Why choose polyimide PCB? This guide details their critical properties, thickness, thermal conductivity, pros and cons, manufacturing processes and applications.
Are you still troubled by these problems?
- Complex circuit design leads to low yield?
- Traditional materials degrade in humid environment?
- Does micro-aperture processing affect circuit accuracy?
Best Technology 丨Polyimide PCB Manufacturer in China Over 18 years:
- High-precision graphic transfer technology: using laser direct imaging (LDI) process, line width/line spacing up to 25μm, yield increased by 30%.
- Ultra-low water absorption material: 0.2% water absorption formula, insulation resistance retention rate in humid environment> 95%.
- Precision micro-hole processing: CO2 laser + UV laser combined drilling, aperture accuracy ±15μm, hole wall roughness <10μm.
Welcome to contact us if you have any request for polyimide PCB: sales@bestpcbs.com.
What Is Polyimide PCB?
A polyimide PCB is a flexible printed circuit board utilizing polyimide as its dielectric substrate, providing remarkable flexibility for repeated bending, folding, or twisting without mechanical damage. This polymer offers exceptional thermal stability, handling temperatures up to 400°C, a low dielectric constant near 3.5, and high tensile strength, making it suitable for electronics requiring dynamic movement or intricate three-dimensional packaging.
Commonly applied in neural implants and wearable devices, these PCBs enable reliable electrical connections in space-constrained environments while maintaining performance under stress. Fabrication involves microelectronics-compatible techniques, supporting mass production for high-density interconnects across medical and consumer applications.
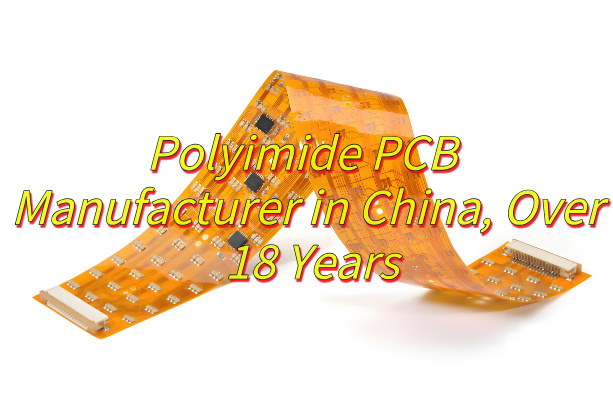
How Thick Is a Polyimide PCB?
Core Material Thickness
- Base Polyimide Film: Typically 12.5 μm to 100 μm (0.0005–0.004 inches), with 25 μm (0.001 inch) and 50 μm (0.002 inches) being industry standards.
Total Stackup Thickness
- Single-Layer Flexible PCB: 50–125 μm (0.002–0.005 inches) when combined with copper foil (9–18 μm).
- Multi-Layer Designs: Ranges up to 0.3 mm (0.012 inches) for 4–6 layer configurations using adhesive bonding.
Influencing Factors
- Copper Foil: Ultra-thin 9–18 μm electrodeposited copper reduces bulk.
- Adhesive Layers: Bonding films add 10–25 μm per layer; adhesive-less laminates reduce total thickness to 30 μm.
- Stiffeners: Localized PI or steel reinforcements (0.1–0.3 mm) enhance connector zones.
Polyimide PCB Material Data Sheet & Properties
Property Category | Test Parameter | Test Standard | Value with Unit | Characteristics |
Physical Properties | Density | ASTM D792 | 1.43 g/cm³ | Lightweight design advantage |
Water Absorption | ASTM D570 | 0.3% | Low moisture absorption for high-frequency stability | |
Flammability Rating | UL94 | Non-flammable | Complies with aerospace safety requirements | |
Mechanical Properties | Tensile Strength | ASTM D638 | 90 MPa | 3× stronger than FR-4 substrates |
Elongation at Break | ASTM D638 | 6-8% | High ductility for dynamic bending applications | |
Flexural Strength | ASTM D790 | 98 MPa | Supports 5mm bend radius designs | |
Thermal Properties | HDT @1.82MPa | ASTM D648 | 360℃ | Withstands reflow soldering |
Continuous Operating Temp. | UL746B | 260℃ | Suitable for automotive electronics | |
CTE (Z-axis) | ASTM D696 | 1-5×10⁻⁵ /℃ | Matches copper foil expansion (Cu: 17×10⁻⁶/℃) | |
Electrical Properties | Dk @1MHz | IEC 60250 | 3.4 | Low signal loss for high-frequency transmission |
Volume Resistivity | IEC 60093 | 10¹⁷ Ω·cm | 100× higher insulation than standard materials | |
Dielectric Strength | IEC 60243 | 110-120 kV/mm | Superior high-voltage breakdown resistance | |
Special Performance | Flex Life @5mm radius | IPC-6013D | >100,000 cycles | Validated in smart wearable devices |
Peel Strength (Cu foil) | IPC-TM-650 | ≥1.0 N/mm | Ensures flex circuit reliability | |
Min. Line Width/Spacing | IPC-2223 | 30/30 μm | Ultra-high-density routing capability |
What Is the Thermal Conductivity of Polyimide Flex PCB?
