural compatibility and aesthetic consistency in end products. Material selection often prioritizes durability and heat dissipation to maintain performance under prolonged operation, while surface-mounted LEDs enhance brightness and energy efficiency. By combining electrical functionality with geometric precision, this PCB type serves as a foundational element in modern lighting solutions requiring reliability and adaptability across diverse environments.
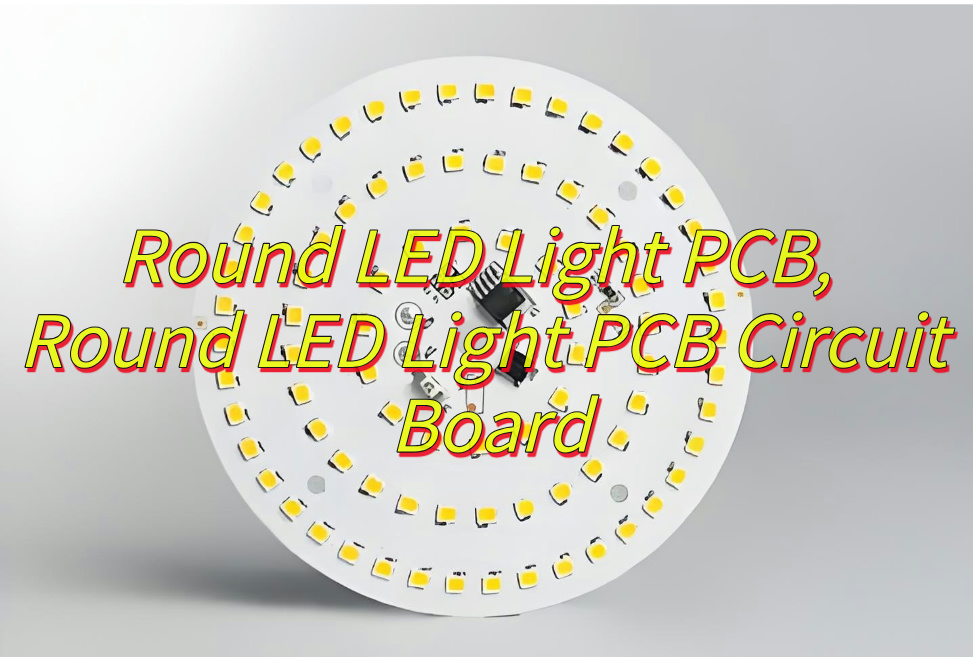
What Are Benefits of Round LED Light PCB?
Benefits of round LED light PCB:
- Enhanced Thermal Management: Round LED Light PCBs are designed with symmetrical thermal paths that distribute heat evenly across the circular surface. This geometry minimizes heat concentration at specific points, preventing localized overheating and extending the lifespan of LED components. Advanced models often incorporate metal-core substrates or thermal vias to further improve heat dissipation, ensuring stable performance in high-power applications.
- Optimized Optical Efficiency: The circular layout enables 360-degree light emission, making it ideal for applications requiring uniform illumination, such as decorative fixtures or indicator lights. By aligning LED chips radially, manufacturers can eliminate dark spots and achieve consistent brightness across the entire circumference. Some designs integrate diffusers or lenses to refine light distribution, enhancing visual comfort.
- Space-Efficient Design: Round PCBs fit seamlessly into compact or spherical fixtures, reducing wasted space compared to rectangular alternatives. This is particularly advantageous for miniature LED modules, wearable devices, or automotive interior lighting, where size constraints are critical. The absence of sharp corners also simplifies integration into curved enclosures.
- Durability in Harsh Environments: Constructed from flexible or rigid-flex materials like polyimide, Round LED Light PCBs resist vibration, moisture, and extreme temperatures. This robustness makes them suitable for outdoor displays, industrial machinery, or automotive lighting systems. Their seamless structure minimizes stress points, enhancing resistance to mechanical fatigue over time.
- Cost-Effective Manufacturing: The circular form factor reduces material waste during production, as PCBs can be nested efficiently on manufacturing panels. Additionally, modular designs allow for standardized component placement, streamlining assembly and reducing labor costs. Some manufacturers adopt semi-circular PCB segments that interlock, balancing cost and performance.
