Looking for aluminum based PCB solution? This guide explores thermal management, performance enhancement, and long-term reliability strategies for optimal lighting solutions.
What Is Aluminum Based PCB?
An aluminum based PCB is a specialized circuit board that uses an aluminum substrate as its foundation instead of traditional fiberglass materials. The board’s structure typically includes three essential layers: a conductive copper layer for circuitry, a thermally conductive dielectric layer for electrical insulation, and the aluminum substrate that provides both mechanical support and heat dissipation.
This design offers superior thermal management compared to conventional PCBs, as the aluminum substrate efficiently transfers heat away from components. Similar to aluminum substrate PCB technology, these boards maintain excellent dimensional stability while operating in high-temperature environments. The metal core also provides natural electromagnetic shielding and vibration resistance.
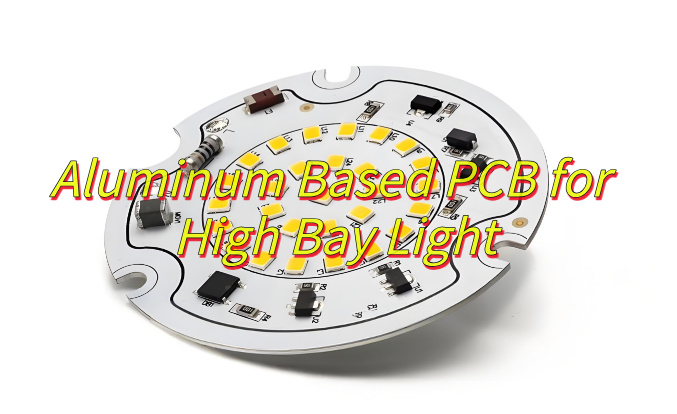
Aluminum Based PCB Thermal Conductivity
Aluminum-based PCBs (Metal Core PCBs or MCPCBs) have a ātypical thermal conductivityā ranging from ā1.0 W/mĀ·K to 8.0 W/mĀ·Kā, depending on the dielectric layer composition. Here’s a detailed breakdown:
Factors Affecting Thermal Conductivity:
Dielectric Layerā:
- The thermally conductive but electrically insulating layer between the copper circuit and aluminum base is critical.
- Standard dielectric: ā1.0ā2.5 W/mĀ·Kā (e.g., epoxy-based).
- High-performance dielectric (filled ceramics/polymers): āUp to 8.0 W/mĀ·Kā.
Aluminum Substrateā:
- Pure aluminum has high thermal conductivity (~220 W/mĀ·K), but the dielectric layer limits overall performance.
Layer Thicknessā:
- Thinner dielectric layers improve heat transfer but reduce electrical insulation.
Aluminum Based PCB Stackup
Aluminum-based PCBs (Metal Core Printed Circuit Boards) typically follow a ā3-layer stackupā optimized for thermal management. Here’s the standard architecture:
Circuit Layer (Top)ā
- āMaterialā: Copper foil (Electrodeposited or Rolled).
- āThicknessā: 1ā10 oz (35ā350 μm).
- āFunctionā: Carries conductive traces/components.
Dielectric/Insulating Layer (Middle)ā
- Materialā: Thermally conductive polymer/ceramic-filled epoxy (e.g., polyimide, aluminum oxide, or boron nitride composites).
- āThicknessā: 50ā200 μm.
- āCritical Propertiesā:
- Thermal Conductivity: ā1.0ā8.0 W/mĀ·Kā (depends on filler).
- Dielectric Strength: ā>2 kVā (electrical isolation).
āBase Layer (Bottom)ā
- Materialā: Aluminum alloy (e.g., 6061 or 5052).
- āThicknessā: 0.5ā3.0 mm.
- āFunctionā: Heat spreading/mechanical support.
Heat Dissipation Solution for Aluminum Substrate Board
- High-Conductivity Dielectric Layers: Select ceramic-filled polymer dielectrics (3ā5W/mĀ·K) to reduce thermal resistance. Optimize layer thickness (50ā150μm) for balanced insulation and heat transfer.
- Thermal Via Arrays: Place dense thermal vias (0.3ā0.5mm diameter, 1mm pitch) under high-power components. Fill vias with silver epoxy or solder to boost vertical heat conduction.
- Radiative Surface Treatments: Apply anodized coatings (10ā30μm thickness) with emissivity >0.8 for radiative cooling. Use matte finishes to minimize heat reflection and enhance airflow.