Material Type | Thermal Conductivity | Enhancement Mechanism |
Pure Polyimide (PI) | 0.18 W/(m·K) | N/A (base material) |
PI/CNNS Nanocomposite | 2.04 W/(m·K) (+1033%) | CNNS in-plane self-orientation |
Graphene-PI Composite | Up to 739.56 W/(m·K) | Layered graphene thermal networks |
What Are the Pros and Cons of Polyimide Circuit Board?
Pros (Advantages)
- High wiring density and miniaturization: Enables compact designs for space-constrained applications like mobile devices or wearables.
- Lightweight and thin profile: Reduces overall weight and thickness of electronic products, ideal for portable electronics.
- Excellent flexibility and durability: Can withstand millions of dynamic bends without wire breakage, supporting complex 3D assemblies.
- Versatility in spatial layout: Allows arbitrary scaling and movement in three-dimensional space for integrated component connections.
- Broad applicability: Suitable for high-reliability fields such as aerospace, military, and digital cameras due to robust insulating properties.
Cons (Disadvantages)
- High initial cost: Design, routing, and photographic processes are expensive due to specialized manufacturing requirements.
- Limited use for general applications: Typically justified only for specific needs, not cost-effective for standard PCBs.
- Maintenance challenges: Repair and rework, such as soldering, require trained personnel to avoid damage.