- Aesthetic Versatility: Round LED Light PCBs offer designers greater creative freedom, enabling sleek, minimalist fixtures that align with modern architectural trends. Their adaptability supports dynamic lighting effects, such as color gradients or rotational patterns, which are popular in retail displays or entertainment venues.
- Energy Efficiency: By optimizing circuit traces and power distribution, Round LED Light PCBs minimize energy loss. This efficiency is critical for battery-powered devices, such as smart home sensors or portable lamps, where prolonged runtime is essential. Some designs incorporate motion sensors or dimming controls to further reduce power consumption.
- Scalability for Diverse Applications: From low-power accent lighting to high-lumen industrial fixtures, Round LED Light PCBs cater to a broad spectrum of needs. Their modular architecture allows easy customization of LED density, color temperatures, and beam angles, ensuring compatibility with specialized requirements.
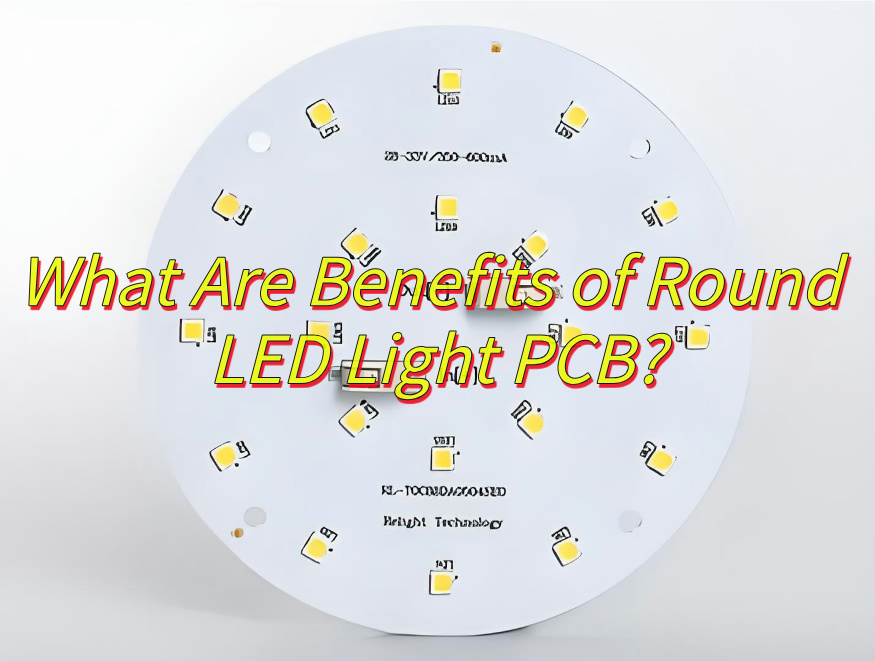
Why Choose A Round PCB with 5050 Warm White LEDs for Lighting?
Here are reasons why choose a round PCB with 5050 warm white LEDs for lighting:
- Symmetrical Design for Uniform Light Distribution: A circular PCB layout enables 360-degree light emission, eliminating dark spots and ensuring consistent illumination. This symmetry is ideal for applications like pendant lights, ceiling fixtures, or decorative lamps, where balanced brightness is essential. The round form factor aligns seamlessly with standard lighting housing designs, simplifying integration.
- Enhanced Thermal Management: Round PCBs distribute heat more evenly across their surface compared to irregular shapes. Paired with 5050 LEDsâknown for their thermal efficiency and robust constructionâthis combination minimizes hotspots, extends lifespan, and maintains stable performance under prolonged operation. The circular geometry also facilitates airflow, aiding passive cooling.
- Optimal Light Quality with Warm White 5050 LEDs: The 5050 LED package delivers high luminous efficacy (typically 20-22 lm/W) while emitting a warm white hue (2700-3000K). This color temperature creates a cozy, inviting atmosphere, making it suitable for residential, hospitality, and ambient lighting. The large chip size of 5050 LEDs ensures broad beam angles, reducing glare and enhancing visual comfort.
