Why choose 4 Layers MCPCB for UVC LED? This guide explores its optimized structure and thermal pathways, superior LED efficiency and reliability.
Are you troubled by the heat dissipation problem of UVC LED?
- High temperature leads to fast light decay, short life and unstable performance?
- Insufficient heat dissipation of traditional PCB affects product reliability?
Best Technology provide:
- Ultra-efficient heat dissipation design – 4 layers of copper + optimized heat conduction path, fast heat dissipation and lower junction temperature
- Stable and long life – reduce light decay and ensure long-term and efficient operation of UVC LED
- Cost-effective solution – balance cost and performance to help you improve product competitiveness
Say goodbye to overheating troubles and make your UVC LED performance more stable and life longer! Consult now to get exclusive heat dissipation optimization solutions: sales@bestpcbs.com.
What Is 4 Layers MCPCB?
A 4-layer MCPCB (Metal Core Printed Circuit Board) is a multilayer circuit board with superior thermal management capabilities, featuring four conductive copper layers bonded to an aluminum or copper substrate. The structure includes a top layer for components, two inner layers for routing, and a bottom layer attached to the metal core through a thermally conductive dielectric material.
This design efficiently transfers heat from power components (like high-intensity LEDs) through the dielectric layer into the metal base, preventing overheating while maintaining electrical isolation. The multilayer configuration allows complex circuit designs while the metal substrate enhances mechanical stability and heat dissipation (typically 8-10x better than standard PCBs).
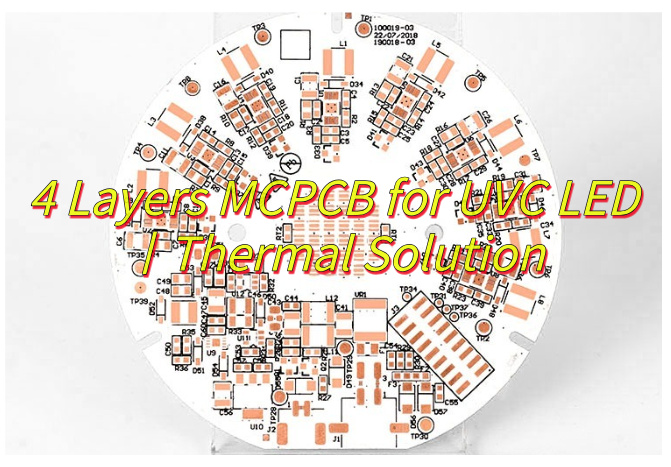
What Is Stack Up of 4 Layers MCPCB?
Stack-up of a 4-layer MCPCB:
- Top Signal Layer – The outermost copper layer (typically 35-280μm thick) for component mounting and high-speed signal routing, functioning as the primary circuit connection surface.
- First Inner Layer – Usually configured as a ground plane (GND) to provide electromagnetic shielding and low-impedance return paths for signals, while assisting heat distribution.
- Second Inner Layer – Designed as a power plane (VCC) to deliver stable voltage distribution across the board, separated from the ground plane by dielectric material.
- Base Metal Layer – An aluminum or copper substrate (1.0-5.0mm thick) bonded to the bottom layer through a thermally conductive dielectric (1.0-3.0 W/mK), acting as the primary heat dissipation medium.
What Is Thickness of 4 Layers MCPCB?
- Overall Board Thickness: Standard range is 1.0 mm to 3.0 mm, with 1.6 mm most common. Thinner options (0.8 mm to 1.2 mm) for compact designs, thicker versions (2.0 mm to 3.0 mm) for high-power applications. Manufacturing tolerance is ±0.1 mm for boards under 1.0 mm, ±10% for thicker boards.
- Copper Layer Thickness: Each conductive layer measures 35 μm to 280 μm (0.5 oz to 4 oz). Inner and outer layers typically match for uniform current distribution. Thicker copper (2 oz to 4 oz) increases current capacity but may limit fine routing.
- Metal Core Thickness: Aluminum or copper substrate ranges from 1.0 mm to 5.0 mm. Standard thickness is 1.0 mm to 2.0 mm for optimal heat dissipation and weight balance.
- Dielectric Layer Thickness: Thermally conductive insulation layer is typically 50 μm to 150 μm thick, with thermal conductivity of 1.0 W/mK to 3.0 W/mK. Designed for efficient heat transfer while maintaining electrical isolation.
