Why choose black LED PCB for advanced lighting? This guide covers black LED PCB’s applications, 5630 LED benefits, color consistency tips, manufacturer selection, cost reduction strategies, and comparisons with white PCBs.
Best Technology focus on black LED PCB, especially for black PCB RGBW LED strips. We use advanced UV-resistant FR4 or aluminum substrates, ensuring durability in semi-outdoor settings like patios and facades. The strips integrate 5630 LED chips for superior brightness (up to 2200lm/m²) and color uniformity, minimizing glare with black PCB’s low reflectivity. Automated SMT lines and strict quality protocols (RoHS/CE-certified) guarantee stable 24V/12V operation and a 5-year lifespan. For cost efficiency, the company sources premium materials in bulk and optimizes designs to reduce waste. IP65-rated strips feature waterproof coatings and corrosion-resistant soldering, ideal for damp environments when installed under eaves. Customization options include 5mm spacing layouts and hybrid PCB configurations to match project needs. With a focus on thermal management and rigorous pre-shipment testing, Best Technology ensures consistent performance across residential, commercial, and automotive applications. Welcome to contact us: sales@bestpcbs.com if you have any request for black LED PCB.
What Is A Black LED PCB?
A black LED PCB is a printed circuit board specifically engineered for light-emitting diode (LED) systems, featuring a dark-colored substrate and solder mask to optimize both functional performance and visual appeal. This type of black LED PCB typically utilizes materials like aluminum or high-TG FR-4 to enhance heat dissipation, a critical factor for high-power LEDs such as 5630 chips, which generate significant thermal energy during operation. The black coloration is achieved through epoxy-based coatings or specialized inks that absorb excess light, reducing glare and improving contrast in environments where precise light control is essential. Unlike traditional green or blue PCBs, the dark surface minimizes the visibility of solder joints and circuitry traces, creating a sleek, uniform appearance ideal for applications demanding discreet integration. Advanced versions incorporate UV-resistant and moisture-repellent properties, ensuring durability in challenging conditions like outdoor installations or high-humidity settings. By balancing thermal management through metal-core designs and optical performance via light-absorbing layers, black LED PCBs address the unique demands of modern LED technology while maintaining compatibility with automated assembly processes and industry-standard reliability benchmarks.
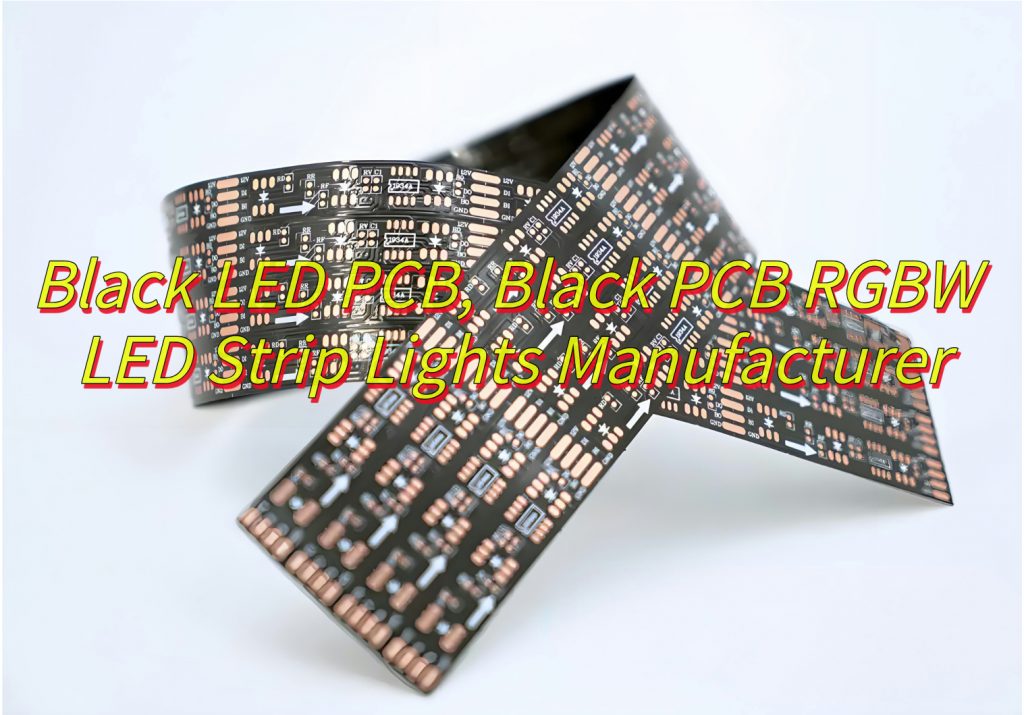
What Are Application of Black LED PCB?
