Struggling to source responsive LED lighting PCB assembly services? Struggling to source responsive LED lighting PCB assembly service? Discover its benefits, application, supplier evaluation tips. reduction cost methods.
Best Technology delivers LED lighting PCB assembly solutions with a vertically integrated supply chain, ensuring uninterrupted access to premium components even during global shortages. Our automated SMT lines and dedicated engineering team enable rapid prototyping in 24 hours and full-scale production within 3-5 days, while emergency orders benefit from prioritized 24-hour turnaround – all backed by strict IPC-A-610 Class 3 quality control for <0.1% defect rates. By combining thermal-optimized DFM analysis (2-6oz copper core integration) with smart panelization algorithms, we reduce material waste by 18% and assembly costs by 15% without compromising luminous consistency (±3% flux variance). Whether you’re developing UV sterilization systems or smart horticultural lighting, our scalable capacity handles 1-piece prototypes to 50k+ batches with identical precision. Welcome to contact us for free design review if you have any request for LED lighting PCB assembly: sales@bestpcbs.com.
What Is LED Lighting PCB Assembly?
LED lighting PCB assembly refers to the specialized process of integrating light-emitting diodes (LEDs) onto printed circuit boards (PCBs) to create functional illumination systems. This involves precise placement of SMD or COB LEDs, resistors, drivers, and thermal management components onto substrates like aluminum-core or FR4 boards, ensuring stable electrical connections and heat dissipation. Advanced techniques such as automated pick-and-place machines, reflow soldering, and conformal coating are applied to achieve consistent brightness, color temperature accuracy (e.g., 3000K warm white), and resistance to environmental stressors like moisture or vibration. The assembly supports diverse applications, from automotive lighting to architectural accents, balancing energy efficiency with mechanical durability while adhering to industry standards for safety and performance.
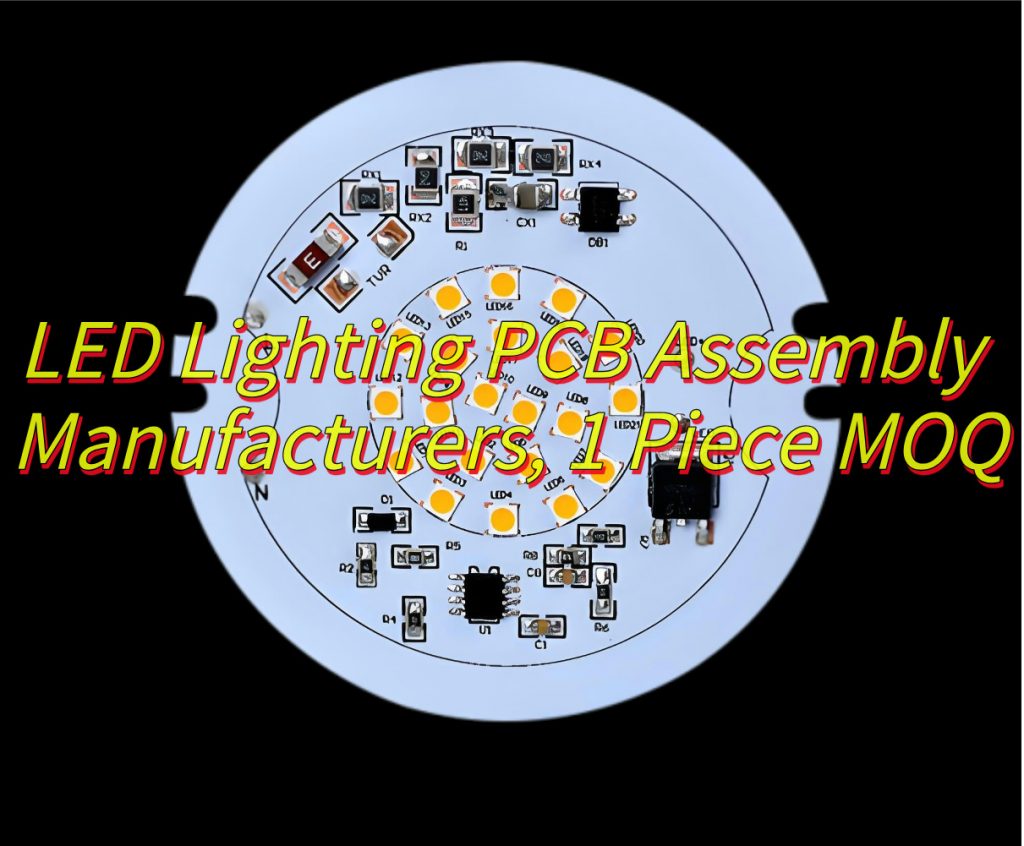
Why Choose LED Lighting PCB Assembly?
