Copper MCPCB聽is widely used in high-power LED and charging systems because of its strong thermal performance and reliability. But many engineers still wonder how to improve the thermal quality even further. Let鈥檚 walk through everything you need to know.
As a major metal core PCB manufacturer in China, Best Technology offers outstanding quality copper MCPCB, DTP copper MCPCB, aluminium core PCB, heavy copper PCB, and PCB assemblies to a rapidly expanding market. With 19 years of seniority, Best Technology has practical experience to tackle customer headaches like thermal resistance from dielectric layer bottleneck and CTE mismatch-induced failures. All our manufacturing processes strictly adhere to the ISO 9001, ISO 13485, IATF 16949, AS9100D, UL, REACH, RoHS. You will get the finest quality copper MCPCB from us. For additional information, call +86-755-2909-1601 or email us at sales@bestpcbs.com.
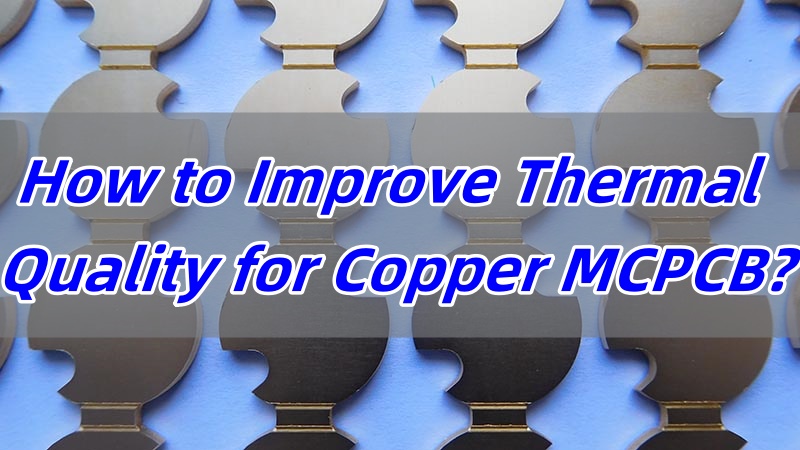
What is Copper MCPCB?
Copper MCPCB stands for Copper Metal Core Printed Circuit Board. It uses copper as the core base material, offering superior thermal conductivity compared to standard aluminum-based PCBs. While the thermal conductivity of typical copper MCPCBs ranges from 8 to 50 W/m路K, advanced designs using direct thermal path (DTP) or thermoelectric separation structures can achieve conductivity levels exceeding 400 W/m路K.
These boards are commonly used in applications requiring efficient heat dissipation, such as high-power LED lighting, automotive electronics, RF power modules, power chargers, industrial motor controllers, and telecom equipment. The copper core effectively spreads and transfers heat away from critical components, reducing thermal stress and enhancing performance stability.
However, manufacturing copper MCPCBs involves more stringent process control than aluminum types. The high thermal conductivity and hardness of copper require precise oxidation control, careful lamination, and well-managed costs. Despite the higher price, copper MCPCBs are a preferred choice for engineers targeting reliability under extreme thermal loads.
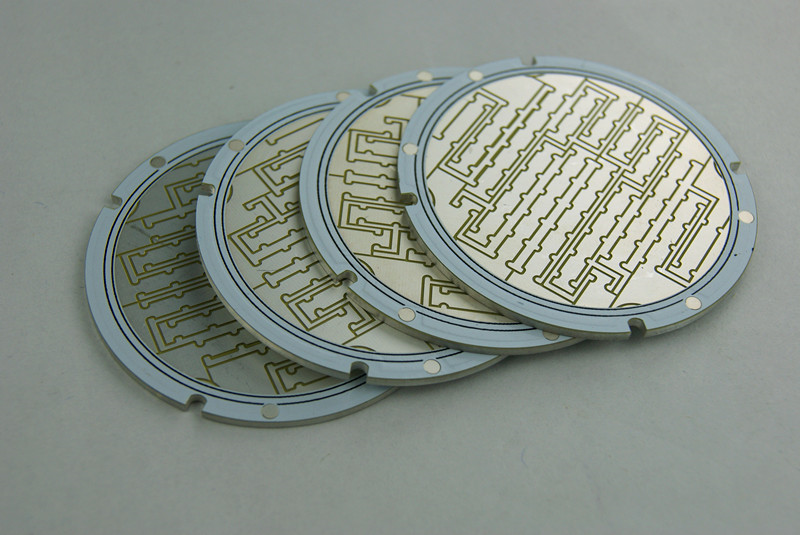
What is the Full Form of MCPCB LED?
MCPCB LED means Metal Core Printed Circuit Board used for LEDs. It has better heat dissipation compared to standard boards. In聽Copper MCPCB LED聽applications, copper acts as the main path for heat flow, helping the lights stay cooler and last longer.
What is the Difference Between DTP Copper MCPCB and Copper MCPCB?
