Aluminium PCB manufacturer plays a critical role in delivering high-performance prototypes for power-dense applications like LED lighting, automotive electronics, and industrial controls. When speed and reliability matter, choosing the right partner makes all the difference.
Best Technology is an aluminium PCB manufacturer in China, supplying better quality aluminium PCB from prototypes to mass manufacturing services in a rapidly growing market. Our factory is fully compatible with ISO 9001, ISO 13485, IATF 16949, AS9100D, UL, REACH, and RoHS. No matter whether you need aluminum PCB board, copper PCB board, China IMS PCB, or custom MCPCB, we have a full product line for your selection. Please email us with your Gerber files or any suggestions at sales@bestpcbs.com. We would be delighted to give you our quote and the viable solutions.
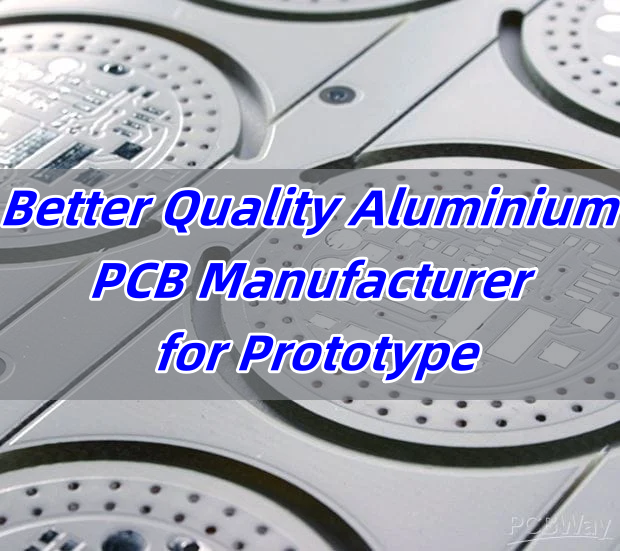
What is the Difference Between Aluminum PCB and FR-4?
Aluminum PCB vs FR4 is one of the most common decisions in circuit designâespecially when thermal performance matters. FR-4 is a standard fiberglass-reinforced epoxy material with good electrical insulation and mechanical strength. Itâs affordable, easy to process, and ideal for most general-purpose electronics. However, its thermal conductivity is quite low, typically around 0.3 W/mK.
In contrast, aluminum PCBs use a metal baseâusually 5052 or 6061 aluminum alloyâpaired with a thermally conductive dielectric. Their thermal conductivity ranges from 5 to 10 W/mK, allowing them to transfer heat much faster than FR-4. This makes aluminum PCBs the better choice for high-power LED lighting, power converters, automotive modules, and motor drivers where heat buildup can affect performance or cause failure.
- When to Use Aluminum PCBs?
Use aluminum when your design includes high-current components, dense LED arrays, or thermal hotspots that demand effective heat dissipation. They’re also beneficial in compact enclosures where airflow is limited.
- When to Use FR-4?
Choose FR-4 for cost-sensitive designs, lower power circuits, or consumer electronics that donât produce much heat. Itâs more flexible in terms of stackup and supports multi-layer routing better.
- Why Choose Aluminum Over FR-4?
Aluminum PCBs protect temperature-sensitive components by lowering the junction temperature. This improves reliability, reduces thermal stress, and extends the productâs lifespan. So, when thermal performance is a key concern, aluminum is a smarter choice than FR-4.
