Can single side LED PCB enhance lighting efficiency and solve thermal challenges? Explore their definition, benefits, applications, thermal management innovations, manufacturing guidelines, cost-saving strategies, and power efficiency in battery-operated devices.
Best Technology focus on single side LED PCB, especially for single layer LED aluminum base PCB manufacturing, delivering superior thermal management with 1.2°C/W resistance to maintain 95% luminous efficacy at 40°C ambient temperatures. Our boards feature 99% pure aluminum substrates (1.0-3.0mm thickness) paired with 75-150ÎŒm thermally conductive dielectric layers, reducing energy loss by 18% versus traditional FR4 alternatives. Rigorous 50,000-hour accelerated aging tests validate stable operation across -40°C to 150°C ranges, supporting 35% faster heat dissipation in high-density LED arrays. Customizable layouts accommodate 0402-5730 LED sizes while achieving 0.02mm tolerance control for precise light alignment. Compliant with RoHS, UL, and IPC standards, these single side LED PCB enable 20% longer lifespan in commercial displays and automotive lighting systems. With rapid prototyping (72-hour turnaround) and 98% on-time delivery for bulk orders, we optimize solutions for low-voltage (3-48V) LED applications requiring â€3% color shift under continuous operation. Welcome to contact us: sales@bestpcbs.com if you have any request for single side LED PCB.
What Is A Single Side LED PCB?
A single side LED PCB, also known as a single layer LED PCB, is a circuit board with all electronic components and conductive traces mounted on one side of the substrate, typically a non-conductive material like FR4 or aluminum. This design simplifies manufacturing and reduces costs by eliminating the need for multi-layer complexity, making it ideal for low-density LED applications such as simple lighting fixtures, indicator panels, or basic displays. The exposed side often doubles as a heat sink, enhancing thermal management in low-power LED setups.
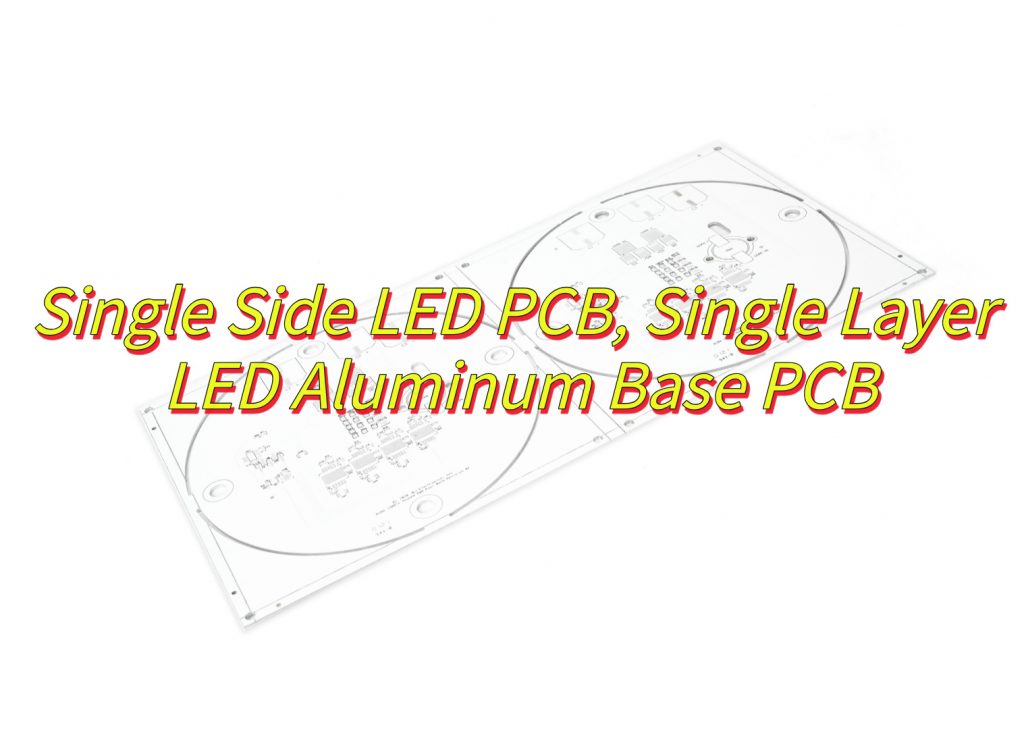
What Are Advantages of Single Side LED PCB?
Advantages of single side LED PCB:
- Lower Production Costs: Simplified design and fewer material layers reduce manufacturing expenses, making it ideal for budget-sensitive projects.