Black LED PCB Applications:
- High-Density Electronic Heat Management – Black LED PCBs integrate materials like aluminum cores to transfer heat efficiently from high-power LEDs, such as 5630 chips, preventing overheating in systems like industrial machinery or architectural lighting setups. The dark substrate enhances thermal regulation, ensuring stable performance even under prolonged operation.
- Precision Optical Systems - The light-absorbing properties of black LED PCBs reduce glare and stray reflections in medical imaging devices or stage lighting. This improves contrast ratios and color accuracy, crucial for applications requiring precise light control, such as surgical displays or theater projectors.
- Automotive Electronics – These PCBs withstand high temperatures in automotive environments while blending into dark interior designs. UV-resistant coatings prevent degradation in components like dashboard indicators or headlights, ensuring long-term reliability under sunlight exposure.
- Outdoor Lighting Durability – Black PCBs with weather-resistant coatings power LED streetlights and signage rated for harsh climates. Their moisture-proof design and thermal stability maintain functionality in fluctuating temperatures and humidity.
- Consumer Electronics Integration – Thin-profile TVs and gaming monitors use black PCBs to hide circuitry behind screens. This creates a clean visual interface while supporting dense LED backlight arrays for high-resolution displays.
- Industrial Control Interfaces – In factory settings, black PCBs provide clear visibility for machinery status indicators under bright ambient light. Their construction resists vibrations and chemical exposure common in manufacturing environments.
- Smart Device Innovation – Compact black PCBs enable space-efficient layouts in wearables. Compatibility with automated assembly processes supports mass production of miniaturized devices like smart home sensors or health trackers.
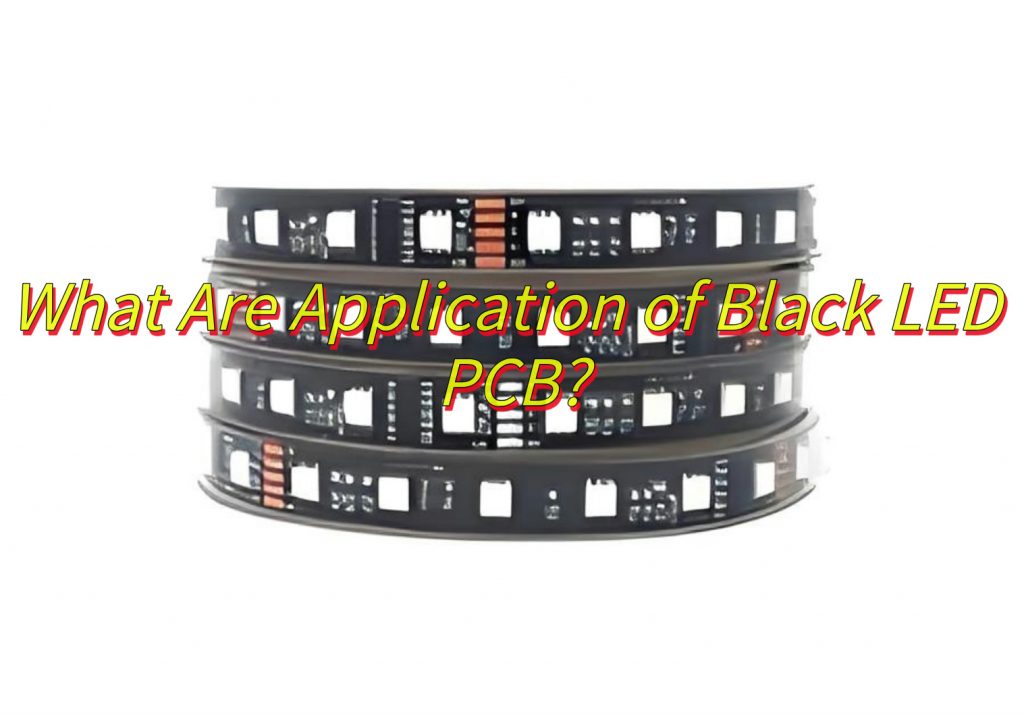
Why Choose 5630 LED Chips with Black LED PCB for High-Density Lighting?