Advantages of LED lighting PCB assembly:
- Efficient Production for Rapid Turnaround – LED lighting PCB assembly streamlines manufacturing through automated processes, enabling quick prototyping and bulk production. Advanced SMT lines and modular workflows ensure fast delivery even for complex designs like high-power automotive lighting systems.
- Precision-Driven Quality Assurance – Every LED lighting PCB assembly undergoes multi-stage inspections, including automated optical (AOI) and X-ray testing, to eliminate defects such as solder bridging or component misalignment. This guarantees reliability in harsh environments like outdoor signage or industrial lighting.
- Expert Support for Design Optimization – Collaborate with engineers who specialize in thermal management and electrical performance for LED lighting. Their insights help avoid common pitfalls, such as improper trace spacing or inadequate heat dissipation, reducing redesign risks and assembly costs.
- Scalable Solutions for Custom Applications – From single-board prototypes to large-scale batches, LED lighting PCB assembly adapts to diverse project needs. Examples include tunable horticultural grow lights and dimmable architectural panels, all built with consistent precision.
- Cost-Effective Material Sourcing – Partnerships with certified suppliers ensure access to high-performance substrates like aluminum-core PCBs and ceramic-filled laminates. This balances durability and budget, critical for projects like street lighting or commercial fixtures.
- Long-Term Durability Under Stress – Rigorous thermal cycling and humidity tests validate that LED lighting PCB assemblies withstand extreme conditions. This is vital for mission-critical applications such as emergency lighting or marine navigation systems.
- Sustainability in Manufacturing – Eco-friendly practices, including lead-free soldering and recyclable packaging, align LED lighting PCB assembly with global environmental standards. Energy-efficient processes further reduce carbon footprints for clients prioritizing green compliance.
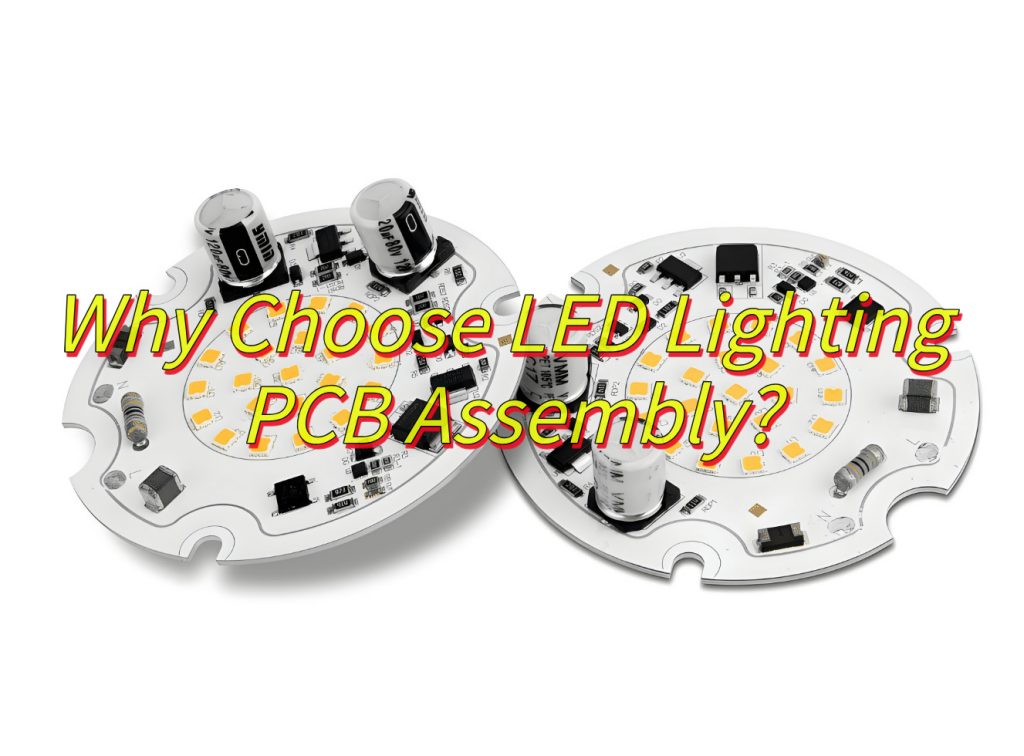
What Are Application of LED Lighting PCB Assembly?