- Component Clustering: Position heat-generating devices (e.g., MOSFETs, LEDs) centrally on the board for uniform heat spreading. Maintain ā„2mm clearance from edges to prevent hotspots.
- Direct Thermal Bonding: Attach components with thermally conductive adhesives (1ā3W/mĀ·K) or solder. Avoid low-conductivity TIMs (<0.5W/mĀ·K) for critical high-power nodes.
- Embedded Heat Spreaders: Integrate copper blocks or heat pipes into the aluminum substrate. Use press-fit or friction-stir welding for robust contact and rapid heat transfer.
- Forced Convection Design: Align fins/channels on the aluminum surface with enclosure airflow. Include mounting holes for external heatsinks or fans (40ā80mm diameter) to enhance cooling.
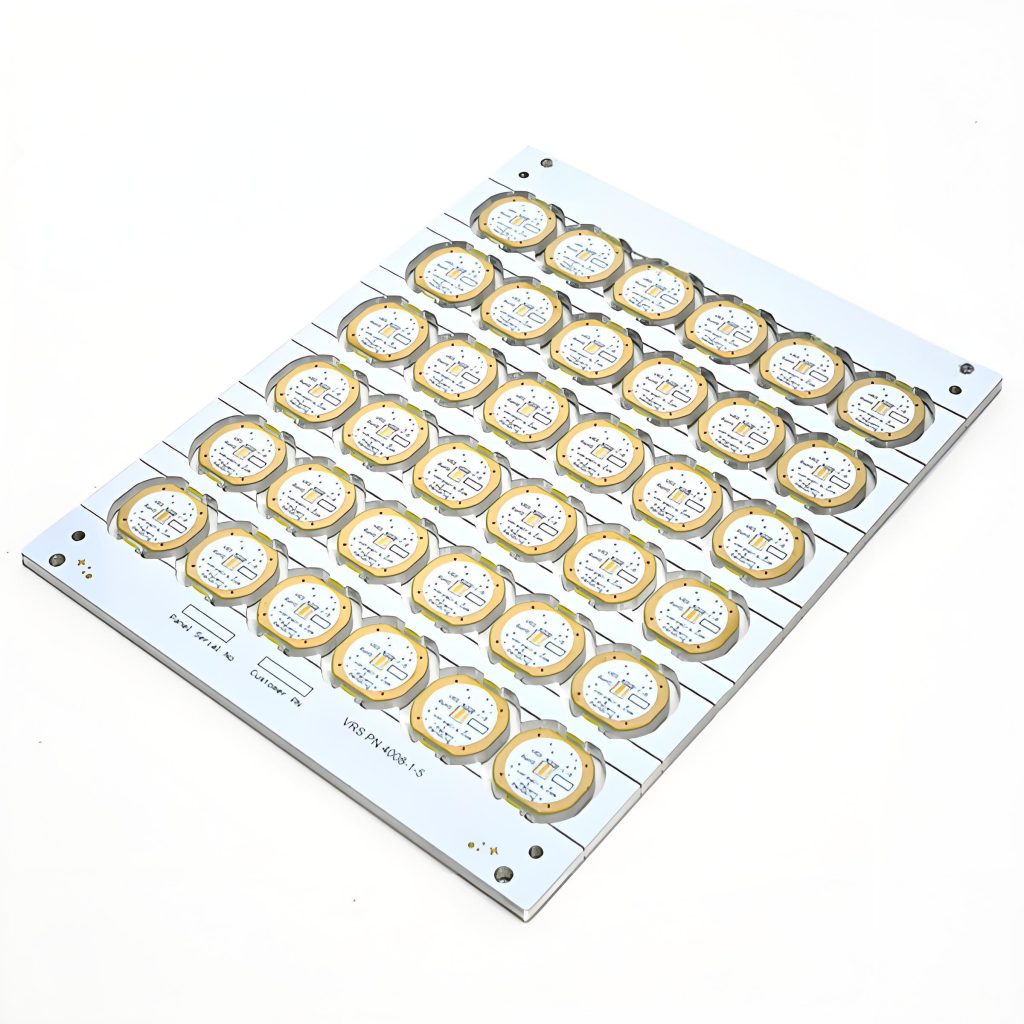
Why Choose Aluminum Based PCB for High Bay Light?