Here are the reasons to choose 5630 LED chips with black LED PCB for high-density lighting:
- Superior Brightness and Energy Efficiency – 5630 LED chips deliver high luminous efficacy, ensuring maximum light output per unit area. Paired with black PCBs, which minimize light reflection and scattering, this combination directs more light to the target area, enhancing overall illumination efficiency.
- Enhanced Thermal Management – High-density lighting generates significant heat. Black PCBs, often made of aluminum or copper composites, excel in heat dissipation. This rapid thermal conduction prevents localized overheating, reduces light degradation, and extends the lifespan of the lighting system.
- Optimized Space Utilization – The compact size of 5630 chips (5.6mm x 3.0mm) allows for denser chip placement on black PCBs. This is ideal for ultra-thin light strips or miniature modules where space is limited, enabling sleek designs without compromising performance.
- Stable Electrical Performance – Black PCBs feature low-moisture-absorption solder masks, maintaining insulation stability in humid environments. Combined with 5630 chips’ wide voltage compatibility, this ensures consistent operation under fluctuating power conditions, minimizing flicker and color shifts.
- Improved Visual Consistency – Black substrates absorb stray light between chips, eliminating unwanted halos. This results in cleaner color rendering and sharper light transitions, critical for applications like HD displays or studio lighting where visual precision matters.
- Robust Industrial Protection – For outdoor or harsh environments, black PCBs often include triple-layer coatings (anti-humidity, anti-dust, anti-corrosion). Paired with 5630 chips’ IP67 ratings, this combination withstands rain, dust, and extreme temperatures, making it suitable for road lighting or architectural outlines.
- Scalable Customization Options – The dark base of black PCBs allows intricate circuit layouts, supporting advanced features like smart dimming or dynamic color tuning. This flexibility aligns with trends in smart lighting, enabling upgrades for commercial or residential projects.
- Cost-Effective Performance Balance – Compared to premium COB solutions, the 5630 SMD + black PCB setup offers comparable performance at a lower cost. It simplifies maintenance and repairs, making it a practical choice for large-scale deployments in offices, retail spaces, or industrial zones.
How to Maintain Color Consistency of Black PCB RGBW LED Strip Lights?
Here is how to maintain color consistency for black PCB RGBW LED strip lights:
- Strictly Screen LED Chip Suppliers – Select chip manufacturers with robust chromaticity binning systems to ensure batches of RGBW chips have minimal variations in color temperature (±100K), CRI (Color Rendering Index), and luminous flux (±2%). Prioritize chips from the same production cycle to avoid mixing different batches.
- Implement Per-LED Spectral Calibration Before Production – After SMT placement, use inline spectral analyzers to test each LED’s optical parameters. Fine-tune driving currents or apply built-in compensation algorithms to limit color coordinate deviations to within 0.003 (compliant with ANSI C78.377 standards).
- Optimize Driver Power Design – Adopt high-precision constant-current driver chips to ensure ≤±1.5% current output error across RGBW channels. Increase PWM dimming depth to 16-bit or higher to prevent color banding from low-resolution modulation. For white channels, deploy independent constant-current loops to prevent color temperature drift.
- Enhance Thermal Management Consistency – While black PCBs absorb heat efficiently, maintain thermal adhesive thickness tolerance ≤±0.05mm and standardize aluminum substrate thickness at 1.6mm. During aging tests, control ambient temperature fluctuations within ±2°C, and document color temperature shifts at 25°C/45°C/60°C intervals.