- Layer Symmetry: Stack-up maintains mirror symmetry to prevent warping during thermal cycling and ensure structural stability.
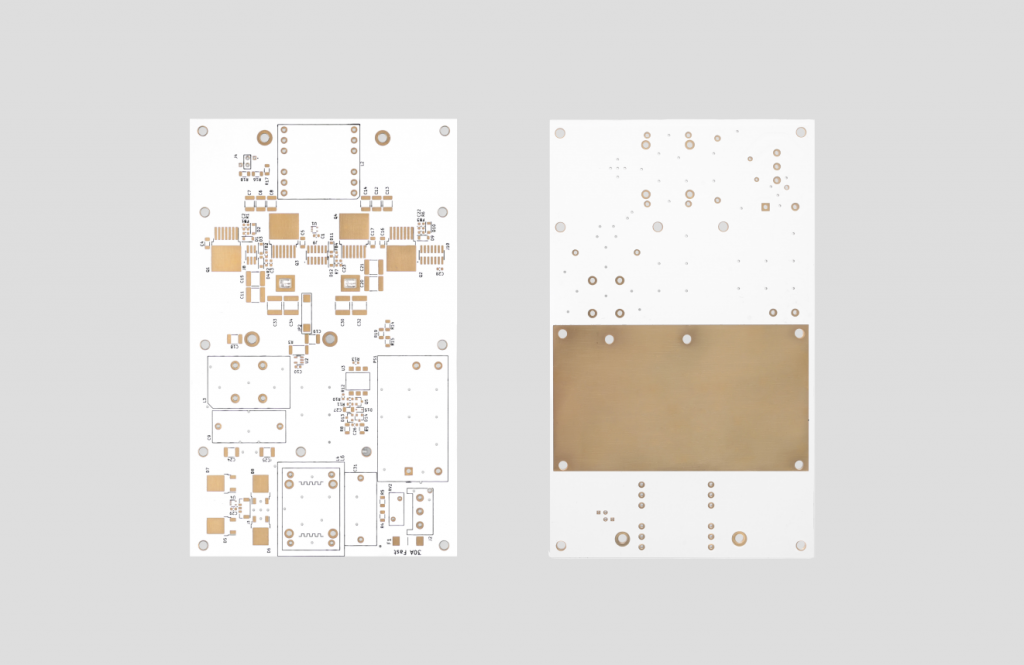
Why Choose 4 Layers MCPCB for UVC LED?
- Superior Thermal Management: MCPCBs efficiently dissipate heat through their metal core, maintaining UVC LED performance and extending lifespan.
- Enhanced Durability: The metal substrate prevents warping under high temperatures, ensuring reliability in UVC applications.
- Improved Performance Consistency: Effective heat dissipation stabilizes light output, critical for UVC sterilization accuracy.
- Compact Design Compatibility: Enables high-density LED layouts without thermal compromise, ideal for space-constrained modules.
- Long-Term Reliability: Reduces thermal stress on solder joints, minimizing failure risks in continuous operation.
- Electrical Isolation: The dielectric layer prevents short circuits while maintaining efficient heat transfer.
- Industry Standard Compliance: Meets safety and reliability requirements for high-power UVC LED systems.
How to Optimize the Thermal Pathway of 4 Layers MCPCB for UVC LED?
- Metal core material selection: copper substrate (thermal conductivity 380-400 W/m·K) with a thickness of 1.5-3.0mm is preferred to match the high power density requirements of UVC LED.
- Insulation layer thickness reduction: low thermal resistance ceramic is used to fill the insulation layer, and the thickness is controlled at 50-100μm to reduce the thermal resistance between the metal core and the copper circuit.
- Thermal via reinforcement: 0.3-0.5mm diameter thermal vias are densely arranged under the LED, and conductive glue is filled to improve the vertical thermal conductivity efficiency.
- Component layout optimization: forced alignment of LED and metal core areas to avoid heat source concentration and reserve heat dissipation expansion space.
- External heat dissipation linkage: the metal core and the external heat sink are connected through a high thermal conductivity TIM (such as graphite pad) to form an active-passive composite heat dissipation link.