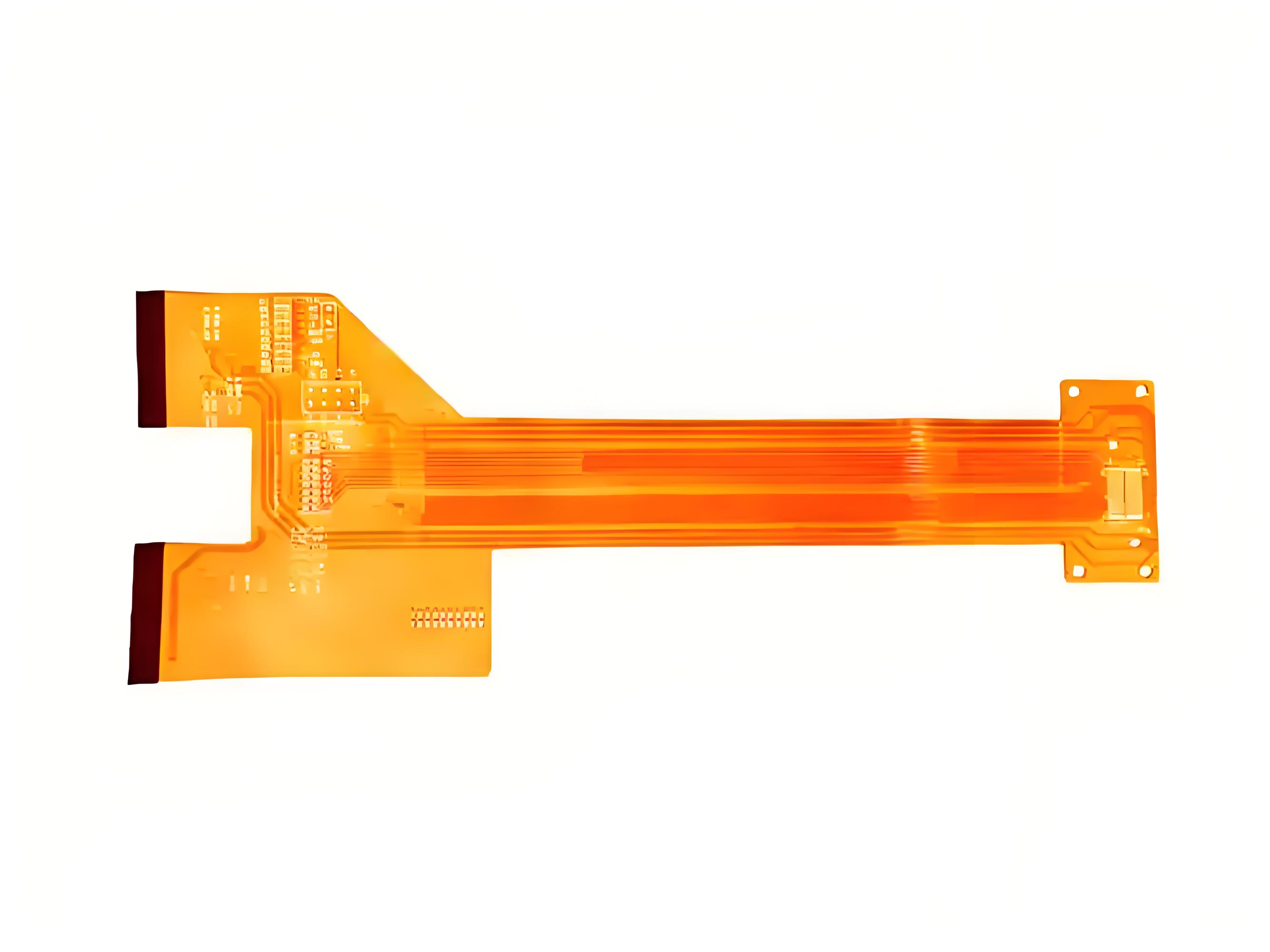
What Are Applications of Flexible Polyimide PCB?
Applications of Flexible Polyimide PCB
- Consumer Electronics – Foldable displays (smartphones/tablets).
- Aerospace – High-temperature wiring in satellites/spacecraft.
- Medical Devices – Wearable sensors (ECG patches/implantable modules).
- Automotive – Battery management systems (EVs) & autonomous vehicle sensors.
- Industrial Automation – Flexible joints in robotic arms/motion control systems.
- Energy – Solar panel interconnections (flexible photovoltaic modules).
- Telecommunications – High-frequency signal routing in 5G/mmWave devices.
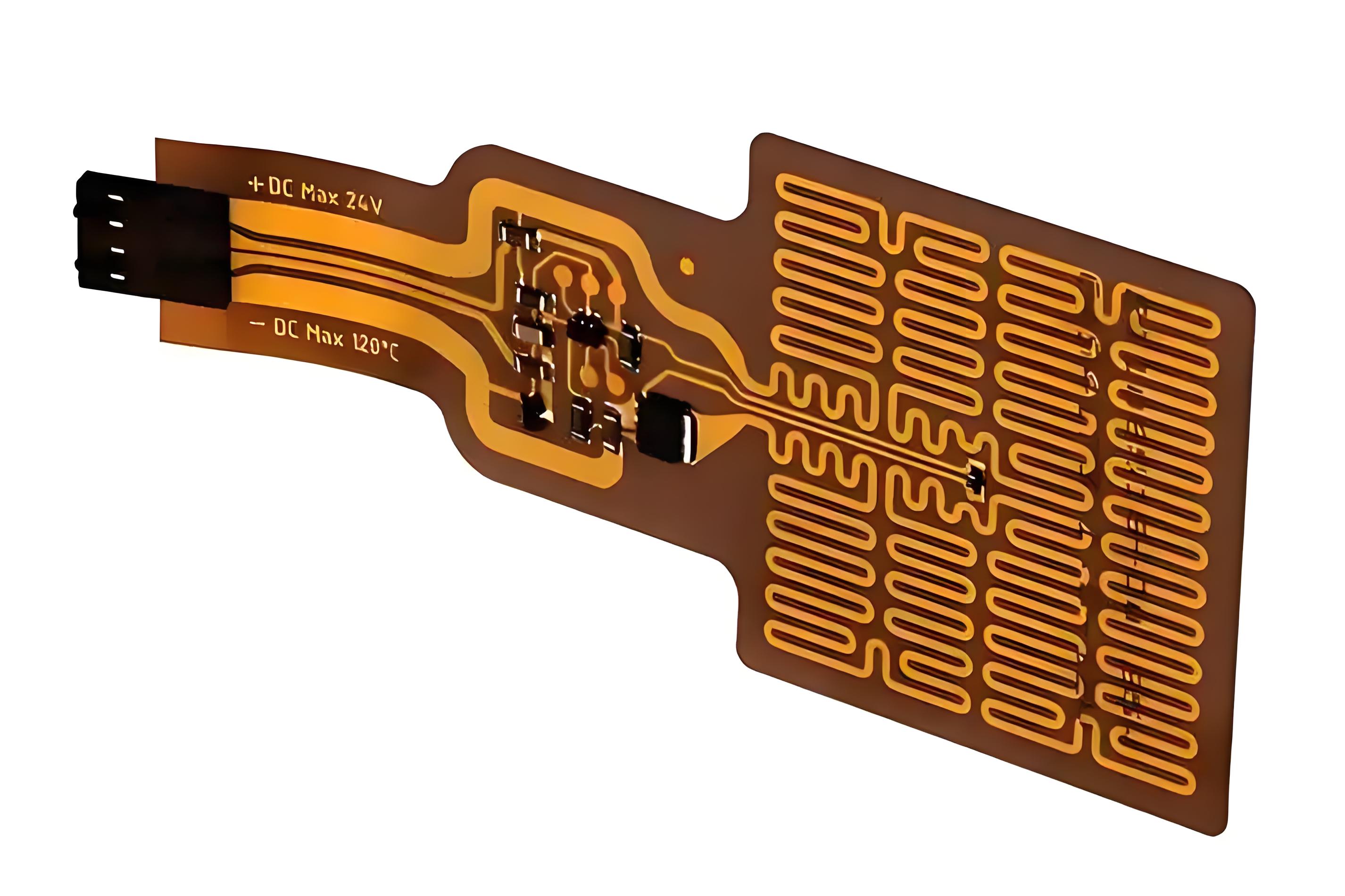
How Are Polyimide PCBs Manufactured?
Manufacturing Process of Flexible Polyimide PCBs
1. Material Preparation
- Base Film: Polyimide (PI) film (12.5–50µm) selected for thermal stability (Tg > 250°C).
- Adhesive Coating: Epoxy/acrylic adhesive applied to PI film for copper bonding.
2. Copper Cladding
- Lamination: Adhesive-coated PI film laminated with electrolytic copper foil (1/3–2 oz) at 180–200°C.
- Temporary Carrier: Aluminum/steel carrier attached for ultra-thin FPCs to prevent warping.
3. Circuit Patterning
- Dry Film Application: Photosensitive dry film laminated onto copper.
- Exposure & Development: UV light exposes circuit pattern; unexposed areas washed away.