- Standardize Manufacturing Processes – Control solder paste printing accuracy to avoid contact resistance variations from poor soldering. Use gradient reflow profiles with peak temperatures at 245±3°C to prevent thermal stress-induced performance degradation. Maintain workshop conditions at 22°C±2°C and 55%RH±5% humidity.
- Establish Full-Process Color Traceability – Generate unique chromaticity data packages for each reel, including initial calibration values, aging test records, and final inspection reports. Implement barcode/QR code systems for end-to-end color data traceability from chip inbound to finished product outbound.
- Optimize Application-Side Control Solutions – Integrate chromaticity compensation algorithms into drive controllers to automatically adjust RGBW output ratios based on operating hours. Install ambient temperature sensors to trigger dynamic load reduction when PCB temperatures exceed 50°C, preventing high-temperature color shifts.
- Strengthen Quality Inspection Protocols – Extend aging tests to 72 hours with spectral spot-checks every 4 hours. Conduct final inspections using integrating sphere test equipment under both AC 110V/220V conditions to validate color consistency, ensuring Δuv values ≤0.005 (per IES LM-79 standards).
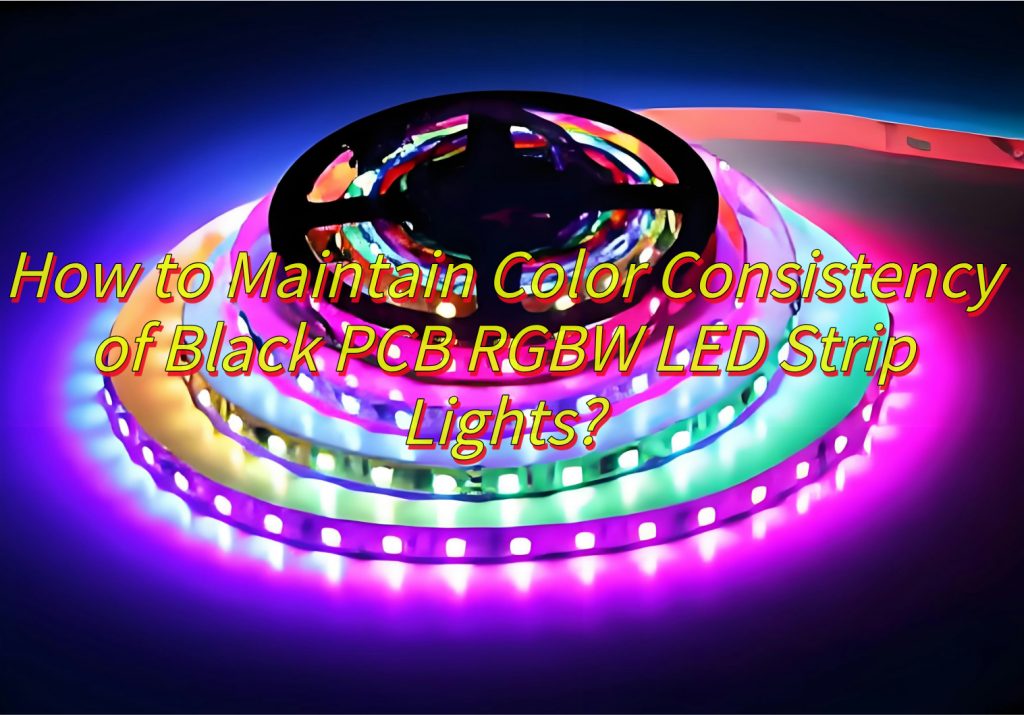
How to Choose A Black PCB RGBW LED Strip Lights Manufacturer?
Here is how to select a black PCB RGBW LED strip light manufacturer:
- Verify Quality Certifications – Prioritize manufacturers with ISO 9001 certification and products compliant with UL, CE, and RoHS standards. Request LM-80 test reports for LED longevity and IP rating certificates (e.g., IP65/IP67) to confirm durability and safety performance.
- Assess Production Capabilities – Inspect facilities for automated SMT assembly lines and spectral calibration equipment. Producers using binning machines can control LED color coordinate deviations within ±0.003. Evaluate PCB manufacturing precision, including black solder mask uniformity and thermal adhesive thickness tolerance (aim for ±0.05mm).