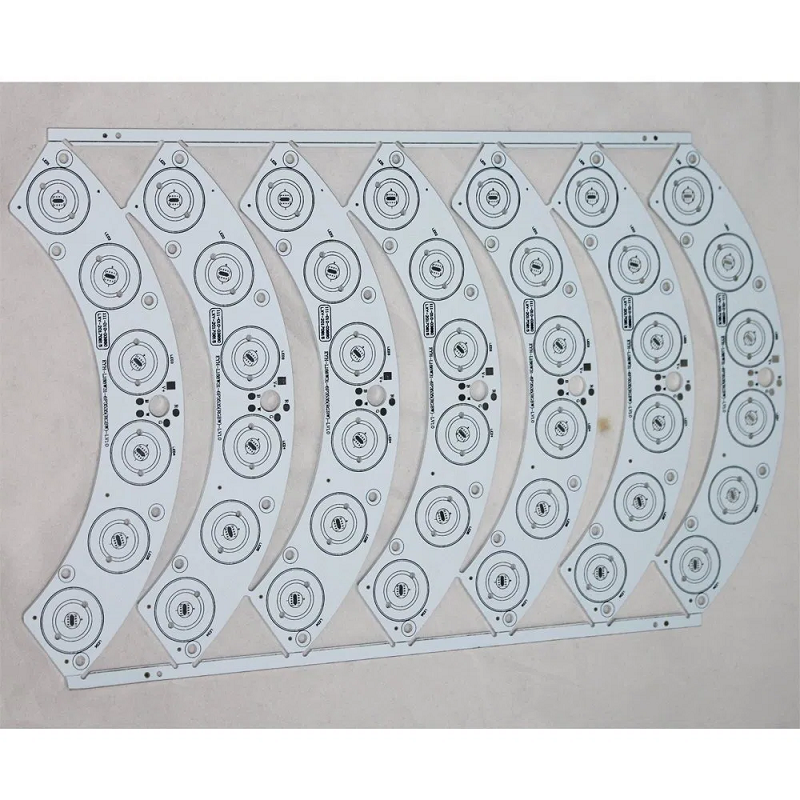
Who Are the Biggest Aluminium PCB Manufacturers in China?
China is a major hub for aluminium PCB manufacturing. Here are three top companies you should know:
- Best Technology: Known for quality and precision, Best Technology provides aluminium PCBs with tight tolerances and fast delivery.
- Suntak Technology: A large volume manufacturer offering mass production services and affordable pricing for general applications.
- JLCPCB: Popular for online orders and low-cost prototyping. While fast, the tradeoff may be limited customization.
In conclusion, if you’re seeking a balance between quality and speed, Best Technology offers advanced control for rapid prototyping while ensuring fewer errors.
Who is the Largest PCB Aluminium LED Manufacturer in North America?
North America has several key players in LED aluminium PCB production. Here are three leading manufacturers:
- Advanced Circuits: Based in Colorado, they specialize in prototype-to-volume PCB builds with quick turnaround and LED capabilities.
- Sunstone Circuits: Offers aluminium core solutions for LED applications with a focus on customer support and design assistance.
- Rush PCB Inc.: Known for fast lead times and complex stackups for high-brightness LED products.
These manufacturers cater to diverse industry needs, from commercial lighting to automotive and industrial applications, leveraging aluminum PCBs’ superior thermal management properties. Their services typically include design validation, rapid prototyping, and volume production with certifications like UL and ISO compliance.
Who Are Aluminium PCB Manufacturers in India?
Indiaâs aluminium PCB market is growing steadily. Below are three reliable manufacturers:
- Shogini Technoarts: Based in Pune, they provide both single and double-sided aluminium PCBs with thermal vias.
- Circuit Systems India: Located in Gandhinagar, offering advanced prototyping and quick delivery.
- Fine-Line Circuits Ltd.: Mumbai-based, experienced in export and specialized PCBs for lighting and industrial sectors.
Overall, Indian suppliers offer affordable solutions, though delivery timelines can be longer. Choose based on your volume and lead time needs.