- Versatility in Compact Spaces: The compact dimensions of 5050 LEDs (5.0mm Ă 5.0mm) allow dense placement on circular PCBs without compromising spacing. This enables high-lumen output in slim fixtures, such as recessed downlights or under-cabinet lighting, where space efficiency is critical.
- Cost-Effective Scalability: Round PCBs are compatible with mass-production techniques like automated surface-mount technology (SMT), lowering manufacturing costs. The widespread availability of 5050 LEDs further reduces procurement expenses, making this configuration a budget-friendly choice for large-scale projects like commercial buildings or smart lighting systems.
- Durability in Diverse Environments: Both circular PCBs and 5050 LEDs exhibit resistance to moisture, vibrations, and temperature fluctuations. This robustness suits outdoor fixtures, industrial settings, or high-traffic areas where reliability is non-negotiable. The epoxy-encapsulated design of 5050 LEDs adds an extra layer of protection against environmental stressors.
- Customizable Lighting Effects: The circular arrangement allows dynamic lighting configurations, such as color-changing rings or dimmable zones, by grouping LEDs into controllable segments. This flexibility supports smart lighting ecosystems, enabling users to adjust intensity or color temperature via apps or sensors.
- Aesthetic and Functional Harmony: The minimalist appearance of a round LED PCB complements modern interior designs, while its functional advantagesâsuch as low profile and even glowâaddress practical needs. Whether used in architectural accents or task lighting, this combination balances form and performance.
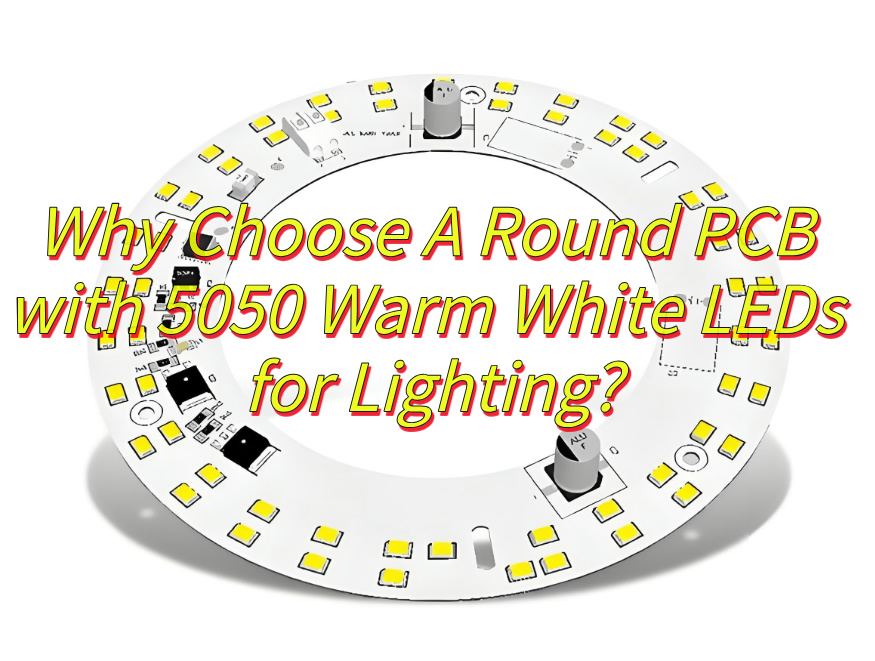
How to Design a Round LED PCB for Ceiling Light?
Here are steps about how to design a round LED PCB for ceiling light:
1. Define PCB Dimensions and Shape
- Determine the diameter and thickness of the round PCB based on the ceiling light fixtureâs specifications.
- Use CAD software to create a circular layout, ensuring alignment with mechanical constraints (e.g., housing, mounting holes).
2. LED Arrangement and Spacing
- Distribute LEDs evenly across the circular surface to achieve uniform light output. Radial or concentric patterns are common choices.
- Calculate spacing between LEDs to balance brightness and thermal performance. Avoid overcrowding to prevent hotspots.
3. Thermal Management
- Integrate thermal vias beneath LEDs to conduct heat toward the PCBâs core or external heat sink.