- Etching: Ferric chloride/alkaline etching removes unprotected copper (line width/spacing ≥25µm).
4. Coverlay Application
- PI Coverlay: Second PI film with adhesive laminated over circuits for protection.
- Laser Ablation: CO₂ laser drills precision holes (via/pad openings).
5. Plating & Surface Finish
- ENIG Plating: Electroless nickel/immersion gold applied to pads for solderability.
- Stiffener Bonding: FR4/PI stiffeners attached to connector zones via thermal bonding.
6. Testing & Inspection
- AOI: Automated optical inspection for defects (open/short circuits).
- Electrical Testing: Flying probe/bed-of-nails tests verify continuity/impedance.
7. Cutting & Forming
- Laser Cutting: Precision shaping of FPC outlines.
- Bending Test: Flexibility validation (1,000+ bend cycles at 180°).
8. Final Cleaning & Drying
- Ultrasonic Cleaning: Removes residual particles from etching/plating.
- Baking: FPCs dried in 80–100°C oven to eliminate moisture.
9. Packaging
- Anti-Static Protection: FPCs placed in anti-static bags with desiccant packs.
- Cushioning: Foam inserts or vacuum-formed trays used to prevent movement.
- Labeling: Barcode/QR code labels include product ID, batch number, and RoHS compliance.
10. Quality Final Check
- Visual Inspection: Confirm no scratches, folds, or contamination.
- Electrical Recheck: Sample testing for critical parameters (e.g., impedance).