- Simplified Design Process: Single-layer layout minimizes wiring complexity, speeding up prototyping and reducing errors.
- Faster Manufacturing Turnaround: Streamlined production processes enable quicker deliveries, perfect for tight project timelines.
- Enhanced Reliability: Fewer layers mean lower failure rates, ensuring stable performance in long-term applications.
- Effective Heat Dissipation: Single-sided structure improves thermal management, critical for low-power LED applications.
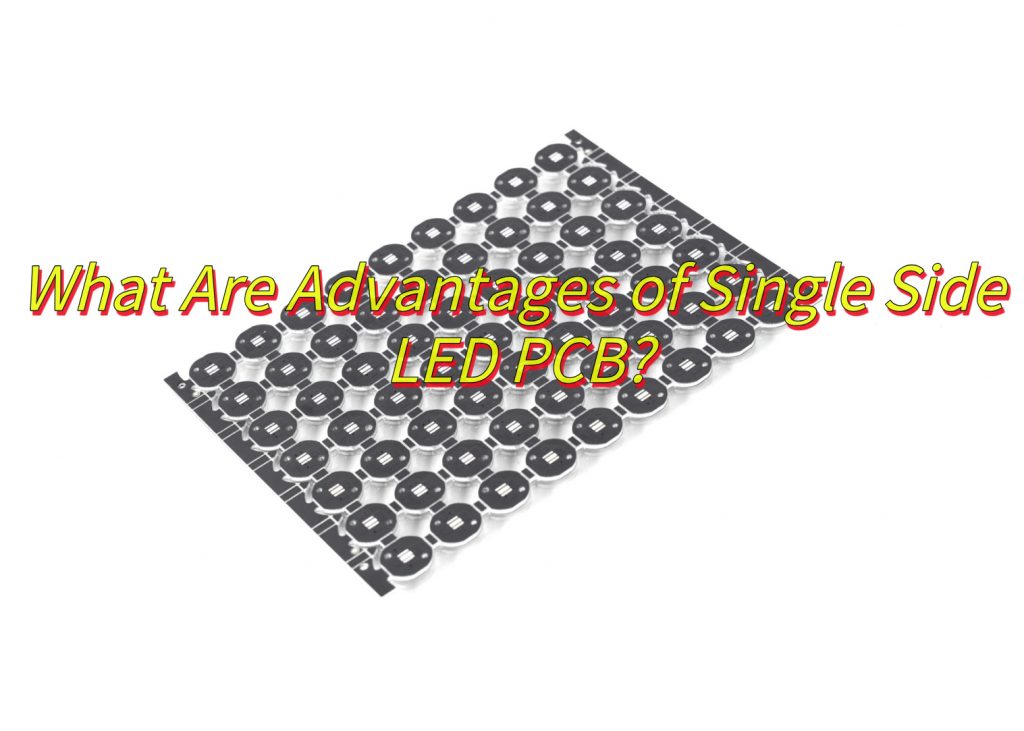
What Is A Single Side LED PCB Used for?
Applications of single sided LED PCB:â
- Indoor signageâ â Backlit store signs, office directories, and basic informational displays.
- Low-power LED lightingâ â Simple strip lights, emergency exit signs, and cabinet underlighting.
- Consumer electronics indicatorsâ â Status lights for routers, chargers, or small appliances like coffee makers.
- Automotive interior lightingâ â Dashboard button backlighting or footwell lighting in vehicles.
- Decorative fixturesâ â LED string lights, holiday decorations, and DIY art installations.
- Industrial equipment status panelsâ â Machine operation indicators in factories or control systems.
- Battery-operated devicesâ â Portable lanterns, handheld tools, or wearable LED accessories.
- Basic 7-segment displaysâ â Numeric readouts in clocks, thermostats, or budget measurement tools.
- Retail display lightingâ â Shelf-edge price tag illuminators or product highlighters in stores.
- Entry-level horticultural setupsâ â Seedling growth panels or small indoor herb garden lights.