Application of LED lighting PCB assembly:
Architectural and Commercial Lighting
- Office/Retail Spaces: Recessed troffers, panel lights, and linear fixtures use LED PCBs for uniform, flicker-free illumination.
- High-End Interiors: Customizable CCT (2700K–6500K) and CRI (>90) options enhance aesthetics in museums, galleries, and luxury retail.
- Smart Buildings: Integration with occupancy sensors, daylight harvesting, and IoT platforms enables automated dimming and energy savings.
Automotive and Transportation
- Exterior Lighting: Headlights, fog lamps, and brake lights use high-power LED PCBs (e.g., 3–10W) with thermal vias and aluminum substrates for heat dissipation.
- Interior Ambiance: RGBW LED strips and dome lights with PWM dimming create customizable cabin environments.
- EV Charging Stations: Weatherproof PCBs with conformal coatings (e.g., parylene) withstand outdoor conditions.
Industrial and Hazardous Environments
- Explosion-Proof Fixtures: ATEX/IECEx-certified PCBs with hermetic seals and copper-core substrates operate in oil refineries or mining sites.
- Machine Vision: High-CRI (>95) LED rings with uniform illumination aid quality control in assembly lines.
- Cold Storage: PCBs rated for -40°C to 85°C with gold-plated traces resist corrosion in freezers.
Healthcare and Medical Devices
- Surgical Lights: Shadowless LED arrays with 50,000+ lux output and color tuning (4000K–5000K) improve surgical precision.
- Phototherapy: UV-A/UV-B LED PCBs with precise wavelength control (e.g., 365nm) treat skin conditions.
- Diagnostic Tools: Endoscopes and dental curing lights use miniaturized PCBs (10mm×10mm) with fiber-optic coupling.
Outdoor and Street Lighting
- Smart Poles: LED PCBs integrate LiDAR, cameras, and 5G antennas for traffic monitoring and Wi-Fi hotspots.
- Solar-Powered Fixtures: Low-power PCBs with MPPT (maximum power point tracking) circuits optimize battery life.
- Tunnel Lighting: High-lumen COB LEDs with adaptive brightness reduce glare and energy use.
Entertainment and Stage Lighting
- Moving Heads: RGBW LED arrays with 16-bit dimming and DMX/RDM control create dynamic light shows.
- Film/TV Sets: High-CRI (>98) bi-color PCBs with tunable CCT (2000K–10000K) mimic natural lighting.
- Lasers and Effects: UV LED PCBs power blacklight effects, while addressable strips enable pixel-level control.
Horticulture and Agriculture
- Grow Lights: Full-spectrum LED PCBs with UV/IR channels optimize plant growth cycles.
- Vertical Farms: Waterproof PCBs (IP67) with daisy-chain connectors scale easily in controlled environments.
- Research: Programmable light recipes (e.g., 18-hour daylight cycles) accelerate crop development.
Consumer Electronics
- Smart Home: Voice-activated LED strips (e.g., Amazon Alexa/Google Assistant integration) for ambient lighting.
- Wearables: Flexible PCBs with 0.3mm-pitch LEDs power fitness trackers and AR glasses.
- Gaming: Addressable RGB LED matrices with 16.8 million colors sync with gameplay.
Emergency and Safety Systems
- Exit Signs: Battery-backed LED PCBs with 90-minute runtime comply with fire codes.
- Aircraft Cabin Lights: Lightweight, flame-retardant PCBs (e.g., polyimide substrates) meet FAA standards.
- Marine Navigation: Corrosion-resistant PCBs with conformal coatings endure saltwater environments.
Art and Interactive Installations
- Kinetic Sculptures: Addressable LED strips with 24-bit color depth enable pixel-mapping animations.
- Museums: Interactive floors with pressure-sensitive LED PCBs respond to visitor movement.
- VR/AR: Micro LED arrays (<50µm pitch) power high-resolution headsets.
