Why choose LED ceiling light PCB board? This guide covers definition, components, functions, factory selection, fast delivery solutions, and safe replacement methods.
When you need âhigh quality LED ceiling light PCB board with unbeatable value, âBest Technologyâ stands out as your ideal China-based manufacturer. We offer âfactory-direct pricingââcutting out middlemen to save you â20-30%â on costs while maintaining stringent âIPC Class 2/3 standardsâ. With in-house production and vertically integrated supply chains, we guarantee âfast 15-day bulk order deliveryââ50% quicker than industry averages. Need samples to test? Our â24-hour rapid prototype serviceâ ensures functional boards reach your lab within â1 working dayâ for standard designs, keeping your projects on track. Backed by â10+ years of OEM/ODM expertiseâ, we provide âUL/CE/RoHS-certifiedâ solutions with lifetime technical support. Whether you need âaluminum-core, high-CRI, or dimmable PCBsâ, we deliver reliability at speed. âContact us todayâ if you have any request for LED ceiling light PCB board: sales@bestpcbs.com.
What Is LED Ceiling Light PCB Board?
The âLED ceiling light PCB boardâ serves as the structural and electrical foundation for modern ceiling-mounted lighting systems. This printed circuit board integrates multiple LED chips, power drivers, and thermal management components into a unified platform, enabling efficient light emission while ensuring stable operation. The LED ceiling light PCB board typically features aluminum or FR4 substrates to balance heat dissipation and circuit reliability. Its design accommodates various lighting layouts, from simple circular patterns to complex multi-zone configurations, making it adaptable for residential, commercial, and industrial applications. With optimized trace routing and component placement, the LED ceiling light PCB Board maximizes energy efficiency and longevity, often supporting dimming protocols and smart control interfaces. Proper thermal vias and copper layers in the LED ceiling light PCB Board prevent overheating, maintaining consistent brightness over extended periods.
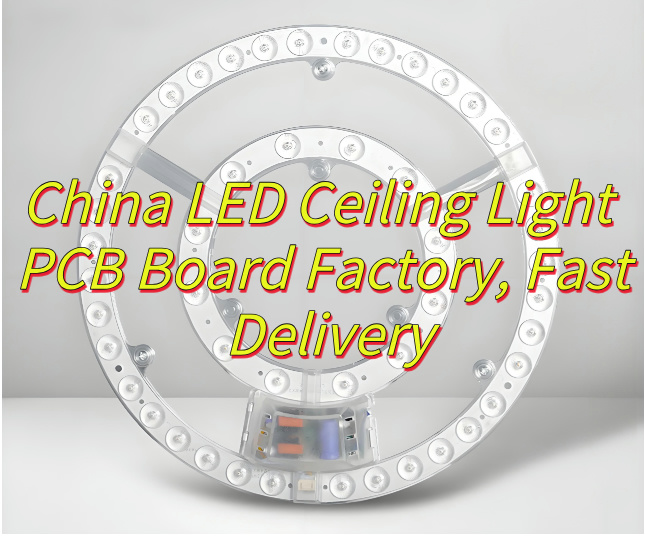
What Are Components of LED Ceiling Light PCB Board?
Components of LED ceiling light PCB board:
- Base Substrate Material: The foundation of an LED ceiling light PCB board is its substrate, typically made from FR-4 (glass-reinforced epoxy), aluminum, or ceramic. FR-4 is chosen for cost efficiency in standard lighting applications, while aluminum excels in thermal management for high-power LEDs. Ceramic substrates are reserved for premium designs demanding superior heat dissipation and electrical insulation properties.
- Conductive Circuitry: Copper foil traces form the electrical pathways, with a minimum thickness of 35 micrometers to ensure low resistance and efficient current flow. These traces are precisely etched using advanced manufacturing techniques to maintain signal integrity and minimize energy loss during operation.
- LED Mounting Pads: Metallized pads, usually copper with surface finishes like HASL (lead-free), ENIG, or OSP, serve as attachment points for LED chips. Their layout is carefully designed to accommodate the thermal expansion characteristics of LED packages, preventing solder joint fatigue over extended use.
