Why choose China LED PCB for your project? This guide examines cost-effective production methods, accelerated delivery protocols, and design customization feasibility within China LED PCB industry, addressing decision-making factors from pricing models to technical validation.
Best Technology delivers China LED PCB manufacturing with 24-hour rapid prototyping supported by three dedicated quick-response lines. Our automated DFM analysis system processes design files within 90 minutes, identifying thermal management conflicts or impedance mismatches before manufacturing. Localized material warehouses maintain 48+ substrate variants, including aluminum-core boards (1.0â5.0mm thickness) and high-frequency Rogers 4350B, enabling immediate processing without procurement delays. Integrated AOI/X-RAY inspection stations achieve 99.98% first-pass yield, combining 10ÎŒm alignment checks with void detection (<5% IACS compliance). Production lines operate under IATF 16949 protocols, executing 4-hour batch changeovers for mixed LED configurations (SMD, COB, high-bay). Real-time logistics coordination through bonded ports ensures global shipments within 72 hours of final testing. Clients benefit from concurrent engineering support â our team resolves EMI/thermal issues during fabrication, eliminating post-production reworks. Continuous capacity scaling maintains 15% reserve throughput for urgent orders. Welcome to contact us: sales@bestpcbs.com.
What Is China LED PCB?
A China LED PCB refers to a printed circuit board specifically designed and manufactured in China to support light-emitting diode (LED) applications. These boards are engineered to manage electrical connectivity, thermal dissipation, and mechanical stability for LED systems. Utilizing materials like FR-4, aluminum substrates, or ceramic composites, Chinese manufacturers optimize these PCBs for high-power LED lighting, automotive headlights, signage, and consumer electronics. Advanced production techniques include precision etching, solder mask application, and surface finishes such as HASL (Hot Air Solder Leveling) or ENIG (Electroless Nickel Immersion Gold) to ensure durability and efficient heat transfer. Chinaâs LED PCB industry leverages scalable manufacturing infrastructure, cost-effective solutions, and compliance with international certifications like UL and RoHS, making it a global supplier for both standard and custom LED lighting solutions. Technical emphasis is placed on layer stacking, copper thickness optimization, and dielectric material selection to enhance luminous efficiency and longevity under varying operational conditions.
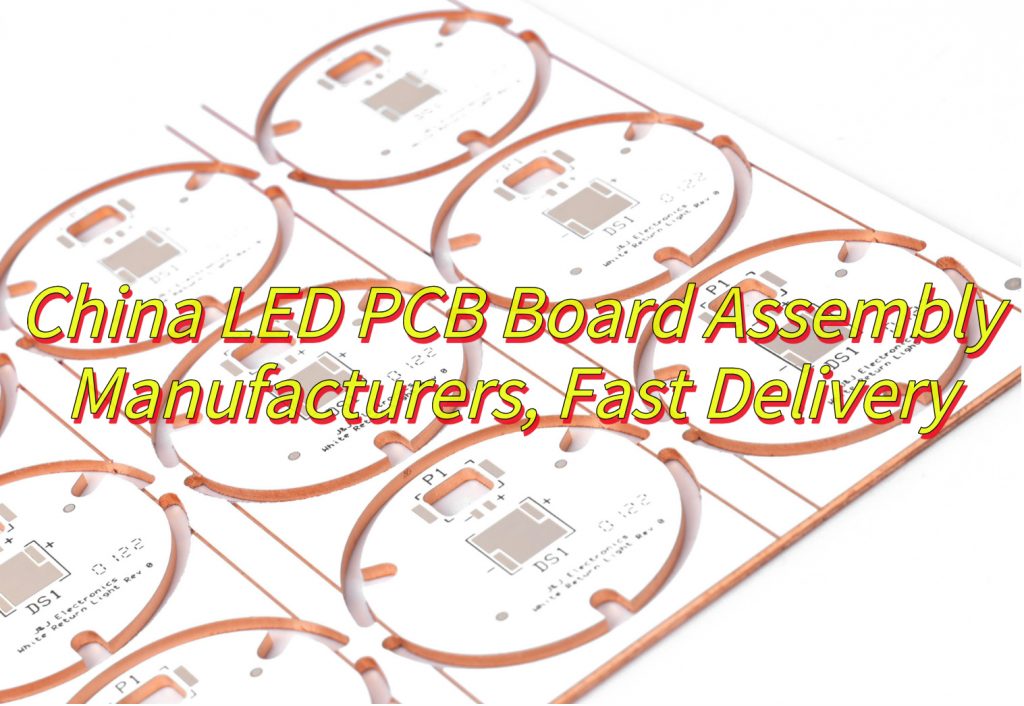
What Are Advantages of China LED PCB?
