In the printed circuit board (pcb) fields, thermal management is a key consideration especially in industries such as automotive, aerospace, tele-communications and power electronics. Ceramic PCBs are known for their excellent thermal conductivity and mechanical properties and are becoming increasingly popular in applications where efficient heat dissipation is essential. Under this situation, solder resistance materials play a vital role not only in protecting the circuit, but also in influencing thermal behavior.
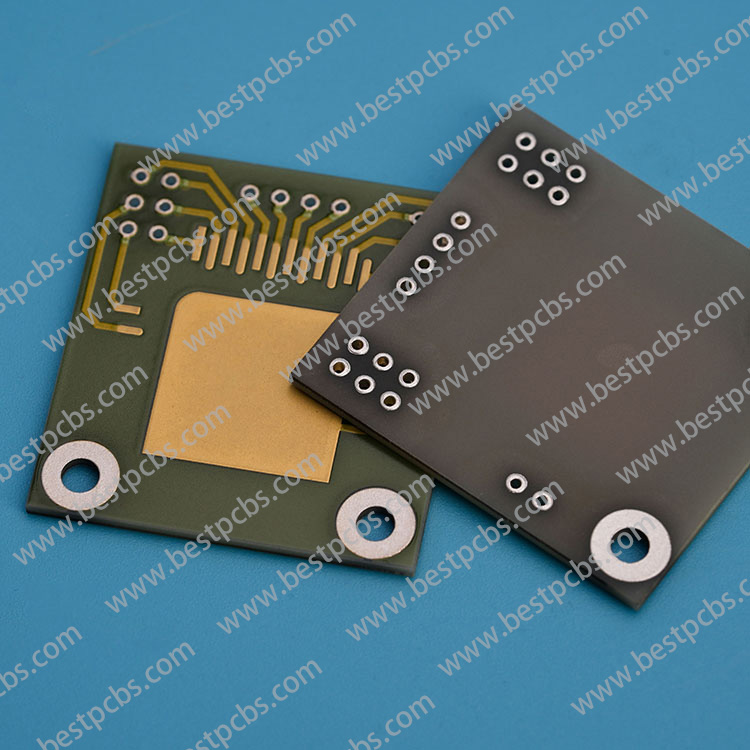
What is Thermal Resistance in Ceramic Circuit Board?
Ceramic PCBs are usually composed of materials such as alumina (Al2O3) or aluminum nitride (AlN), which have superior thermal conductivity compared to traditional glass fiber PCB substrates. This inherent thermal conductivity promotes the efficient transfer of heat from heating components, improving the reliability and performance of electronic devices. However, while substrate materials make an important contribution to thermal management, the thermal resistance of solder resistance materials must also be considered.
Solder mask materials are mainly used to isolate conductive wires on the pcb, prevent unexpected electrical connections, and protect the circuit from environmental factors such as moisture, dust, and chemical contaminants. Although solder mask is not generally praised for their thermal conductivity, their thermal resistance can affect the heat dissipation within the PCB components.
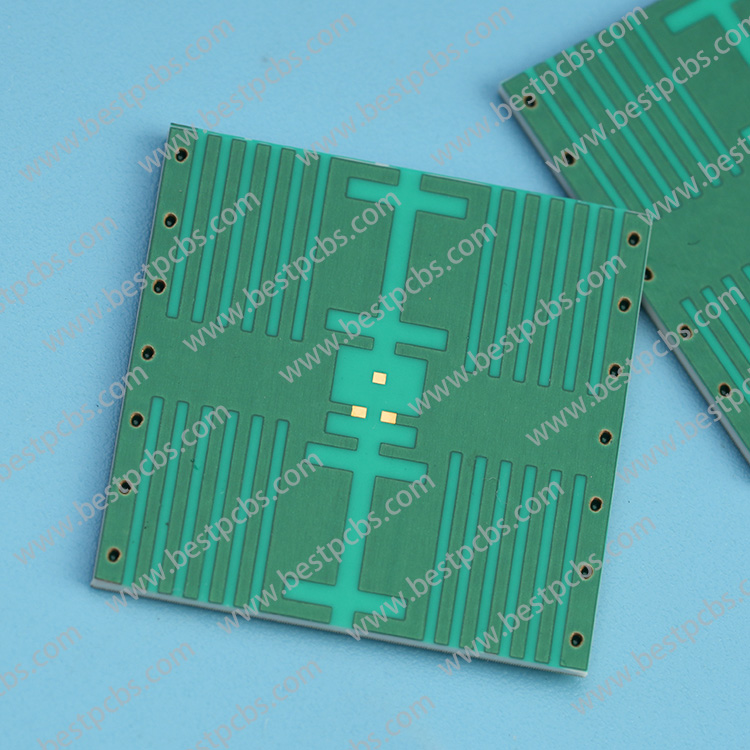
What Factors Influencing Solder Mask Thermal Resistance?