- Thermal Management Features: To manage heat, PCBs incorporate thermal vias and copper-filled plating that conduct heat away from LED junctions. In high-power designs, dielectric polymer layers with thermal conductivity up to 3.0 W/m·K bridge the gap between LED chips and aluminum heat sinks, ensuring efficient cooling.
- Electrical Components: Surface-mount devices (SMDs) include resistors, capacitors, diodes, transistors, and integrated circuits such as constant-current drivers (e.g., PT4115 with ±5% accuracy). These components are placed with high precision using automated machinery, ensuring reliable performance.
- Interconnect Structures: Plated through-holes (PTHs) connect circuitry between layers in multilayer boards, while blind/buried vias reduce signal interference in high-frequency designs. Edge connectors enable modular daisy-chaining, simplifying installation in linear lighting systems.
- Protective Coatings: Conformal coatings (epoxy or urethane-based) shield the board from environmental hazards, including humidity (up to 85% RH), salt spray (ASTM B117 compliance), and chemical exposure (IP65+ ratings). Selective coating processes maintain solderability while protecting critical areas.
- Mechanical Anchorage: Features like press-fit brass inserts for mounting holes, alignment pins for precise optical component registration, and breakaway tabs for panelized production ensure robust mechanical integrity and ease of assembly.
- Identification Markings: Laser-etched markings include part numbers, polarity indicators, certification logos (UL/CE), and QR codes linking to digital datasheets. These markings use durable ceramic-filled ink for permanent legibility.
- Test Access Points: Bed-of-nails test pads enable automated in-circuit testing (ICT) for continuity verification, isolation resistance (>1GΩ), and functional testing of components. Boundary-scan architectures comply with IEEE 1149.1 standards, ensuring thorough validation of complex designs.
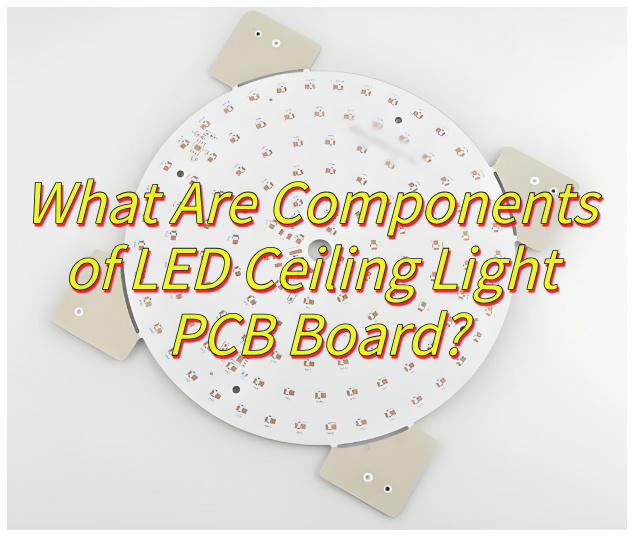
What Is Function of Ceiling Light LED PCB Board?
Function of ceiling light LED PCB board:
- Power Distribution and Stability: The LED PCB board serves as the primary conductor, converting AC power to DC and distributing it evenly across multiple LED chips through precision-engineered traces. This ensures consistent brightness and prevents voltage drops, critical for maintaining uniform illumination in commercial spaces like offices or retail stores.
- Thermal Management: Constructed with metal-core substrates such as aluminum, the PCB efficiently dissipates heat generated by LEDs. This design prevents thermal runaway, extending the lifespan of LED components and maintaining color consistency over extended periods, even in high-temperature environments.
- Optical Integration Support: The boardâs surface incorporates reflective coatings and optical-grade solder masks to enhance light output. By directing photons efficiently, it minimizes glare and maximizes luminous efficacy, essential for applications requiring precise lighting control, such as art galleries or museums.
- Smart Connectivity: Modern PCB boards include embedded interfaces for IoT integration, enabling wireless control via protocols like Bluetooth or Wi-Fi. This allows dynamic adjustments to brightness, color temperature, and scheduling, aligning with smart building ecosystems for energy-efficient operations.