Advantages of China LED PCB:
- Advanced Thermal Management Solutionsâ – Chinese manufacturers employ aluminum-core substrates and ceramic composites to achieve superior heat dissipation, critical for maintaining LED performance in high-power applications like automotive lighting and industrial systems.
- Cost-Effective Production Scalingâ – Leveraging mature industrial clusters and automated manufacturing processes, China delivers competitively priced LED PCBs without compromising quality, supporting global demand for consumer electronics and commercial displays.
- Compliance with International Sustainability Standards â- Adoption of RoHS-compliant materials and energy-efficient production methods aligns with global environmental regulations.
- Customization for Smart Lighting Systemsâ – Integrated circuit designs enable compatibility with ADB (Adaptive Driving Beam) modules, meeting evolving requirements for automotive and smart city infrastructure.
- Rapid Technological Iteration Capabilitiesâ – Continuous R&D investments drive innovations in Micro LED miniaturization and ultra-fine pitch displays, positioning Chinese suppliers at the forefront of high-resolution visual solutions.
- Robust Supply Chain Integrationâ – Proximity to raw material suppliers and streamlined logistics networks ensure reliable component sourcing and reduced lead times, particularly for large-scale OEM/ODM projects.
- Diverse Application Adaptabilityâ – From automotive headlights to virtual production studios, Chinese LED PCBs demonstrate versatility across industries, supported by modular designs and multi-layer stacking techniques.
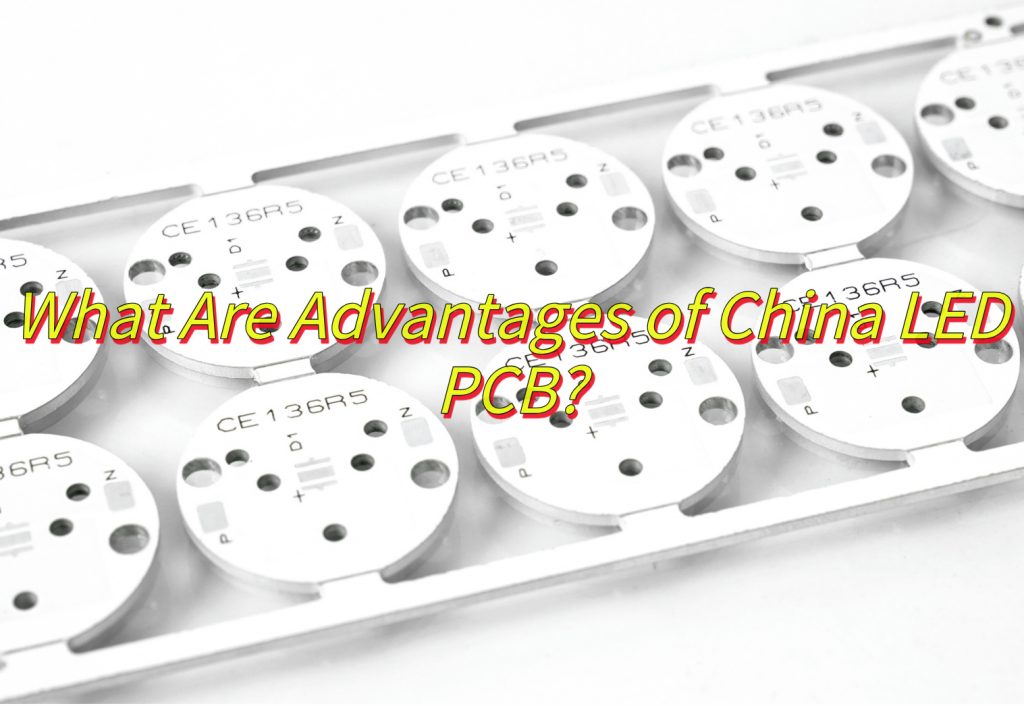
Why Choose China LED PCB Assembly Manufacturers?