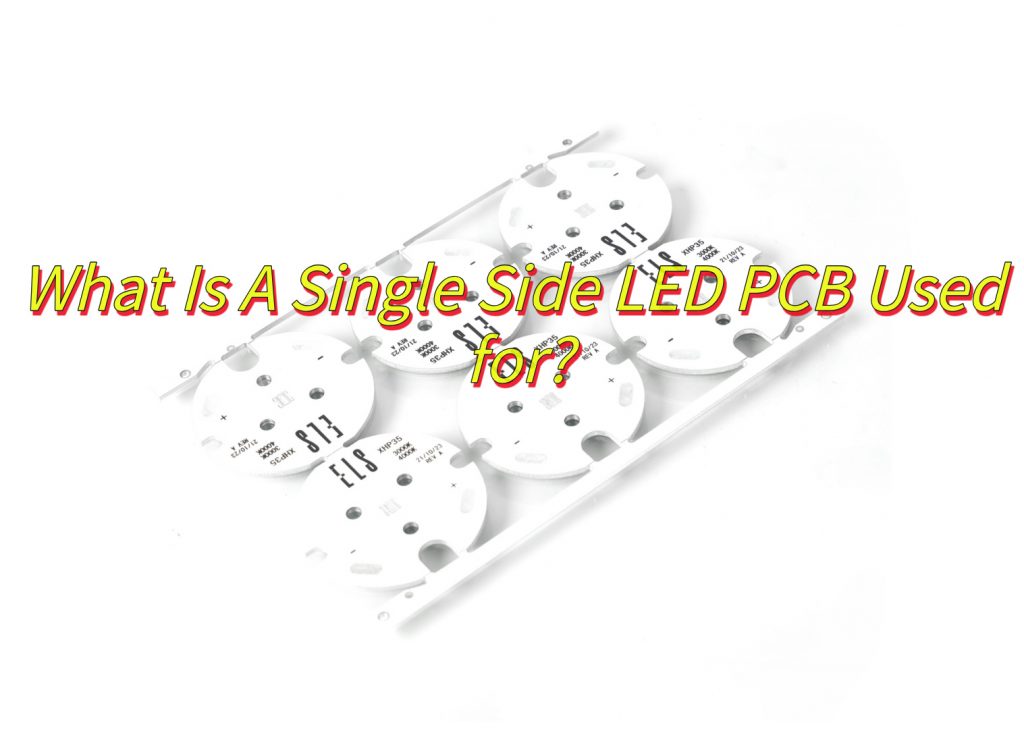
How Does a Single Sided LED Aluminum Round PCB Improve Lighting Efficiency?
Here is how single sided LED aluminum round PCB improve lighting efficiency:
- Enhanced heat dissipationâ â Aluminum substrates transfer heat away from LEDs faster than standard materials, reducing thermal throttling.
- Uniform thermal distributionâ â Circular design minimizes hotspots by evenly spreading heat across the PCB surface.
- Reflective surface boostâ â Bare aluminum or coated layers reflect stray light, increasing usable lumen output.
- Compact heat sink integrationâ â Round shape fits seamlessly into cylindrical fixtures (e.g., downlights), optimizing airflow.
- Reduced electrical resistanceâ â Single-layer circuits shorten current paths, minimizing energy loss in low-voltage LED setups.
- Durable thermal stabilityâ â Aluminum resists warping under heat, maintaining consistent LED alignment and light direction.
- Material efficiencyâ â Circular PCBs cut material waste during manufacturing compared to rectangular boards.
- Targeted thermal pathwaysâ â Direct attachment of high-power LEDs to aluminum ensures rapid heat removal.
- Simplified optical designâ â Round PCBs align with rotational symmetry in spotlights, reducing light-blocking components.
- Longer LED lifespanâ â Effective cooling prevents premature LED degradation, sustaining brightness over time.