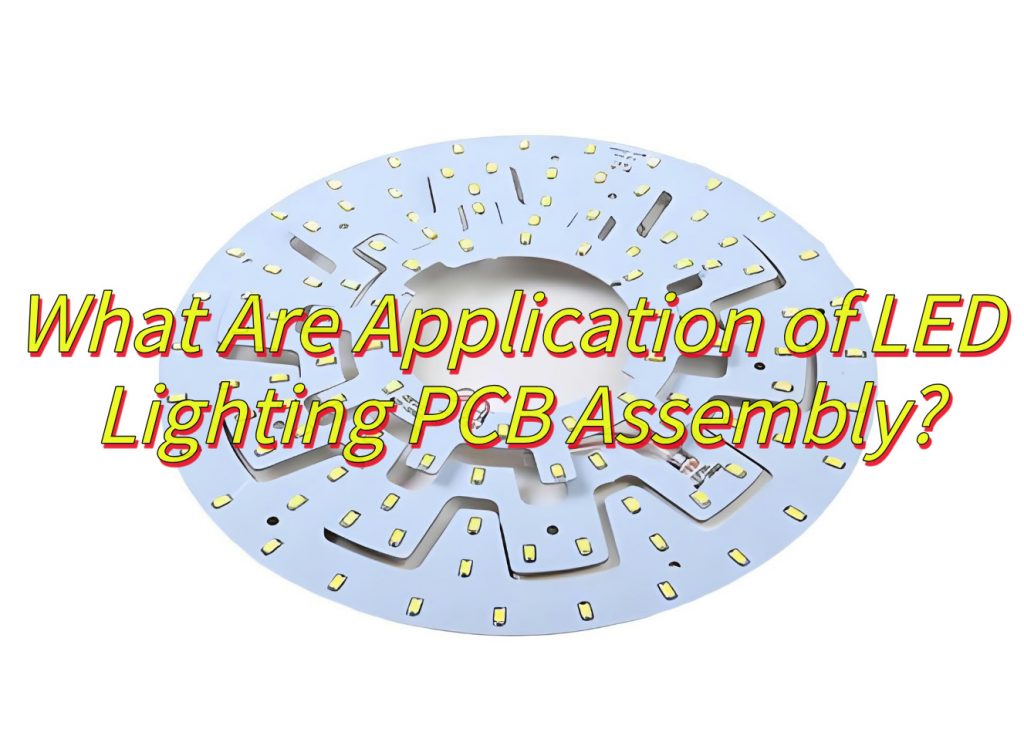
How to Optimize LED Lighting PCB Design to Reduce Assembly Cost?
Here are practical strategies to optimize LED Lighting PCB Assembly design for cost reduction while maintaining performance:
- Simplify Component Selection: Use standardized, high-yield LED packages (e.g., 2835, 5050 SMD) and integrated driver ICs to minimize part counts. Avoid niche components that require manual soldering or special handling, reducing labor costs by up to 30%.
- Adopt Design for Manufacturing (DFM) Rules: Align trace widths (≥0.2mm) and spacing (≥0.15mm) with automated SMT equipment capabilities. Larger solder pads (e.g., 0.6mm×0.6mm) improve pick-and-place accuracy, cutting rework rates by 25%.
- Optimize Panel Utilization: Arrange multiple PCBs in a panel with shared edges and tooling holes. This increases material yield by 15–20% and reduces per-unit costs for small-batch orders.
- Reduce Layer Counts: Use 2-layer PCBs with thermal vias for basic lighting instead of 4-layer boards. For high-power designs, employ aluminum-core substrates to eliminate the need for external heat sinks.
- Streamline Power Distribution: Place decoupling capacitors close to LED drivers (≤5mm) to stabilize voltage and reduce EMI filtering components. This simplifies BOMs and lowers parts sourcing expenses.
- Implement Panelized Testing: Design PCBs with shared test points for automated electrical testing (AET). This reduces inspection time by 40% compared to manual probing of individual boards.
- Leverage Bulk Sourcing: Partner with manufacturers to procure LEDs, resistors, and connectors in bulk. Volume discounts can lower component costs by 5% for large projects.
- Minimize Through-Hole Components: Replace axial resistors or electrolytic capacitors with SMT equivalents to enable fully automated assembly. This eliminates wave soldering steps and associated chemical costs.