Reasons why choose aluminum base PCB for high bay light:
- Thermal Efficiency: Conducts heat efficiently, reducing LED junction temperature by 20ā30% (vs. FR-4), extending lifespan to 50,000+ hours.
- Mechanical Strength: Supports heavy LED arrays/lenses, resists vibration and thermal expansion in harsh environments (e.g., factories).
- Cost Savings: Eliminates external heatsinks/fans, cutting initial costs and long-term maintenance from thermal failures.
- Compact Design: Allows dense component placement (e.g., multi-chip LEDs) without overheating, enabling slim fixtures for elevated/confined spaces.
- Environmental Resilience: Corrosion-resistant, stable (-40°C to 150°C), ideal for outdoor/dusty industrial settings.
- Energy Optimization: Stable thermal environment ensures consistent LED output, maximizing lumen/watt efficiency at higher drive currents.
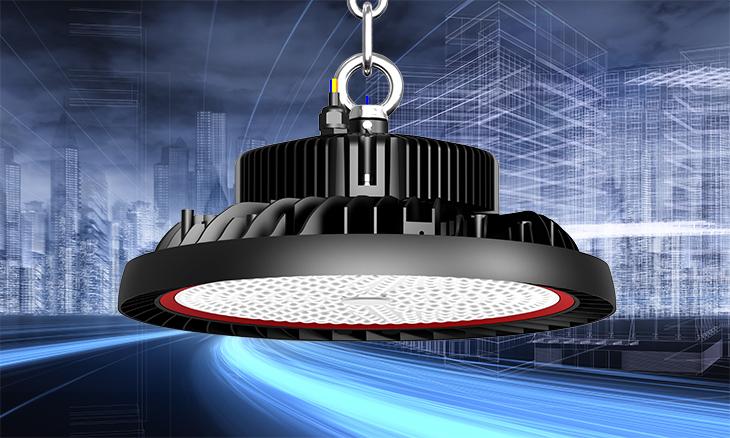
How to Improve the Electrical Performance of Aluminum PCBs in High Bay lighting?
- Thicken Copper Traces: Use 2ozā4oz copper to lower DC resistance, reducing voltage drop and heat in power lines. Supports 5Aā20A currents without overheating.
- Match Impedance: Design 50Ī© microstrip lines with ground planes to minimize signal reflection. Critical for stable RF communication in dimming controls.
- Isolate Power/Analog Circuits: Separate high-current drivers (e.g., MOSFETs) from low-noise analog sections. Prevents EMI coupling in LED control systems.
- Ground Plane Bonding: Connect ground layers to aluminum via thermal vias. Enhances EMI shielding and heat dissipation simultaneously.
- High-Voltage Insulation: Apply ā„100μm dielectric layers with >500V breakdown rating. Prevents arcing in AC-DC converter zones of mains-powered luminaires.
- Low-ESR Capacitors: Select polymer/MLCC types (<10mΩ ESR) to stabilize driver outputs. Reduces ripple and extends lifespan under thermal stress.
- Thermal-Electrical Co-Design: Use simulation tools to balance trace widths, via densities, and component placement. Avoids hotspots that degrade electrical reliability.
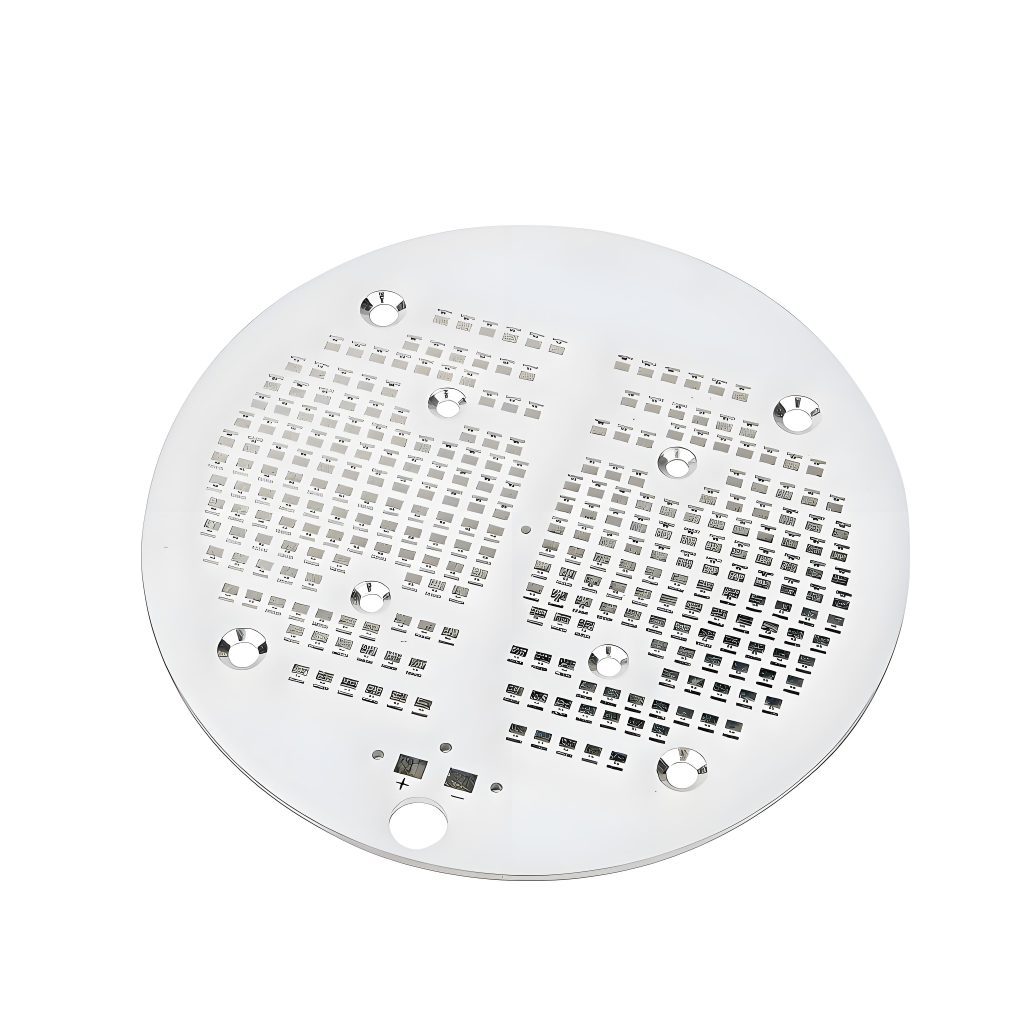
Long-Term Durability Strategies for Aluminum-Based PCBs in High-Bay Light