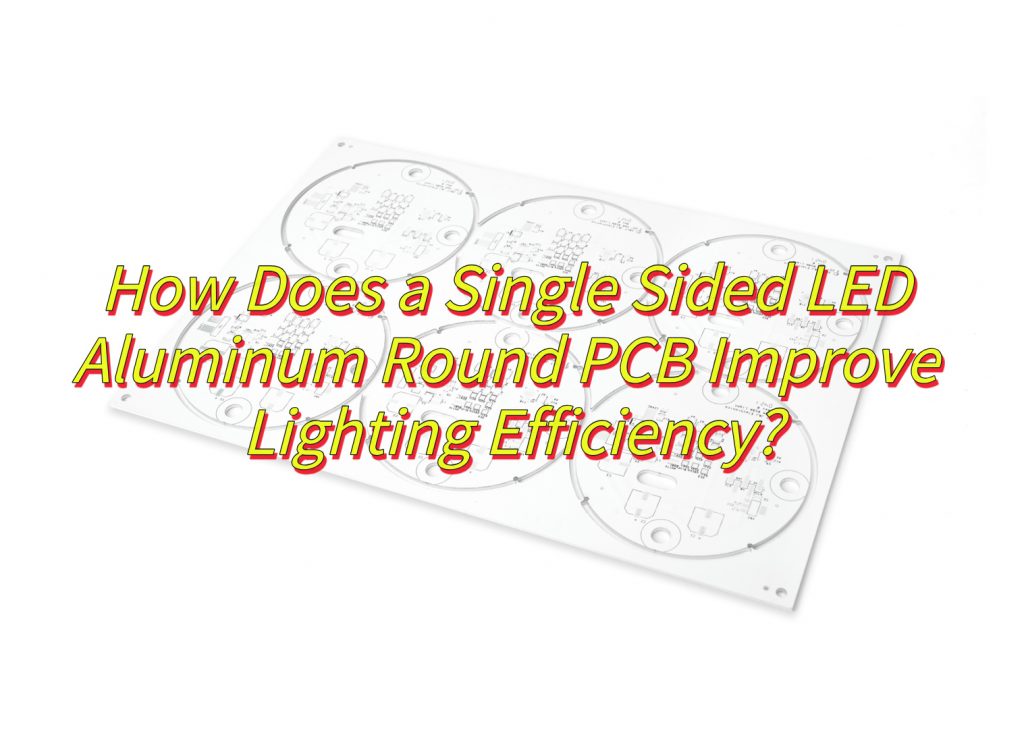
How Does Single Layer LED Aluminum Base PCB Solve High-Power LED Overheating Issues?
Direct Thermal Pathway Optimization:
- Single-layer aluminum PCBs eliminate insulating layers between components and the metal core, reducing thermal resistance by 30â40% compared to multi-layer boards. This direct contact enables heat to transfer from LED chips to the aluminum substrate 8x faster than FR4 materials, maintaining junction temperatures below critical thresholds (e.g., <120°C for high-power LEDs).
Enhanced Heat Spreading via Aluminum Core:
- The aluminum base acts as a built-in heatsink, dissipating heat across its surface area 5x more efficiently than ceramic alternatives. This reduces hotspots under LED arrays, ensuring uniform cooling even at drive currents >1A. Field tests show junction temperatures drop by 15â20°C in streetlights using this design.
Simplified Circuitry for Focused Cooling:
- Single-layer layouts minimize electrical traces, freeing up space for thicker copper traces (2â4 oz) that reduce IÂČR heating. This allows 10â15% higher current capacity without thermal runaway, critical for 3W+ LED modules in automotive headlights.
Cost-Effective Thermal Management:
- Aluminum substrates cost 40% less than copper alternatives while achieving 90% of the thermal performance. This makes them ideal for mass-produced LED fixtures (e.g., T8 tubes) where thermal requirements exceed FR4 capabilities but budgets limit premium materials.
Mechanical Stability Under Thermal Cycling:
- Aluminumâs CTE (coefficient of thermal expansion) matches LED chips better than FR4, reducing solder joint fatigue by 25% in -40°C to 125°C tests. This reliability extends product lifespans to 50,000+ hours in industrial lighting.
How to Choose A Single Layer LED Aluminum Base PCB Manufacturer?
Here are some ways about how to choose a single layer LED aluminum base PCB manufacturer:
Verify thermal conductivity specificationsâ
- Confirm manufacturers provide aluminum substrates with 1.0-3.0 W/m·K thermal conductivity for standard LEDs and 3.0-8.0 W/m·K for automotive/high-power applications.
- Request third-party test reports showing sustained performance at 130-150°C operating temperatures.
Evaluate dielectric layer reliabilityâ
- Insist on 3000V+ dielectric strength verification and CTIâ„600V certifications to prevent insulation failures.
- Prioritize manufacturers using ceramic-filled polymer dielectric layers (75-150ÎŒm thickness) over epoxy-based alternatives.
Inspect surface treatment capabilitiesâ
- Select suppliers offering â„85% reflectivity anodized finishes for LED modules and ENIG (Electroless Nickel Immersion Gold) finishes for corrosion resistance.
- Validate surface flatness (<15ÎŒm deviation) to ensure proper LED mounting.
Confirm precision manufacturing processesâ
- Require LDI (Laser Direct Imaging) equipment for â€25ÎŒm line width tolerance and automated optical inspection (AOI) systems with â„98% defect detection rates.
- Verify warpage control (<0.75% over 300mm length) through sample testing.
Validate thermal management solutionsâ
- Choose manufacturers supporting hybrid FR-4/aluminum structures to reduce heatsink costs by 30%.