- Use Open-Source Design Tools: Adopt free PCB layout software for initial designs. Simulate thermal and electrical performance digitally to reduce prototype iterations.
- Incorporate Design Reuse: Create modular PCB templates for common lighting formats (e.g., 12V round boards). Reusing 60–70% of the layout accelerates time-to-market and cuts engineering hours.
By integrating these tactics, LED Lighting PCB assembly projects can achieve around 20–35% cost savings without compromising quality, scalability, or regulatory compliance.
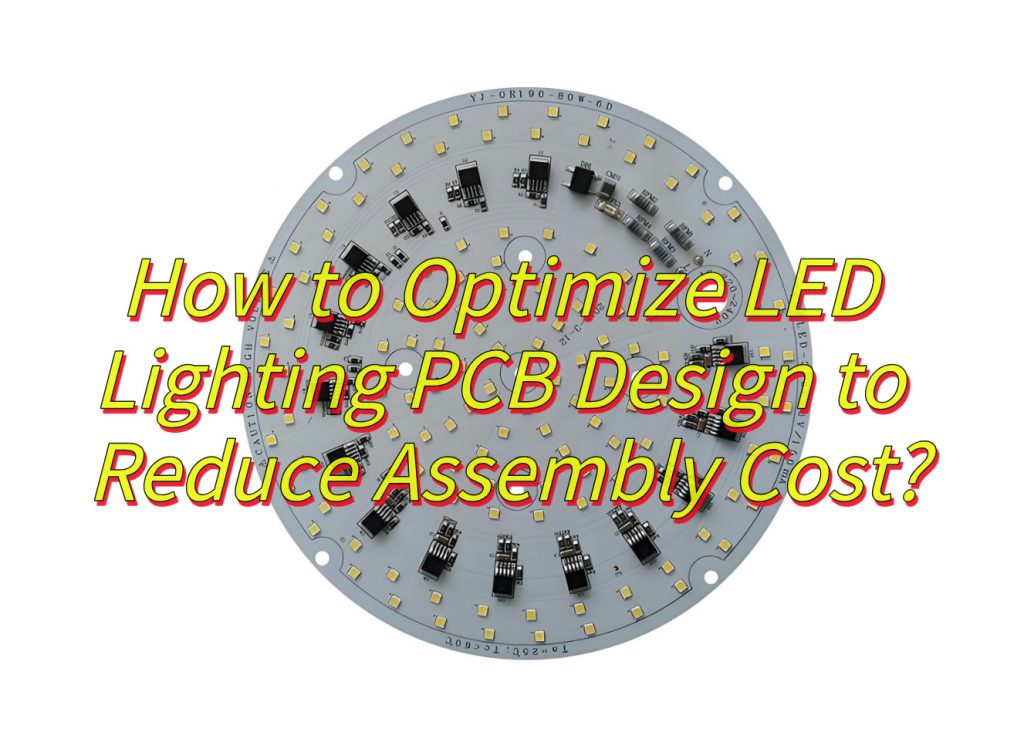
How Are LED lighting PCB Assembled?
Here are assembly process of LED Lighting PCB:
Here’s a detailed, step-by-step breakdown of the LED Lighting PCB Assembly process, focusing on technical workflow and execution:
1. Material Preparation and Pre-Assembly Inspection
- Engineers inspect PCB substrates (e.g., FR-4, aluminum-core), LED components, and surface-mount technology (SMT) parts for defects, compatibility, and alignment with design specifications.
- Components are organized into tape-and-reel feeders or trays for automated assembly.
2. Solder Paste Application
- A precision stainless-steel stencil is placed over the PCB.
- Automated stencil printers deposit solder paste onto exposed pads using a squeegee blade, ensuring uniform coverage for component attachment.
3. Automated Surface-Mount Technology (SMT) Placement
- High-speed pick-and-place machines mount LEDs, resistors, capacitors, and integrated circuits (ICs) onto the PCB.
- Components are placed with high positional accuracy (typically ±0.05mm) using vacuum nozzles and vision alignment systems.
4. Reflow Soldering
- PCBs enter a reflow oven, where solder paste melts to form permanent electrical and mechanical connections.
- Temperature profiles are optimized to prevent thermal damage to LEDs and sensitive components.
5. Automated Optical Inspection (AOI)
- Multi-angle cameras scan the assembled PCB for defects such as solder bridges, missing components, or misaligned LEDs.