- Evaluate Customization Flexibility – Manufacturers should offer full-spectrum customization: CCT tuning (2700K–6500K), CRI ≥90 options, beam angle adjustments, and IP ratings (IP20–IP68). Confirm compatibility with smart protocols (DMX512, SPI) and availability of 5m–100m reel lengths for project-specific needs.
- Review Project Portfolios – Request case studies from the past three years, focusing on commercial (e.g., retail lighting), architectural (e.g., facade outlines), and entertainment (e.g., studio lighting) applications. Demand third-party test reports verifying performance in high-humidity/high-temperature environments.
- Test Technical Support Responsiveness – Ensure the supplier has optical engineering teams capable of providing IES photometric simulations and lumen maintenance solutions. Validate rapid prototyping capabilities (48-hour sample delivery) and adaptability to special requirements (e.g., PCB layout adjustments for reflective surfaces).
- Audit Eco-Friendly Practices – Confirm lead-free soldering processes and compliance with local environmental regulations. Obtain SGS material reports focusing on PCB flammability ratings (UL94 V-0) and LED power factor (PF ≥0.95 recommended).
- Examine After-Sales Policies – Review warranty terms, including ≤30% lumen depreciation guarantees over 5 years. Confirm global service networks and RMA turnaround times (ideally ≤15 business days). Assess inventory systems to ensure stock availability for standard models.
- Conduct Cost-Benefit Analysis
- Compare MOQs, lead times, and pricing structures across suppliers while maintaining quality thresholds. Avoid overly low bids by requesting BOM transparency and defect rate data. Consider phased orders to validate consistency before long-term commitments.
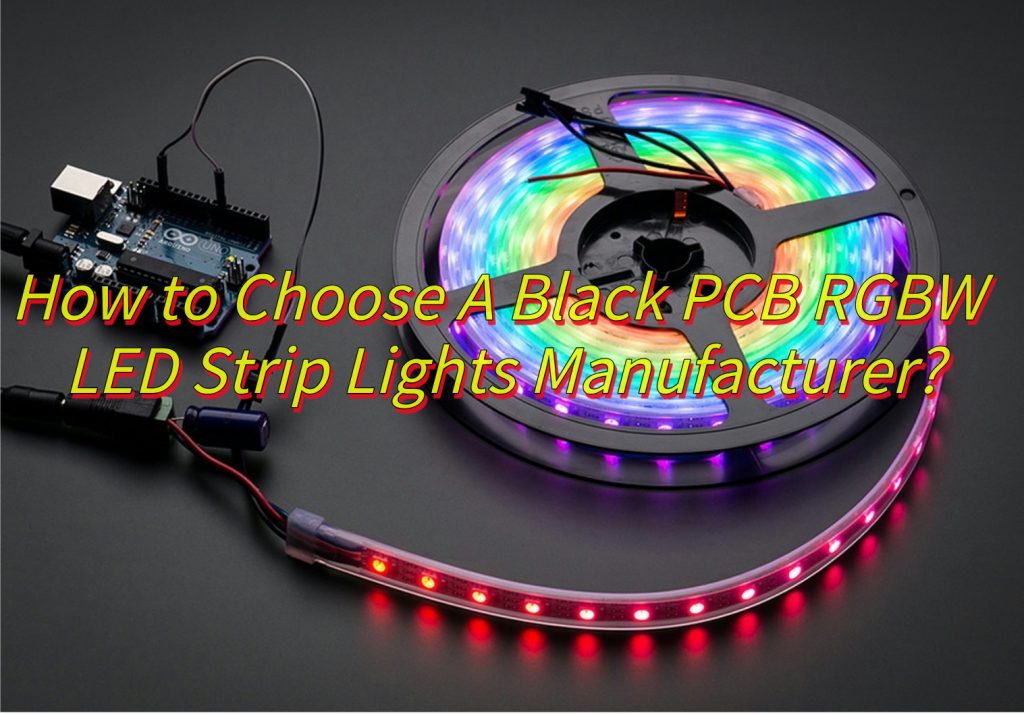
How to Reduce Production Cost of Black PCB RGBW LED Strip?