Solder resistance thermal resistance is an important feature in the design and performance of printed circuit boards, especially when considering thermal management of electronic devices. There are several factors that affect the thermal resistance of solder pads, and understanding these factors can help optimize the thermal design of the PCB. Here are the key factors:
Solder Mask Composition
The type of resin and fillers used in the solder mask can significantly affect its thermal properties. Epoxy resins are common, but other materials may offer better thermal conductivity.
Thickness
Thicker layers of solder mask can increase thermal resistance because they add more insulating material between the heat source (such as electronic components) and the ambient environment. Thinner layers might improve heat dissipation but could be less effective in protecting against physical damage or corrosion. Generally, solder mask has around 20-25um thickness and has 0.2W/m.k thermal conductivity.
Curing Process
The process conditions under which the solder mask is cured (temperature, time, and environment) can impact its mechanical and thermal properties. Improper curing can lead to reduced heat transfer efficiency.
Dielectric Constant
The dielectric constant of the solder mask material influences its ability to conduct heat. Materials with higher dielectric constants may provide higher thermal resistance.
Interface with Substrate
The interface between the solder mask and the ceramic substrate can affect thermal resistance. Poor adhesion or air gaps may decrease heat transfer between the layers.
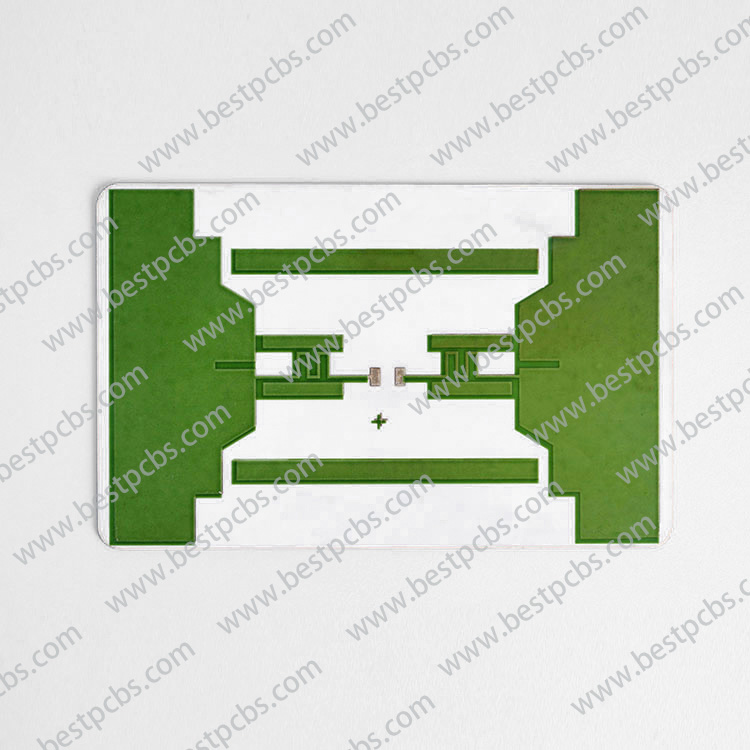
What are the Importances of Thermal Resistance in Ceramic PCBs?