- Choose metal-core PCBs (e.g., aluminum or copper) to enhance heat dissipation. Specify thermal conductivity ratings (e.g., 1â3 W/m·K) based on power requirements.
4. Power Supply and Circuit Design
- Design a constant-current driver circuit to stabilize LED performance and extend lifespan.
- Include AC-DC conversion components (e.g., rectifiers, capacitors) if mains-powered. Isolate high-voltage sections to meet safety standards.
5. Material Selection
- Choose FR-4 substrate for cost efficiency or metal-core PCBs for high-power applications.
- Select copper thickness (e.g., 1â2 oz) and trace width based on current-carrying capacity to minimize voltage drop.
6. Component Placement and Routing
- Place LEDs symmetrically to simplify wiring and reduce electromagnetic interference (EMI).
- Route high-current traces away from sensitive analog components. Use ground planes to stabilize voltage and reduce noise.
7. Mounting and Assembly Considerations
- Add mounting holes or slots at the PCB edge for secure attachment to the ceiling fixture.
- Include solder pads or connectors for easy integration with external drivers or dimming modules.
8. Dimming and Control Features
- Incorporate PWM (Pulse Width Modulation) circuits for adjustable brightness if dimming functionality is required.
- Ensure compatibility with smart home protocols (e.g., Wi-Fi, Bluetooth) by reserving space for microcontrollers or modules.
9. Testing and Validation
- Prototype the PCB and test thermal performance using infrared cameras or thermocouples.
- Verify lumen output, color temperature, and CRI (Color Rendering Index) against design targets.
- Conduct aging tests to confirm long-term reliability under continuous operation.
10. Compliance and Safety
- Adhere to electrical safety standards (e.g., IEC 60598 for luminaires) and RoHS directives.
- Include fusing or overcurrent protection to prevent damage during faults.
How to Find Reliable Factories for Custom Round LED Light PCB Orders?
Below are how to find reliable factories for custom round LED light PCB orders:
- Online B2B Marketplaces: Utilize platforms like Alibaba, Global Sources, or Made-in-China, where manufacturers list their capabilities. Use filters to narrow down suppliers specializing in Round LED Light PCB production. Prioritize vendors with verified certifications (e.g., ISO 9001) and detailed product descriptions showcasing customization options. Request quotes and sample production timelines directly through these platforms.
- Industry Trade Shows and Exhibitions: Attend electronics-focused events such as Electronica (Germany), CES (USA), or regional lighting expos. These gatherings feature manufacturers displaying their expertise in Round LED Light PCB designs. Engage in live discussions to assess technical proficiency, production capacity, and compliance with safety standards (e.g., UL, RoHS).
- Specialized PCB Directories: Explore niche directories like PCB Directory or PCB Shopper, which categorize suppliers by specialization. Search for factories explicitly listing Round LED Light PCB fabrication as a core service. These platforms often include customer reviews and comparative tools to evaluate pricing and lead times.
- Social Media and Technical Forums: Join LinkedIn groups or Reddit communities focused on PCB engineering. Post inquiries about trusted manufacturers for Round LED Light PCB projects. Leverage forums like EEWeb or Electronics Point to gather recommendations from peers based on real-world collaborations.
- Referral Networks: Contact industry associations (e.g., IPC – Association Connecting Electronics Industries) for member directories. Request referrals from peers or distributors who have previously sourced Round LED Light PCB components. Case studies or white papers from electronics trade publications may also highlight reliable suppliers.
- Quality Certification Databases: Verify manufacturers through certification bodies like UL or TĂV Rheinland. Use their online databases to confirm factories hold valid certifications for Round LED Light PCB production, ensuring adherence to thermal management, electrical safety, and durability standards.
- Local Chambers of Commerce or Export Agencies: Consult regional trade organizations for lists of PCB manufacturers with export experience. These entities often vet members for reliability and may provide insights into factories experienced in Round LED Light PCB customization for global markets.