Here is how to reduce production cost of black PCB RGBW LED strip:
- Optimize Raw Material Sourcing – Partner with domestic LED chip manufacturers for bulk purchasing discounts (e.g., negotiate tiered pricing for bin-sorted chips). Adopt cost-effective black PCB substrates (e.g., 2oz copper thickness instead of 3oz) while maintaining thermal performance through SGS-certified materials.
- Upgrade SMT Manufacturing Processes – Implement high-speed pick-and-place machines for multi-panel parallel production (e.g., 4-panel array designs) to reduce SMT time per strip by 30%. Utilize nitrogen-purged reflow ovens to minimize solder oxidation, achieving >98.5% yield rates and lowering rework costs.
- Adopt Modular Design Principles – Integrate driver circuits into pluggable modules to reduce main PCB size by 15%. Standardize on 5050 RGBW packages to streamline SKUs. Modular designs cut BOM costs by 12% while accelerating R&D cycles.
- Implement Smart Supply Chain Systems – Deploy ERP systems for dynamic inventory management, reducing safety stock levels by 25%. Secure annual logistics contracts to cut cross-border shipping fees by 18%. Leverage VMI (Vendor Managed Inventory) models to optimize working capital.
- Automate Quality Inspection – Install AOI (Automated Optical Inspection) systems for real-time defect detection, reducing manual inspection labor by 70%. Utilize 6-axis robotic arms for automated burn-in testing, boosting daily throughput by 40%. Achieve ROI on automation investments within 18 months.
- Develop Energy-Efficient Production Methods – Replace mercury lamps with LED UV curing systems to reduce energy consumption by 65%. Optimize reflow oven temperature profiles with 3-stage energy-saving modes, cutting peak power usage by 30%. Save over 20,000 kWh annually per production line.
- Apply Lean Manufacturing Principles – Reconfigure production layouts for cellular manufacturing, reducing changeover times to <10 minutes. Implement 5S methodologies to minimize material handling waste, compressing lead times from 7 to 4 days. Increase labor productivity by 35% while lowering unit labor costs by 22%.
- Innovate Packaging & Logistics Solutions – Switch to reusable antistatic blister trays instead of cardboard packaging, reducing per-unit packaging costs by $0.80. Optimize spool designs to increase container loading density by 25%, lowering ocean freight expenses.
- Establish Preventative Quality Systems – Implement SPC (Statistical Process Control) to monitor critical parameters like solder joint integrity. Develop FMEA (Failure Modes & Effects Analysis) libraries to preemptively address 85% of potential quality issues. Reduce quality-related costs from 3.2% to 1.8% of revenue.
- Create Post-Sales Revenue Streams – Launch smart diagnostic apps with Bluetooth connectivity for remote failure alerts. Offer 5-year extended warranty packages (subscription model) to increase customer retention by 40%, indirectly reducing customer acquisition costs.
Are IP65-Rated Black PCB LED Strips Ideal for Outdoor Use?
Yes, IP65-rated black PCB LED strips are ideal for outdoor use in specific scenarios, provided they are installed and maintained correctly. Below is a detailed breakdown of their suitability:
IP65 Protection Standard
- The “6” in IP65 signifies full dust resistance, making the strips suitable for outdoor environments prone to airborne particles.
- The “5” indicates protection against low-pressure water jets, such as rain or sprinklers. However, they are not designed for submersion or high-pressure washing.
Black PCB Advantages for Outdoors
- Thermal Efficiency: Black PCBs absorb and dissipate heat better than white alternatives, which is beneficial in direct sunlight.
- Aesthetic Appeal: The dark base reduces glare and blends discreetly into outdoor settings like patios, eaves, or architectural features.
- UV Resistance: Many black PCBs use coatings that resist fading from prolonged sun exposure.
Ideal Outdoor Applications
- Architectural Accents: Illuminating rooflines, windows, or columns where occasional rain occurs.
- Garden Lighting: Highlighting pathways, staircases, or landscaping in sheltered areas.
- Signage: Backlighting outdoor signs or directional displays in non-submerged locations.