Here are reasons why choose China LED PCB assembly manufacturers:
âAdvanced Material Engineeringâ
- Chinese manufacturers utilize aluminum-core substrates and ceramic composites to achieve thermal conductivity up to 8W/m·K, essential for high-power LED applications such as automotive headlights and industrial lighting systems. These materials prevent thermal degradation, ensuring LED longevity under continuous operation.
Precision Manufacturing Standards
- Adherence to IPC-A-610F assembly guidelines and ISO 9001-certified processes guarantees consistent quality, with automated optical inspection (AOI) systems detecting defects at rates below 0.08%. Strict DFM (Design for Manufacturing) analysis preemptively resolves layout conflicts, reducing post-production revisions.
Cost-Efficient Production Scaling
- Integrated industrial clusters in regions like Guangdong enable bulk procurement of raw materials, lowering unit costs by 20-35% compared to Western counterparts. Economies of scale support high-volume orders exceeding 500,000 units/month without compromising lead times.
Certification Compliance
- Manufacturers hold IATF 16949 for automotive-grade modules and ISO 13485 for medical lighting, meeting stringent EU RoHS and REACH regulations for global market access. UL-recognized PCBs ensure safety compliance in North American markets.
R&D-Driven Innovationâ
- Investment in Micro LED and COB (Chip-on-Board) technologies enables pixel pitches as fine as 0.4mm, catering to 4K commercial displays and virtual production studios. IoT-integrated designs support wireless dimming and color temperature adjustments for smart city infrastructure.
Agile Supply Chain Networksâ
- Proximity to Shenzhenâs electronics hubs facilitates 24-hour component sourcing, with JIT (Just-in-Time) inventory systems reducing material shortages during peak demand. Dual sourcing strategies mitigate geopolitical trade risks for critical semiconductors.
Comprehensive Testing Protocols
- End-to-end validation includes thermal cycling (-40°C to 150°C), 72-hour burn-in testing, and IP68 environmental stress screening to ensure reliability in harsh conditions. In-circuit testing (ICT) and flying probe systems verify electrical parameters with ±1% tolerance.
Customization Flexibilityâ
- Multi-layer stack-ups (up to 32 layers) and hybrid rigid-flex designs address space-constrained applications like wearable devices and aerospace instrumentation. Engineers optimize copper weights (2-12 oz) and solder mask textures for specific luminosity and EMI shielding requirements.
Sustainability Initiativesâ
- Closed-loop water recycling systems and lead-free HASL surface finishes reduce ecological impact, with 98% material utilization rates in high-volume production. Solar-powered facilities align with carbon neutrality targets for eco-conscious clients.
Global Logistics Supportâ
- Dedicated customs brokerage teams expedite shipments to major ports, achieving 99.5% on-time delivery rates for EU and North American clients through bonded warehouse networks. Real-time SAP tracking integrates with client ERP systems for supply chain transparency.