- Material Durability: Use 5052/6061 aluminum alloys for corrosion resistance. Pair with polyimide dielectrics (Tg ā„150°C) to resist thermal degradation.
- Thermal Stress Management: Gradual copper trace transitions reduce expansion mismatches. Thermal relief pads for through-hole components prevent solder fatigue.
- Protective Coatings: 10ā20μm hard-anodized aluminum surfaces resist scratches. Conformal coatings shield traces/solder joints from humidity/dust.
- Vibration Resistance: Epoxy adhesive or fasteners secure heavy components. Optimized via placement distributes mechanical loads.
- Humidity Control: Moisture-resistant solder masks (ā„60μm LPI) and sealed edges prevent delamination. Store PCBs in dry packs (ā¤5% RH).
- UV/Chemical Protection: UV-stable dielectrics/solder masks for outdoor use. Avoid chemical cleaners; use alcohol-based solvents.
- Maintenance Protocols: Temperature sensors/thermal fuses detect overheating. Biannual inspections check for corrosion, cracks, or material wear.
Why Choose Best Technology As Your Aluminum Based PCB Manufacturer?
- Guaranteed Reliability ā IPC Class 3 certified manufacturing with automated optical inspection (AOI) ensures <0.1% defect rates, preventing costly field failures in high-bay installations.
- Transparent Cost Structure ā No hidden fees with upfront pricing, including complimentary thermal simulations and DFM analysis to optimize designs before production.
- Thermal Management Expertise ā Free integrated heat-spreader solutions reduce LED junction temperatures by 15-30°C, extending luminaire lifespan without additional cooling components.
- Risk Mitigation Services ā Complimentary design-for-manufacturing (DFM) reviews identify potential issues (e.g., CTE mismatches, copper balancing) before tooling, avoiding 80% of post-production problems.
- Industrial-Grade Durability ā Anodized aluminum substrates with ceramic-filled dielectrics withstand 500+ thermal cycles (-40°C to 150°C), ideal for warehouses with extreme temperature swings.
- One Stop Solution ā Dedicated engineering team provides real-time production updates and technical guidance, streamlining procurement from prototype to volume orders.
If you have any request for aluminum based PCB, welcome to contact us: sales@bestpcbs.com.