- Results are analyzed in real-time to flag rework requirements.
6. Selective Wave Soldering (For Through-Hole Components)
- If through-hole parts (e.g., connectors) are included, PCBs pass through a nitrogen-inerted wave soldering machine.
- Molten solder adheres only to exposed through-hole pads, minimizing thermal stress on the board.
7. Manual Inspection and Rework
- Technicians address AOI-flagged issues using precision soldering irons or rework stations.
- LED polarity and optical alignment are double-checked under magnification.
8. Functional Testing
- Assembled PCBs undergo electrical testing to verify current draw, voltage tolerance, and LED brightness consistency.
- Some designs undergo accelerated aging tests (e.g., 48-hour burn-in) to identify early-life failures.
9. Conformal Coating or Potting
- Protective coatings (e.g., acrylic, silicone) are applied to resist moisture, dust, and vibrations.
- For harsh environments, PCBs may be fully encapsulated in epoxy resin.
10. Final Assembly and Packaging
- Completed PCBs are integrated into lighting fixtures, paired with lenses or diffusers, and connected to power supplies.
- Units are packaged in anti-static bags or custom trays for safe shipping.
How to Evaluate LED Lighting PCB Assembly Manufacturers?
Here are practical guidelines to evaluate LED lighting PCB assembly manufacturers:
Review Certifications and Standards Compliance
- Verify adherence to industry standards (e.g., IPC-A-610 for assembly quality, UL for safety, RoHS for environmental compliance).
- Check certifications like ISO 9001 (quality management) or ISO 14001 (environmental management) to gauge systematic processes.
Audit Production Capacity and Flexibility
- Assess equipment capabilities (e.g., SMT line speed, reflow oven types) to handle your project’s volume and complexity.
- Inquire about rapid prototyping services (e.g., 24-hour turnaround) and scalability for future demand spikes.
Inspect Quality Control Protocols
- Request details on inspection tools (e.g., AOI, X-ray machines) and testing procedures (e.g., thermal cycling, LED binning).
- Confirm defect rates (e.g., <0.1% escape rate) and rework policies to ensure accountability.
Evaluate Material Sourcing Practices
- Probe component traceability (e.g., LED lot codes, solder paste batch numbers) to ensure reliability.
- Check if the manufacturer offers BOM optimization services to reduce costs without compromising performance.
Assess Engineering Support
- Test responsiveness to DFM (Design for Manufacturing) feedback (e.g., trace width adjustments, thermal via recommendations).
- Inquire about simulation tools (e.g., thermal, electrical) to preempt design issues.
Examine Supply Chain Resilience
- Review supplier diversification strategies to mitigate component shortages.
- Confirm inventory management practices (e.g., JIT delivery, safety stock levels) for critical materials.
Request Sample Testing and Pilot Runs
- Order a small batch to validate assembly quality, lead times, and communication efficiency.
- Monitor post-assembly performance (e.g., LED luminous decay, solder joint integrity) under real-world conditions.
Review Intellectual Property Protections
- Confirm NDAs, non-compete clauses, and data security measures (e.g., encrypted file sharing, access controls).
- Check for patent compliance procedures to avoid legal risks.
Analyze Communication and Project Management
- Evaluate transparency in reporting (e.g., daily production updates, yield metrics).
- Test multilingual support and timezone alignment for global projects.
Probe Post-Production Services
- Inquire about warranty terms (e.g., 2–5 years for LED assemblies), repair logistics, and end-of-life recycling programs.
- Confirm support for product iterations or redesigns.
How Long Does it Take to Deliver 1 Piece Sample?
The delivery time for a single LED lighting PCB assembly sample typically ranges from 2 to 8 days, depending on several factors. Below is a detailed breakdown:
Standard Delivery Time (5–8 Days)
Most manufacturers follow a structured workflow:
- Day 1–2: Material preparation, solder paste stenciling, and automated SMT placement.
- Day 3–4: Reflow soldering, AOI inspection, and selective wave soldering (if needed).
- Day 5–6: Functional testing, conformal coating, and final assembly.
- Day 7–8: Quality control checks and packaging for shipping.
Expedited Delivery (24–48 Hours)
For urgent requests:
- 24-Hour Rush: Skip non-critical steps (e.g., selective wave soldering) and prioritize SMT placement and reflow.