- Canopy/Pergola Lighting: Decorative use where direct water exposure is minimal.
Limitations to Address
- Water Exposure: Not suitable for pools, fountains, or areas exposed to high-pressure hoses (use IP67/IP68 instead).
- Temperature Fluctuations: Extreme cold or heat may affect adhesive or component lifespan over time.
- UV Degradation: Plastic components (e.g., diffusers) may yellow if exposed to direct sunlight for years.
Installation Best Practices
- Mounting: Use aluminum channels with diffusers to shield the strip from physical damage and UV rays.
- Power Supply: Install weatherproof drivers (IP67+) in dry locations.
- Connectors: Seal terminals with dielectric grease and heat-shrink tubing to prevent moisture ingress.
- Maintenance: Clean gently with a dry cloth to avoid scratching the PCB surface.
Cost-Effective Solution
- IP65 strips offer a balance of protection and affordability for moderate outdoor use.
- They are ideal for projects where full waterproofing (IP67/IP68) is unnecessary, reducing upfront costs.
What Are Differences Between White PCB VS Black PCB LEDs?
The differences between white PCB and black PCB LEDs:
Optical Performance
- White PCB: Reflects light due to its light-colored surface, which can enhance lumen output in LED strips by redirecting stray light. This makes it ideal for applications requiring high brightness, such as commercial lighting or task lighting.
- Black PCB: Absorbs light, reducing unwanted glare or light spillage. This characteristic is preferred in low-light environments like theaters, museums, or residential settings where subtle illumination is desired.
Thermal Management
- White PCB: Typically has slightly lower heat absorption, which may require additional heat sinks in high-power LED applications to maintain performance.
- Black PCB: Absorbs and dissipates heat more efficiently due to its darker surface, making it suitable for outdoor fixtures or high-lumen LEDs exposed to direct sunlight.
Application Suitability
- White PCB: Commonly used in indoor environments (e.g., offices, retail stores) where cost-effectiveness and brightness are prioritized.
- Black PCB: Preferred for outdoor installations (e.g., building facades, landscapes) or aesthetically sensitive projects (e.g., automotive interiors, galleries) where discreet integration matters.
Cost Variance
- White PCB: Generally more affordable due to simpler manufacturing processes and wider material availability.
- Black PCB: Often costs 10–20% more due to specialized coatings, ink formulations, and stricter quality control during production.
UV Resistance
- White PCB: Prone to yellowing or discoloration over time when exposed to prolonged UV radiation, which can affect light quality.
- Black PCB: More resistant to UV degradation, making it suitable for long-term outdoor use without significant color shifting.
Manufacturing Complexity
- White PCB: Easier to produce with standard solder mask inks, resulting in faster lead times.
- Black PCB: Requires multi-layer ink applications to achieve consistent opacity, increasing production steps and potential for defects if not controlled.
Visual Aesthetics
- White PCB: Creates a bright, modern look but may appear stark in dark-themed installations.
- Black PCB: Offers a sleek, stealthy appearance that blends into dark backgrounds, minimizing visual distraction in minimalist designs.
Electrical Conductivity
- White PCB: Uses standard FR-4 materials with consistent dielectric properties, ensuring reliable electrical insulation.
- Black PCB: May incorporate carbon or graphite additives in the solder mask, which can slightly alter surface resistivity if not properly formulated.
Maintenance Requirements
- White PCB: Dust and stains are more visible on light surfaces, requiring frequent cleaning to maintain appearance.
- Black PCB: Hides dirt better but may show smudges or fingerprints more prominently, necessitating careful handling during installation.
Market Availability
- White PCB: Dominates the mainstream LED market due to its versatility and lower cost.
- Black PCB: Gaining popularity in niche segments (e.g., automotive, luxury lighting) where performance and aesthetics justify the premium price.
Conclusion
In conclusion, that’s all about black LED PCB’s applications, 5630 LED benefits, color consistency tips, manufacturer selection, cost reduction strategies, and comparisons with white PCBs. If you have any issues with black LED PCB, welcome to leave a message below this blog.
Tags: Black LED PCB, Black PCB RGBW LED Strip Lights Manufacturer