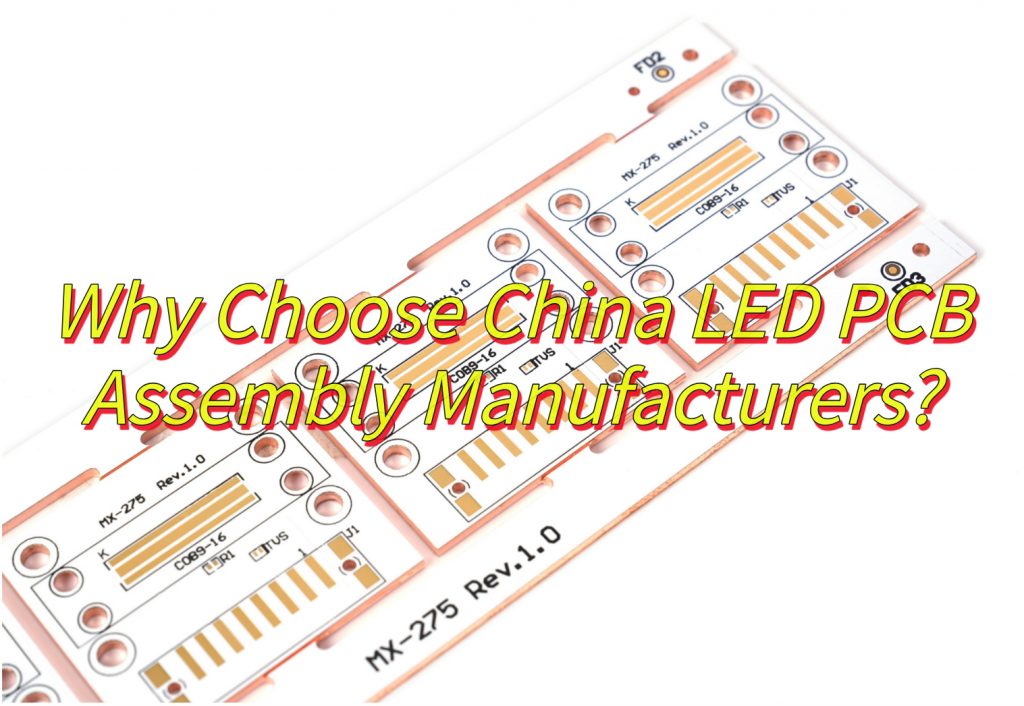
How to Get a Cheap LED PCB Quote from China Manufacturers?
Strategies to how to get a cheap China LED PCB:
- Utilize Online Quotation Toolsâ – Submit detailed specifications through manufacturersâ web-based quote systems to receive instant pricing estimates.
- Optimize PCB Design Specificationsâ – Reduce costs by minimizing layer counts (4-6 layers for standard LED applications) and selecting FR-4 standard substrates unless high thermal demands require premium aluminum cores. Standardized panel sizes (18âĂ24â) maximize material utilization rates.
- Request Volume Discount Structuresâ – Manufacturers typically offer tiered pricing models, with unit costs decreasing 12-18% for orders exceeding 10,000 pieces. Confirm breakpoints for bulk pricing during initial negotiations.
- Compare Supplier Quotes Strategically – âEvaluate multiple manufacturers through B2B platforms like Made-in-China, cross-referencing unit prices against included services (DFM analysis, functional testing). Prioritize suppliers offering free engineering reviews.
- Negotiate Component Sourcing Optionsâ – Choose partial turnkey services to leverage existing component inventories, reducing procurement lead times by 7-10 days. Confirm alternate part approvals for non-critical components to avoid sole-source markup.
- Verify Certifications Earlyâ – Ensure manufacturers hold ISO 9001 and UL certifications for your target markets. Non-certified suppliers may appear cheaper initially but risk non-compliance penalties during customs clearance.
- Clarify Logistics Responsibilitiesâ – Choose EXW (Ex-Works) terms to maintain control over shipping methods and customs brokerage. Consolidate shipments through freight forwarders for orders under 500kg to reduce per-unit logistics costs.
- Request Prototyping Subsidiesâ – Leading manufacturers often waive NRE (Non-Recurring Engineering) fees for prototype orders that convert to production batches within 60 days, lowering upfront development costs.
- Monitor Material Market Trendsâ – Time orders during copper foil price dips (typically Q2-Q3) to secure better rates. Manufacturers adjust quotes based on raw material indices updated weekly.