- 48-Hour Turnaround: Include basic functional testing but omit accelerated aging tests.
Example: Some factories in Shenzhen (China) like Best Technology advertise 24-hour dispatch for simple designs, though this may exclude advanced coatings.
Main Factors Influencing Delivery Time
- Design Complexity: Multi-layer boards (e.g., 4+ layers) or fine-pitch components (e.g., 0.3mm pitch) add 1–2 days.
- Customization: Specialty materials (e.g., aluminum-core PCBs) or conformal coatings may extend timelines by 24–48 hours.
- Certification Requirements: UL/CE compliance testing adds 1–3 days.
- Shipping: Air freight (3–5 days) is faster than sea freight (15–30 days).
How to Shorten Lead Times
- Pre-share Gerber/BOM Files: Submit design files upfront to reduce pre-production delays.
- Opt for Standard Specs: Use commonly stocked materials (e.g., FR-4 substrates, 0805/0603 components).
- Local Manufacturers: Choose a regional supplier to minimize shipping time (e.g., 1–2 days for domestic delivery).
Hidden Delays to Avoid
- Design Errors: Revisions after production starts can add 3–5 days.
- Component Shortages: Obsolete or niche parts (e.g., specific LED wavelengths) may delay orders by 7–10 days.
- Peak Seasons: Chinese holidays (e.g., Chinese New Year) can extend lead times by 2–4 weeks.
What Factors Affect LED Lighting PCB Assembly Manufacturing Cost?
The manufacturing cost of LED lighting PCB assembly is influenced by a combination of material, process, and logistical factors. Below is a prioritized breakdown of main cost drivers:
Material Costs (30–50% of Total Expense)
- PCB Substrates: Aluminum-core boards (for thermal management) cost 20–30% more than standard FR-4 materials.
- LED Components: High-power LEDs (e.g., 3W+) or specialty wavelengths (e.g., UV, IR) increase costs by 15–40%.
- Passive Components: Precision resistors (±1% tolerance) or automotive-grade capacitors add 5–10% to BOM costs.
Design Complexity (15–25% Impact)
- Layer Count: 4-layer PCBs cost 30–50% more than 2-layer boards due to additional lamination and drilling steps.
- Component Density: Fine-pitch SMT placement (e.g., 0.3mm pitch) requires advanced equipment, raising assembly fees by 10–20%.
- Specialty Features: Blind/buried vias or gold finger contacts add 15–30% to production costs.
Assembly Process (20–35% Impact)
- Labor Intensity: Manual soldering for through-hole components increases costs by 25–40% compared to fully automated SMT lines.
- Testing Requirements: X-ray inspection for BGA components or accelerated life testing adds 10–15% to per-unit costs.
- Conformal Coating: UV-cured acrylic coatings cost 0.05–0.20 per board, while potting compounds add 0.50–2.00.
Order Volume and Scalability (10–20% Impact)
- Economies of Scale: Prototypes (1–10 units) cost 5–10x more per unit than batches of 1,000+ due to setup time and material waste.
- NRE Fees: Non-recurring engineering fees (e.g., stencil fabrication, CAM engineering) average 200–800 per project.
Certification and Compliance (5–15% Impact)
- Safety Standards: UL or ENEC certification adds 500–2,000 per model for testing and documentation.
- Environmental Compliance: Lead-free solder (RoHS) and halogen-free laminates increase material costs by 8–12%.
Supply Chain Factors (Variable Impact)
- Component Lead Times: Long-lead-time items (e.g., custom LED drivers) may incur expedited shipping fees (10–20% premium).
- Currency Fluctuations: Exchange rates for imported materials (e.g., Japanese capacitors) can alter costs by 5–10%.
Geographic Location (10–25% Impact)
- Labor Costs: Manufacturing in Southeast Asia (e.g., Thailand, Vietnam) reduces labor costs by 30–50% compared to Western countries.
- Logistics: Air freight from Asia adds 50–150 per shipment, while sea freight takes 4–6 weeks but costs 70% less.
Engineering Support (5–10% Impact)
- DFM Reviews: Iterations to optimize trace routing or thermal via placement may add 100–500 in engineering fees.
- Custom Tooling: Specialized stencils or fixtures for irregular board shapes cost 300–1,000.
By understanding these factors, you can balance performance, compliance, and budget requirements for your LED lighting PCB assembly project.