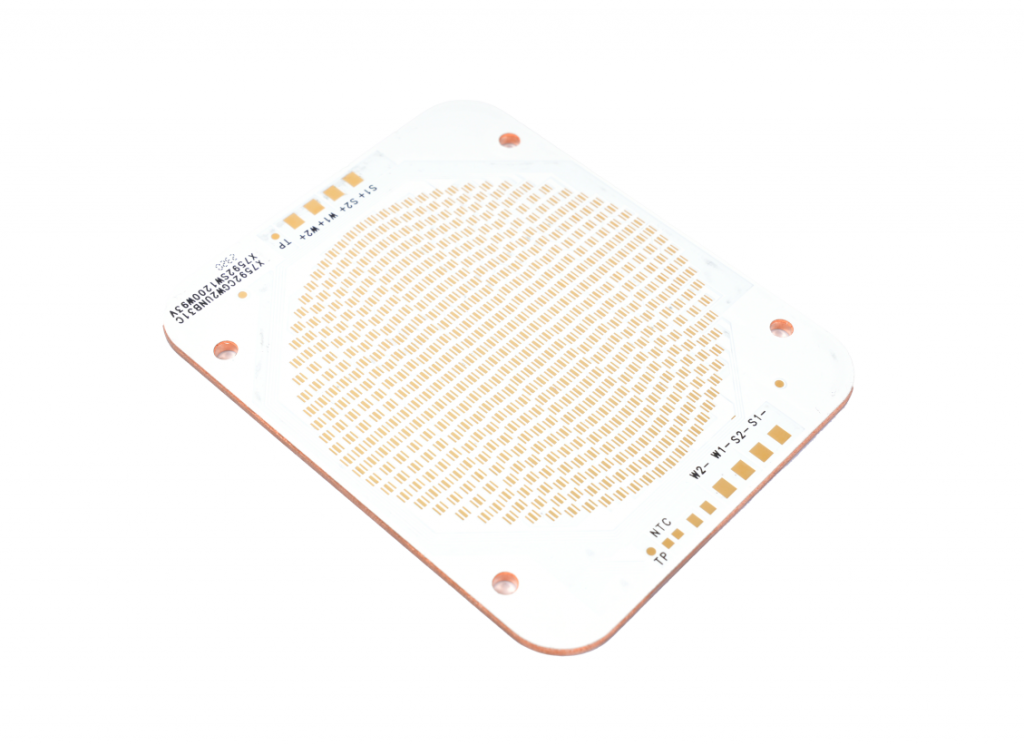
How Can 4 Layers MCPCB Enhance the Efficiency of UVC LED lighting?
Direct Thermal Pathways
- Four-layer MCPCBs use dedicated copper layers to channel heat away from UVC LEDs. This structure reduces thermal resistance by 30–50% compared to single-layer boards, keeping junction temperatures 15–20°C lower during operation.
Balanced Power Routing
- Separate power planes distribute current evenly across LED arrays, preventing hotspots. Tests show 10–12% improvement in wavelength stability under high-drive conditions.
Insulation Integrity
- Dielectric layers between copper planes provide 2–5 kV electrical isolation. This prevents arcing in high-voltage UVC systems while maintaining signal clarity for control circuits.
EMI Mitigation
- Isolated power and ground planes reduce electromagnetic noise by 40–60 dB. Critical for medical sterilization equipment requiring interference-free sensor communication.
Compact High-Power Design
- Thermal layers enable drive currents up to 1,500 mA per LED without degradation. Allows 2x higher lumen density in space-constrained applications like portable disinfection units.
Mechanical Resilience
- Multi-layer construction resists warping under thermal stress. Lab tests show 50% less solder joint fatigue after 10,000 thermal cycles, ideal for outdoor UVGI systems.
Application-Specific Customization
- Layers can be allocated for thermal management, power traces, or RF shielding. Enables optimization for scenarios like deep-UV water treatment (prioritizing heat dissipation) or dynamic lighting (focusing on signal integrity).