- Direct Outreach to Manufacturers: Compile a list of factories from the above channels and send detailed RFQs (Requests for Quotations). Specify requirements such as board diameter, thermal conductivity, and LED integration. Evaluate responses based on technical feasibility, MOQ (Minimum Order Quantity) flexibility, and willingness to provide material certifications (e.g., FR-4, aluminum core).
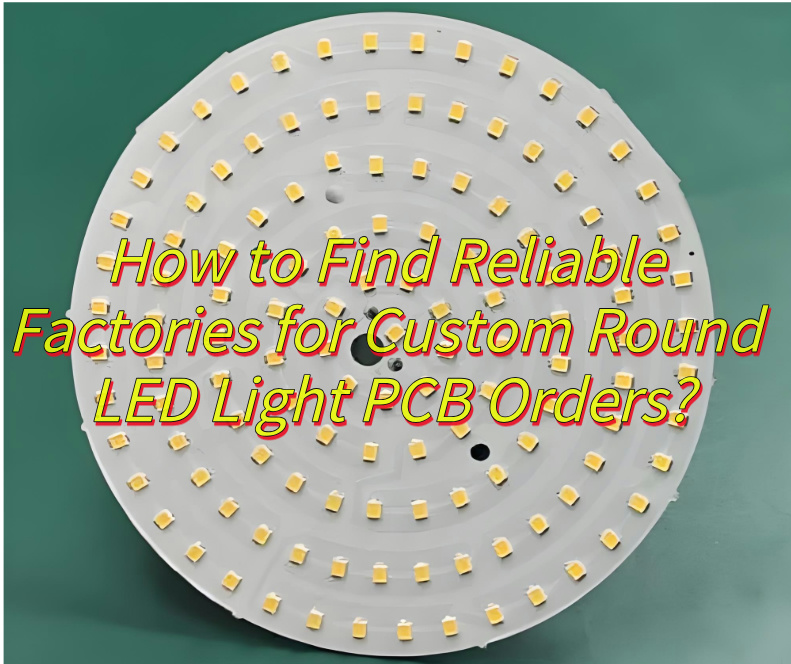
How to Choose A Reliable Round LED Light PCB Manufacturers in China?
Here’re methods about how to choose a reliable round LED light PCB manufacturer in China:
- Verify Technical Expertise and Experience: Prioritize manufacturers with proven experience in producing round LED light PCBs. Review their portfolio for projects involving similar specifications, such as thermal management, high-precision drilling, and copper thickness requirements for LED applications. Inquire about their familiarity with industry standards like IPC-A-600 and IPC-6012, which ensure reliability for lighting products.
- Assess Production Capacity and Equipment: Ensure the manufacturer has advanced machinery tailored for circular PCB fabrication, such as CNC routers for precise contour cutting and automated optical inspection (AOI) systems to detect defects in curved traces. Confirm their capacity to handle both small-batch prototypes and large-scale orders while maintaining consistency in quality.
- Evaluate Quality Control Processes: A reliable supplier should implement rigorous testing protocols, including electrical continuity checks, solderability tests, and thermal cycling simulations specific to round LED light PCBs. Request details on their inspection procedures, such as flying probe testing or X-ray inspection for hidden layer issues, to guarantee defect-free products.
- Review Material Sourcing and Compliance: Confirm the manufacturer uses high-quality substrates (e.g., FR-4, aluminum-backed PCBs) suitable for LED heat dissipation. Check if their materials comply with environmental regulations like RoHS and REACH, which are critical for global market access. Ask for certificates of conformity (CoC) for raw materials to avoid subpar components.
- Customization and Design Support: Look for manufacturers offering engineering support to optimize your round LED light PCB design. This includes assistance with trace width calculations for current-carrying capacity, annular ring adjustments for via reliability, and impedance control for signal integrity. Providers with in-house design teams can streamline iterations and reduce time-to-market.
- Pricing and Payment Terms Transparency: Request detailed quotes breaking down costs for materials, labor, tooling, and testing. Avoid suppliers with unusually low pricing, as this may indicate compromised quality. Negotiate flexible payment terms, such as milestone-based payments, to balance cash flow with delivery timelines.