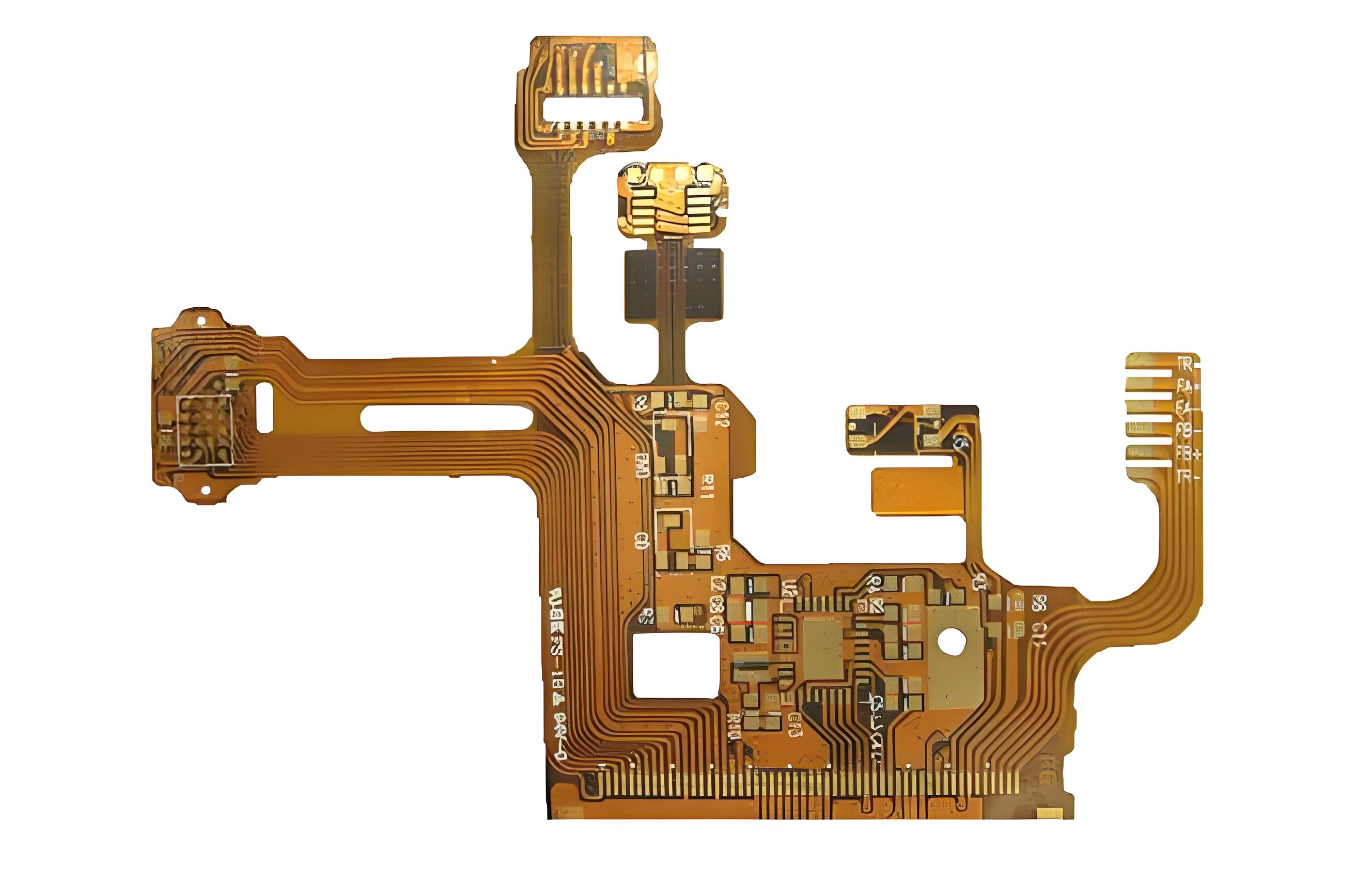
Polyimide PCB Manufacturer in China – Best Technology
Reasons why choose us as polyimide PCB manufacturer:
- 24-hour rapid prototyping: shorten the R&D cycle by 50% and accelerate product launch.
- 1 Piece MOQ: zero inventory risk, trial production cost reduced by 90%.
- Competitive & Transparent Pricing – No hidden costs, offering the best value without compromising quality.
- Turnkey Solutions – Full-service PCB manufacturing from design to delivery, accelerating your product’s time-to-market.
- ISO 14001/ISO 13485 certification: medical/automotive customers are exempt from secondary testing, and compliance costs are reduced by 30%
- 0.075mm ultra-thin substrate processing: folding screen FPC thickness is reduced by 40%, and the bending life reaches 200,000 times.
- Mature blind and buried via technology: circuit density increased by 40%, adapting to the needs of 5G modules/medical implants.
- Free DFM (Design for Manufacturability) Analysis: Optimizes PCB layouts to reduce material waste, lower production costs, and avoid late-stage design revisions.
Please feel free to contact Best Technology if you have any inquiry for polyimide PCB: sales@bestpcbs.com. Looking forward to hearing from you soon!
Tags: Polyimide Flex PCB, Polyimide PCB