DTP stands for Direct Thermal Path. DTP Copper MCPCB directly connects the heat source to the copper base. Regular Copper MCPCBs still transfer heat well, but DTP models handle more power. In short, DTP boards suit ultra-high-power needs. Standard Copper MCPCBs are better for regular thermal jobs and cost less.
Feature | Standard Copper MCPCB | DTP Copper MCPCB (Direct Thermal Path) |
Structure | Dielectric layer separates copper trace and base | Heat source connects directly to copper base |
Thermal Conductivity | Typically 8鈥50 W/m路K | Up to 400 W/m路K with thermal separation |
Heat Transfer Efficiency | Good | Excellent 鈥 minimal thermal resistance |
Application Power Level | Moderate power devices | Ultra-high-power devices |
Typical Applications | LED lighting, consumer chargers | Laser diodes, power amplifiers, industrial lasers |
Manufacturing Complexity | Standard copper core processing | Requires precise drilling, metal bonding |
Cost | Lower | Higher due to advanced structure |
Design Flexibility | More design options with dielectric layer | Less flexible but highly efficient thermally |
What is the Thermal Conductivity of Copper Base PCB?
Copper base PCBs offer excellent thermal conductivity, but the actual range depends on the structure and processing method. In standard multilayer copper MCPCBs, the thermal conductivity of the entire board is typically between 1 and 8 W/m路K鈥攎ainly limited by the dielectric layer. However, with advanced designs like direct thermal path (DTP) or thermoelectric separation, the thermal conductivity can reach up to 398 W/m路K, which is very close to the theoretical value of pure copper.
In contrast, aluminum-based PCBs usually provide thermal conductivity in the range of 1 to 2 W/m路K, though some high-end aluminum substrates can approach 237 W/m路K under special processing.
This significant difference is why copper base PCBs are widely used in high-power LED lighting, automotive headlamps, industrial lasers, and RF modules. The superior thermal path enables faster heat dissipation, better reliability, and longer component lifespan in demanding thermal environments.
How Thick is the Copper in Copper Core PCB?
The copper thickness in a copper core PCB鈥攐ften referred to as copper PCB thickness鈥攙aries based on the electrical load and thermal demands of the application. Standard copper foil thicknesses used in most copper MCPCBs include:
- 1oz (35渭m): Common for signal layers or low-current applications
- 2oz (70渭m) to 4oz (140渭m): Preferred for power electronics, especially in high-current or thermally demanding circuits
- 10oz (350渭m): Considered ultra-thick copper, used only in special high-power designs and requires advanced fabrication techniques
- Up to 20oz (approximately 680渭m): Possible in industrial PCBs, though rarely used due to design and cost complexity
A 4oz copper PCB is often the sweet spot鈥攊t offers enough copper to carry substantial current and dissipate heat effectively without over-complicating the board structure.
The right copper thickness ensures electrical reliability and thermal safety. Thicker copper allows wider traces to carry higher current, reducing resistance and improving heat spreading. However, extremely thick copper may affect impedance control and manufacturability, so designers must balance thermal performance with structural feasibility.
What Are PCB Copper Mechanical Properties?
Copper has great mechanical strength. It can handle vibration, bending, and pressure without cracking. Its ductility makes it easy to shape during production. These聽PCB copper mechanical properties聽also help reduce thermal stress on components.
How to Improve Thermal Quality for Copper MCPCB?
Improving the thermal quality of Copper MCPCB isn’t just about using thicker copper鈥攊t requires a systematic approach from material selection to layout design. Here’s how you can achieve better thermal control:
1. Optimize Copper Thickness
Using 4oz copper foil (about 140渭m) is a common way to enhance heat dissipation. It allows for larger current flow and better thermal spread. However, it works best when combined with an array of thermal vias that direct heat from the surface to the copper core. For extreme thermal loads, 10oz or thicker copper can be used, but that requires special etching techniques and significantly increases production costs.
2. Improve PCB Layout and Component Placement
Thermal design begins with smart layout. Place heat-generating components as close to the copper core as possible, ideally near the board edges or in well-ventilated zones. For vias:
- Use thermal via diameters of around 0.3mm
- Keep via spacing between 1mm and 1.5mm
- Consider filling vias with conductive silver paste, which can reduce thermal resistance by up to 30%
This structure ensures heat travels downward efficiently instead of staying at the surface.
3. Choose Low Thermal Resistance Dielectric Materials
The dielectric layer plays a critical role in thermal conductivity. Materials with low thermal resistance鈥攍ike ceramic-based substrates鈥攈elp minimize heat bottlenecks between the copper layer and the metal core.
Be cautious with standard epoxy resins, which have low thermal conductivity (~0.276 W/m路K). They might be cost-effective but can limit heat transfer in high-power designs.
4. Add Thermal Pads and Use Proper Interface Materials
Use thermal pads directly under the heating elements. The pad area should match the chip’s contact pad size. For better contact, apply thermal grease or thermal silicone with at least 3 W/m路K thermal conductivity. This reduces the gap resistance and ensures smoother heat flow.
Thermal pads are especially helpful in MCPCB LED modules and Copper MCPCB charger circuits, where consistent heat transfer is essential for performance and safety.