- Communication and Project Management: Choose a manufacturer with fluent English-speaking project managers and clear communication channels (e.g., ERP systems for real-time updates). Timely responses to inquiries and proactive updates on production status are essential for avoiding delays, especially for time-sensitive round LED light PCB orders.
- Check Post-Sales Support and Warranty
A trustworthy supplier will offer a minimum 12-month warranty covering manufacturing defects. Inquire about their process for handling reworks or replacements, including response times and shipping logistics. Case studies or client references can provide insights into their post-sales reliability. - Audit Ethical and Environmental Practices
Ensure the manufacturer adheres to ethical labor standards and environmental policies, such as ISO 14001 certification. This not only aligns with corporate social responsibility but also reduces risks related to supply chain disruptions or regulatory penalties. - Visit Facilities or Request Virtual Tours
If feasible, conduct an on-site audit to verify cleanroom standards, inventory management, and employee training programs. For remote assessments, ask for live virtual tours focusing on critical areas like the SMT assembly line or quality control lab.
How to Reduce Lead Time of LED Light PCB Circuit Board?
Here are strategies to reduce lead time for round LED light PCB circuit boards:
Design Optimization for Manufacturability
- Simplify Layer Stack-Up: Use standardized layer configurations (e.g., 4-layer or 6-layer boards) to streamline production planning and reduce setup time. Avoid overly complex designs that require custom tooling.
- Panelization Efficiency: Optimize PCB panel layouts to maximize the number of Round LED Light PCB units per panel while maintaining adequate spacing for automated assembly and testing.
- Component Placement: Prioritize surface-mount technology (SMT) components over through-hole parts to eliminate drilling steps and enable faster automated assembly.
Adopt Advanced Manufacturing Technologies
- Laser Direct Structuring (LDS): For 3D mid-plane LED PCBs, LDS eliminates traditional etching and plating steps by laser-activating plastic surfaces for selective metallization, reducing lead time by 30â50%.
- Automated Optical Inspection (AOI): Integrate AOI systems post-soldering to detect defects in real time, minimizing rework cycles.
- Round LED-Specific Tooling: Use circular-shaped stencils and fixtures designed for Round LED Light PCB geometries to reduce alignment errors during solder paste printing and component placement.
Streamline Supply Chain Coordination
- Localize Material Sourcing: Partner with regional suppliers for critical materials (e.g., FR-4 substrates, copper foils) to reduce shipping delays and customs clearance times.
- Just-in-Time (JIT) Inventory: Implement JIT systems for LED chips, resistors, and capacitors to minimize storage costs while ensuring raw materials arrive 1â2 days before production starts.
- Vendor-Managed Inventory (VMI): Allow key suppliers to monitor stock levels and replenish materials automatically, avoiding stockouts.
Process Automation and Lean Production
- SMT Line Balancing: Deploy multi-head pick-and-place machines with parallel nozzles to assemble Round LED Light PCBs at speeds exceeding 80,000 components/hour, reducing assembly time by 40%.
- Conveyor System Upgrades: Replace manual conveyors with smart conveyors featuring automatic width adjustment and RFID tracking to handle varying PCB diameters without downtime.
- Concurrent Engineering: Overlap design validation and manufacturing preparation phases using simulation tools to identify and resolve issues before physical prototyping.
Quality Assurance Acceleration
- In-Line Electrical Testing: Conduct flying probe tests during assembly rather than as a final step, enabling immediate correction of faults without disrupting workflows.
- Accelerated Thermal Cycling: Use infrared (IR) reflow ovens with rapid heating/cooling rates (â„5°C/sec) to shorten soldering cycles while maintaining joint reliability.
- Automated Functional Testing: Deploy robotic test jigs with programmable LED drivers to validate Round LED Light PCB performance in <2 minutes per unit.
Logistics and Order Management
- Digital Twins for Order Tracking: Create virtual replicas of production lines to simulate lead times under different order volumes and prioritize urgent Round LED Light PCB batches.
- Express Shipping Partnerships: Collaborate with logistics providers for guaranteed 24-hour delivery of finished goods to regional hubs, reducing final-mile transit time.
- Dynamic Capacity Allocation: Reserve 10â15% of daily production capacity for expedited Round LED Light PCB orders, adjusting schedules using AI-driven algorithms.