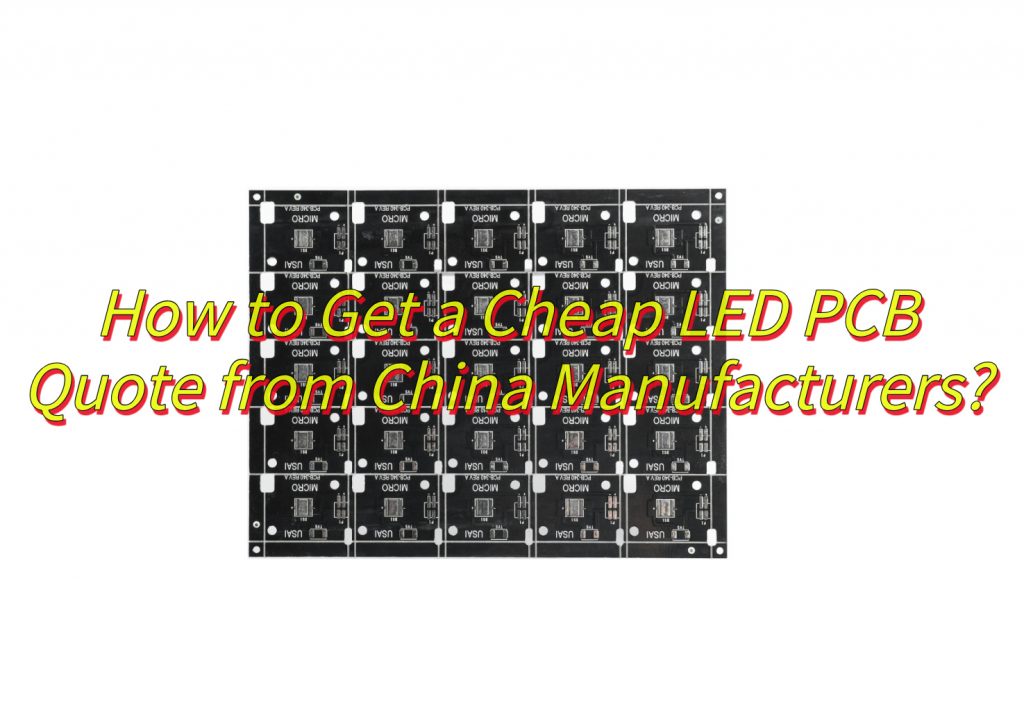
How to Shorten LED PCB Lead Time with Chinese Manufacturers?
Here is how to shorten the lead time of China LED PCB:
Streamline Order Processing and Documentation
- Submit Complete Production Files Upfront: Provide Gerber files, BOM lists, and assembly drawings in one batch to minimize back-and-forth corrections. Clearly specify solder mask colors, surface finishes (e.g., HASL, ENIG), and other technical requirements.
- Designate a Single Point of Contact: Avoid delays from multi-department coordination by assigning one person to liaise with the manufacturer via email or instant messaging tools for real-time updates.
Simplify Design and Reduce Process Complexity
- Adopt Standardized Layouts: Prioritize single-sided or double-sided PCBs over multilayer designs (e.g., 6+ layers). If high-density interconnects are unavoidable, negotiate partial HDI production for critical sections only.
- Avoid Specialty Materials/Processes: Use domestically sourced FR-4 substrates and standard finishes like HASL instead of immersion gold or OSP to accelerate material sourcing.
Partner with Agile Manufacturers
- Evaluate Production Flexibility: Select factories with multiple automated lines (e.g., plating, etching) that can reprioritize orders during downtime. Request historical lead time data to gauge reliability.
- Leverage Regional Supply Chains: Engage manufacturers in the Pearl River Delta (Shenzhen) or Yangtze River Delta for faster access to component suppliers and logistics hubs.
Negotiate Expedited Production and Shipping
- Pay Premium for Rush Orders: Offer 10â20% extra to shorten key steps (e.g., drilling, plating). For example, a 7-day lead time might reduce to 4â5 days with dedicated line allocation.