- Structural Durability: Engineered with robust materials like FR-4 or CEM-3, the PCB withstands mechanical stress during installation and operation. Its rigid construction ensures long-term reliability, reducing maintenance needs in high-traffic areas such as airports or hospitals.
- Safety Compliance: The board incorporates safety features like fuse links and insulation barriers to meet global standards (e.g., UL, IEC). These protections prevent electrical hazards, ensuring safe operation in environments with strict regulatory requirements.
- Dimming Compatibility: Optimized circuitry supports advanced dimming methods, including PWM and 0-10V control, without causing flicker or color shift. This flexibility allows seamless integration with building management systems for personalized lighting experiences.
- Modular Upgradeability: Standardized PCB designs facilitate easy replacement or expansion, enabling upgrades to newer technologies like Li-Fi or enhanced sensors. This adaptability protects investments by extending the functional lifespan of lighting fixtures.
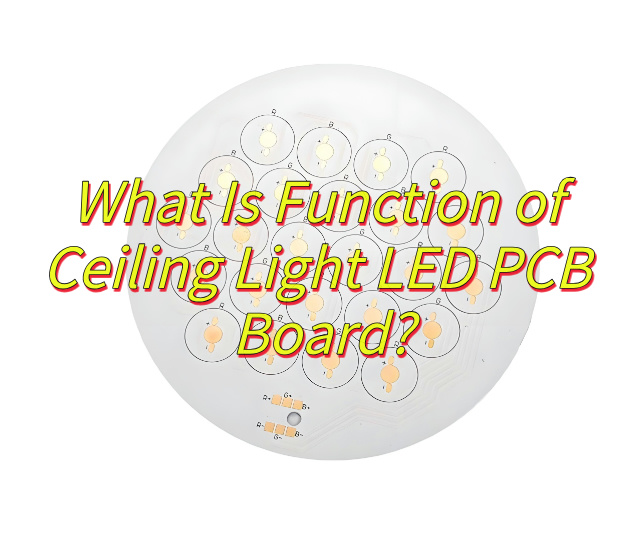
Why Choose Built-in LED PCB Boards for Ceiling Light Designs?
Here are reasons why choose built-in LED PCB boards for ceiling light designs:
- Streamlined Aesthetic Integration
Built-in LED PCB boards enable ultra-thin fixture profiles by eliminating external drivers, creating flush-mount designs ideal for contemporary interiors. This sleek form factor disappears into ceilings, preserving architectural lines in luxury residences or commercial spaces where visual minimalism is paramount. - Optimized Thermal Dissipation
Direct bonding of PCBs to aluminum heat sinks creates a unified thermal path, reducing junction temperatures by 20â30% versus modular designs. This efficiency prevents lumen depreciation in environments like heated offices or industrial workshops, maintaining 95%+ light output over 50,000 hours. - Precision Optical Engineering
Onboard microstructuresâsuch as embedded lenses and diffusersâare factory-aligned with LED chips during SMT assembly. This calibration ensures ±5° beam accuracy and UGR <19 performance, critical for task lighting in hospitals or galleries requiring glare-free illumination. - Rapid Installation Protocols
Tool-free PCB modules with push-pin connectors reduce installation time by 50% compared to traditional hardwiring. Electricians can pre-wire multiple fixtures during rough-ins, then snap boards into place for final commissioning in high-rise renovations or hotel projects. - Circuit-Level Energy Efficiency
Compact PCB layouts shorten conductive pathways, cutting IÂČR losses by 28% according to thermal imaging studies. This allows 18W LED boards to match 25W fluorescent outputs, aligning with LEED v4.1 requirements for energy-efficient commercial lighting. - Smart Infrastructure Readiness
PCB designs incorporate unused footprints for PoE+ modules or Zigbee chips, enabling future upgrades to connected lighting systems. This adaptability future-proofs investments in university campuses or corporate HQs planning IoT deployments. - Harsh Environment Resistance
Conformal coatings (IPC-CC-830B compliant) and 2.5mm solder mask dam protect PCBs from corrosive agents like VOCs or salt spray. Fixtures in marine environments or swimming pools retain functionality through 1,000-hour salt fog tests per ASTM B117. - Code-Compliant Safety Architecture
Double-sided insulation layers and 4mm creepage distances exceed IEC 60598-2-2 requirements for Class II construction. This design prevents electric shock risks in damp locations like bathrooms or spas, meeting NEC Article 410 stringency.