Design for Assembly (DFA) Enhancements
- Uniform Component Spacing: Maintain â„0.3mm spacing between LEDs and passive components on Round LED Light PCBs to simplify automated soldering and reduce bridging risks.
- Polarity Markings: Include laser-etched polarity indicators on PCBs to eliminate manual inspection steps during assembly.
- Test Point Standardization: Place dedicated test points at 120° intervals on circular PCBs to ensure consistent access for in-circuit test (ICT) probes.
What Are Factors Affect Round LED Light PCB Circuit Board?
Here are factors affect round LED light PCB circuit board:
Material Selection
- Base Substrate: Aluminum-backed PCBs (MCPCB) are preferred for thermal conductivity (1.0â2.0 W/m·K), reducing heat accumulation compared to standard FR-4 materials.
- Copper Thickness: Heavier copper layers (e.g., 2 oz vs. 1 oz) improve current-carrying capacity and heat dissipation but increase cost and manufacturing complexity.
- Dielectric Layer: High-quality insulating materials with low thermal resistance (e.g., <0.2 W/mK) ensure efficient heat transfer from LEDs to the substrate.
Thermal Management
- Heat Sink Integration: Proper alignment of LEDs with thermal vias and direct contact to heat sinks minimizes junction temperature rise.
- Airflow Optimization: Circular layouts require strategic component placement to avoid hotspots, often using radial symmetry to promote uniform cooling.
- Thermal Interface Materials (TIM): High-performance TIMs (e.g., silicone pads or phase-change materials) bridge gaps between PCBs and heat sinks, reducing thermal resistance.
Circuit Layout and Trace Design
- Current Distribution: Uniform spacing of LED traces prevents voltage drops and ensures consistent brightness across the circular array.
- Power/Ground Planes: Solid copper planes reduce impedance and electromagnetic interference (EMI), critical for stable LED operation.
- Component Placement: Critical components (e.g., drivers, capacitors) are positioned near the center to minimize trace lengths and thermal gradients.
Mechanical and Structural Considerations
- Board Flexibility: Rigid-flex PCBs may be required for curved installations, balancing durability with conformal fit to non-planar surfaces.
- Hole and Via Placement: Plated through-holes (PTHs) and blind vias must avoid LED footprints to prevent light blockage or structural weakness.
- Tolerance and Assembly: Tight mechanical tolerances (e.g., ±0.1 mm) ensure LED alignment, critical for color mixing and beam uniformity.
Power Delivery and Efficiency
- Voltage Regulation: Constant-current drivers with high power factor correction (PFC) maintain LED longevity and efficiency.
- Wire Sizing: Thicker traces (e.g., >20 mil) for high-current paths reduce resistive losses and heat generation.
- Dimming Compatibility: PWM or analog dimming circuits must be isolated from sensitive analog sections to prevent flicker.
Environmental and Reliability Factors
- Moisture Sensitivity: Conformal coatings protect against humidity in outdoor or high-humidity applications.
- UV Resistance: Materials for outdoor use must resist degradation from prolonged UV exposure.
- Vibration Resistance: Sturdy solder joints and component anchoring prevent failures in dynamic environments (e.g., automotive lighting).
Optical Performance
- Light Diffusion: PCB surface finishes (e.g., matte solder mask) reduce glare, while reflective coatings enhance lumen output.
- Color Consistency: Binning of LEDs by wavelength and luminous flux ensures uniform color temperature across the circular array.
- Beam Angle Control: PCB layout interacts with secondary optics (e.g., lenses, reflectors) to shape light distribution patterns.
Manufacturability and Cost
- Layer Count: Minimizing layers reduces costs but requires careful partitioning of power, ground, and signal traces.
- Panelization: Circular boards are often arrayed in rectangular panels for efficient SMT assembly, with breakaway tabs for final separation.
- Testing Accessibility: Test points and fiducial markers must be placed to avoid LEDs and ensure automated optical inspection (AOI) compatibility.
By addressing these factors, designers can optimize round LED light PCBs for thermal efficiency, reliability, and optical performance while balancing cost and manufacturability.