- Choose Air Freight: For orders under $5,000, negotiate with suppliers to cover partial air shipping costs (common for maintaining client relationships), cutting delivery from 15â20 days to 3â5 days.
Implement Parallel Production and Quality Checks
- Overlap Inspection with Fabrication: Conduct flying probe testing and AOI checks during etching to catch defects early, avoiding post-production rework.
- Early Third-Party Validation: Engage labs to test solderability and thermal stress after etching, enabling immediate process adjustments if issues arise.
Foster Long-Term Collaboration and Inventory Sharing
- Sign Strategic Agreements: Lock in priority scheduling and inventory pooling via annual contracts. For example, pre-reserve capacity or stock common specs (e.g., 1.6mm FR-4) for urgent orders.
- Co-Manage Safety Stock: Allow suppliers to pre-produce generic modules (e.g., driver boards) based on purchase history, enabling rapid fulfillment by only customizing LED sections per order.
Leverage Digital Tools for Efficiency
- Integrate EDI Systems: Sync order, production, and shipping data with suppliersâ systems to eliminate manual entry delays. Auto-trigger production scheduling upon order confirmation.
- Use Free DFM Software: Pre-screen designs with supplier-provided tools to fix issues like trace/space violations before formal submission, preventing production pauses.
Standardize Modules and Plan Alternatives
- Design Modular Architectures: Separate LED arrays into scalable modules (e.g., driver + light engine). Stock standard drivers and produce custom light engines on demand, halving lead times.
- Create Approved Alternate Parts Lists: Collaborate with suppliers to pre-qualify substitute components (e.g., equivalent LEDs, capacitors) to avoid delays from primary material shortages.
What’s the Real Cost of LED PCB Assembly from China vs Local Suppliers?
Here are price comparison between China LED PCB and Local LED PCB:
1. Direct Manufacturing Costs: China vs Local Suppliers
- China: Labor-intensive steps (e.g., SMT placement, through-hole assembly) cost $0.003â$0.008 per pad for LED PCBs, depending on component density. A 100-piece order with 500 pads per board might total $150â$400 for assembly alone.
- Local Suppliers (e.g., U.S./Europe): Same work ranges from $0.01â$0.02 per pad, tripling assembly costs to $500â$1,000 for the same 100-piece batch.
2. Material Sourcing and PCB Fabrication
- China: Full-service factories bundle PCB fabrication and assembly. A 1.6mm thick, 2-layer FR-4 LED board with white solder mask costs $0.10â$0.30 per unit for 1,000+ pieces, including materials like 35”m copper and HASL finish.
- Local Suppliers: PCB fabrication alone costs $0.50â$1.50 per unit for equivalent specs, excluding assembly. Material markups (e.g., Rogers/Isola substrates) add 20â50% if specified.
3. Logistics and Duties for China Sourcing
- Shipping: Air freight adds 2â5 per board for express 3â5 day delivery, while sea freight reduces this to $0.30â$1.00 per unit but takes 3â4 weeks.
- Tariffs: LED products under HTS code 9405.42 face 0â6% duties depending on regional trade agreements (e.g., U.S.-China Phase One deal).
4. Quality Control and Rework Risks
- China: Mid-tier factories charge 2â5% of order value for AQL 2.5 inspection and functional testing. Failure rates for LED alignment or thermal issues average 1â3%, incurring $50â$150 per 1,000 boards in rework.
- Local Suppliers: Typically include free AQL 1.0 inspection, with failure rates under 0.5%, minimizing rework costs but offset by higher upfront prices.
5. Tooling and NRE Fees
- China: Stencil and fixture costs average $150â$300 one-time fees, amortized over 5,000+ units. Prototyping (5â10 boards) adds $200â$500 for engineering support.
- Local Suppliers: NRE fees start at $500â$1,000, with prototyping priced at $300â$800 for equivalent services, reflecting higher labor rates.
6. Volume Discounts and Scalability
- China: Price breaks occur at 500, 1,000, and 5,000 units. A 10,000-unit order might drop per-unit assembly costs to $0.002â$0.005 per pad vs. $0.01â$0.015 locally.