Efficient thermal management is crucial for maintaining the reliability and longevity of electronic devices, especially in applications where high temperatures can degrade components or compromise performance. In ceramic PCBs, where heat dissipation is a key advantage, minimizing thermal resistance throughout the assembly is essential.
While ceramic substrates inherently offer excellent thermal conductivity, the solder mask layer presents a potential bottleneck for heat transfer. Therefore, selecting solder mask materials with optimal thermal properties and ensuring proper application are critical steps in PCB design and manufacturing.
Applications and Considerations:
Ceramic PCBs find applications in various industries, including power electronics, LED lighting, automotive systems, and telecommunications infrastructure. In these applications, where thermal management is critical, careful consideration of solder mask thermal resistance is essential for meeting performance requirements and ensuring reliability under challenging operating conditions.
Designers and engineers must balance the need for thermal management with other considerations such as cost, manufacturability, and compatibility with assembly processes. Collaboration with experienced PCB manufacturers and material suppliers can help optimize the selection of solder mask materials and design solutions tailored to specific application requirements.
The thermal resistance of solder mask materials is an important consideration, especially in applications where heat dissipation is a concern, such as high-power electronics or devices operating in harsh environments.
Solder mask materials are designed to withstand the temperatures encountered during the PCB fabrication process, including solder reflow, typically ranging from around 220°C to 280°C (428°F to 536°F), depending on the specific materials and processes used.
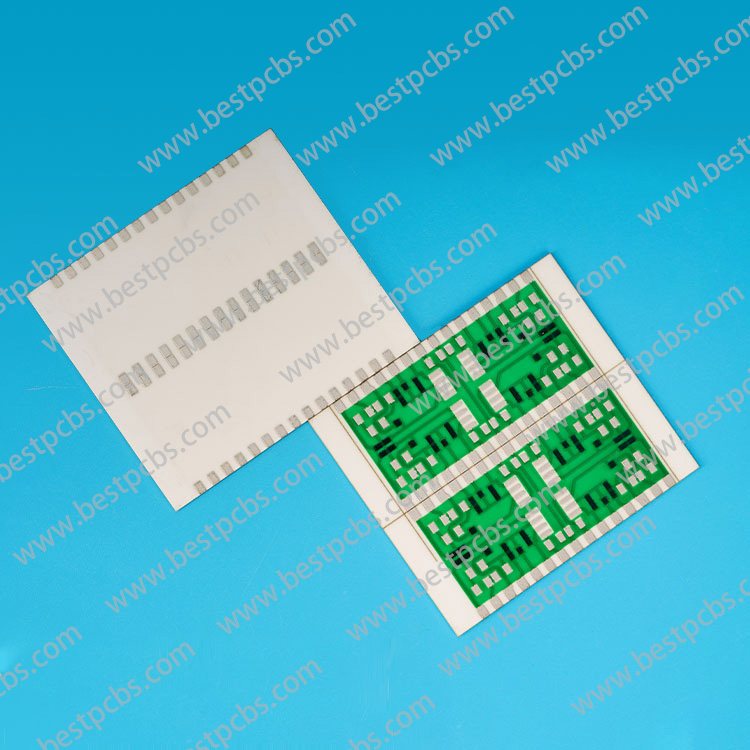
However, when it comes to the thermal resistance of solder mask materials in terms of their ability to dissipate heat away from components or traces on a PCB, they generally have lower thermal conductivity compared to materials like copper or aluminum. This means that they are not as effective at transferring heat away from heat-generating components.
In high-power applications or those where thermal management is critical, additional measures may need to be taken, such as incorporating heat sinks, thermal vias, or selecting solder mask materials with improved thermal properties. Some manufacturers offer solder mask materials with enhanced thermal conductivity for specific applications where heat dissipation is a concern.
As electronic devices continue to evolve with increasing power densities and miniaturization, the demand for advanced thermal management solutions will grow. In the realm of ceramic PCBs, ongoing research and development efforts aim to enhance the thermal properties of solder mask materials, enabling more efficient heat dissipation and further improving the reliability and performance of electronic systems.