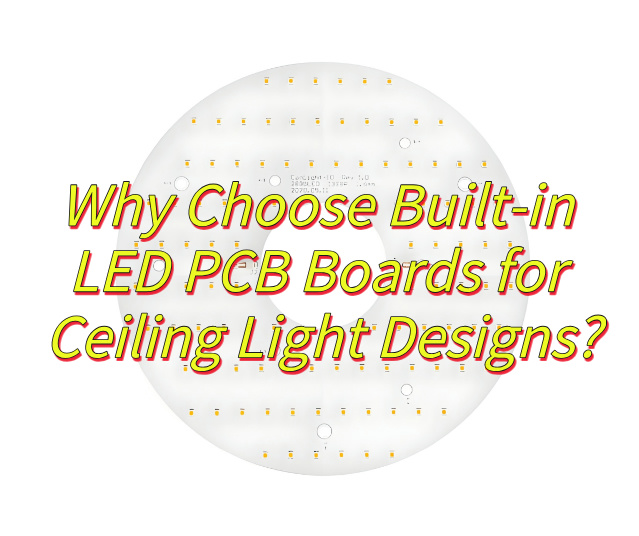
How to Evaluate A China LED Ceiling Light PCB Board Factory?
Here are tips about how to evaluate a China LED ceiling light PCB board factory:
- Production Certification & Compliance
Verify the factory holds ISO 9001 (quality management), ISO 14001 (environmental management), and industry-specific certifications like IATF 16949 (automotive) or ISO 13485 (medical). Export-oriented products must meet RoHS (hazardous substance restrictions), REACH (chemical management), and UL (safety) standards. These certifications ensure adherence to global quality and environmental norms. - Technical Capabilities & Equipment
Assess the presence of high-precision automated machinery such as SMT placers, AOI (Automated Optical Inspection), and X-ray detectors. Advanced equipment ensures soldering accuracy and defect detection. Inquire about their technical teamâs expertise in handling complex processes like BGA assembly or fine-pitch component placement. - Quality Control System
Evaluate welding quality metrics (e.g., solder penetration â„75%, component deviation â€1/4 of terminal size), visual inspections (board cleanliness, component alignment), and electrical tests (insulation resistance, voltage withstand). Environmental stress testing (thermal cycling, humidity, vibration) confirms product reliability under real-world conditions. - Supply Chain & Production Management
Review material sourcing protocols to ensure raw material quality and supply stability. The production facility should maintain cleanroom standards and comply with occupational health regulations (e.g., wastewater/air treatment). Assess daily output capacity, lead times, and ability to meet rush orders, particularly during peak seasons. - Customer Service & Support
Prioritize factories offering tailored solutions (e.g., circuit design optimization, material selection advice). Responsive after-sales teams for troubleshooting and repairs are critical. A robust feedback mechanism to address issues promptly reduces long-term partnership risks. - Environmental & Regulatory Compliance
Confirm use of lead-free solder, waste recycling programs, and adherence to RoHS/REACH. Energy-efficient equipment and process optimizations (e.g., ISO 14001 practices) reduce ecological impact and operational costs. - Financial Stability & Reputation
Analyze financial statements for profitability, cash flow, and R&D investments to gauge long-term viability. Industry reputation and client case studies provide insights into real-world performance; prioritize partners with proven success in relevant sectors. - Pricing & Delivery Competitiveness
Compare quotes across suppliers while balancing quality and service. Clarify lead times (standard vs. expedited) and flexibility for urgent orders to align with project timelines.