5. Use Effective Surface Finishes
Surface finishes impact both thermal and soldering performance. Consider:
- ENIG (Electroless Nickel Immersion Gold): Offers smooth thermal pathways and protects copper from oxidation
- OSP (Organic Solderability Preservative): Cost-effective and avoids excess coverage over thermal areas
Avoid placing solder mask over critical heat zones. This layer acts as an insulator and can block effective heat transfer if not handled properly.
6. Validate the Design with Thermal Simulations and Real Tests
Design isn’t complete without validation. In MCPCB LED applications, combining copper cores with heat pipes has shown to lower junction temperatures by 5鈥8掳C. For high-power chargers, applying a vapor chamber or uniform heat spreader can control surface temperature variation within 卤3掳C, improving long-term reliability.
In summary, by combining these design methods, copper MCPCB performance can be enhanced dramatically, especially in fields where thermal failure isn’t an option. Best results come from a balanced approach鈥攏ot only thicker copper, but smarter architecture, better materials, and validated thermal paths.
What is the Use of Copper Substrate PCB?
With a thermal conductivity of up to 398 W/m路K, copper cores enable reliable and efficient heat dissipation, making them ideal for compact, high-performance circuits.
Copper MCPCBs are especially suitable for automotive electronics, LED lighting, fast-charging applications and power devices thanks to better heat control. During high current flow, the copper base reduces the junction temperature of power ICs by 15鈥20掳C, preventing thermal stress and improving charging stability. The use of via arrays (鈮0.3 mm) in these boards ensures vertical heat conduction from heat sources to the copper layer.
Compared to standard FR4 boards, copper substrate PCBs offer 50%鈥70% lower thermal resistance, and can handle 3 to 5 times more current density. This allows engineers to design more compact layouts without compromising on reliability. However, to maintain long-term performance, oxidation-resistant surface finishes such as OSP or ENIG are required. Also, for boards thicker than 1.5 mm, custom drilling techniques are necessary to prevent damage during manufacturing.
Why Choose Best Technology for Your Metal Core PCB Manufacturer?
At Best Technology, we understand customers face problems like unstable quality, slow delivery, and poor service from other PCB suppliers. That’s why we focus on:
- Strict Quality Control:聽We follow ISO9001, ISO13485, IATF16949, and AS9100D standards.
- Advanced Systems:聽Our MES system keeps all components traceable, reducing risk.
- Experienced Engineers:聽Our team helps customers with聽Metal core PCB design guidelines聽to improve thermal performance.
- Complete PCB Support: You will get the superior-quality MCPCB prototype, fabrication, and PCBA service from us without consuming a lot of time and cost between different copper MCPCB suppliers.
- Reliable Delivery:聽We understand time is money. Our lead times are consistent and fast. For some complex copper MCPCB, the lead time is 2-3 weeks. For urgent copper MCPCB circuits, we can ship out from our factory within 48 hours.
Whether you need聽heavy copper PCB,聽copper substrate PCB, or advice on聽Metal core PCB stackup, we are here to help. Many clients came to us after problems with others and stayed because of our service.
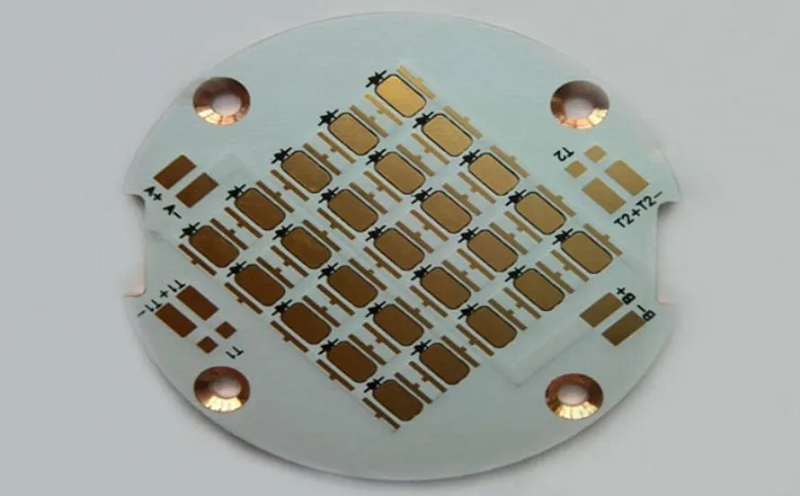
To conclude, copper MCPCB聽plays a key role in handling heat in electronics. From聽MCPCB LED聽lighting to high-speed chargers, it boosts stability and performance. By choosing smart designs and working with reliable partners like Best Technology, you can improve heat transfer, cut risks, and gain viable solutions.
If you鈥檝e had problems with inconsistent quality or long delays before, give Best Technology a try. A warm welcome to call us at +86-18923412995 or fill out a contact form online and share with us your Gerber files, any special requirements, and the order quantity. And we can give you our practical quote quickly.
Tags: Copper MCPCB