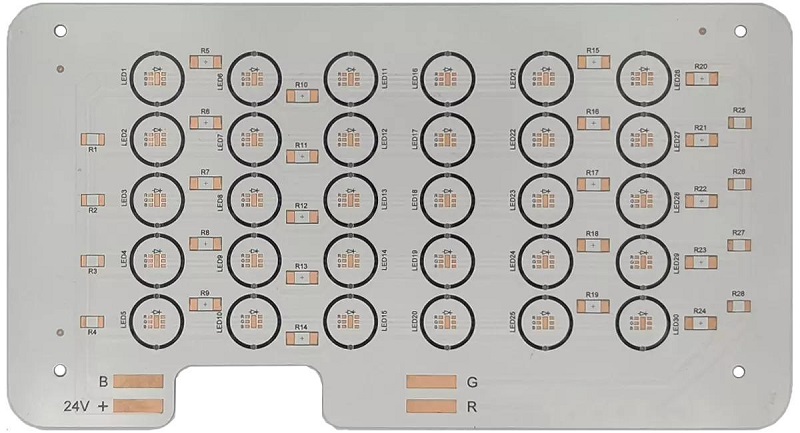
What is the Aluminium PCB Manufacturing Process?
- Raw Material Preparation:Â Selection of aluminium base material and defining the copper foil thickness depending on the design’s power needs.
- Aluminium Surface Treatment:Â The aluminium base undergoes chemical oxidation or passivation to improve bonding strength with the dielectric layer.
- Lamination:Â High-pressure and high-temperature lamination process bonds the copper foil, dielectric layer, and aluminium base firmly. This stage is critical, as poor bonding causes delamination.
- Image Transfer:Â Circuit pattern is created using dry film photoresist, UV exposure, and development to define the copper traces.
- Etching:Â Unwanted copper is removed using etchants such as ferric chloride or cupric chloride to form the circuit pattern.
- Drilling:Â Special carbide or diamond-coated tools are used to drill through high-hardness aluminium with high precision.
- Plating:Â Via holes are electroplated with copper or nickel to improve conductivity and ensure strong interconnection.
- Solder Mask:Â Applied via screen printing or spray, then exposed and developed to protect copper traces. Most aluminium PCBs use white solder mask with black silkscreen for better LED light reflection. Black solder mask with white silkscreen is used for decorative or display lighting, offering better contrast.
- Surface Finish:Â OSP, HASL, or ENIG is applied depending on component requirements. OSP suits flat pads for SMT. HASL is common for through-hole assembly. ENIG is ideal for fine-pitch ICs.
- Profiling:Â CNC or V-cut machines shape the board. CNC depth control is especially critical for cavity designs in LED arrays.
- Inspection:Â AOI and X-ray machines are used to verify solder quality and detect internal defects like voids or bridging.
Some challenging stages include lamination (risk of delamination), surface treatment (poor bonding), and CNC profiling (cavity depth tolerance within ±0.01mm). Best Technology optimizes these with real-time thermal simulation, high-speed CNC, and MES-based quality tracking for better consistency.
Why Use Aluminium PCB Board for LED?
LEDs generate significant heat during operation. Aluminium PCBs help dissipate this heat efficiently, protecting both the light output and the lifespan of the LEDs. Compared to standard FR-4 boards, an aluminium PCB board for LED can typically reduce the junction temperature by around 15°C to 30°C, depending on factors like copper thickness, thermal structure, and ambient conditions. This enhanced thermal performance improves the long-term reliability of LEDs, especially in demanding applications like automotive lighting and streetlamps.
What is the Most Costliest PCB?
The most costly PCBs are those that combine high layer counts with advanced fabrication processes. Multi-layer boards with 16 layers or moreâespecially up to 32 layersâare at the top end due to their complex lamination, precise drilling, and intricate interconnections. These boards often require multiple press cycles and tight registration, significantly increasing production time and cost.
HDI PCBs (High-Density Interconnect) also fall into the premium category, especially Type III HDI structures. These use laser-drilled microvias, stacked vias, and via-in-pad designs. The fabrication complexity and yield challenges can push their cost 180% to 200% higher than standard multilayer boards.
Aluminum core PCBs, though cost-effective in handling heat for power applications, are inherently more expensive than traditional FR-4 boards due to the metal substrate. When designers add thermal vias, copper coin inserts, or heat-sink cavities, the manufacturing process becomes more demandingâfurther raising costs.