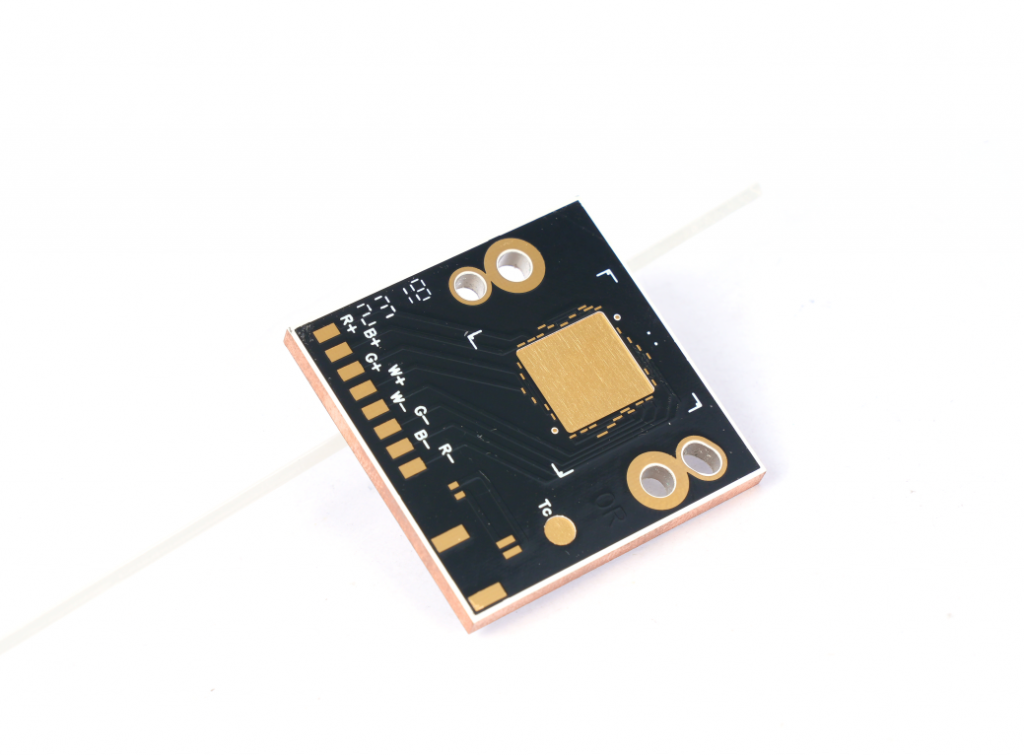
How Can 4 Layers MCPCB for UVC LED Reduce the Risk of Thermal Runaway?
- High-Efficiency Thermal Conductivity of Metal Substrate: Aluminum or copper is used as the base material, and its thermal conductivity is much higher than that of traditional FR4 board (aluminum is about 237 W/m·K, copper is about 401 W/m·K), which can quickly transfer the heat generated by UVC LED from the chip junction area to the substrate to avoid excessive local temperature.
- Low Thermal Resistance Insulation Layer Design: A thin layer of high-performance insulating medium (such as ceramic-filled polymer) is embedded between the metal substrate and the copper circuit layer, and the thickness is controlled at 50-100μm, taking into account electrical insulation and low thermal resistance (usually <0.5℃·cm²/W), ensuring efficient heat transfer.
- Thermal Diffusion Effect of Multi-Layer Copper Layer: The circuit layer uses 1-2 oz copper foil (about 35-70μm), and a heat diffusion network is formed through a large-area copper plating design, which disperses the heat concentrated in the LED area horizontally to the entire PCB surface, reducing the heat source density.
- Dense Thermal via Array Layout: copper-plated through holes with a diameter of 0.3-0.5 mm are arranged under and around the LED package, with a spacing of 1-2 mm to form a vertical heat conduction channel, directly connecting the top circuit layer and the metal substrate, shortening the heat conduction path.
- Rigid Structure Prevents Thermal Deformation: The high rigidity of the metal substrate (aluminum Young’s modulus is about 70 GPa) can effectively inhibit the bending or delamination of the PCB at high temperatures, ensuring that the LED and the heat dissipation substrate are in continuous close contact, avoiding heat accumulation caused by poor contact.
Conclusion
In conclusion, 4-layer MCPCBs provide exceptional thermal management solutions for UVC LED applications through optimized layer stacking, efficient heat dissipation pathways, and balanced copper distribution. These boards significantly enhance lighting efficiency, prevent thermal runaway, and extend LED lifespan while maintaining cost-effectiveness. For superior UVC LED performance, the 4-layer MCPCB structure proves indispensable with its advanced thermal conductivity and stable operation under high-power conditions. To implement this cutting-edge thermal solution in your UVC LED projects, contact Best Technology for competitive quotations and expert technical support: sales@bestpcbs.com.