- Local Suppliers: Discounts plateau at 1,000 units, with minimal per-unit reduction beyond 5,000 pieces, limiting scalability for high-volume projects.
7. Intellectual Property and Compliance Costs
- China: NDA enforcement and IP audits add 1,000â3,000 annually. RoHS/REACH compliance certification costs $500â$1,000 per product family.
- Local Suppliers: IP protection is often included in contracts, while compliance certifications average $200â$500, reflecting regional regulatory efficiency.
8. Total Cost of Ownership Comparison
- China Example: 1,000 LED PCBAs (2-layer, SMT assembly, air freight) =Â $800(PCBs)+$2,500 (assembly) +Â $1,200(logistics/duties)+$100 (inspection) = $4,600 total.
- Local Example: Same project =Â $1,500(PCBs)+$8,000 (assembly) +Â 0(logistics)+0 (inspection) = $9,500 total.
- Savings: China sourcing offers 50â70% lower TCO for batches â„500 units, despite added logistics and compliance overhead.
Do China LED PCB Suppliers Offer Free Gerber File Review Services?
Yes, many China LED PCB suppliers like Best Technology offer free Gerber file review services to ensure designs meet manufacturability standards before production begins. Below is a detailed breakdown of how this service works, its limitations, and best practices for leveraging it effectively:
Purpose of Free Gerber Reviews
Design for Manufacturing (DFM) Checks: Suppliers analyze Gerber files to identify potential issues such as:
- Inadequate trace/space clearances (e.g., <5mil for standard LED boards).
- Missing solder mask layers or improper silkscreen placement.
- Incompatible hole sizes (e.g., drill diameters exceeding 80% of PCB thickness).
- Incorrect impedance control settings for high-speed LED driver circuits.
- Cost Avoidance: Early detection of errors prevents rework, material waste, and production delays.
Service Scope and Exclusions
Included in Free Reviews:
- Layer stack-up validation.
- Drill file accuracy (tool sizes, plating requirements).
- Basic electrical clearance checks.
Typically Excluded:
- Advanced thermal analysis or signal integrity simulations.
- Full redesign assistance (e.g., routing adjustments, component placement).
- Compliance testing (e.g., UL certification, RoHS documentation).
Turnaround Time and Process
- Standard Timeline: 24â48 hours for most suppliers, depending on file complexity.
- Expedited Options: Some factories offer 4â6 hour reviews for urgent orders (may charge 20â50 for priority handling).
- Delivery Method: Results are shared via email or an online portal with annotated Gerber files highlighting issues.
Conditions for Free Access
- Order Commitment: Free reviews are usually contingent on a confirmed quote or intent to place an order.
- File Format Requirements: Accepted formats include Gerber RS-274X, ODB++, or IPC-2581. Legacy formats (e.g., Gerber X2) may require conversion fees.
- Complexity Thresholds: Free reviews apply to standard LED PCBs (e.g., single/double-sided, through-hole components). HDI, flex, or metal-core boards often require paid engineering reviews (50â200).
How to Request a Review
- Pre-Quote Submission: Attach Gerber files when requesting a quotation to trigger automatic DFM analysis.
- Supplier Portals: Larger manufacturers (such as Best Technlogy) offer free online tools for instant DFM feedback.
- Direct Engagement: Email files to sales engineers with a clear request: âPlease conduct a free DFM review prior to formal quotation.â
Potential Pitfalls to Avoid
- Automated-Only Checks: Ensure a human engineer verifies results, as purely automated tools may miss contextual issues (e.g., LED footprint alignment).
- Language Barriers: Work with suppliers offering English-speaking engineering support to clarify design intent.
Alternatives to Free Reviews
- Third-Party DFM Tools: Use free software like KiCadâs DRC or PCB Checker to self-audit files before submission.
- Paid Engineering Support: For mission-critical projects, budget 50â200 for detailed reviews by specialists.
Negotiating Enhanced Support
- Prototype Runs: Request a free âNPI (New Product Introduction) packageâ including 1â2 Gerber reviews with prototype orders.