Another major cost driver is embedded component technology, where passive or active elements are integrated directly into the board. This technique requires special materials like ABF (Ajinomoto Build-up Film) and precision layering. The result is a thinner and more compact product, but with a substantial cost increase.
In Summary, while aluminum boards with advanced thermal designs can be expensive, 32-layer multilayer PCBs and advanced HDI PCBs represent the highest cost segment due to their demanding processing and tight tolerances. Embedded component PCBs also contribute to the top-tier pricing because of the material and manufacturing complexity involved.
How to Choose Aluminium PCB Manufacturers in China?
Look for the following when selecting a partner:
- Certifications (IPC, RoHS, UL, IATF16949).
- Experience with aluminium substrates and thermal design.
- In-house testing: AOI, thermal cycling, X-ray.
- Fast lead times without sacrificing quality.
- MES system for traceability and defect tracking.
Best Technology ticks all the above boxes and goes beyond with engineering support to solve failure-prone designs.
Why Choose Best Technology as Your Trustworthy Aluminium PCB Manufacturer?
Best Technology stands out as a dependable aluminium PCB manufacturer by addressing customers’ needs directly:
- Reducing Technical Failures:Â AOI and X-ray inspections stop solder bridging. Low-CTE dielectrics prevent warpage. Optimized lamination cuts delamination risk.
- Better Thermal Management:Â Plugged copper vias and aluminium substrates dissipate heat fast. ANSYS-based thermal simulation avoids hotspots.
- Certified Assurance:Â IPC Class III, ISO 9001, ISO 13485, IATF 16949, and AS9100D ensure lower field failures. Every board meets RoHS and UL standards.
- Rapid Lead Time: 48-hour precision machining with ±0.01mm tolerance and sequential lamination means no trade-off between speed and complexity.
- One-stop manufacturing service: Our factory provides services from prototype to assembly. Whether you need 1 PCS prototype or 1,000,000 PCS MCPCB SMT PCBA, we can support you fully with rapid lead time.
Unlike other aluminium PCB board manufacturers, Best Technology offers solutions, not excuses. We help customers avoid costly rework by controlling each detail from design to delivery. This makes our aluminium PCB SMT manufacturing trusted by global brands in lighting, automotive, and industrial sectors.
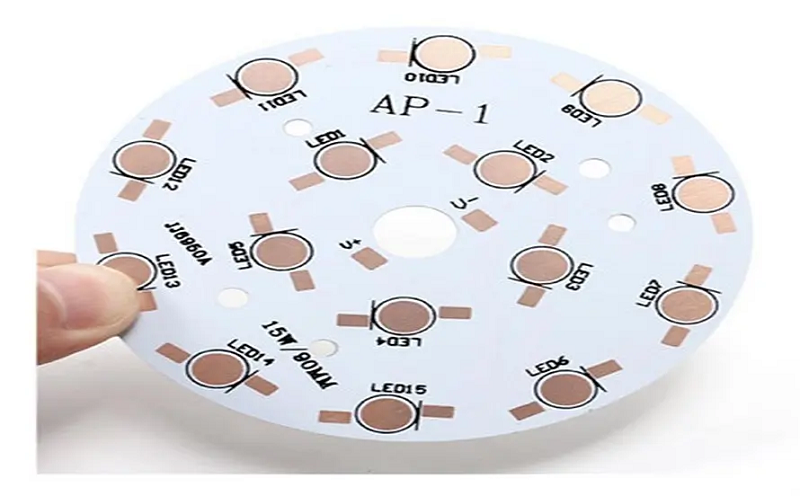
So, if you are tired of sourcing from unreliable aluminium PCB manufacturers in China or facing repeated failures in your LED boards, itâs time to consider Best Technologyâwhere speed, reliability, and care meet in every prototype we deliver. Please feel free to email us at sales@bestpcbs.com if you have any questions or would like a quote.