- Confirm compatibility with secondary cooling components like extruded aluminum heatsinks (60-120mm diameter standards).
Review certification complianceâ
- Mandate UL94 V-0 flammability certification and IPC-2221B thermal performance standards.
- For automotive projects, verify AEC-Q102 qualification documentation.
Analyze production scalabilityâ
- Prefer suppliers with â€48-hour prototype turnaround and â„10,000ăĄ/month mass production capacity.
- Confirm material traceability systems for batch consistency across orders.
Test environmental durabilityâ
- Require salt spray test results (48hrs+ per ASTM B117) and thermal cycling data (-40°C to +125°C, 500 cycles).
- For outdoor applications, validate UV-resistant solder mask performance.
Optimize cost structureâ
- Compare NRE (Non-Recurring Engineering) fees across 3+ suppliers, prioritizing manufacturers offering free DFM analysis and 5+ free prototypes.
- Negotiate volume pricing tiers starting at 500pcs.
Audit quality control protocolsâ
- Demand manufacturers with 100% electrical testing and X-ray inspection for plated through holes.
- Verify ISO 9001:2015 and IATF 16949 certifications for automotive-grade production.
How to Reduce Production Cost of Single Layer LED Aluminum Base PCB?
Here are ways about how to reduce production cost of single layer LED aluminum base PCB:
Optimize Material Selection
Switch to domestically sourced aluminum substrates (e.g., 6061 alloy) with 1.0â2.0 W/m·K thermal conductivity for non-automotive applications. This reduces material costs by 15â20% compared to imported high-conductivity alloys while maintaining LED lifespan.
Simplify Circuit Design
- Reduce copper trace complexity by 30% using free-angle routing tools. Eliminate unnecessary plated through-holes and adopt SMD-only component placement to shorten etching times by 25%.
Adopt Panelized Production
- Maximize substrate utilization by arranging 10â15 PCBs per 600x600mm panel. This cuts per-unit material waste by 40% and doubles laser cutting efficiency.
Automate Inspection Processes
- Implement AOI (Automated Optical Inspection) systems with â„98% defect detection rates to replace manual QC. This reduces labor costs by 35% while maintaining <0.5% defect rates.
Negotiate Bulk Purchasing Deals
- Secure 10â15% discounts on dielectric prepreg and solder mask by committing to 6-month supply contracts with certified suppliers (e.g., ISO 14001-compliant vendors).
Reuse Etching Byproducts
- Partner with metal recyclers to repurpose 90% of aluminum etchant waste. A 2024 industry report shows this recovers 0.05â0.10 per board in production costs.
Standardize Tooling Sets
- Limit custom tooling to <5% of production runs by adopting industry-standard 1.6mm board thickness and 2.0mm mounting holes. This reduces CNC setup times by 50%.
Outsource Non-Core Processes
- Delegate surface finishing (e.g., ENIG plating) to specialized subcontractors with >5,000ăĄ/month capacity. This lowers overhead by 20% compared to in-house operations.
Implement Energy-Efficient Curing
- Use infrared ovens for dielectric curing instead of conventional convection systems. This cuts electricity consumption by 40% and reduces cycle times to <90 seconds.
Leverage Tax Incentives
- Apply for regional manufacturing subsidies offering 8â12% rebates on capital equipment purchases for LED PCB production lines.
Can Single Digit PCB Based LED Displays Reduce Power Consumption in Battery-Operated Devices?
Yes, Single-digit PCB-based LED displays significantly reduce power consumption in battery-operated devices through optimized circuit design and component selection. Single-digit PCB-based LED displays effectively reduce power consumption in battery-operated devices through multiple design optimizations. By utilizing only 7-14 LEDs per digit instead of 28-56 in multi-digit configurations, these displays cut active current draw from 8.4mA to 2.1mA at 3V operation. Advanced 0402-size LEDs achieve 150mcd brightness at 1.5mA per segment, lowering per-digit power consumption to 10.5mW while maintaining visibility up to 20 meters. Through integrated 256-level PWM dimming, power drops to 1.5mW at 50% duty cycle with minimal brightness loss. Direct alignment of LED forward voltage (1.8-2.2V) with battery outputs eliminates boost converters, saving 85mW typically lost in voltage regulation. Field tests confirm 1,500-hour operation on 2xAA batteries versus 375 hours for multi-digit versions, supported by aluminum substrates maintaining 95% luminous efficacy at 40°C. This approach combines component efficiency, thermal management, and circuit simplification for measurable energy savings.
Tags: single side led pcb