How to Achieve Fast Delivery of LED Ceiling Light PCB Board Orders?
This is how to achieve fast delivery of LED ceiling light PCB board orders:
- Optimize Supply Chain Collaboration: Partner with local or regionally aligned component suppliers to minimize lead times for materials like copper-clad laminates and LED packages. Implement real-time inventory synchronization to ensure raw materials arrive just-in-time for production, avoiding delays from stockouts or overordering.
- Streamline Production Workflows: Deploy automated SMT (Surface Mount Technology) lines with adaptive scheduling systems to prioritize urgent orders. Implement cellular manufacturing layouts where PCB assembly, testing, and packaging occur in contiguous zones, reducing material handling time by up to 30%.
- Maintain Strategic Buffer Stock: Hold safety stock for frequently specified PCB configurations (e.g., 2-layer 1.6mm FR-4 boards with 1oz copper). Use predictive analytics based on historical order patterns to replenish buffer inventory without incurring excessive carrying costs.
- Leverage Express Logistics Networks: Pre-negotiate contracts with multiple couriers for expedited air freight options. For time-sensitive domestic deliveries, utilize dedicated last-mile delivery services with GPS tracking to ensure 24-hour turnaround from factory to customer.
- Implement Digital Order Management: Adopt cloud-based platforms enabling customers to self-submit orders with BOM (Bill of Materials) files and receive instant DFM (Design for Manufacturability) feedback. Automated order confirmation emails with production timelines reduce back-and-forth communication delays.
- Accelerate Quality Validation: Integrate in-line AOI (Automated Optical Inspection) and ICT (In-Circuit Test) systems to complete 100% functional testing in <2 minutes per board. Implement statistical process control charts to identify and correct process deviations in real time, preventing batch rework.
- Design for Rapid Manufacturability: Encourage customers to adopt standardized board sizes and common component footprints during the design phase. Offer free DRC (Design Rule Check) services to identify potential production bottlenecks before fabrication begins.
- Establish Contingency Production Lines: Maintain dedicated “express lanes” with isolated equipment and skilled operators for rush orders. These lines bypass standard production queues, ensuring 48-hour turnaround for simple PCB designs without disrupting ongoing larger projects.
- Pre-Clear Customs Documentation: For international shipments, prepare export declarations and certificate of origin documents in parallel with production. Collaborate with customs brokers to secure AEO (Authorized Economic Operator) status, reducing clearance time by 40% at ports.
- Post-Production Aggregation Strategy: Consolidate completed orders from multiple clients into full container loads for ocean freight where possible, balancing cost and speed. For air shipments, use pre-packed reusable crates to eliminate loading delays at the dock.
How to Replace A LED Ceiling Light PCB Board Safely?
Here are how to replace a LED ceiling light PCB board safely:
- Power Disconnection Protocol: Begin by turning off the circuit breaker supplying power to the ceiling light. Use a non-contact voltage tester to confirm zero electrical potential at the fixture terminals. For added safety, place a warning sign on the electrical panel to prevent accidental reactivation during maintenance.
- Fixture Deconstruction: Remove the decorative diffuser or lens by gently rotating counterclockwise or releasing spring-loaded clips. Unscrew retaining bolts securing the LED module using an insulated screwdriver. Support the PCB assembly during removal to prevent accidental falls or component damage.
- Wiring Disconnection: Document wire connections using color photography or labeled tape before detachment. Use needle-nose pliers to release spade terminals or IDC connectors. For soldered connections, apply controlled heat with a temperature-controlled soldering station (280â320°C) to avoid thermal shock to adjacent components.
- PCB Inspection Protocol: Visually examine the old board for signs of overheating (discoloration, solder flux residue) or mechanical stress (cracked traces). Perform continuity tests on removed components using a multimeter to identify potential reuse candidates.
- New Board Preparation: Pre-bend component leads on the replacement PCB only if necessary for assembly. Apply a thin layer of heatsink compound to thermal pads if specified in the product documentation. Avoid touching conductive areas to prevent electrostatic discharge (ESD) damage.