- Long-Term Agreements: Secure annual contracts with monthly DFM quotas (e.g., 10 free reviews/month) in exchange for volume commitments.
Can China LED PCB Manufacturers Meet My Custom Design Requirements?
Yes, China LED PCB manufacturers can meet custom design requirements, offering flexibility in specifications, materials, and production processes. Below is a detailed analysis of their capabilities, limitations, and best practices for collaborating effectively:
Design Customization Capabilities
- Layer Count and Stack-Up: Capable of producing single-layer to 12+ layer boards, with options for blind/buried vias and controlled impedance for high-speed LED drivers.
- Material Selection: Access to specialized substrates like aluminum-backed PCBs for thermal management, FR-4 for cost efficiency, and high-frequency materials (e.g., Rogers 4350B) for RF applications.
- Surface Finishes: Offer HASL, ENIG, immersion tin, and OSP finishes to suit soldering requirements and environmental resistance.
- Component Placement: Support for 01005 passives, QFNs, BGAs, and through-hole LEDs with automated optical inspection (AOI) for accuracy.
Specialized Processes for LED Applications
- Thermal Vias and Copper Cores: Manufacturers routinely incorporate thermal vias (e.g., 0.2mm diameter, 1:1 aspect ratio) and copper-core layers to dissipate heat from high-power LEDs.
- Optical Clearance: Precision routing to maintain 0.5mm+ clearance between LED pads and copper traces to prevent light bleed.
- White Solder Mask: Standard offering for LED boards, with options for matte finishes to reduce glare in lighting applications.
Design Collaboration Workflow
- DFM Reviews: Free analysis of Gerber files to flag issues like trace/space violations (e.g., <5mil for standard LED boards) or missing solder mask layers.
- Engineering Support: Larger factories employ in-house engineers to suggest design optimizations, such as panelization strategies to reduce costs.
- Prototyping: Rapid turnaround (24â72 hours) for 5â10 piece prototype batches using SMT lines dedicated to small orders.
Quality Control for Custom Designs
- Electrical Testing: Flying probe testing (FPT) for prototypes and dedicated fixtures for high-volume runs, ensuring continuity and isolation resistance meet IPC-A-600 standards.
- Thermal Cycling: Optional stress testing (-40°C to +125°C) for automotive or outdoor LED applications, typically costing 50â150 per batch.
- Cross-Section Analysis: Destructive testing to validate plating thickness and layer adhesion, often included in NPI (New Product Introduction) packages.
Limitations and Risk Mitigation
- Minimum Order Quantities (MOQs): Custom designs may require 50â100 piece MOQs due to setup costs for specialized tooling (e.g., stencils, fixtures).
- Lead Time Extensions: Custom stack-ups or exotic materials (e.g., ceramic substrates) can add 3â5 days to lead times.
- Language Barriers: Use suppliers with English-speaking engineers to clarify design intent during reviews.
Cost Considerations
- NRE Fees: One-time charges for stencils (50â150) and fixtures (100â300), amortized over 1,000+ units.
- Material Premiums: Aluminum-backed PCBs cost 20â40% more than FR-4, while Rogers 4350B adds 50â100% to material costs.
- Volume Discounts: Per-unit costs drop 30â50% when scaling from 100 to 1,000 pieces, with further reductions at 5,000+ units.
How to Ensure Success with Custom Designs
- Provide Detailed Specifications: Include thermal requirements, optical clearance rules, and mechanical constraints in the RFQ.
- Request Sample Runs: Order 5â10 pieces for validation before full production, especially for rigid-flex or HDI designs.
- Secure Intellectual Property: Use NDAs and watermark sensitive files during the quoting phase.
By aligning design complexity with supplier capabilities and proactively addressing potential risks, buyers can leverage Chinaâs manufacturing ecosystem to produce high-quality, customized LED PCBs at competitive costs.
Tags: China LED PCB, China LED PCB Board, China LED PCB Board Assembly Manufacturers