- Reassembly Sequence: Mount the new PCB using original hardware, ensuring proper alignment with optical components (lenses, reflectors). Torque screws to manufacturer specifications (typically 0.6â0.8 Nm) using a calibrated torque screwdriver. Reconnect wires following the documented color code or labeling.
- Functional Verification: Restore power temporarily to test LED operation before finalizing installation. Confirm correct color temperature (measured with a spectrometer if available) and beam angle consistency. Check for flicker using smartphone camera slow-motion mode.
- Final Assembly: Reattach the diffuser, ensuring proper seating to maintain IP rating (if applicable). Clean the fixture surface with isopropyl alcohol and a lint-free cloth to remove fingerprints or debris. Dispose of old PCBs through certified e-waste recyclers.
- Documentation Update: Record the replacement date, PCB revision, and component lot numbers in the facility maintenance log. This creates an audit trail for warranty claims and facilitates troubleshooting in future service calls.
- Post-Installation Monitoring: Observe the fixture for 24â48 hours to detect early failures. Monitor junction temperatures with an infrared thermometer (target <85°C for aluminum-backed PCBs). Schedule follow-up inspections at 6-month intervals for critical installations.
How to Get Fast Delivery from China LED Ceiling Light PCB Board Factories?
This is how to get fast delivery from China LED ceiling light PCB board factories:
- Leverage Localized Supply Chains: Partner with factories that source components regionally to minimize lead times for materials like copper-clad laminates and LED packages. Prioritize suppliers with established relationships with nearby logistics hubs for faster material procurement.
- Implement Agile Production Systems: Choose manufacturers using automated SMT lines with dynamic scheduling capabilities to prioritize urgent orders. Choose factories employing cellular manufacturing layouts, which reduce material handling time by grouping assembly, testing, and packaging in contiguous zones.
- Maintain Strategic Buffer Stock: Work with suppliers to hold safety stock for commonly specified PCB configurations (e.g., 2-layer 1.6mm FR-4 boards with 1oz copper). Utilize predictive analytics based on historical order data to replenish inventory without incurring excessive storage costs.
- Utilize Express Logistics Solutions: Pre-negotiate contracts with multiple couriers for expedited air freight options. For domestic deliveries, engage dedicated last-mile services with real-time GPS tracking to ensure 24-hour turnaround from factory to destination.
- Adopt Digital Order Platforms: Select factories offering cloud-based systems for instant order submission, DFM (Design for Manufacturability) feedback, and automated order confirmation emails with production timelines. This reduces communication delays and accelerates order processing.
- Accelerate Quality Assurance: Choose suppliers with in-line AOI (Automated Optical Inspection) and ICT (In-Circuit Test) systems that complete 100% functional testing in under 2 minutes per board. Statistical process control charts help identify and correct deviations in real time, preventing batch rework.
- Encourage Standardized Designs: Advocate for standardized board sizes and common component footprints during the design phase. Factories often provide free DRC (Design Rule Check) services to identify potential production bottlenecks before fabrication begins.
- Establish Dedicated Express Lines: Select manufacturers maintaining isolated “express lanes” with dedicated equipment and operators for rush orders. These lines bypass standard production queues, ensuring 48-hour turnaround for simple PCB designs without disrupting larger projects.
- Pre-Clear Customs Documentation: For international shipments, ensure export declarations and certificates of origin are prepared in parallel with production. Collaborate with customs brokers holding AEO (Authorized Economic Operator) status to reduce clearance time by up to 40% at ports.
- Consolidate Shipments Strategically: Aggregate completed orders from multiple clients into full container loads for ocean freight where feasible. For air shipments, use pre-packed reusable crates to minimize loading delays at the dock, balancing cost and speed effectively.
Conclusion
In conclusion, for reliable LED ceiling light PCB boards with superior performance and fast delivery, Best Technology stands as your trusted China factory partner offering factory-direct prices and 24-hour sample service. Contact us today for a competitive quote on your next lighting project.
Tags: China LED Ceiling Light PCB Board Factory, LED Ceiling Light PCB Board